How Is 3D Printing Changing the Wind Energy Sector?
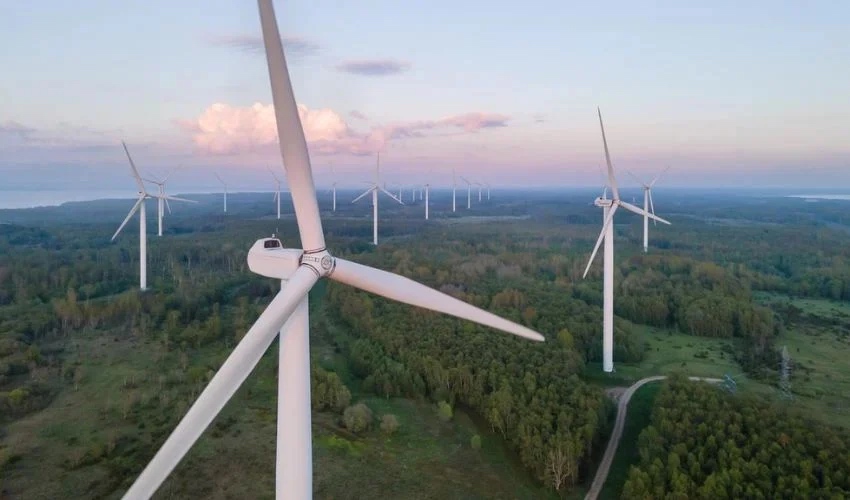
The growing use of 3D printing is spreading across a variety of sectors, with more and more companies recognizing its benefits in manufacturing processes. The energy sector is no exception. According to a report from Additive Manufacturing Research, the 3D printing market in this sector is expected to reach €17 billion by 2032. 3D printing is notably expected to play a crucial role in the development and maintenance of essential wind energy equipment.
Market players are increasingly recognizing the advantages of 3D printing in the field of renewable energies, particularly wind power. This technology offers the possibility of reducing production costs, while allowing size customization to the specific needs of each location. What’s more, the challenges posed by traditional methods of manufacturing wind turbines are well known: blades are generally made from glass-fiber reinforced plastic, a material that is difficult to recycle.
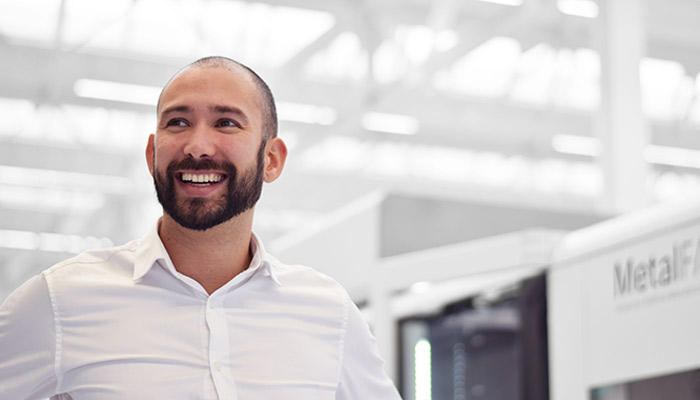
Photo Credits: GE General Electric
The 3D Printing Processes and Materials Used
Among the 3D printing techniques most commonly used in the wind energy sector, FDM technology has a notable place. This method is often chosen for the manufacture of prototypes and parts. Another widely used method is SLS with materials like nylon. Advantages of this approach include the stability of prototypes and finished products, as well as the production of wind energy components, particularly suited to small parts. In addition, binder jetting is also frequently employed.
DMLS has already been implemented in the wind energy sector for the 3D printing of highly precise and complex metal parts, whether prototypes, final components or repairs to existing wind turbines. Companies such as Siemens Gamesa Renewable Energy and Vestas have already used it to manufacture and optimize their turbines. The wind turbine industry also makes frequent use of materials such as PLA and ABS in the manufacture of prototypes and housings for wind turbines. Nylon, polyamide, metal powders, glass and carbon fibers and resins are also used in 3D printing to meet the industry’s specific needs.
The Advantages and Limitations of 3D Printing in Wind Energy
As already mentioned, 3D printing in the wind energy sector is particularly well suited to the production of prototypes. This efficiency stems from the technology’s ability to produce parts economically and quickly, thus fostering innovation in this sector. Furthermore, 3D printing offers the possibility of producing more complex shapes than those obtained using traditional methods, thus improving the performance of rotor blades, as illustrated by a research project carried out at the Technical University of Berlin. As part of this study, the researchers succeeded in printing an entire wind turbine in one piece using the BigRep 3D printer.
It is also possible to design custom-made wind turbine parts for customers, to adapt them precisely to the location of the wind turbines. The use of 3D printing offers the possibility of producing components directly on site, and provides greater flexibility to continuously adjust molds and components. This approach reduces the cost of transporting molded parts, making it easier to supply new printed molds quickly and economically. In the USA, transportation constraints impose length limits of 53 to 62 m for rotor blades due to the existing rail and road infrastructure. This is why 3D printing, possibly combined with robotics, offers considerable potential for on-site manufacturing, particularly for the production of larger, more powerful equipment.
Given the long lead times associated with traditional production methods, 3D printing also offers the possibility of producing replacement parts more quickly and on demand. This reduces ordering and manufacturing times, eliminating the need to constantly maintain high inventory levels. Moreover, this technology creates lightweight, complex structures for wind turbines, helping to reduce their overall weight.
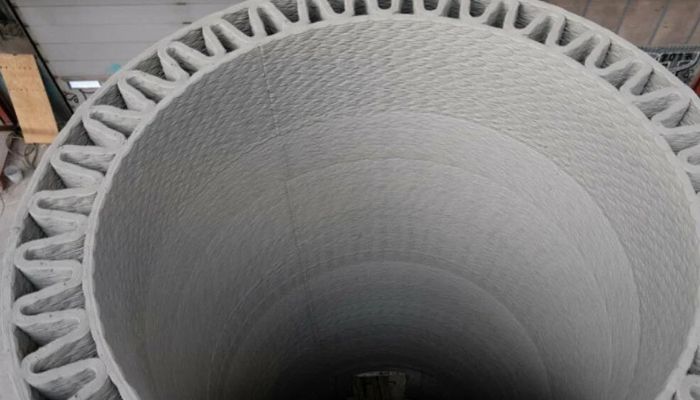
3D printing offers the advantage of being able to produce wind turbines directly on site. (photo credits: en-former)
That does not mean there are not still changes. Although 3D printing offers advantages in terms of reducing the cost of producing prototypes, the initial investment in 3D printers and the materials required is still very high, which can lead to costs when using this technology. In addition, it is often difficult to meet the stringent requirements of standards and certifications when using 3D printing, also resulting in additional costs.
Beyond that, there are still limitations on the size of wind turbine parts that can be 3D printed, and projects such as the ACC remain among the few that allow very large wind turbine parts to be printed. Given that experience of 3D printing in the wind energy sector is still relatively limited, it remains to be seen whether 3D-printed parts will exhibit reliable and stable characteristics over time.
3D Printing Applications in Wind Turbine Manufacturing
3D printing plays a crucial role, applying to various aspects throughout the wind turbine production process. In particular, additive manufacturing is used for the production of components and molds, as well as for prototyping new components. This method makes it possible to rapidly create prototypes for testing and improvement before their use in mass production. For example, US-based General Electric (GE) began 3D printing large wind turbine components in 2019 and opened a 3D printing plant in the USA in 2021, dedicated to research. GE has also used 3D printing to manufacture lighter turbine blades for its GE9X engines.
Another company exploiting 3D printing in this sector is start-up Orbital Composites, which specializes in the production of turbines, wind turbine blades, foundations and towers using on-site, high-throughput, large-scale additive manufacturing. As part of this project, Orbital Composites aims to demonstrate and validate the use of its 3D printing robots for the manufacture of wind turbine blades. The company also aims to develop systems capable of 3D printing wind blades exceeding 100 meters in length, as well as offshore wind turbines directly on board ships at sea.
To achieve these goals, the start-up is collaborating with Oak Ridge National Laboratory (ORNL) and the University of Maine, whose research will be discussed in a later section. Orbital Composites has already received $4 million in financial support from the Department of Energy (DOE) and the Office of Energy Efficiency and Renewable Energy (EERE).
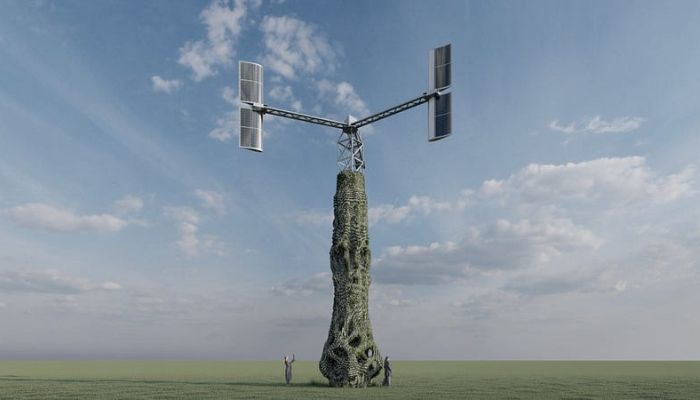
Photo Credits: Soleolico
Research Into 3D Printing in the Wind Energy Sector
Researchers at several universities around the world are exploring the application of 3D printing in the field of wind energy, such as the project at the Technical University of Berlin entitled “3D Printing Powers Wind Turbine Research”. Led by Immanuel Dorn, a technical engineer, and Sascha Krumbein, a master’s student in engineering who is also an instructor on the project, the team is investigating the optimization of rotor blades using 3D printing. Their work includes testing different blade configurations in a large wind tunnel, where they evaluate the performance of rotors subjected to multiple production iterations with various 3D printed materials. The researchers began with aerodynamic design, then moved on to structural design, involving filling and material selection, requiring several iteration cycles to adjust and adapt the materials used. Finally, the team conducted “real-life” aerodynamic tests in their wind tunnel, including crash tests, to assess the performance of the blades.
Many American universities are also involved in research in this field. For example, Purdue University in Indiana, in collaboration with RCAM Technologies and Floating Wind Technology Company, is working on the development of more cost-effective concrete turbine anchors and structures, while exploring additive tool manufacturing for wind turbine rotor blades. This project, conducted in partnership with several companies and financially supported by the US Department of Energy (DOE) to the tune of $2.8 million, aims to speed up tool manufacturing and reduce the cost of finished products through 3D printing.
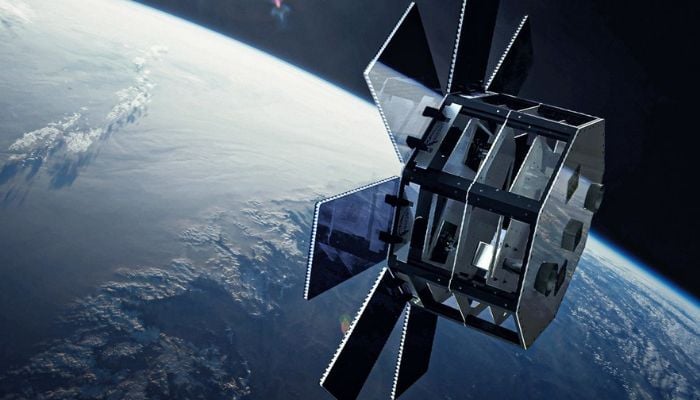
As part of the “3D Printing Powers Wind Turbine Research” project, the team from the Technical University of Berlin is investigating how to optimize rotor blades using 3D printing. (photo credits: BigRep)
In any case, it is clear that the use of 3D printing in wind energy is becoming increasingly important, and shows great potential for innovation and improved efficiency. Companies and research institutes around the world are recognizing the benefits of this technology and investing in the development and application of additive manufacturing methods.
The many applications of 3D printing range from the production of prototypes and components to the manufacture of entire wind turbines. They allow flexibility and adaptability that traditional manufacturing methods cannot offer. Although challenges remain, the way is open for 3D printing in wind energy to transform the sector in a sustainable way and further improve access to clean energy.
What do you think of the use of 3D printing in the wind energy sector? Let us know in a comment below or on our LinkedIn, Facebook, and Twitter pages! Don’t forget to sign up for our free weekly newsletter here for the latest 3D printing news straight to your inbox! You can also find all our videos on our YouTube channel.
*Cover Photo Credits: Photocase