Honda Is Leveraging (and Improving!) Laser Powder Bed Fusion for Transportation
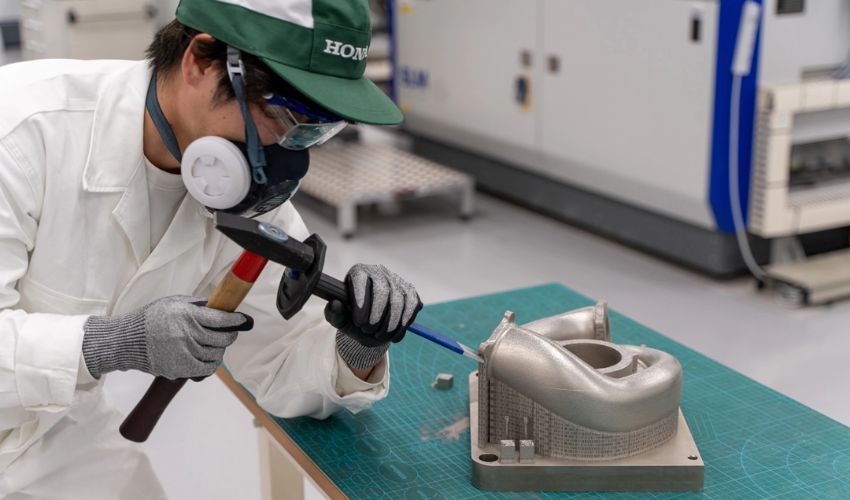
Japanese car manufacturer Honda recently revealed how it uses 3D printing to increase efficiency. The company’s technology of choice? Laser powder bed fusion (LPBF). This metal additive manufacturing technology can create complex geometries that are impossible to achieve through casting and forging, suitable for quickly producing one-off items or small quantities of diverse products. However, the process is not without challenges. So, Honda’s research and development facilities have adopted a deformation prediction simulation technology to address the inefficiencies they faced with the technology.
One of the major ways Honda’s facilities optimized its LPBF practice is related to gas circulation. While LPBF is taking place, an inert gas is circulated in the chamber to create an oxygen-free environment. The purpose of this gas is to remove fumes and spatters that are generated by the melting metal and to prevent oxygen from getting into the part. Otherwise, oxygen can create voids and defects in the product.
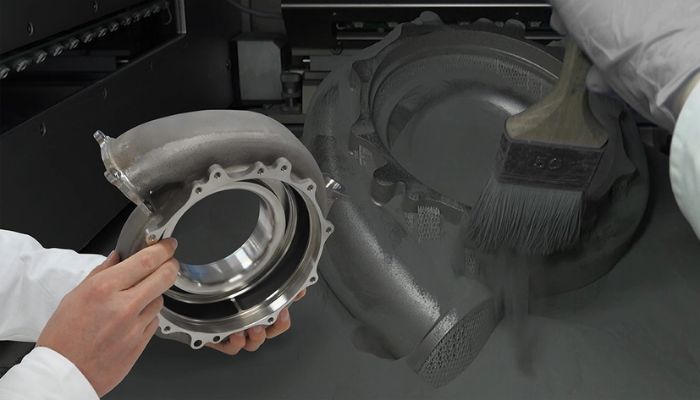
A part from Honda made with LPBF
The company explained that the larger the build area, the more susceptible it is to external disturbances. This is because in areas on the downwind side, where the inert gas flow speed is slow, they cannot remove fumes and metal spatters, resulting in modeling problems on this downwind side. The team’s solution is to use a high-speed camera to check the spatter removal status for each layer. That way, they identify the root of the problem, comparing spatter removal with the wind speed distribution that they measure with a wind speed sensor. Having this data allows them to optimize the wind speed and determine precise conditions for the entire modeling area.
Honda uses this method of trial and error and data collection to improve additional aspects of the LPBF process. By taking pictures of each layer to check the melting state, along with the temperature and laser output, the team can better understand the material, laser and gas flow.
Once they have a piece, the Honda team will also test its tensile strength. Their goal is to form parts where each layer has no gaps. If the laser power is not strong enough, the beads (parts where the metal powder melts and solidifies) will be too small, meaning insufficient layer thickness and gaps in the part. Through monitoring their processes closely, they can optimize their processes and ensure high-quality parts.
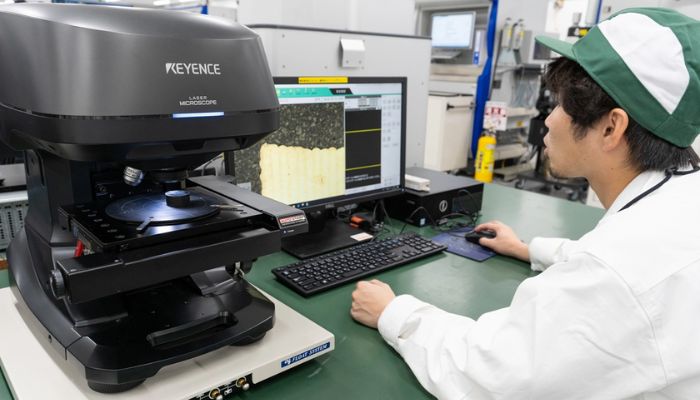
A part being tested for internal quality
What Is Honda 3D Printing?
Honda has a history of using and supporting additive manufacturing. Back in 2016, the company 3D printed components for its Micro Commuter vehicle, and in 2020, they updated the car with 3D printed lightweight metal crankshafts. In 2023, Honda also made headlines for investing in Seurat Technologies, an AM company that focuses on producing metal parts. This latest news from Honda highlighted two different use cases: Formula 1 parts and wheelchair racer’s handlebars.
Formula 1 Parts
For Formula 1, weight optimization and part strength are key. That is why, since 2020, Honda has used AM to quickly produce unique parts with complex shapes and thin walls. For instance, Honda has used metal 3D printing to fabricate pistons, which used to be made of forged aluminum. Now, they use iron, which has a higher specific gravity than aluminum, meaning it would normally be heavier than aluminum. But because of AM, they can fabricate iron parts that are lightweight and strong enough to withstand combustion pressure.
Another F1 part they manufacture with LPBF is turbine housings. Previously, these were made with precision casting, and now they make them through AM with Inconel, a highly heat-resistant nickel-based alloy. These turbine housings and pistons were able to pass strict dimensional standards while shortening production time and reducing costs.
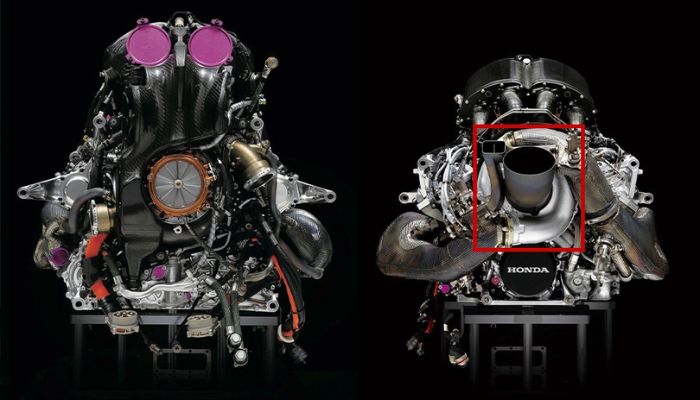
3D printed turbine housing area
Wheelchair Racer’s Handlebars
Honda also produces racing wheelchairs and uses 3D printing to create their aluminum handlebars. What is special about these handlebars is that they can be customized to the athlete. Traditionally, these handlebars were welded together, which made it difficult for them to be personalized. With additive technology, they could not only create handlebars for specific athletes but also have them be weight optimized with mesh grips, a design that can only be made possible with AM. Instead of humans adapting to objects, the objects are adapted to humans, all while improving the performance of a part.
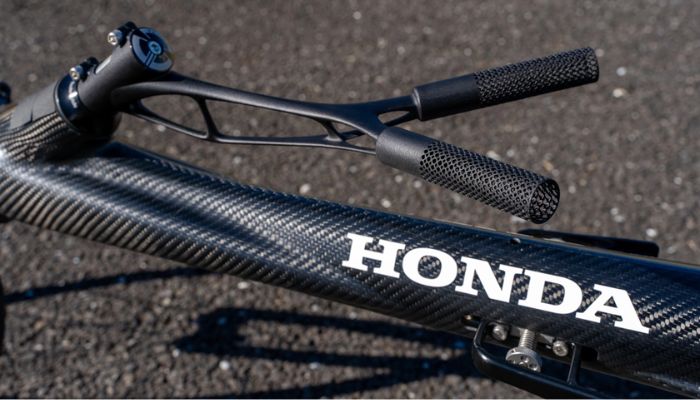
3D printed wheelchair racer handlebars
Honda used topological optimization to create the handlebars, ensuring that they were creating the most efficient structures possible, with no unnecessary components. The handlebars and the F1 car parts are just two examples of how the iconic brand is leveraging AM, but there are sure to be many more use cases to come. To learn more about Honda’s work with AM, click here.
What do you think about Honda’s use of 3D printing? Let us know in a comment below or on our LinkedIn, Facebook, and Twitter pages! For more on automotive 3D printing, click here. Don’t forget to sign up for our free weekly Newsletter here, the latest 3D printing news straight to your inbox! You can also find all our videos on our YouTube channel.
*All Image Credits: Honda
The article has very interesting content.