Hot Isostatic Pressing VS Annealing: Which Heat Treatment Should You Choose?
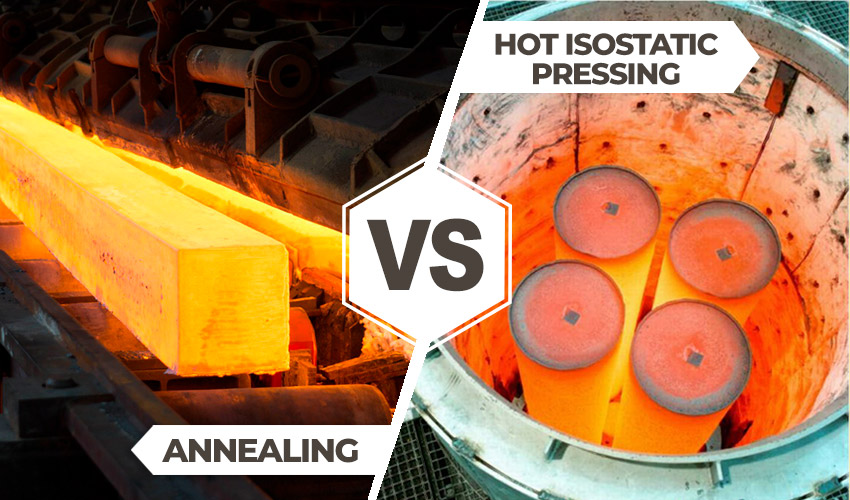
As additive manufacturing continues to industrialize, post-processing is becoming ever more crucial. Through this critical stage, users can improve parts, making them stronger and denser or even giving them specific properties, ensuring they can be used for important end-use applications. Out of all the different types of post-processing, one of the most important for powder bed 3D printing—especially for metals—is heat treatment.
But which heat treatment is suitable for a part? How does it work? To answer these questions, we wanted to look at two commonly used heat treatment processes: hot isostatic pressing (HIP) and annealing.
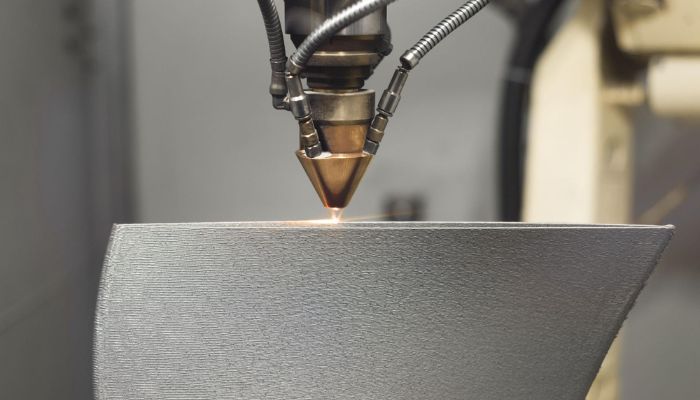
A metal part being additively manufactured (Image credit: Industrial Metal Service)
Both are compatible with metal processes, including LPBF, EBM, binder jetting, DED and even nanoparticle jetting. They also can be used with ceramics and polymers, although to differing extents. They also have many benefits, namely strengthening materials, making them easier to work with and improving material properties. At their most basic, these two techniques will optimize components, but their processes—and specific outcomes—differ.
How HIP and Annealing Work
To understand the differences and similarities between HIP and annealing, we will go over each procedure. Firstly, annealing is a heat treatment that involves heating metals, glass, ceramics or polymers and allowing the material to cool slowly to remove internal stresses. This process alters the physical, and sometimes chemical properties, of a material, increasing its ductility and reducing its hardness to make it easier to work with.
HIP, on the other hand, is when a part is exposed to a combination of high temperatures and gas pressures to eliminate porosity in metallurgy materials. It can also increase the density of many ceramics, turning them into fully dense components.
Remember that the “I” in HIP stands for isostatic. In this case, it refers to the gas, which isostatically applied, meaning it exerts pressure equally in all directions on a material. This results in a uniform force around the object. Similarly to annealing, HIP improves a material’s mechanical properties and workability. The process can also bond together dissimilar materials to make unique parts.
The Annealing Process
Annealing takes place in an annealing furnace. These differ depending on the needs of the materials and the cost, but generally speaking, they can be heated between 300°C – 1000°C (for the higher-end models). The temperature in the furnace must be carefully controlled, which is why these annealing furnaces are often recommended, though if it meets the temperature requirements theoretically any furnace that reaches the right temperature could be used.
Annealing consists of three stages, all determined by temperature parameters that are dependent on the type of material used. To conduct annealing, knowledge of the material and its temperature requirements is critical.
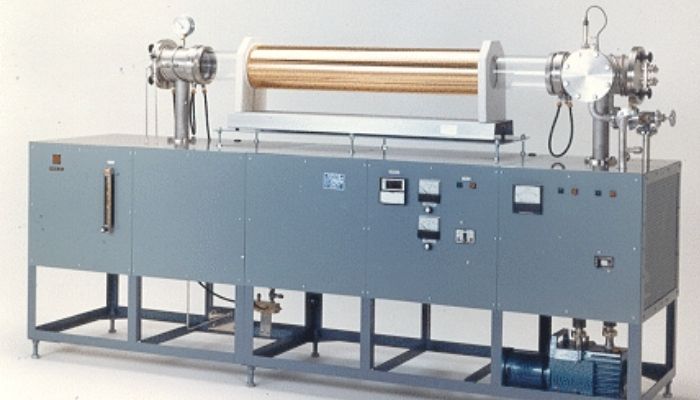
An annealing furnace (photo credits: Thermcraft)
1. Recovery Stage
In the first stage of annealing, the recovery stage, the temperature of the material is raised to above the crystallization temperature so that atoms have the energy to move around. The atoms’ movement helps redistribute and eradicate dislocations (irregularities within a crystal structure), particularly in metals. This makes the metal more deformable and therefore more ductile. The same effect can take place with ceramics but to a lesser degree. Overall, this stage relieves internal stress in the material.
2. Recrystallization Stage
As the material continues to heat up, it eventually reaches the recrystallization stage, which is at a temperature high enough for recrystallization but still below the melting point. Here, new strain-free grains form and grow, replacing space left by previous dislocations.
3. Grain Growth Stage
Once recrystallization is complete, the object can begin to cool, entering the grain growth stage. As it cools, new grains develop and grow. However, the growth of these grains is not random. It is controlled depending on the rate of cooling and the atmosphere in which it cools.
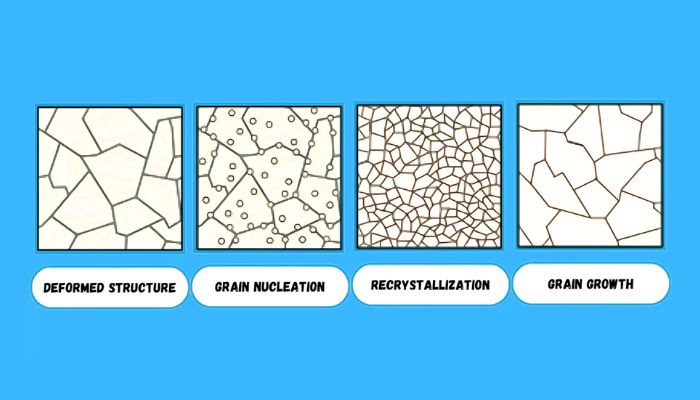
A graphic representation of what happens to molecules during annealing (photo credits: MechDaily)
Depending on the material, annealing could take as little as four hours, or as long as a full day. Also, note that there are several types of annealing. Although not a comprehensive list of all annealing processes, some of the most commonly used include full or complete annealing, isothermal annealing, spheroidizing annealing, diffusion annealing and stress relieving.
Additively manufactured parts, or at least those made with suitable materials, can benefit from all these processes. If deciding between different types of annealing processes, your material and application will be determining factors.
The HIP Process
HIP involves loading parts into a high-pressure containment vessel and exposing them to a high temperature and high isostatic gas pressure. How high? The temperatures can be up to 2,000°C, and the pressure up to 45,000 psi (or about 310 MPa) – about the same pressure as the Mariana Trench 11,000 m deep in the Pacific Ocean. This will cause the material to contract, keeping its initial shape until the pores inside disappear, densifying the part. The process is widely used to relieve stresses in sintered, cast and additively manufactured components
Argon is the most widely used pressurizing gas for the process. Notably, argon is an inert gas, so it will not make the material chemically react. The type of metal used can also minimize the effects of a chemical reaction. Some systems also use associated gas pumping to achieve the necessary pressure level. These gases are applied evenly to the object and maintained for a specific time.
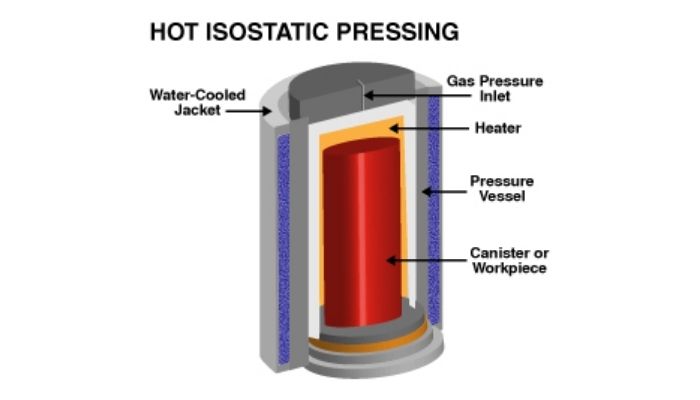
Photo Credits: Metal Powder Industries Federation
The temperature and gas pressure levels, as well as the length of the cycle, are all determined by the type of material used and the desired properties of the final product. The cycles can take eight to twelve hours or days. The process gives the parts a uniform microstructure, improving their properties.
In terms of 3D printing processes, Hiperbaric, a leader in hot isostatic pressing, notes that HIP can be easily combined with laser power bed fusion and EBM for superior parts. Binder jetting, DED, metal material extrusion and metal material jetting (such as in nanoparticle jetting) are also compatible.
Material Compatibility for HIP and Annealing
We mentioned it briefly above, but HIP and annealing do have some overlap when it comes to materials. Namely, both processes can be used with various metals. Furthermore, there do not seem to be restrictions on the metals that can be used for either process.
Take annealing, for example. The post-processing method is compatible with both amorphous and crystalline materials. As such, it can be used for refractory metals, alloys and steel among others. Stainless steel is noted as one of the most commonly used materials for annealed parts but bronze, aluminum, copper and brass are also mentioned.
In HIP, all metals seem to be compatible. This means it also works with most metal 3D printing processes and their compatible materials. It can even be used with difficult-to-work-with materials like nickel superalloys and titanium alloys.
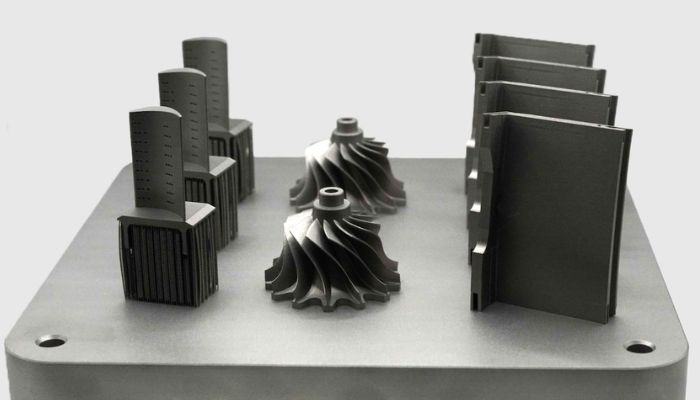
Example of 3D printed nickel superalloy (photo credits: Alloyed Aubert & Duval)
However, metals are not the only compatible materials. Ceramic parts can also be post-processed with either HIP or annealing. Again, it seems as long as the properties of the ceramic material are respected, all ceramics would be compatible with either process.
Something that stands out with annealing, meanwhile, is that it is also compatible with most polymers. As annealing does not involve pressure and instead is related to temperature changes, many polymers used for AM can be annealed. Indeed, annealing has often been cited as a way to improve the strength of ABS parts. Other standard materials which do not have the best properties such as PLA and PETG parts are increasingly being annealed even by makers. This is not necessarily the case for HIP.
Polymer HIP is a less developed area, especially in additive manufacturing. However, some researchers have found that if the temperature is lowered, in a process known as warm isostatic pressing (WIP), materials like nylon or HPP can be post-processed using this method. It however would usually be an outlier, especially considering the cost of HIP compared to annealing. This method is best suited to industrial applications and materials.
Benefits and Drawbacks of the Processes
While annealing and HIP involve different processes, the advantages are similar. Both improve ductility and remove imperfections in the material, whether they are pores (HIP) or dislocations within the crystal structure (annealing). Annealing and HIP essentially remove internal defects and stresses and improve microstructural homogeneity and material properties. Both processes also allow for the consolidation of steps, because many metal 3D printed parts require heat treatment to reduce residual thermal stress anyway.
Annealing, because it causes molecules to migrate within the microstructure, removes strain that may have been introduced while forming the material. The process also prevents cracking and improves machinability. What’s more, with the dislocations in the metal’s crystal lattice rectified, the metal’s electrical conductivity is improved, along with the magnetic properties. Annealing can permit a material to be precisely manipulated for desired traits by selectively heating and cooling and therefore obtaining the desired type of grains, influencing the physical properties of the material.
HIP is great for increasing a material’s density because the process forms metallurgical bonds between different materials through diffusion bonding. These improvements are critical for applications requiring high strength and reliability. The method can also repair defects in a material. For instance, a metal piece with an interior hole could be subject to HIP, so that the hole is filled in with compressed material. In general, both HIP and annealing can help minimize material waste because they can improve existing material, ensuring that it will last longer and reducing the need to acquire more material.
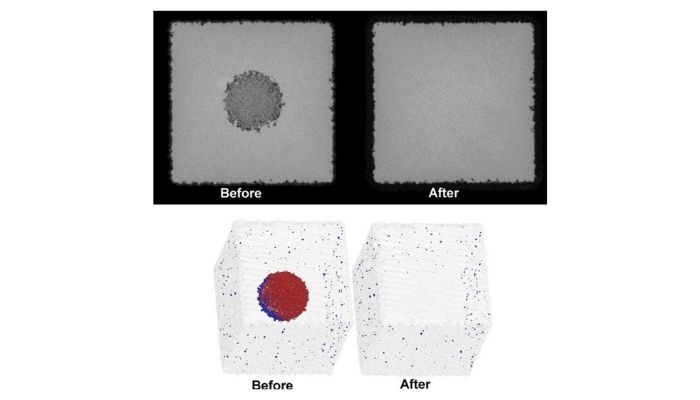
A before-and-after depiction of a material subject to HIP (photo credits: Hot isostatic pressing in metal additive manufacturing X-ray tomography reveals details of pore closure, Science Direct, A. du Plessis a b, E. Macdonald)
A disadvantage to both HIP and annealing is the time it takes to complete the process. Both methods can take over 24 hours, and HIP in particular can take several days. Of course, both technologies are also an added expense. They require upfront costs for equipment and skilled operators, and then they require high amounts of energy for heat. Annealing can also entail forced cooling, which means even more energy. For both methods, the time and cost will greatly depend on the material you are using and the size of your production.
Lastly, both processes can affect the final dimensions of a piece, which is not necessarily a disadvantage, but something to consider. Annealing can cause a change in dimensions because the material’s microstructure will be modified, and this can also happen with HIP because the material is being compressed. The degree of change will depend on factors like the material being used and the parameters for the process.
So, when are annealing and HIP not the answer? If your parts do not require enhanced mechanical properties, it might not be worth it to pay for these processes. HIPing in particular may not be suitable if you have a part with internal cavities or intricate channels that could collapse due to the pressure. HIP is great for when you want a part to be dense, so if you have an additively manufactured part that is already fully dense (like a high-quality laser powder bed fusion part), it would not be necessary.
Applications for HIP and Annealing
In terms of applications, the biggest for both is general post-processing as a way to improve material properties in parts. This means that technically both annealing and hot isostatic pressing could be used in any sector where material properties are important. Although it is necessary to mention that while HIP is relatively inaccessible except at the industrial level, annealing can be done much more easily, opening it up to a wider audience.
There are, however, also specific sectors where these post-processing methods are commonly used. HIP for example was first used in a commercial setting in the aerospace industry. More specifically, it was used to produce jet engine turbine blades. Of course, at the time this was not for parts made with additive manufacturing.
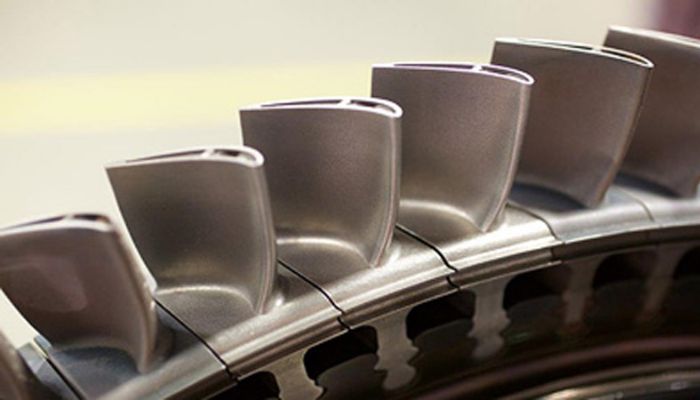
3D printed turbine blades (photo credits: Siemens)
If we want to look specifically at the use of HIP when combined with 3D printing, there are many sectors where benefits are seen. For example, in the medical sector, HIP and LPBF can be used to create hip and knee prostheses using titanium alloys. In aerospace, nickel superalloys are used with LBPF for turbine blades and CoCR for fuel injectors. HIP is also present in the automotive sector as it allows for greater confidence in 3D printed parts. Essentially anywhere where guarantees against pores and internal cracks, often present in 3D printed parts, would be important as well as improved fatigue properties from eliminated stress concentrations.
Annealing can be found in similar industries, since it improves ductility, eliminates stress and reduces the hardness of materials. The brittleness of metals can also be reduced while enhancing magnetic properties. Therefore, applications where those are valued are the best fit.
Key industries for annealing include medical, aerospace, automotive and semiconductor equipment. In aerospace, it is commonly used for aircraft components and can be used similarly for body panels in the car manufacturing sector. Meanwhile, in medicine, it can be used for medical devices like orthopedic implants as it can be useful in forming alloys and metals that are biocompatible with the required strength and durability. Last but not least, since annealing can improve electric conductivity, it can be useful in the electronics industry for making semiconductors or solar cells.
Manufacturers & Price
To complete annealing, you do not necessarily need an annealing furnace. Sometimes, standard furnaces like lab furnaces will be suitable, especially for small-scale or DIY projects, where extreme precision is not necessary, mostly with polymers. However, for cases where you need high precision, a dedicated annealing furnace may be required. Manufacturers of annealing furnaces include Precons, Gasbarre Products, Inc and CM Furnaces, Inc.
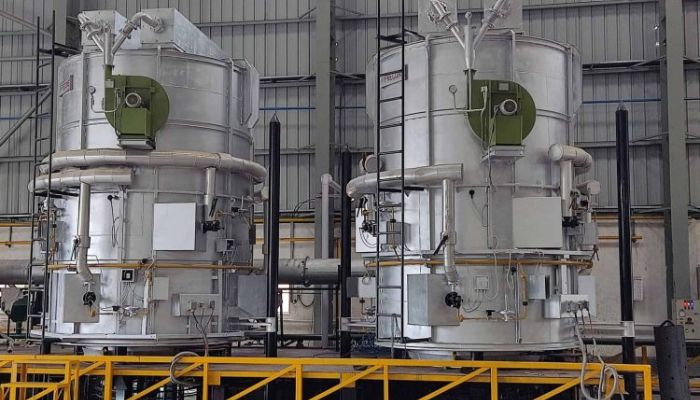
Bell annealing furnaces (photo credits: Precons)
Unlike annealing, HIP demands specialized machines. You could either use an HIP service or consider purchasing a machine yourself. Some notable manufacturers include Bodycote, Kobe Steel, Aalberts, Quintus and ESPI.
The cost of annealing and HIP will depend on various factors like the material you are using, the scale of your production, the requirements for your application, and whether you want to outsource the service or complete treatment in-house.
For annealing, lab furnaces can start at around $500, and industrial annealing furnaces could cost anywhere from $3,000 to upwards of $100,000. Hot isostatic pressing machines follow similar price ranges, with small HIP machines available at around $7000, and large ones could cost hundreds of thousands of dollars or more.
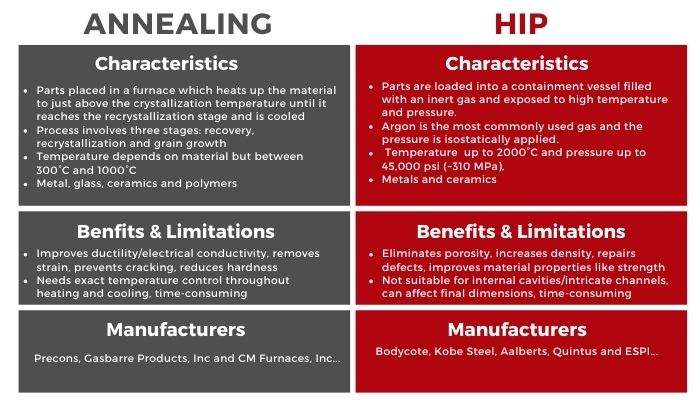
Credits: 3Dnatives
Do you prefer hot isostatic pressing or annealing? Let us know in a comment below or on our LinkedIn, Facebook, and Twitter pages! Don’t forget to sign up for our free weekly Newsletter here, the latest 3D printing news straight to your inbox! You can also find all our videos on our YouTube channel.
*Cover Photo: Annealing (image credit: Aria) and HIP (image credit: ThermalProcessing.Com)