HILOS and its 100% Recyclable 3D Printed Shoes
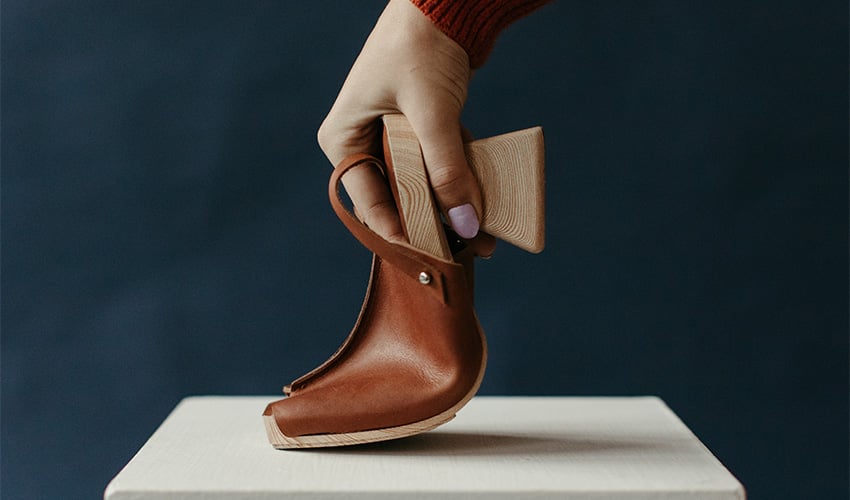
If you’re curious about the different applications of 3D printing, you are probably aware that several companies have been producing footwear using additive manufacturing. Adidas, Reebok, and New Balance are some of the largest companies to use 3D printing to design parts of their shoes. But they are not the only ones. HILOS, a Portland-based startup founded in 2019, makes shoes by combining 3D printing and leatherworking. A finalist for the “Forward AM Innovation Award”, the young company notably offers a collection of 100% recyclable heeled shoes. To learn more about their manufacturing process, and understand what are the advantages of 3D printing in the footwear industry, 3Dnatives met with Elias Stahl, co-founder, and CEO of HILOS.
3DN: Can you introduce yourself and your company?
I’m Elias Stahl, co-founder and CEO of HILOS. Think of us as a new operating system for consumer products, freeing brands from traditional supply chains, allowing them to make circular product completely on-demand, starting with footwear.
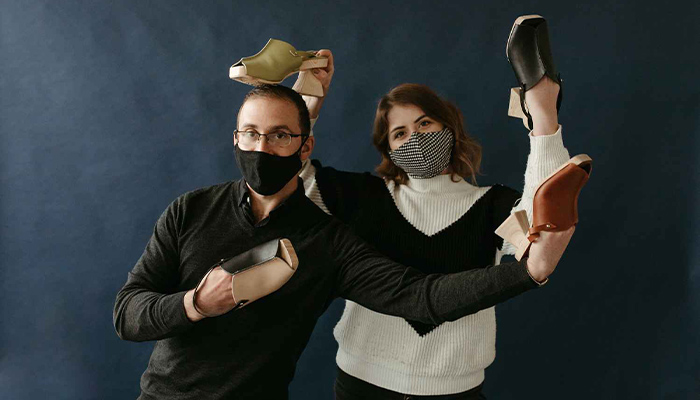
Photo Credit: HILOS
3DN: Why did you turn to 3D printing?
Our mission is to change the way the world manufactures, allowing us to make only what we need, where we need it, and take the product back when done. On-demand manufacturing requires tool-free production capabilities, and 3D printing is one of the most advanced among them when it comes to design freedom and material breadth. New materials also allow for complete recycling.
3DN: What are the advantages of additive manufacturing in the footwear industry?
They are not uniform. The benefits of a 3D printed sneaker are much more subtle than the immediate impact of a 3D printed hoof or mule. The main advantage is that it allows us to introduce new performance materials into what has long been an uncomfortable product category, creating comfort and durability unmatched in the market. Freedom of design and speed to market are also essential factors. We can bring new product lines to market in just two weeks, compared to the industry average of 12 to 15 months. In addition, by making to order, we can offer more sizes and styles, suitable for each foot and customized for each customer.
They are not uniform. The benefits of a 3D printed sneaker are much more subtle than the immediate impact of a 3D printed clog or mule. The main benefit is allowing us to introduce new performance materials into what has generally been an uncomfortable class of product, creating comfort and durability unlike anything in market. Design freedom and speed to market are also critical factors. We can bring new product lines to market in just two weeks, compared to the industry average of 12 to 15 months. Additionally, by manufacturing on-demand we can offer more sizes and styles, tailored to each foot and personalized for each customer.
3DN: What 3D printing process and what materials do you use most often?
We use selective laser sintering. When it comes to materials, we use TPU, mainly due to its strength and flexibility. It is naturally suitable for shoe applications.
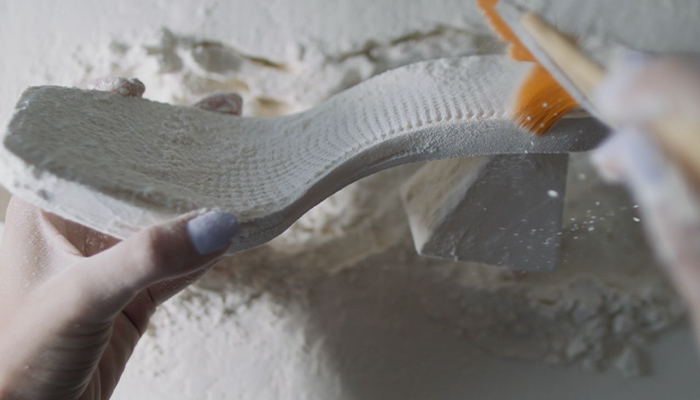
Photo Credit: HILOS
3DN: What is the difference between HILOS printed shoes and conventionally manufactured shoes?
Design, comfort, durability, and sustainability. They outperform in every category. We’ve developed our own rigorous testing regimen and our latest heeled clog has gone through over 200 miles of testing with barely a scratch. Maybe most important though, every shoe we make is truly made-to-order, for you not a shelf.
3DN: What are the future projects of HILOS?
We’re launching our first brand collaboration this Fall, with HELM, and have several others coming up the following Spring. Every season we’ll release new HILOS product lines to demonstrate the possibilities of digitally crafted footwear and are excited to help other brands launch new on-demand, circular product lines.
3DN: A final word for our readers?
I think we are on the cusp of a turning point that will profoundly reshape the way we make things. It’s a movement that needs everyone’s participation – don’t just sit there. We cannot continue to overproduce abroad. I think collaboration will be the key to the success of this movement. I know we wouldn’t have gotten this far, so fast, without the help of other big companies.
I think we’re at the on the cusp of a turning point that will profoundly reshape how and where we make things. This is a movement that needs everyone’s participation – don’t be passive. We cannot continue overproducing overseas for warehouse distribution centers and landfills. I think collaboration will be key to this movement’s success. I know we wouldn’t have gotten so far, so fast, without standing on the shoulders of giants. You can find out more on our website HERE.
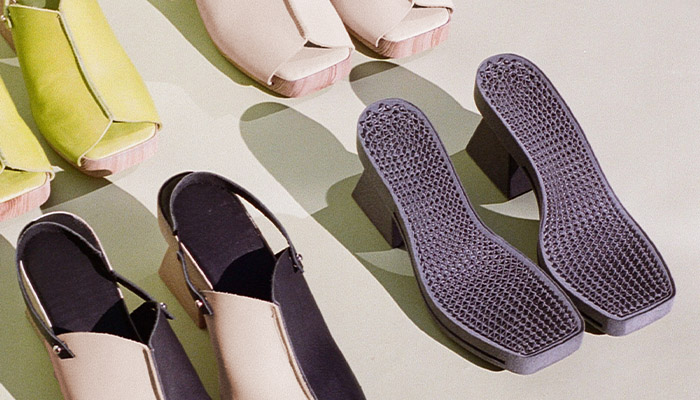
Photo Credit: HILOS
What do you think of HILOS’ 3D printed shoes? Let us know in a comment below or on our Facebook and Twitter pages. Don’t forget to sign up for our free weekly newsletter, with all the latest news in 3D printing delivered straight to your inbox!