How to 3D print high-performance materials (PAEK, PEI…): Experts give their advice!
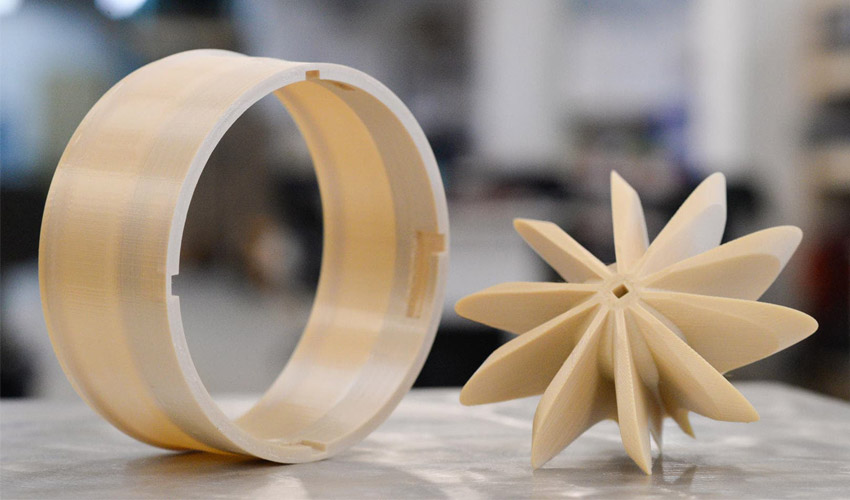
The additive manufacturing sector has seen an expansion in high-performance materials research in recent years, particularly for polymers. These include high-performance thermoplastics, better known by their acronyms, PEEK, PEKK and PEI (ULTEM). We are also seeing the development of new materials such as PPSU or PVDF. These materials are sparking manufacturers’ interest as they offer greater mechanical properties. Some of these materials can even be reinforced with carbon fiber or glass, which gives them interesting properties. Even though the benefits of these materials are numerous, it should be noted that these materials are harder to print with, as they must meet demanding criteria. This is why we come to you today with another expert advice focusing on this family of materials. What are their characteristics? How do we use them in AM? And for which applications? We interviewed three industry experts to give you exclusive advice! Today we focus on 3D printing these materials using FDM technologies; in fact high performance materials can also be printed using SLS technologies. For your information, you can find a previous guide we wrote about these advanced thermoplastics polymers HERE.
Who are our experts?
Our first expert, Dr. Abraham Avalos, is the Head Scientist of AON3D’s 3D printing research department. AON3D is a Canadian manufacturer of high-performance 3D printers. He completed his PhD on polymer synthesis for biosensing applications, before working on fused deposition modeling of PEEK and CF PEEK to gain further expertise in this segment. Our second expert, Nicolas Morand is Kimya’s RDI & Industrialisation Manager at ARMOR: his mission is to design and produce their 3D printing materials, including a range of high-performance materials. Finally, our third expert is Bernd Rauch, Managing Partner of Rauch CNC Manufaktur, one of the leading 3D printing services for high-performance plastics in Europe, who has been involved in additive manufacturing since 2010. Bernd Rauch is responsible for the establishment and overall management of the AM (Additive Manufacturing) division. Our third expert not only has experience with FDM, but also with the SLS process and the “ThermoMelt” process, which is based on a patent from AIRBUS and which Rauch AM has in-house as a pilot user.
- Dr. Abraham Avalos
- Nicolas Morand
- Bernd Rauch
High-performance 3D printing materials: what are the benefits for the industry?
The PAEK family (PEEK, PEKK) and the PEI family have a number of advantages that could be grouped into three categories: good thermal properties, high mechanical characteristics and finally a set of various resistances (to solvents, acids, etc.).
Our three experts agree that thermal resistance is one of the key benefits of these thermoplastics. Dr. Avalos explains, “Withstanding extreme temperature conditions is a primary consideration for people who are looking to integrate high-performance thermoplastics into their manufacturing. PEEK, for example, offers a continuous service rating above 240°C and maintains its stiffness up to 170°C. Thermal resilience also means that some high-performance thermoplastics are autoclavable, which is necessary for many use cases in the biomedical field.” Moreover, this is a characteristic that the automotive sector is particularly fond of Nicolas Morand adds, “The automotive sector is particularly interested because the materials offer a good combination of hardness, durability and thermal resistance.”
High-performance materials are also known for their great mechanical properties. Nicolas explains, “The PAEK family has many interesting mechanical properties such as high rigidity. They make it possible to obtain lightweight parts compared to standard machined parts.” In some cases, a weight reduction of around 40% can be achieved.” This has a direct impact on costs for sectors such as aeronautics: by reducing the weight of a part on an aircraft, for example, its overall fuel consumption can be reduced.
Moreover, these materials are resistant, Dr. Avalos explains in more detail “High-performance thermoplastics stand up to operating conditions that require resistances to various chemicals, radiation and hydrolysis. PEEK and PEKK resist a wide range of chemicals and solvents as well as beta, gamma, and x-rays. Many grades of ULTEM offer particular chemical resistance properties that are useful in the aerospace and automotive industries. ULTEM is significantly less expensive than other high-performance thermoplastics.”
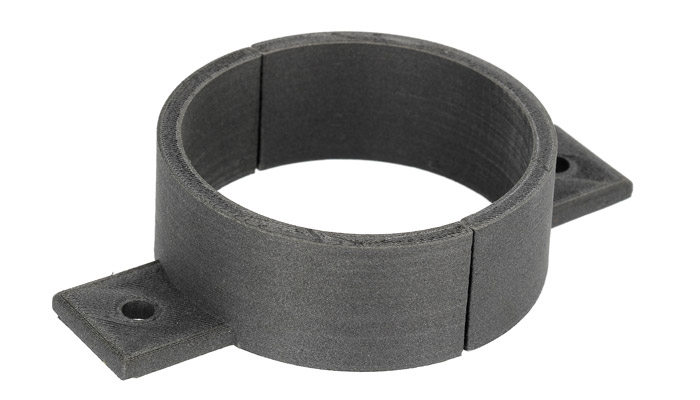
A 3D printed piece with Carbon PEKK from Kimya | Credits: Kimya
In general, Bernd Rauch comments that “High temperature and/or high performance plastics give us the opportunity to open up new fields of application for additive manufacturing that were not possible with previous rapid prototyping materials such as nylon or ABS. High-performance plastics will thus enable more series applications.”
What are the main parameters to consider when 3D printing high-performance materials?
Three temperature environments must be taken into account: that of the extrusion, the printing plate and finally the printing chamber. Dr Avalos explains, “The extruder or nozzle temperature tunes the thermoplastic for strong layer welding. If the nozzle temperature is too high, it can result in part deformation and filament oozing. Too low, and the inter-layer welding is weakened along with poor printing of fine features due to the increased polymer viscosity.” For the bed temperature, he adds, “The bed temperature affects the adhesion of the first printed layer to the bed surface and is usually set to glass transition temperature of the material. Excessive bed temperatures can result in the first layer adhering too strongly to the bed, making part removal almost impossible and potentially damaging the bed. If the bed is too cold, the first layer may not attach strongly, and the part may warp or even shift in the middle of a print run.”
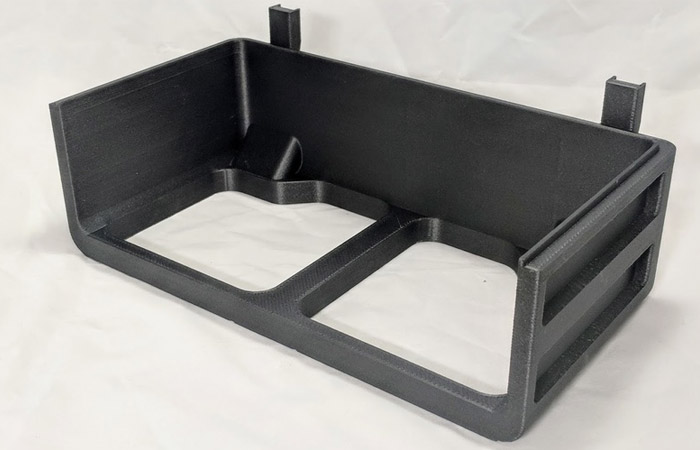
3D printed piece with the AON3D M2 machine | Credits: AON3D
Finally when it comes to the heated chamber, this temperature is key to avoid shrinkage and material change from molten to solid states. “It also reduces the generation of residual stress within the part which, when poorly controlled, can produce cracks, warping and deformation. Chamber temperature is usually kept slightly below the glass transition temperature of the material. More generally, there are particular risks with printing semi-crystalline materials, like PEEK and PEKK. Since they tend to form crystals in environments hotter than their glass transition temperature, this crystallization will lead to shrinkage first, then warping, and finally detachment from the bed, often before the print is even finished.”
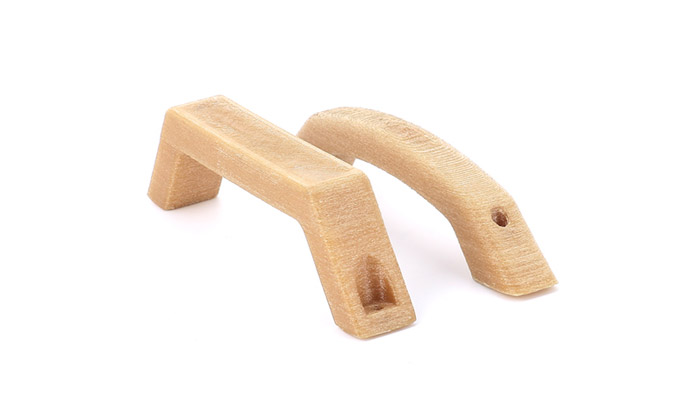
Door handle 3D printed with Kimya’s PEI | Credits: Kimya
What material is best ?
Now that you know more about PEEK, PEKK and PEI, our three experts give you their impressions and some practical advice to help you make your choice. While this will depend a lot on the final application, it remains that some of these thermoplastics are easier to handle than others. Nicolas Morand told us, “PAEKs are still quite expensive, with few compatible FDM printers on the market, even if we are seeing an ever-increasing development of them. These materials feel quite difficult to use, it is important to be well aware of this. However, I would tend to say that PEKK is easier to print than PEEK. Same for PEI, it is easier to handle than PEEK.”
Bernd Rauch confirms that choosing the right material is completely dependent on the application, “There is no “special” application. One simply has to check which material is best suited for the respective application. This also applies to the technology. I am often asked which process is the best. Here, too, one has to say quite clearly: It depends on the application. Each process has its particular strengths and weaknesses. That is why we are always open to new processes. I would like to give the readers a piece of my mind. Components made of high performance plastics are several times more expensive than you are used to for rapid prototyping with inexpensive nylon. Thus, the saving potentials change. For an initial rough test we therefore often follow this guiding principle: Everything that can be conventionally produced by milling or other mechanical processing should also be produced in this way.”
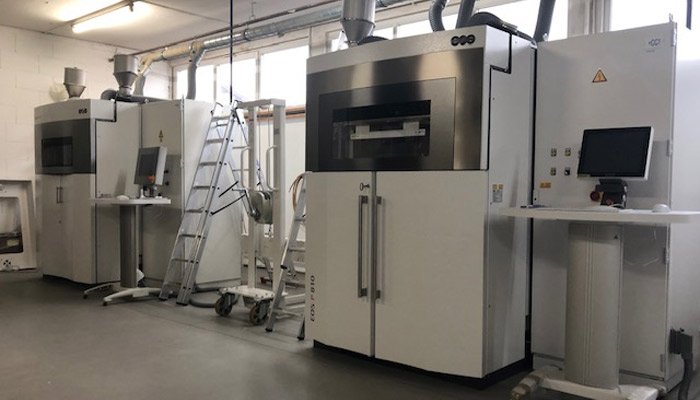
Production unit of RAUCH with the two SLS machines from EOS (P810 in the foreground and P800 in the background)| Credits: Rauch
ULTEM in general is good for the aerospace and automotive industries due to its chemical resistance to many fluids used in these industries. As well as alcohols and weak acids. And as mentioned previously, even though it offers a lower continuous operating temperature, it is also substantially less expensive than other high-performance materials.
Finally, Dr. Abraham Alvos concludes: “Make sure that the industrial 3D printer you choose is able to provide the type of thermal control necessary to obtain high quality parts. Go beyond the machine’s technical data sheet and build a relationship of trust with the manufacturer who has expertise in materials science. It will help you to obtain the best possible results for your application.”
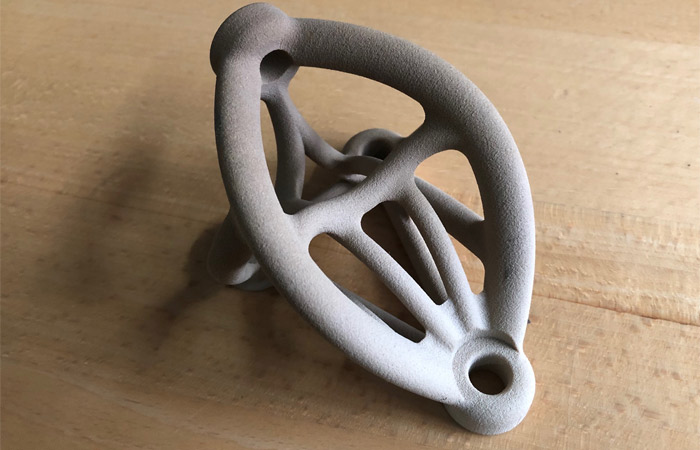
SLS component made of PEEK. The design shows why additive manufacturing is interesting for this | Credits: Rauch
Find more information on these websites: AON3D, Kimya and Rauch.
Was this useful? Let us know in a comment below or on our Facebook and Twitter pages! Don’t forget to sign up for our free weekly Newsletter, with all the latest news in 3D printing delivered straight to your inbox!