From High Fashion to Surgery Robotics, XJet’s Metal 3D Printing Is Enabling Innovation
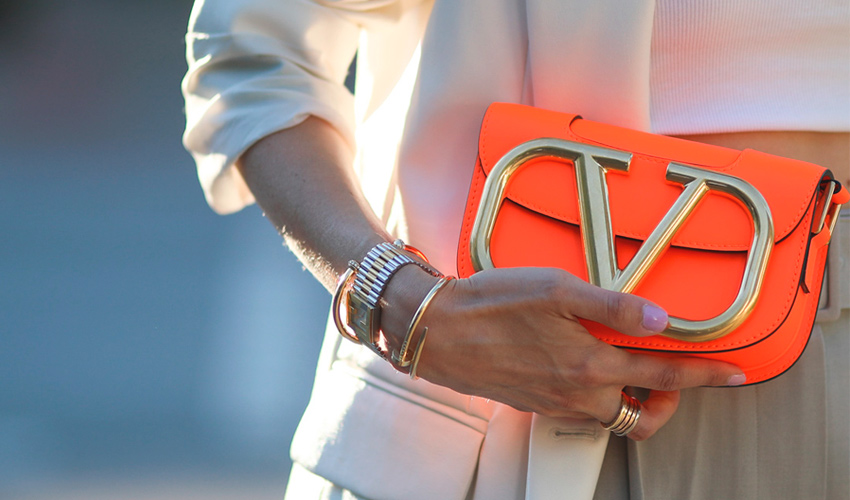
Metal and ceramic additive manufacturing (AM) has grown exponentially in recent years. According to one report from USD Analytics, the global metal AM market size is worth an estimated $4.9B in 2023 and expected to grow at a rate of 22.85% through 2030. Ceramic 3D printing is a smaller field since the materials are more difficult to work with, but still the market is expected to be worth approximately $3.5 billion by 2030. The reason for this growth is simple. Due to the properties of the materials, 3D printing with ceramics and metal allows for heretofore unrealized applications in many fields. This is the case as well for XJet, whose 3D printing technology is making its impact especially on sectors like fashion and healthcare.
This is not the first time we have spoken to you about XJet. The Israeli company is notable for its groundbreaking material jetting technology, Nano Particle Jetting (NPJ), which is pushing boundaries in both metal and ceramic 3D printing of high-quality end-use parts, at scale. NPJ uses inks containing either metal or ceramic solid nanoparticles that are jetted onto the build tray. This process is more environmentally friendly, as it is entirely powderless and involves the use of a fully water-soluble support material. Such benefits are now being recognized in different sectors, including high fashion accessories and medical surgery tools. Applications in these verticals, and more, will be demonstrated by the company and its partners at Formnext this year.
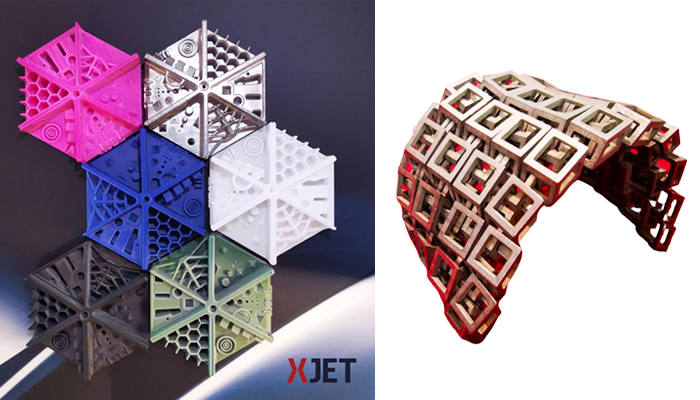
XJet is notable for its groundbreaking technology, Nano Particle Jetting (NPJ)
Reinventing High Fashion Accessories With XJet
For those of you who are familiar with high-precision, direct material jetting in general, it should come as no surprise that NPJ is so uniquely suited for high fashion as well as other wearables such as glasses, ceramic earbuds, luxury and smartwatches. Thanks to the precise nature of the technology, it can create complex and accurate parts with very high surface quality. This is especially critical when making goods that will be worn directly by users.
Normally, high fashion accessories are made using traditional manufacturing technologies as they are tailored to meet the industry’s high requirements for quality and design. However, these technologies have long lead times, and limited flexibility in design and short runs. Some of the traditional technologies involve manual steps, and polluting finishing processes.
This market has been looking for a scalable 3D manufacturing technology that will meet the quality standards of the industry while reducing manual assembly and finishing processes. XJet’s solution fills this role as it is based on an automated three-step process, Print – Wash – Sinter, which offers scalable manufacturing of high-quality parts and complete assemblies. All while allowing users to take advantage of the full benefits of design and run-size flexibility of additive manufacturing.
One example of a metal additive manufacturing technology being adopted for the manufacturing of jewelry and luxury fashion accessories, is clear through the use of XJet’s solution by XOLUTIONS. Composed of Progold, a setter in alloys and master alloys for jewelry manufacturing, and Blucad, a market leader in electroplating solutions for metal accessories, XOLUTIONS is aiming to become a cornerstone of the Italian fashion accessory and jewelry markets. For this reason, it made sense for them to turn to XJet’s printers, specifically the XJet Carmel 1400M system.
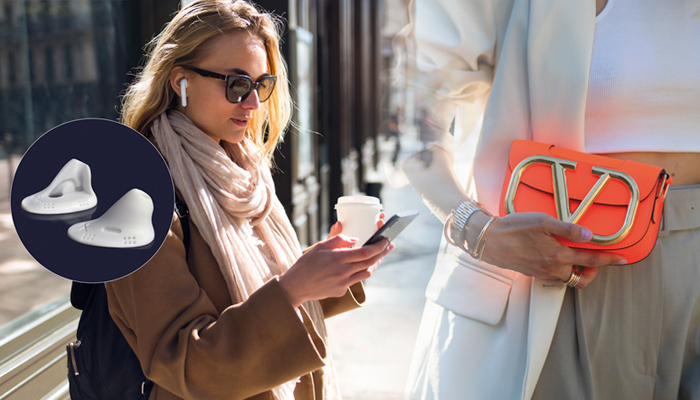
The Israeli company has a multitude of applications for the fashion and consumer goods sector
Damiano Zito, CEO of Progold, explained, “XJet technology fits the needs of the luxury market perfectly. The surface finish and the resolution – crucial for this market – that is achieved by NanoParticle Jetting is a step change above what any other AM technology can deliver, there is just no comparison.” The company will be creating parts in stainless steel and point to not just the freedom of design and fast time-to-market as benefits of adopting NPJ, but also its ability to deliver highly intricate and attractive pieces. The company expects that 3D printing will be a gamechanger for everything from watches to personalized jewelry, allowing “fashion not just to be worn but experienced.”
And this is not the only example. In fact, it could be safe to say that additive manufacturing has ushered in a new era for not just the fashion industry but consumer goods in general. This is due to a few factors but especially for its ability to personalize pieces, such as watches, precisely and quickly. But also, for its immense potential for on-demand production which could reduce the waste generated while keeping the exclusivity of seasonal collections and limited editions.
XJet points to the fact that the ability to manufacture products will reduce waste, aligning perfectly with an evolving consumer mindset. We have all seen the consequences of fast fashion in recent years as well as the growing concern with sustainability and our own environmental footprints. XJet’s NPJ technology is particularly eco-friendly, making it even more effective.
Innovative Ceramic 3D Printing for the Medical Sector
Of course, though metal NPJ is a huge draw for the fashion and luxury sectors, XJet’s ceramic solutions are also notable. Particularly for use in the medical sector, as ceramic parts are highly biocompatible. NPJ also makes their creation easier as often ceramics can be difficult to work with in both traditional methods and other additive manufacturing processes. This has been recognized by leading technical ceramic manufacturer Ceramaret, which has turned to the XJet Carmel 1400C Additive Manufacturing system for medical applications.
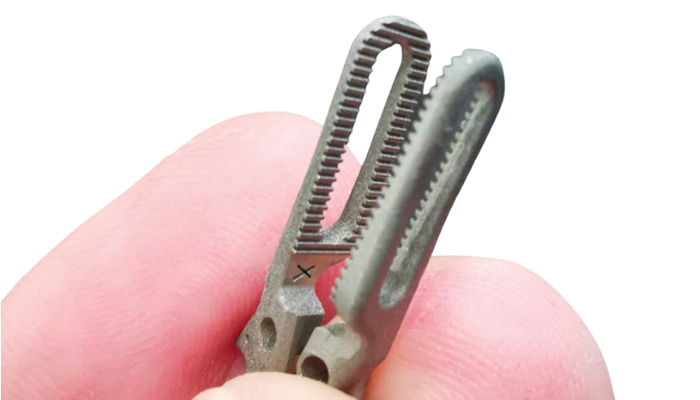
Example of a 3D printed part for the medical sector
Senad Hasanovic, Ceramaret VP of Innovation expands, “XJet technology will provide us with new capabilities, new geometries we can offer our customers, whilst also delivering exceptional time-to-market. We saw parts that are beyond the reach of any other production method. In particular, there were parts with internal shapes or channels down to 300 microns in diameter and near 300 mm long, which either cannot be produced in a single piece or cannot be produced in bulk with our existing techniques.”
In terms of 3D printed parts for healthcare, the company is creating everything from rotary valves and pump elements for fluid handling to endoscope tips and surgical instruments. And they will not be stopping there. Ceramaret will be testing 39 distinct products, consisting of around 300-400 manufacturer parts to see firsthand the value of additive manufacturing in their field. If you would like to learn more about XJet, you can go to their website HERE. You can also meet them at Formnext 2023 where they will be in Hall 12.0 at Booth C139.
What do you think of these applications for XJet’s NPJ technology? Let us know in a comment below or on our LinkedIn, Facebook, and Twitter pages! Don’t forget to sign up for our free weekly Newsletter here, the latest 3D printing news straight to your inbox! You can also find all our videos on our YouTube channel.
*All Photo Credits: XJet