Hi.Stories on 3D Printing for Cultural Heritage
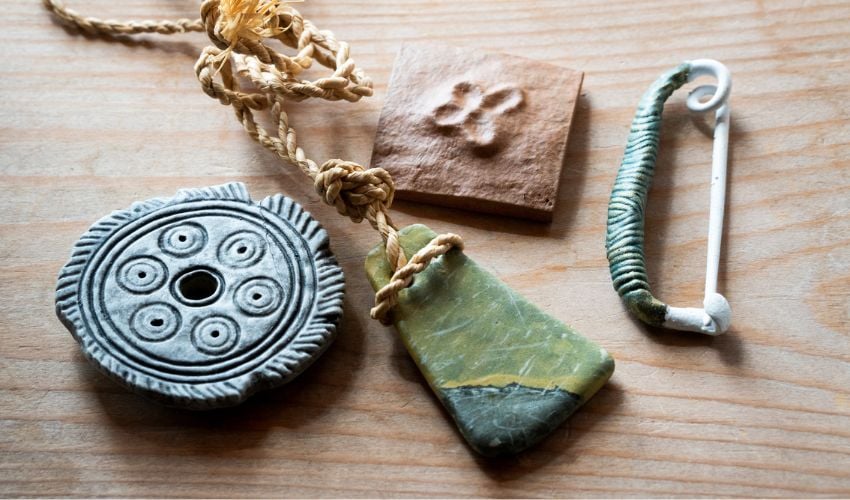
There are so many applications for additive manufacturing in the art and cultural heritage sector. We have covered them in our recent infographic about art and 3D printing, and also wrote a dedicated article about cultural heritage preservation. To learn more, we sought out the expertise of professionals who work in this field every day, creating adapted museum tools, reproductions of works, casts for restoration and more. Riccardo Bonina, CEO of Sicilian company Hi.Stories, told us about the benefits of using 3D printing for cultural heritage, how 3D technologies can make art and heritage more accessible.
3DN: Can you introduce yourself and tell us how you discovered 3D printing?
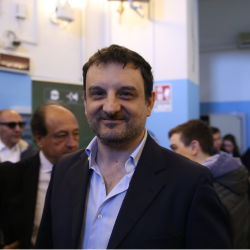
Riccardo Bonina
I am Riccardo Bonina, CEO of Hi.Stories, a company focused on applying 3D technologies to cultural heritage based in Catania, Italy. I and other Hi.Stories partners were curious about 3D printing, and drawn to the technology that, in our opinion, applied to the cultural heritage sector and has a social impact.
3DN: How did Hi.Stories come about, and what is its mission?
Hi.Stories was born in 2017, following participation in the Cultura Crea call for proposals, promoted by Invitalia within the PON Culture and Development ERDF 2014/2020 to foster the birth of cultural and creative enterprises. Our idea was to develop an activity to enhance cultural heritage through technology, leveraging its potential to create interactive enjoyment in cultural centers.
From next year, we will also become a benefit company and, as such, we will promote social impact initiatives to raise awareness and communicate the use of digital tools (and therefore also 3D printing) for accessibility and cultural enhancement.
3DN: For what applications does Hi.Stories use 3D printing?
3D printing is one of the services that we have always offered, precisely because of what was mentioned earlier, which is the promotion of digital as a facilitator of understanding cultural heritage. In particular, in the cultural heritage sector, 3D printing is widely used in the creation of tactile paths for the visually impaired, thus improving museum accessibility. Through a 3D print, accompanied by a caption in Braille, the visually impaired visitor can appreciate the shapes and, in some cases, even the reliefs present in the artifacts in the collection. Not only that, but artifacts can also be 3D printed that are then used as educational materials, or objects from the collections that are momentarily on loan, but of such importance to the cultural institution that it decides to make a copy that can still be displayed.
3DN: What additive technologies and materials do you use?
There is no one-size-fits-all material for printing; it depends on the client’s request and the need for the final output. We tend to favor resin printing when it comes to exhibits where the detail is of great importance, such as for a skylight or pendant, and extrusion printing when it comes to larger volumes or where the detail is a secondary factor.
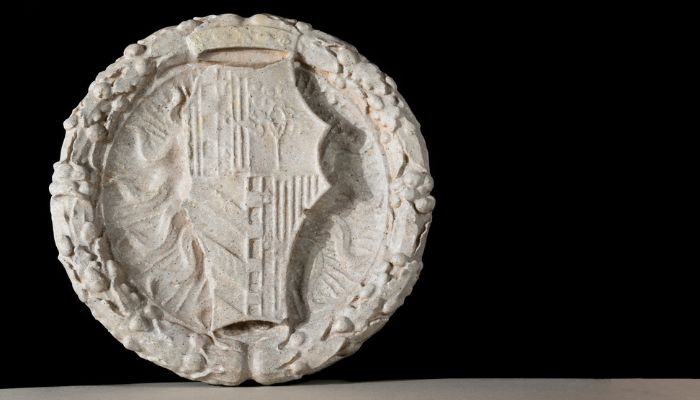
3D printing of coats of arms of the Rocca Roveresca fortress in Senigallia.
3DN: What are the biggest benefits that additive manufacturing brings to your business compared to traditional methods?
Certainly, the main advantage over more artisanal methods is the speed with which prototypes can be made. While 3D printing can hardly be applied to making numerous copies of a single subject, it is excellent for making models that can then also be used by design artisans who want to make their own works with a different and more innovative approach. In our specific field, then, since the print comes from a previously scanned model, there is the added advantage of being able to reproduce the artwork in a manner virtually identical to the original.
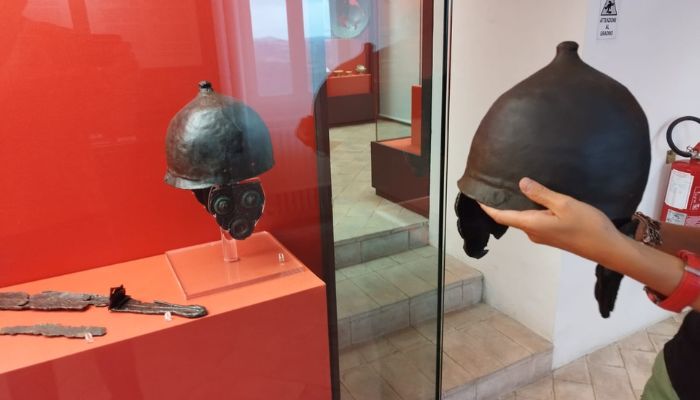
3D copy next to original (inside case) of Montefortino-type helmet (National Archaeological Museum in Arcevia – AN).
3DN: Do you have any current and future projects involving 3D printing?
We have several projects in the pipeline related to the topic of museum accessibility, which certainly today is probably the segment where there is the most demand.
3DN: In your opinion, what is the future of using 3D technologies in the cultural heritage sector?
In the cultural heritage sector, there is a big focus on 3D technologies for its many uses like reproductions to improve accessibility and display copies of artifacts. However, it can also be used in restoration to have casts with which to then proceed with restorative interpolations.
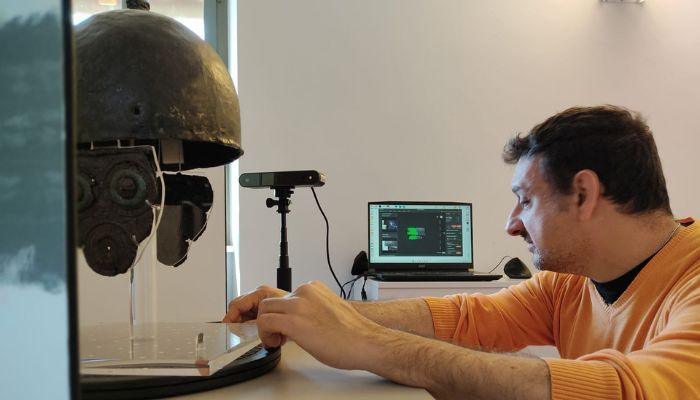
On-site survey work.
3DN: Any last words for our readers?
I would like to emphasize something that is not often considered: making 3D prints also involves craftsmanship. What comes out of the machine has to be perfected in post-processing. In our case, working with cultural heritage, it is often a matter of making a resin print a true artistic object, manually reproducing reliefs or decorations, sometimes even with freehand painting. Therefore, in addition to having a good starting model, in which engravings and bas-reliefs are well highlighted, having an artistically trained person on your team turns out to be an element that can make a difference in the creation of the finished product.
To learn more about Hi.Stories, visit their website HERE.
What do you think of Hi.Stories’ business? Let us know in a comment below or on our LinkedIn or Facebook pages! Plus, don’t forget to sign up for our free weekly Newsletter to get the latest 3D printing news straight to your inbox. You can also find all our videos on our YouTube channel.
*All Photo Credits: Hi.Stories