Henkel and Fortify partner to develop 3D printed injection molding tools
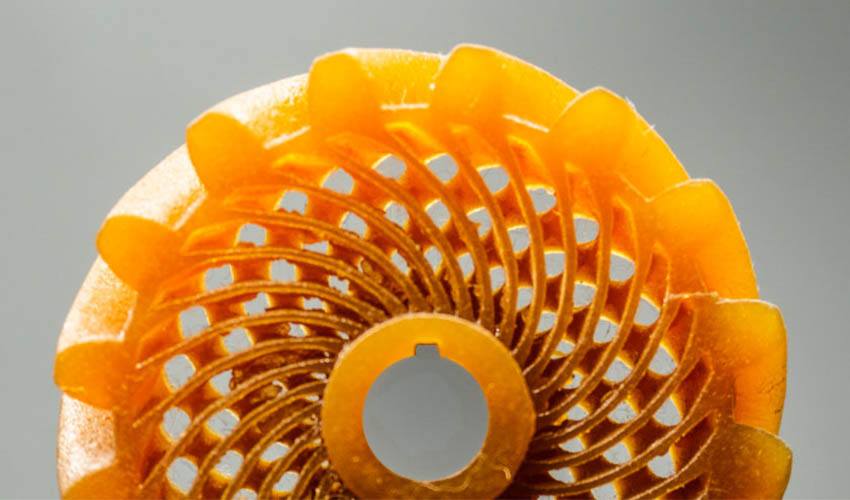
Henkel and Fortify announced a new collaboration to enable high-performance applications in 3D printing. The two companies will be partnering to find innovative solutions for injection mold tooling, prototyping and low volume production. Fortify is well known in the 3D printing industry for its patented DCM (Digital Composite Manufacturing) platform that can produce high-resolution custom composite parts. Through this partnership, the German chemical group has developed custom technology to create durable, high-temperature, high-modulus resins for Fortify’s platform.
Composite 3D printing is gaining momentum, especially for industrial applications. Fiber-reinforced polymers can produce strong yet lightweight parts that showcase high performance. In fact, Henkel claims that injection molded parts that are reinforced with fibers typically show 20 to 100% increases in strength, stiffness and heat deflection temperature (HDT) – definitely interesting for the industry. Joshua Martin, CEO and Co-Founder of Fortify adds: “The Fortify platform enables our customers to leverage materials that weren’t conceivable, yet alone practical on other platforms. With Henkel’s assistance, we are pushing this technology forward and solving the customer problems we expected as well as discovering exciting new opportunities.”
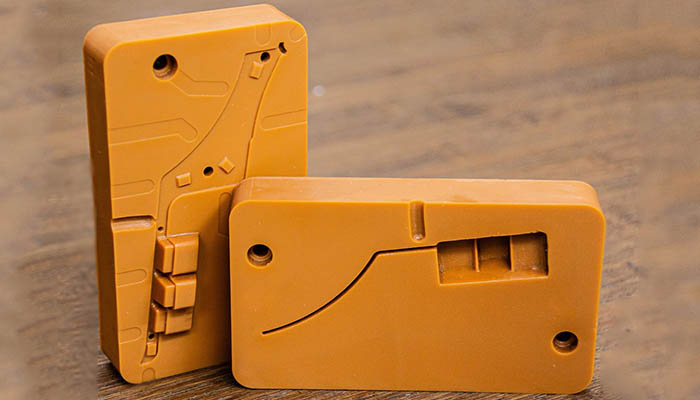
A 3D printed tool by Fortify which is used to mold an automotive part
Generating more industrial applications
3D printed injection mold tools are one application where Fortify is focusing in its partnership with Henkel. By replacing traditional metal tooling with inserts that are 3D printed, molders can cut weeks or months out of their schedules while saving a significant amount of costs. While this application has been pursued by others, the step change in performance from reinforced material is the key to success in demanding applications.
Creating a mold using traditional manufacturing techniques is a lengthy and costly process. When it comes to prototyping or producing parts in small runs, these tooling cost and time are major barriers for manufacturers. The aim of the partnership is to offer an alternative: 3D printed molds that utilize Henkel’s resin. Karlos Delos Reyes, Vice President of Applications and Co-Founder at Fortify explains: “As we help injection molders reduce the expense and time involved with producing molds, they can quickly react to new opportunities.”
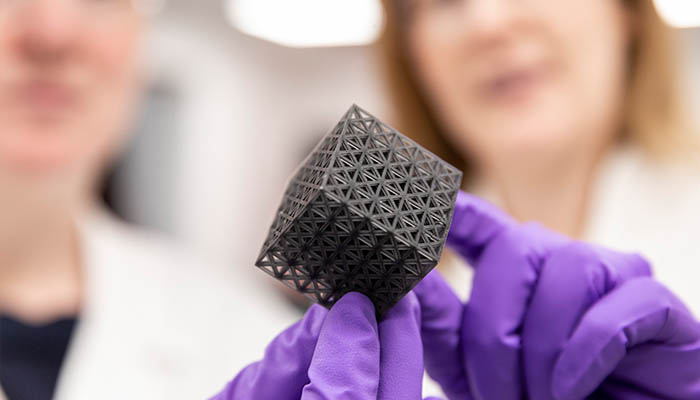
A 3D printed sample of Henkel’s resin
Finally, Fortify will begin field beta testing its 3D printers in the spring of 2020. Beyond injection molding, Henkel and Fortify are looking at several end use part applications where their combined solutions offer a significant advantage. You can find more information HERE.
What do you think of this partnership between Henkel and Fortify? Let us know in a comment below or on our Facebook and Twitter pages! Sign up for our free weekly Newsletter, all the latest news in 3D printing straight to your inbox!