Heat Treatment in 3D Printing: All You Need to Know

Post-processing is a key stage in additive manufacturing. Indeed, there are a number of different methods used in the industry, which differ depending on the 3D technology used: depowdering, removal of supports and coloring, among others. Now it’s time to explore yet another post-processing method in additive manufacturing: the heat treatment of 3D printed parts.
This can take several forms, depending on the desired results, the material used and the preferred technology. These include sintering, annealing for metals, curing and hot isostatic pressing. This type of post-processing has a clear goal: reducing the internal stresses of a 3D-printed part and improve its mechanical properties. Depending on the technique chosen, different results will of course be obtained, but the aim is to influence the residual stresses that may arise during printing.
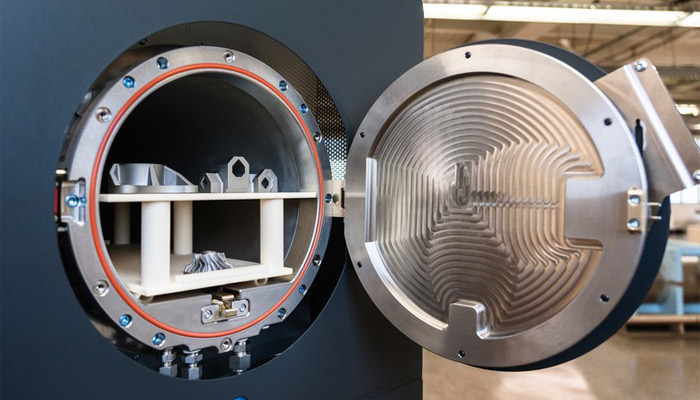
A range of equipment is available for heat treatment in additive manufacturing (photo credits: Markforged)
In additive manufacturing, the parts produced are subjected to different temperatures and undergo heating and cooling phases of varying degrees, depending on the printing process chosen. These phases have a direct impact on the parts, which accumulate residual stresses. Heat treatment after printing is therefore crucial, not only to eliminate these residual stresses, but also to influence the mechanical characteristics of the parts, such as bending strength, ductility and final hardness. We took a closer look at the different heat treatment methods used and what they do.
Sintering, a Critical Post-Processing Step for Metals and Ceramics
Sintering is one of the heat treatment methods that can be used in additive manufacturing. Please note that sintering is more of a step in the manufacturing process than a post-processing method in its own right. In fact, it is mandatory when using binder jetting or indirect 3D printing. By the latter, we mean methods that use plastic filaments incorporating metal particles.
By sintering the green part obtained after printing, we get rid of the binder and solidify the metal particles together. To achieve this, a sintering furnace is required: the temperature is raised to just below the melting point of the material used. This technique removes the original powder particles, reduces the porosity of the parts and increases their hardness. It is mainly used with metal or ceramic powders.
Take into account the phenomenon of shrinkage of the final part. During sintering, the particles of material bind together and take the place of the binder, reducing the size of your original part. This reduction is of the order of 15 to 20%.
Curing, Heat Treatment for Polymer 3D Printed Parts
If we now turn our attention to polymers in additive manufacturing, there is one particular heat treatment technique used for parts in order to improve their final properties. This is of course curing, which is mainly used in resin 3D printing.
Resin is made up of several monomers that are not bonded together in their liquid state. When exposed to a UV source, these same monomers bind together to form the desired part. However, after printing, some areas will not be optimally cross-linked, risking compromising the overall strength of the printed component. This is where the curing stage can be of interest, as it will enable all possible cross-linking to take place.
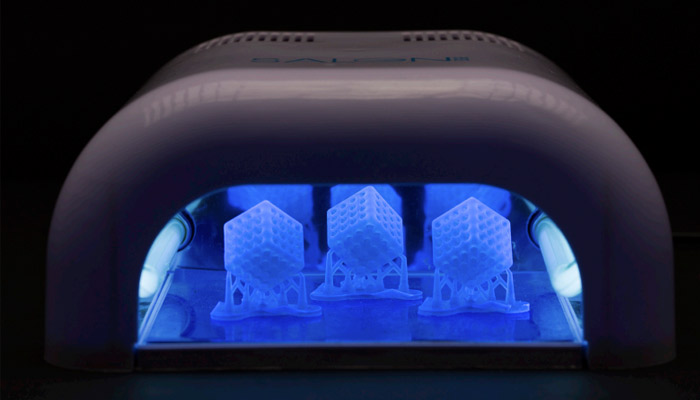
Curing is a common heat treatment method for parts made with resin 3D printing (photo credits: Formlabs)
Once the part has been created, it is cleaned to remove excess non-photopolymerized resin and printing supports. The part can then be placed in a suitable machine – generally, 3D resin printer manufacturers offer their own curing station, like Formlabs and its Form Cure solution. This is a UV chamber that hardens the printed part and gives it its final properties. This reduces fragility and the risk of breakage. Curing also fixes the resin’s color and makes it safer to handle.
The result is a more durable part, which is crucial in many sectors. Factors such as the type of resin used and the size of the part will have a direct impact on this heat treatment stage. More often than not, the larger the part, the longer it will take to harden. This is a factor to be taken into account in your manufacturing process.
Annealing as a 3D Printing Heat Treatment Method
This method of heat treatment involves exposing the 3D-printed part to a certain temperature, the heat can be higher or lower depending on the material used. Once heated, it is gradually cooled to increase its strength. This technique is widely used for metals, but also for glass. Some plastics can also be annealed, such as PLA and PETG. For other thermoplastics, such as ABS, annealing is not appropriate, as the heat will cause warping.
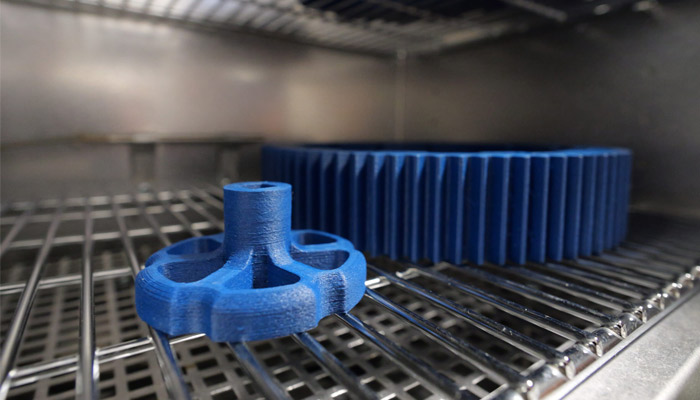
Some thermoplastics are compatible with annealing, enabling it to be used as a heat treatmen method (photo credits: UltiMaker).
But how exactly does it work? In concrete terms, annealing involves heating the material to a temperature higher than its crystallization temperature, but lower than its melting point. With polymers, this will enable the molecules to reorganize, thus improving the stability of the final part. In the case of metals, annealing allows the grains to increase in size through recrystallization.
In both cases, the duration of annealing will influence the structure of your final part: the longer it is exposed to heat, the more its structure will change. For example, plastic components can become smaller after annealing, as heat accelerates their shrinkage. This is an important point to take into account when designing your part. Note that annealing in 3D metal printing improves the ductility and strength of the parts created. This technique is particularly used with steel.
Heat Treatment Methods for Metals
We’ll conclude our guide with a few additional heat treatment methods used specifically for metals. The first is hot isostatic pressing (HIP). It combines very high temperatures and isostatic inert gas pressure, which, when applied simultaneously, increase a part’s density and strength. In concrete terms, the part is enclosed in a high-pressure containment vessel and exposed to this heat/pressure combination. This removes all internal voids and residual porosity. This technique is also compatible with ceramics.
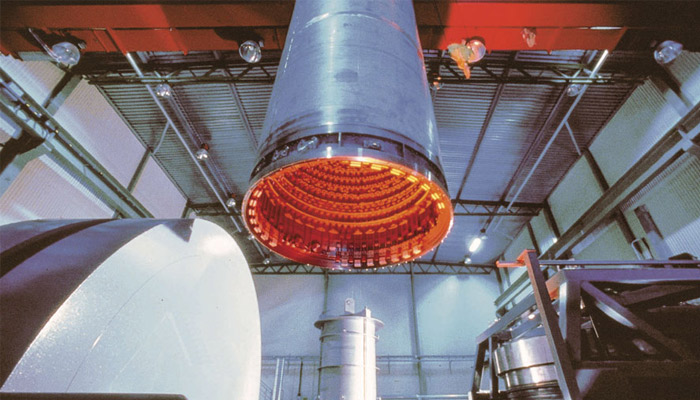
The HIP tank is installed on top of the 3D-printed part (photo credits: Bodycote).
3D-printed metal parts can also be strengthened by quenching: this involves heating the part to a very high temperature and then cooling it very quickly. This will have an impact on the component’s microstructure. Quenching usually requires the use of a fluid to cool the part. There are many other heat treatment methods now compatible with additive manufacturing, and the list is not exhaustive. But you now have a good overview of the techniques available and their importance! Don’t forget to take certain parameters into account right from the design phase, such as part shrinkage.
If you have any questions or comments, please let us know in the comments section below or on our Linkedin, Facebook, and Twitter pages! Don’t forget to sign up for our free weekly Newsletter here, the latest 3D printing news straight to your inbox! You can also find all our videos on our YouTube channel.
*Cover photo credits: Mark3D