GREENFILL3D on Transforming Production Waste into 3D Printing Materials
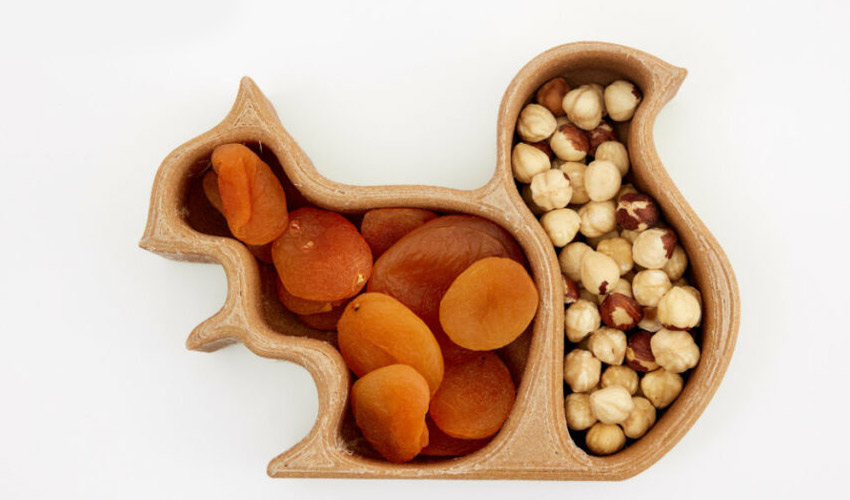
We have previously told you about GREENFILL3D, a Polish startup that develops ecological and biodegradable materials for 3D printing. Notably, it developed a wheat bran-based filament, GF3D Branfill3D. This material was created in accordance with modern concepts of zero waste and circular economy: wheat bran is a production waste from the manufacture of pasta. From this filament, the startup 3D printed its own POS (Point of Sales), on which pasta packages will be presented and sold. This project is developed in collaboration with the MASPEX group, one of the largest food producers in Europe. To find out more about the company’s work and its filaments, we met its director, Pawel Slusarczyk.
3DN: Could you introduce yourself and your connection to 3D printing?
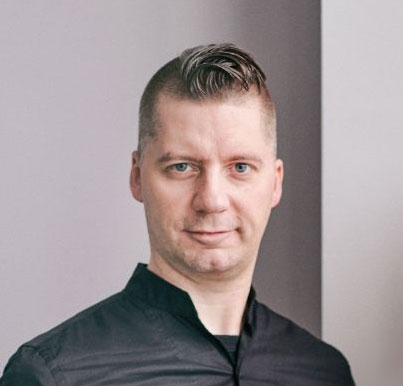
Pawel Slusarczyk
My name is Pawel Slusarczyk and I have been working in the 3D printing industry for over 9 years. In January 2013, I founded Centrum Druku 3D, the largest 3D printing site in Poland, which has helped to develop the Polish additive manufacturing industry. All major Polish companies, such as Zortrax, Sinterit, Zmorph, Omni3D, 3DGence, Technology Applied, Spectrum Filaments, Fiberlogy and many others, made their debut on our site. I have many years of experience in implementing innovative projects – in 2019, we created our own 3D bioprinters – called SKAFFOSYS, and subsequently launched a 3D bioprinting lab in Poland. In 2020, this project was detached from our company and continued by another independent team.
3DN: How did the idea to create GREENFILL3D come about? What is its mission?
In 2021, we established a cooperation with MASPEX Group, the largest food producer in Poland and one of the largest in Europe. MASPEX Group contacted us with the idea of creating advertising materials from their waste. The company had different post-production waste, both organic (vegetable waste, wheat bran, etc…) and cardboard and plastic. In the end, we decided on wheat bran, from which we decided to produce a filament for FDM / FFF technology. In July 2021, we signed a formal cooperation agreement and started the research and development process.
We decided to immediately separate this project from CD3D and, in July 2021, we created a new independent company: GREENFILL3D. We also participated in an EU project – ScaleUp, which provided us with adequate funding for research and development. Furthermore, we were invited to cooperate with PAN (Polish Academy of Sciences), the largest and most prestigious scientific institution in Poland, with whom we already collaborated on the 3D bioprinter project. Together we developed a unique chemical mixture of wheat bran, PLA and other chemical compounds, all of which are fully biodegradable!
In conclusion, our mission is to search for environmentally friendly materials, with a focus on bioplastics that are truly biodegradable and compostable. At the same time, we are looking for applications where the use of these materials is functional and makes sense – we are aware that at the moment bioplastics cannot replace, for example, polyamides or polycarbonate. We are looking for objects that can be printed, for example from wheat bran, but that remain functional. We do not want to impose bioplastics where they are not suitable.

This decoration and kitchen utensil were both printed using the wheat bran filament (photo credits: GREENFILL3D)
3DN: What are the main benefits of turning wheat waste into filament for 3D printing? What are its limitations?
Wheat bran has some fantastic and amazing properties. At the beginning of the project, we were very concerned that the filament would be brittle and break, but because the bran is fibrous, the finished 3D prints are flexible, not like polypropylene or TPU, but they are not easily broken. While testing our stands, we loaded a shelf with a few pounds on it – over the course of the week, the shelf and sidewalls bent a lot, but did not break. Also, when we rotated the shelf 180 degrees and applied the same weight to it, it straightened out in 2-3 days, then bent on the other side. But there was no evidence of cracks.
In addition to the physical properties of wheat bran in filament form, the idea of using production waste and turning it into a 3D printing material, from which we create supports to promote the pasta from which it is made, is fascinating.
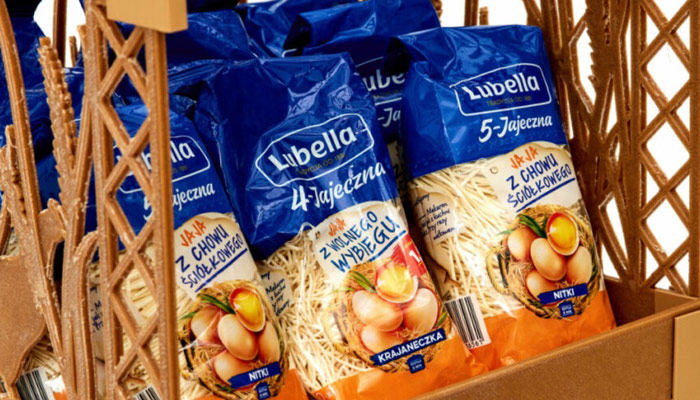
The filament is used to print displays for pasta (photo credits: GREENFILL3D)
As for the limitations, they are very few and I think they are easy to solve. For the moment, you have to use a 3D printer with a larger diameter nozzle: 0.5 – 0.6 – 0.8 mm; of course, we are able to print the filament with a diameter of 0.4 mm, but with larger diameters, we are sure that the material will come out correctly. At the moment, we only have a 1.75 mm diameter filament, which is not very suitable for the Bowden extruder, so we only recommend the direct extruder. However, we are planning to use a 2.85 mm filament and will test it, for example, on an Ultimaker or BCN3D, and I am sure that the problem with the Bowden extruder will be solved.
3DN: Do you at GREENFILL3D plan to develop other filaments from food waste in the future?
Yes, of course. At GREENFILL3D, we have a detailed roadmap for future R&D actions. First, we want to increase the percentage of wheat bran use to 40% at the production scale, and then develop something new. We will probably continue to use wheat bran, but the other components will be different. There are a lot of interesting bioplastics to try.
3DN: Where do you see the future of zero waste in 3D printing?
Everywhere. Over the past few months, I’ve been exploring in depth the subject of producing plastics from environmentally friendly materials and I can assure you that there is not a single major chemical company in the world that is not researching this area. We are on the verge of a major revolution in plastics, many of which are based on the concept of zero waste. The effects will be visible in a few years but it is certain and inevitable.
For now, industrial 3D printing is far from green. Everyone is working to replace metals with high-performance plastics, but they are not forever. Recycling of these plastics seems better in theory than in practice: worldwide, only 10% of plastic waste is recycled, with the rest going to landfill or floating in the seas and oceans.
Until this problem is solved on a large scale – and we’re talking about giant waste factories here – GREENFILL3D believes that the best solution is bioplastics, which are designed to break down naturally from the start. Of course, all of this applies not just to 3D printing, which remains a niche, but to all plastics worldwide.
3DN: Any last words for our readers?
Be responsible when 3D printing at home or at your workplace. If you don’t absolutely have to, try to use environmentally friendly materials. Also think about the common use of plastics in everyday life. People worry about dying from COVID-19, when the real threat is the plastic that floods us everywhere. This is one of many real threats that almost no one is aware of. Read, think and consider making some changes. Don’t wait for others to do it. You can learn more about our projects on our website HERE.
Que pensez-vous des développements menés par GREENFILL3D ? N’hésitez pas à nous dire ce que vous pensez dans les commentaires de l’article. Retrouvez toutes nos vidéos sur notre chaîne YouTube ou suivez-nous sur Facebook ou Twitter !
*Cover Photo Credits: GREENFILL3D