Gravity Industries, The Company That Lets You Fly With 3D printing!
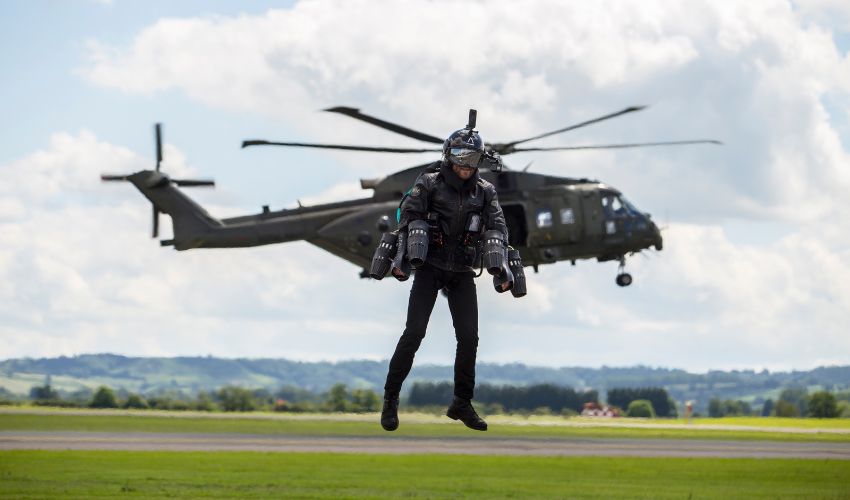
It is possible to fly… no, really! We have always heard that in the future it would be possible to fly and the future has arrived, it is today. This has been made possible thanks to today’s featured company: Gravity Industries; and, of course, the role of additive manufacturing. Who are the lucky ones who will be able to fly? You will be able to do it yourself thanks to the training and experiences they offer. For the development of the Jet Suit, the suit that allows you to fly, they have conducted numerous tests with all 3D printing technologies with a clear winner. Here, you can learn more about the work done by this company with the interview we conducted with its chief designer Sam Rogers!
3DN: Can you introduce yourself and explain your involvement with additive manufacturing?
I’m Sam Rogers, lead designer for Gravity Jet Suit. I worked on some of the first 3D printed copper rocket engines for space shuttles, designing combustion chambers and turbo pumps to be optimally suited to 3D metal printing. This led me to join Gravity in its early stages, where we have applied 3D printing to our fully 3D printed Jet Suit.
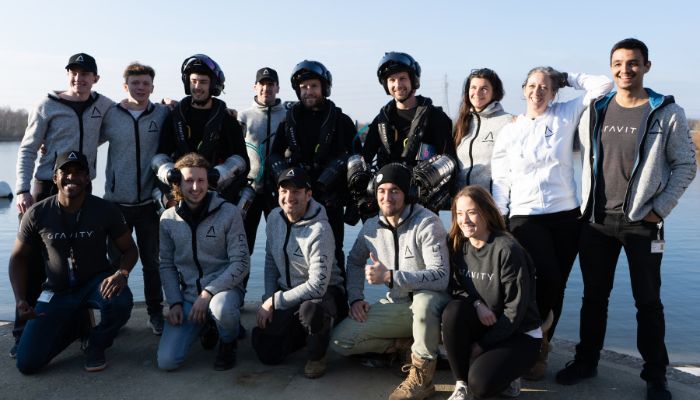
The Gravity Industries team
3DN: How did the Gravity Industries adventure begin?
In 2016, Richard Browning decided to experiment with augmenting the propulsion of the human body, just for the pleasure of the challenge and to explore whether a human’s natural balance and control system could be applied to control thrust mounted on limbs, in this case turbojet engines. Through a series of iterations, mounting engines in the legs, back and arms, he arrived at the design of the Jet Suit we fly today.
3DN: What materials do you work with, what technology do you use and what is the manufacturing process like?
The Jet Suit is almost entirely 3D printed in polypropylene, nylon and aluminum using SLS and DMLS processes. I think we have experimented with almost every 3D printing process available, and SLS has been a clear winner for us because of its design flexibility, surface finish and robustness.
3DN: What advantages and limitations do you find in 3D printing?
3D printing allows us to easily improve the Jet Suit design with each iteration, while offering tremendous flexibility in terms of aesthetics and internal structures. We can optimally design for assembly, reducing the number of manual processes to build each Jet Suit. It’s quick and easy to innovate and iterate.
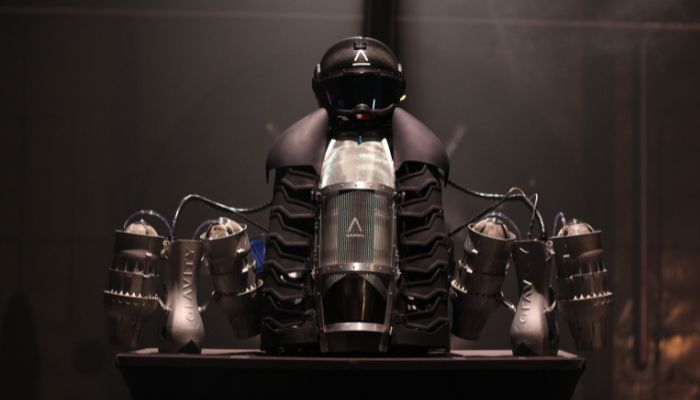
The 3D printed Jet Suit.
3DN: What are your future developments at Gravity Industries?
It’s a secret, we’ve come a long way in making the Jet Suit into a tool, a robust and rugged product that is easy to use, which is essential for any device to be used in real-life situations. We will make the suit easy to use, tougher and, most importantly… it will look good.
3DN: Any last words for our readers?
One of Gravity’s main goals is to inspire people about what is possible. We also organize flight training courses for those who want to learn to fly by themselves. You can take and learn more about the latest test flights on our website HERE and follow us on social media.
What do you think of Gravity Industries? Let us know in a comment below or on our Facebook and Twitter pages. Don’t forget to sign up for our free weekly newsletter, with all the latest news in 3D printing delivered straight to your inbox!
*All photo credits: Gravity Industries