General Motors relies on additive manufacturing to reduce the weight of their cars
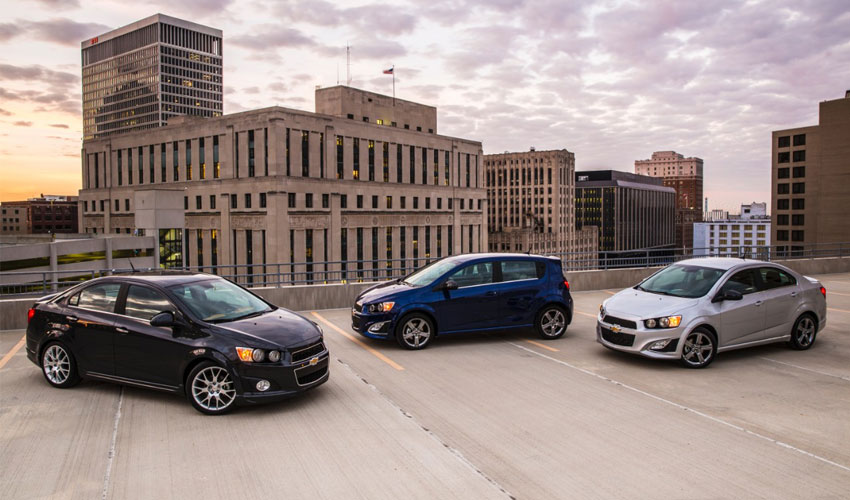
US automaker, General Motors (GM), has announced a new partnership with Autodesk. The goal of GM is to design 3D printed parts for their new electric cars to make them lighter and more efficient, all at a lower cost. The manufacturer hopes to build 20 cars by 2023. GM is believed to be one of the first in the United States to use Autodesk’s generative design technology.
Electric cars are becoming increasingly popular in the automotive market, as people continuously look for new solutions to help reduce carbon emissions and the overall environmental impact of vehicles. This is something that additive manufacturing is also working towards, with many initiatives already being developed using 3D technologies to design electric vehicles. General Motors could well follow this trend as they have said that they will commercialize new electric vehicles by 2021.
GM explains that the key lies in the weight of the parts; the more it will be reduced, the more it will be able to maximize energy efficiency. So when we know that additive manufacturing can significantly lower the weight of components, it is not surprising to see that General Motors is looking to bring this technology into their newer vehicle designs. Demonstrating this, GM presented a 3D printed stainless steel seat bracket, that was manufactured with the help of Autodesk.
“Generative design is the future of manufacturing, and GM is a pioneer in using it to lightweight their future vehicles,” said Scott Reese, Autodesk Senior Vice President for Manufacturing and Construction Products. “Generative technologies fundamentally change how engineering work is done because the manufacturing process is built into design options from the start. GM engineers will be able to explore hundreds of ready-to-be-manufactured, high-performance design options faster than they were able to validate a single design the old way.”
By manufacturing it in the traditional way, such a piece would have required eight different components, coming from several suppliers. Through additive manufacturing, the seat support would consist of one piece only, made directly from a 3D digital model. A method that will make it 40% lighter and 20% stronger; in fact, when there are several components, the joints increase the final weight of the part but also reduce its strength.
General Motors’ Director of Design and Additive Manufacturing, Kevin Quinn, says 3D-printed parts will appear in high-end vehicles by the end of next year. He goes on to explain that their main challenge today is to produce on a larger scale. Within 5 years, however, the manufacturer hopes to manufacture thousands or even tens of thousands of parts for mass production, as the technology continues to improve.
Find more information on General Motor’s official website.
.
What do you think lies ahead for the future of 3D printing in the automotive sector? Let us know in a comment below or on our Facebook and Twitter pages! Don’t forget to sign up for our free weekly Newsletter, with all the latest news in 3D printing delivered straight to your inbox!