Genera’s industrial G2/F2 system streamlines all steps of the AM workflow
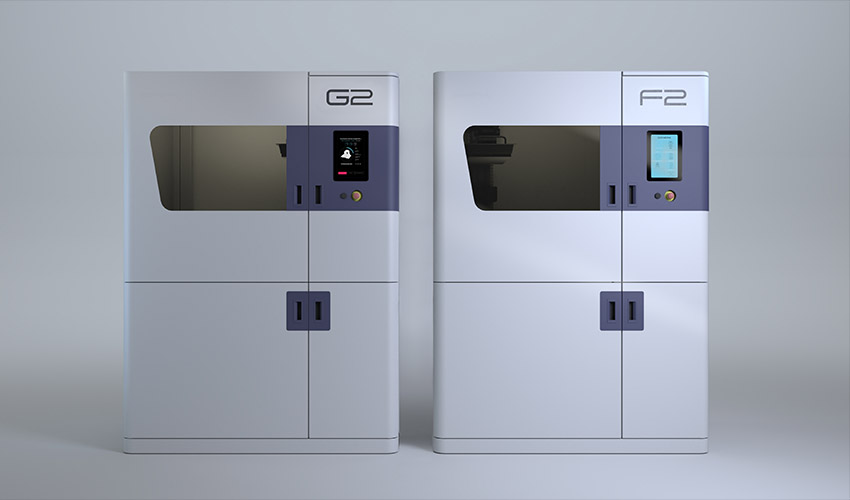
Founded in 2015, Genera is a Viennese startup that is developing comprehensive 3D printing solutions. During its development phase, the startup identified a key limitation users were facing during production. In fact, users were often left to themselves to manually coordinate the various steps of the additive manufacturing workflow, which was directly affecting repeatability. “All of us at Genera have been long time 3D printing users and therefore know the special needs and problems facing the industry,” explains CEO Klaus Stadlman.
Today, many industries are aware of the potential of 3D printing to shorten lead times, reduce the cost of prototyping, introduce more personalization in products, etc. However, on some fronts, such as for high volume production runs, 3D printing is not able to compete with conventional methods that deliver higher repeatability and quality.
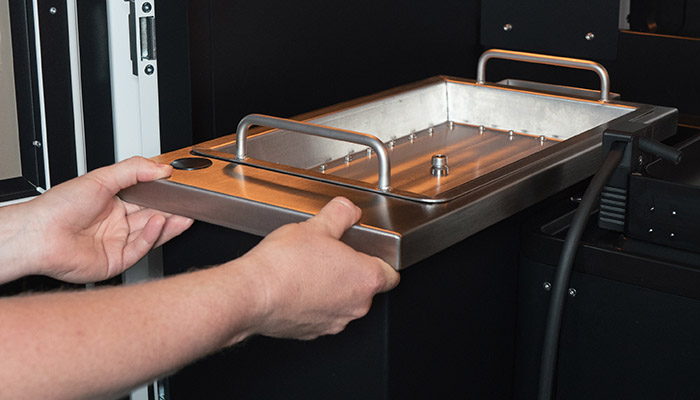
Image via Genera
This is the reason why Genera developed and is launching its G2/F2 system: based on DLP technology, it offers a completely integrated process to enable the same quality as injection molding. Therefore, the G2/F2 is more than a DLP 3D printer. Printing, washing and curing are coordinated, documented and monitored at the same time in order to achieve outstanding part quality for low or high volume production runs (up to 1,000 parts). The Genera team decided to develop a Digital Light Processing (DLP) technology, which similarly to the well-known SLA process, uses a light source to harden a UV-sensitive resin layer after layer.
The Genera G2/F2 System
Given that the system aims to be more than a 3D printer, various aspects have been optimized. The production volume is large, the software adapted to the workflow, the process glove-free, and the post-processing steps streamlined. More precisely, the Genera glove-free system is based on a shuttle solution: the part/component travels in this shuttle from the 3D printer to the post-processing unit. A special memory chip is inserted in the shuttle which stores all data of the print job, making the process repeatable and traceable. Stadlmann adds, “I especially hate wearing gloves. The so-called “shuttle”, covers the 3D printed part and guides it through the entire process. It protects the precious parts and ensures the user’s hands are kept clean.”
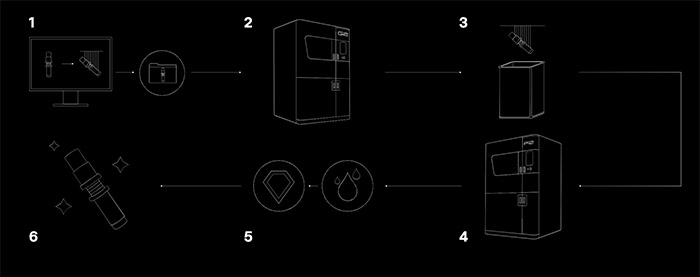
The shuttle (3) covers the 3D printed part and guides it through the entire manufacturing process | Image via Genera
Developed for industrial use, service providers and factories alike, by improving quality and repeatability but keeping prices low, Genera aims to enable users to achieve their manufacturing goals. Unveiled for the first time on September 22 during a virtual launch event, you can find much more information on the official website!
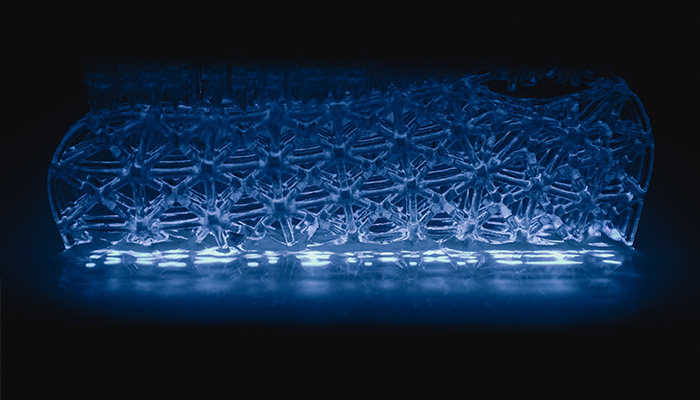
DLP part made using the Genera G2/F2 system | Image via Genera
What do you think of the G2/F2 system? Let us know in a comment down below or on our Facebook and Twitter pages! Don’t forget to sign up for our free weekly Newsletter, with all the latest news in 3D printing delivered straight to your inbox!