GE Research 3D printed a heat exchanger for more efficient energy conversion
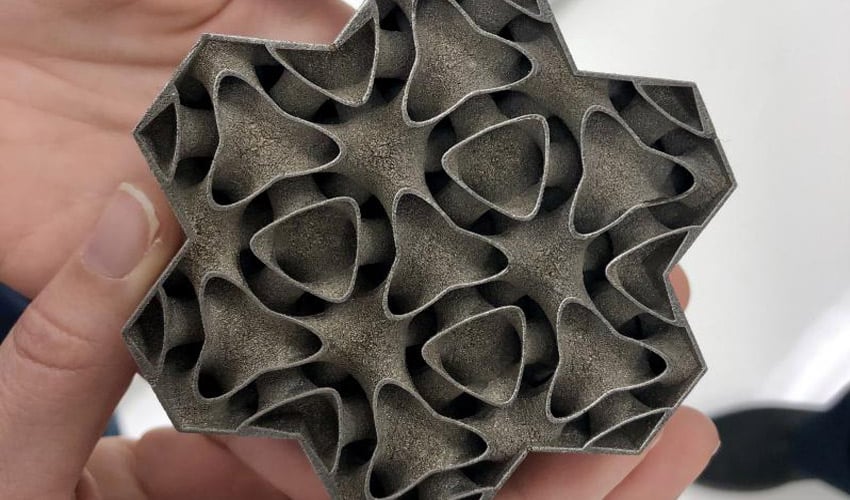
As part of a two-and-a-half year mission led by Advanced Research Projects Agency, GE Research launched a $2.5 million project to 3D print a high temperature, high pressure and super compact heat exchanger. This should produce cleaner and more efficient energy for the platforms of existing and future power plants. The group’s research division has teamed up with the University of Maryland and the Oak Ridge National Laboratory (ORNL) to complete this ambitious project. The partners were able to present a first prototype that was quite convincing.
A heat exchanger is a device that allows a fluid to be heated or cooled by another fluid circulating at a different temperature, without the two fluids mixing. These devices are beginning to be designed using additive manufacturing, a method that offers more complexity to the part while reducing production times and costs.
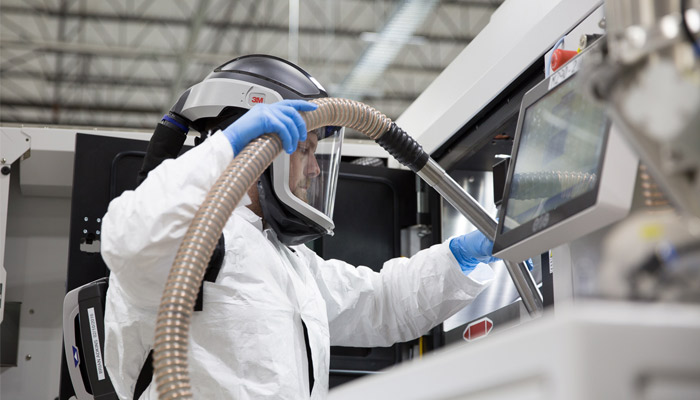
Credits: GE Research
A 3D printed heat exchanger by GE Research
GE and its partners explain that their heat exchangers should operate in environments up to 900°C and 248 bar. Peter deBock, thermal engineer at GE Research explains: “We use our extensive knowledge in metal management and thermal management and apply it like never before thanks to the power of 3D printing. Thanks to this method, we can now realize new architectural designs that were previously impossible. This will allow us to create a “UPHEAT” device that can operate cost-effectively at temperatures higher than those of current heat exchangers (+250°C).“
It should be noted that heat exchangers perform a function that is similar to that of our lungs. DeBock says: “The lungs are the ultimate heat exchanger. They circulate the air you breathe to allow the body to operate at full capacity while regulating its temperature. Heat exchangers in power generation equipment, such as gas turbines, perform essentially the same function, but at much higher temperatures and pressures. Through additive manufacturing, GE and the University of Maryland will now explore more complex biological shapes and designs to enable a radical change in heat exchanger performance, offering increased efficiency and reduced emissions.” Teams should therefore use the human body, and more specifically the lungs and body, as a model for their exchanger.
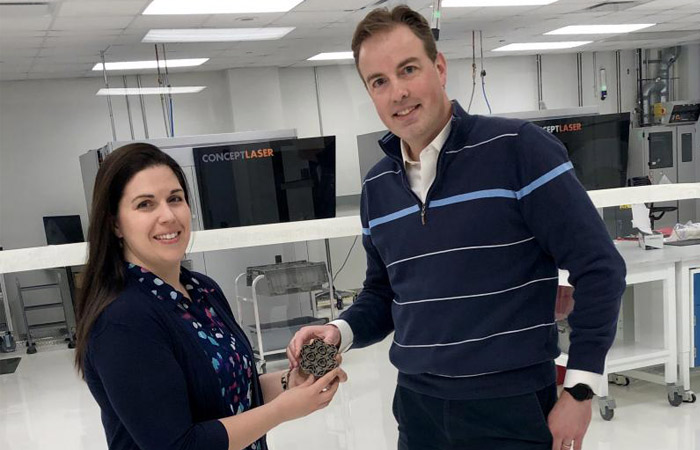
Laura Dial (Materials Scientist at GE Research) and Peter DeBock | Credits: GE Research
It should also be 3D printed from a nickel superalloy resistant to breakage, high temperatures, designed specifically for the additive manufacturing process by GE Research’s team. The solutions developed by Concept Laser should be used for the occasion, such as the M2 Cusing. The ORNL should use its expertise in corrosion science to test and validate the long-term performance of materials.
The partners claim that once completed, the heat exchanger will increase the thermal efficiency of indirect power cycles such as Brayton’s supercritical carbon dioxide (sCO2) power generation, thereby reducing energy consumption and emissions. It could also open up new opportunities in the aerospace sector, especially for particularly advanced applications. You can find more information about the project HERE.
What do you think of this efficient heat exchanger? Let us know what you think in a comment below or on our Facebook and Twitter pages! Don’t forget to sign up for our free weekly Newsletter, with all the latest news in 3D printing delivered straight to your inbox!