French Astronaut Thomas Pesquet Brings 3D Printing to the ISS
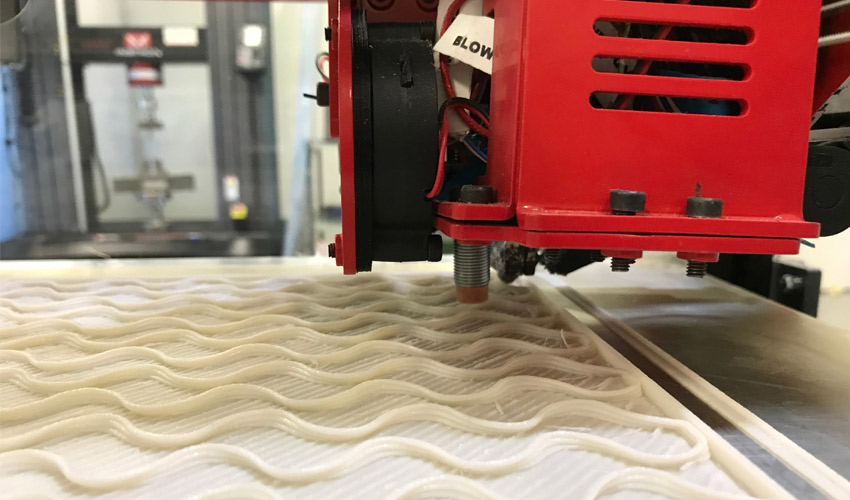
Two weeks ago, French astronaut Thomas Pesquet flew for the second time to the International Space Station (ISS) for a six-month trip, becoming the ISS’s first French commander. What we found particularly interesting was that 3D printing accompanied him on the journey, he embarked with 3D printed parts, including packaging for meals provided by the Hénaf group as well as a protective case for the French astronaut’s sleep headband. These parts were designed from a recyclable and edible foam made from PHA, a naturally occurring polymer synthesized by bacteria. These foams, designed by the ComposiTIC technical platform, offer a high level of protection, isolating shocks and vibrations, particularly important as you could image for the flight to space.
The ComposiTIC technical platform was created in 2014 at Southern Brittany University (UBS). Its goal is to develop innovative composites thanks to a robotized fiber placement technology. The platform was requested by CNES as part of the ESA’s Alpha mission carried out by Thomas Pesquet. During the next six months, the French engineer will conduct several maintenance operations as well as a hundred scientific experiments on board the ISS. And additive manufacturing has been involved in the implementation.
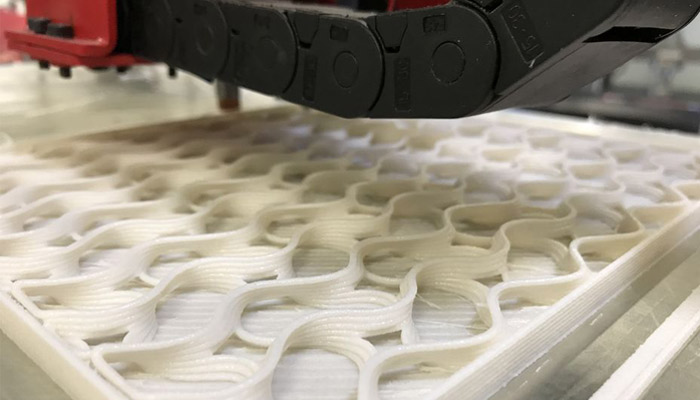
PHA granules were transformed into filament to 3D print the parts (photo credit: UBS)
A 3D printed foam to protect scientific equipment
Conducting scientific experiments in space has different constraints from those on Earth, especially in terms of packaging: any test on board the ISS must be carefully stored in a kind of box made of foam that protects against vibrations, the objective being to ensure that the equipment is functional and reliable once it arrives on the ISS. For the Alpha mission, one of the requests made by the French astronaut was to replace the traditional material from the oil industry with a recyclable foam, which would take up less space and above all generate less waste.
One of Thomas Pesquet’s experiments concerns sleep in space: the astronaut will wear a headband, designed by the startup Dreem, which will make it possible to analyze the duration and quality of his sleep. Yves-Marie Corre is the technical manager of the ComposiTIC technical platform. He explains: “We were contacted as part of the “Renewable Foam” experiment to design a recyclable foam by 3D printing that would be used to protect Thomas Pesquet’s sleep study headband. This packaging is intended to isolate the device from shocks and vibrations.”
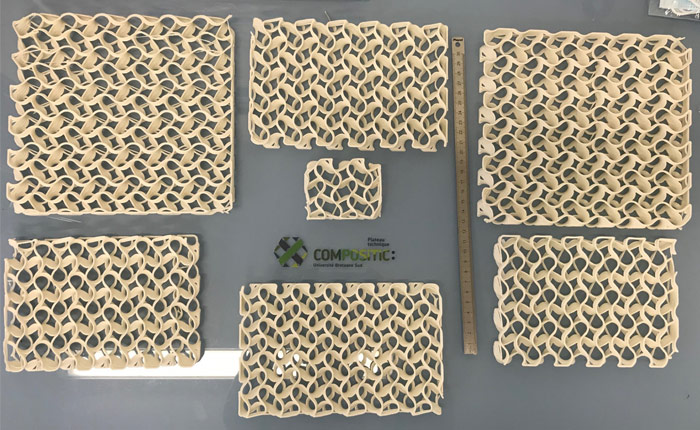
Several panels have been 3D printed (photo credits: ComposiTIC)
The technical platform therefore 3D printed a protective casing from a recyclable foam made of PHA. Using design for additive manufacturing (DfAM) methods, the team was able to devise a honeycomb structure to optimize the weight and strength of the part. What is interesting is the choice of material. Yves-Marie Corre says: “Even if it is still plastic, this time it is no longer made from petroleum-based materials but synthesized by living organisms: bacteria, giving these bioplastics the ability to degrade very quickly in the environment. About 20 plates would have been 3D printed to create 4 boxes to protect not only the headband but also the rest of the scientific equipment during the trip. These parts will then be used on board to grow vegetables: the material will be able to degrade and offer the plant all the nutrients it needs to grow.
The second element designed by 3D printing is also a piece of protection but this time it involves food. Called Edible Foam, the packaging is composed of 3D printed walls with an edible foam; these walls could therefore be eaten by astronauts. Note, however, that for the Alpha mission, only the storage functionality has been retained, the foam will not be consumed. We imagine however that the edible character could interest future missions.
What do you think of the 3D printed parts and the recyclable foam that Thomas Pesquet brought to the ISS? Let us know in a comment below or on our Facebook, Twitter and LinkedIn pages! Sign up for our free weekly Newsletter here, the latest 3D printing news straight to your inbox!