First 3D Printed Stainless Steel Fuel Component Installed at the Forsmark Nuclear Power Plant
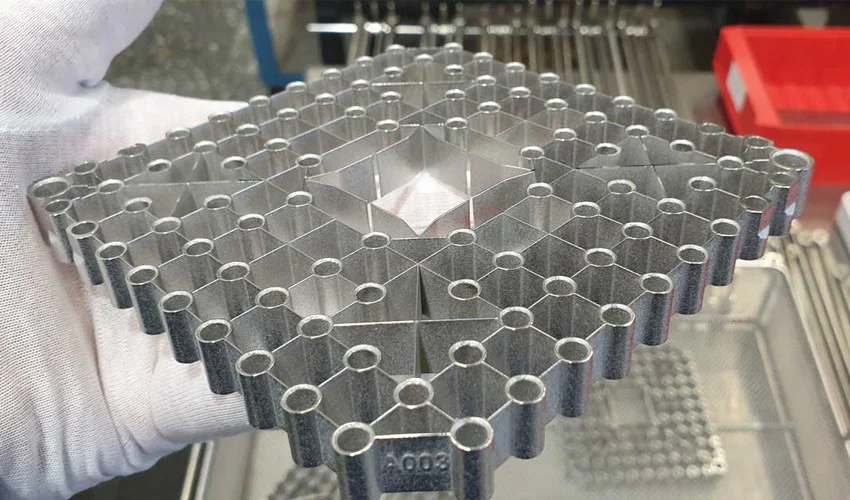
Founded in 1958, Framatome is a French multinational nuclear company that began using 3D technologies in 2015. It recently announced the development of its first 3D-printed, stainless steel fuel component. These upper tie plate grids designed and manufactured at a nuclear power plant in Sweden operated by Swedish company Vattenfall. They were successfully installed in the plant as part of a multi-year irradiation program.
Last week, we presented the possibilities offered by additive manufacturing in the oil & gas industry, which is currently able to produce parts with complex geometries to improve the performance of market solutions. It is a more cost-effective, efficient production method that allows components to be created in one go, without the need for time-consuming and expensive assembly steps. Additive manufacturing also ensures the safety of processes and personnel operating on site, a key point in the industry. The technologies have also been gaining ground in the nuclear industry, including for safety-critical parts in power plants. Indeed, last year Framatone was also involved in the creation of a 3D printed stainless steel fuel assembly channel fastener along with Oak Ridge National Laboratory which was placed in the U.S. commercial BWR nuclear power plant.
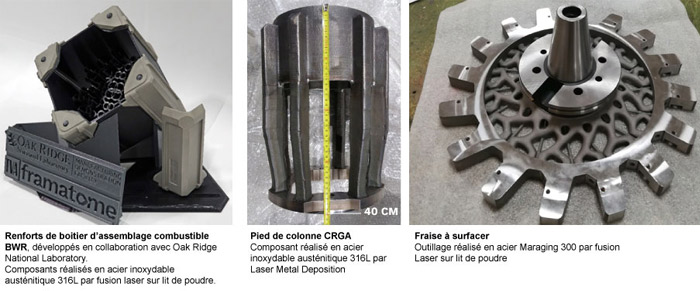
Different 3D printed parts from Framatome (photo credits: Framatome)
This latest announcement is yet another first for Framatome, as it has successfully installed the first 3D printed stainless steel part in a Swedish power plant. The upper tie plate grid is a non-structural weight-bearing component that holds the fuel rods, the metal tubes in which cylindrical pellets of sintered uranium dioxide are stacked. The grid also serves to prevent bulky debris from entering the fuel assembly. Lionel Gaiffe, senior executive vice president, Fuel Business Unit, at Framatome, added: “Advancements in the integrity of components manufactured using 3D-printing are revolutionary in the generation of safe, reliable low-carbon energy for long term operations. We appreciate Vattenfall for opening its doors and providing a steppingstone for future innovations and developments that will replace conventional manufacturing.”
Traditionally, the manufacturing process of these grids includes multiple steps and requires a high level of operator supervision. In fact, they are oftenmade from plates that are cut and stamped and then welded together via a laser. By leveraging additive manufacturing, teams can bypass these steps and come up with more complex designs to deliver more performance. Ella Ekeroth of Vattenfall Nuclear Fuel AB stated:
“The safe operation of fuel assemblies is key to Vattenfall. Along with this basic principle, our contributions to the development of efficient and reliable manufacturing processes are in the best interest of the entire nuclear industry. The overall goal of these activities is to maintain and further enhance safety and enable economically viable long term operations.”
While awaiting to learn more about the impact of this first 3D printed stainless steel component installed in a Swedish nuclear power plant, you can find the official press release HERE.
What do you think of this 3D printed stainless steel fuel component? Let us know in a comment below or on our LinkedIn, Facebook, and Twitter pages! Don’t forget to sign up for our free weekly Newsletter here, the latest 3D printing news straight to your inbox! You can also find all our videos on our YouTube channel.
*Cover Photo Credits: Framatome