Fortify combining magnetics and DLP technology for 3D printing
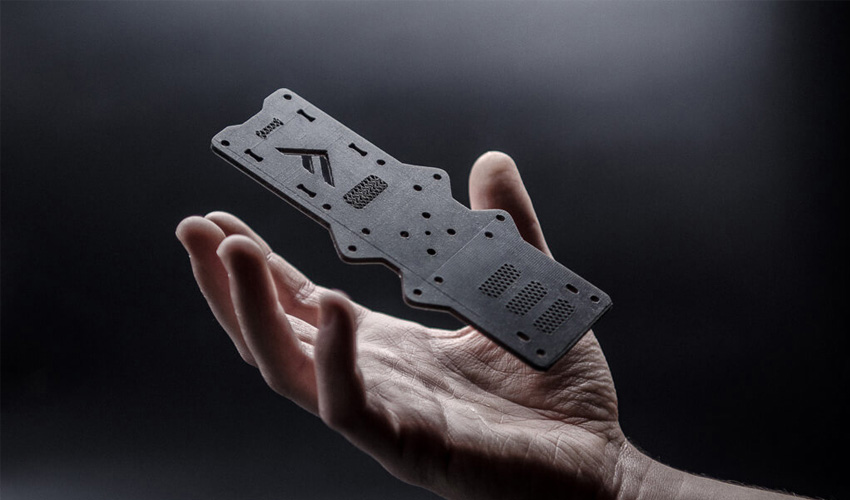
Fortify is a young company that seeks to revolutionise the long delivery cycle and the often poor material quality of traditional manufacturing processes.The company was founded on research on composite 3D printing by Randall Erb and Joshua Martin at Northeastern University. Its objective is to enable fast and transparent manufacturing of composites with optimised microstructures. Therefore, it has invented a 3D magnetic printing process called Fluxprint. It is a process that combines DLP technology and magnetics, offering a fast, fluid and high quality production. The technology is mainly intended for applications in automotive and aerospace industries. To learn more about Fortify’s process and future developments, we met Joshua Martin, CEO and co-founder of one of the most recognised startups in additive manufacturing today.
3DN: Can you introduce yourself and tell us more about Fortify?
My name is Josh Martin and I am the co-founder and CEO of Fortify. I have a PhD in materials’ science that focused on understanding the relationship between structure and ownership of biological compounds. In other words, biocomposites such as bones are made of relatively weak materials, but are designed to offer impressive mechanical properties. Fortify focuses on applying these principles to create robust composite materials.
3DN: Can you tell us more about Fluxprint technology?
Digital Composite Manufacturing™ (DCM) is an additive manufacturing platform that uses technical resins reinforced with special additives to produce high resolution parts. Fluxprint™ is our patented technology that controls the microstructure of printed parts by means of magnetic fields. It allows the printing of objects with reinforced and optimised structures for each geometry and each application.
3DN: What are the advantages of DCM and what are the challenges associated with this technology?
DCM offers the advantage of a high-resolution surface with robust strength and rigidity, even at high temperatures. However, we work with solid resins that are more complicated to treat. Fortify should overcome these obstacles by combining materials’ science with the development of appropriate hardware.
3DN: Where do you most often see 3D magnetic printing applications?
Fortify is currently focusing on the injection moulding part. This is a demanding application because the parts must withstand high pressures (often greater than 1500 psi) and high temperatures (50 to 240°C) while maintaining defined tolerances.
3DN: What are Fortify’s future projects?
DCM technology is currently used to manufacture drones components with a high weight/strength ratio. Fortify is committed to developing parts for the automotive and aerospace industries that require good temperature stability. For example, propeller blades or some assembly components for drone can be printed.
3DN: Any last words for our readers?
It is known that additive manufacturing processes based on photopolymerisation have the best surface rendering and resolution. However, the mechanical properties are generally not optimal. Fortify solves this material problem by combining a new generation of photochemistry with advanced additives and processes. For more information, please visit our official website HERE.
Let us know what you think of this article in a comment or on our Facebook and Twitter pages! Don’t forget to sign up for our free weekly Newsletter, with all the latest news in 3D printing delivered straight to your inbox!