What Role Does 3D Printing Play in Formula 1?
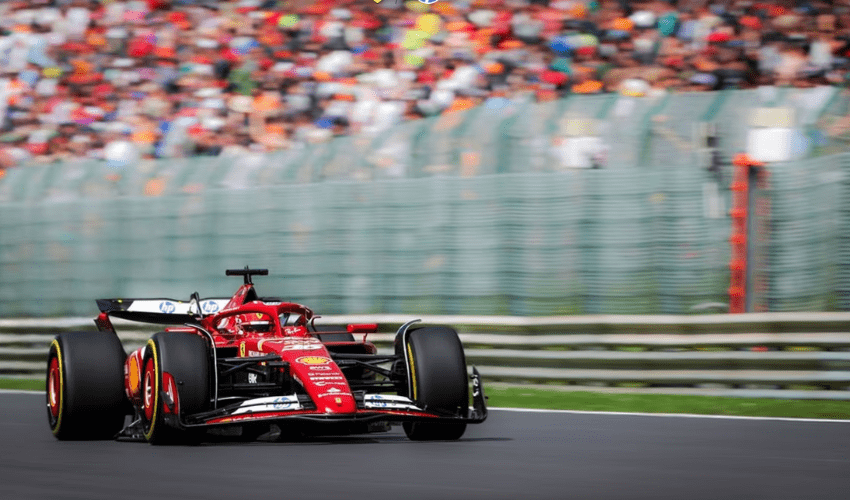
Formula 1 motor racing is a demanding sport, where the quest for performance and speed is essential. But behind every sensation offered to spectators, every fraction of a second counts. Moreover, performance is not only based on the driver’s skills, but also on the technical optimization of the car. At the heart of this constant move to improve, 3D printing has established itself as a revolutionary technology in the sport. The cars of recent years are a good illustration of this progress, making increasing use of 3D printing to maximize their performance. Introduced to motor sport in the early 2000s, additive manufacturing enables the creation of lightweight, high-performance parts that also comply with the strict regulations of the FIA (Fédération Internationale de l’Automobile).
Formula 1 continues to evolve, adopting rapid prototyping methods and the production of complex parts thanks to 3D printing. F1 teams are increasingly adopting this technology and over the years, partnerships have been forged between racing teams and 3D printing pioneers. But what are the concrete uses of 3D printing in Formula 1? What advantages and challenges does this technology present? And what future prospects does it offer in this demanding field? Fasten your seatbelts and find out in this article.
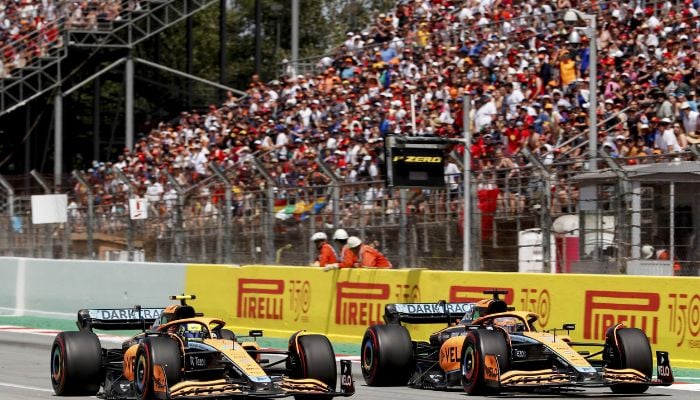
McLaren is one of the Formula 1 teams making extensive use of 3D printing for its single-seaters (photo credits: Stratasys).
Teams Turn to 3D Printing
Motorsport is known for its constant innovation, and Formula 1 is often at the forefront of new technologies. Indeed, 3D printing has proven itself to be invaluable for Formula 1 cars, with teams increasingly turning to the leaders in this technology to optimize their performance.
Notable examples include Red Bull Racing, Constructors’ Champion since 2022, who has been working with Hexagon Manufacturing Intelligence for 18 years. This partnership has enabled the team to test and adopt innovative technologies while ensuring the safety and reliability of its cars, gaining fractions of a second on the racetrack. In particular, Red Bull Racing uses digital twins and simulations to virtually design and test their cars before creating physical prototypes.
McLaren F1 Racing meanwhile uses 20 Stratasys 3D printers to produce over 9,000 parts a year, exploiting 3D printing for the creation of prototypes. Visa Cash App RB has also collaborated with ROBOZE to rethink the design and production of key components for their single-seaters.
Last but not least, Alpine has enjoyed the support of 3D Systems for over 20 years, with numerous SLA and LPBF machines at its disposal. Pat Warner, ADM Manager at Alpine, explains, “3D Systems is our main partner for all our in-house equipment and materials, which we then outsource to various companies as required.”
Thus, the use of 3D printing in Formula 1, although present for some time, is becoming increasingly widespread. According to Pat Warner, the former Renault F1 Team acquired its first 3D printer back in 1998. However, the importance of 3D printing really took off in the 2010s.
What Are the Concrete Applications and 3D Printing Technologies Used in Formula 1?
In terms of applications, 3D printing stands out for its efficiency in rapid prototyping, something that is particularly beneficial to Formula 1 racing teams. The technology enables new parts to be designed, manufactured and tested, accelerating the innovation development cycle. What’s more, 3D printing is not just reserved for prototypes: it is also used to produce functional components that are directly integrated into racing vehicles.
In terms of the technologies employed, fused deposition modeling (FDM) is widely used for rapid prototyping and sample production in Formula 1 racing. Polymers, particularly nylons, are frequently chosen for their mechanical properties. High-performance thermoplastics such as PEKK and PEEK are also commonly used. These materials are favored for their high resistance to heat, essential in an environment where temperatures can exceed 1,000 degrees, as is often the case for certain parts of a single-seater.
In 2014, McLaren broke new ground by introducing the first 3D-printed part for its race cars: a valve cover for the engine, manufactured using FDM technology. Later, the team expanded its use of 3D printing by producing a structural support to attach the hydraulic line to the MCL32 race car. This support, designed using FDM technology and made from carbon-fiber-reinforced nylon, was printed in just four hours.
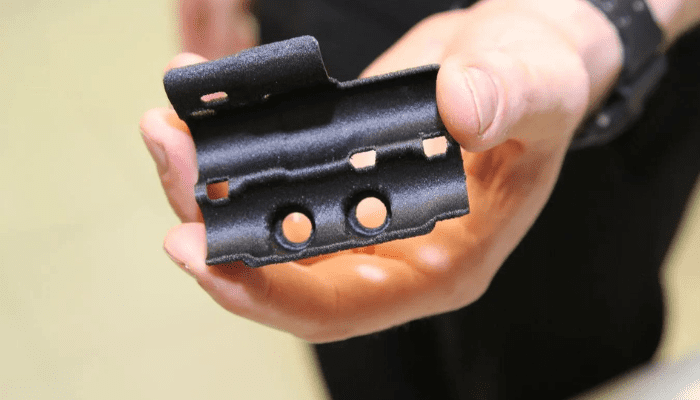
The 3D-printed hydraulic pipe support for the MCL32 single-seater using FDM technology (photo credits: Mclaren)
Of course, FDM is not the only 3D printing technology used in Formula 1. “Stereolithography (SLA) is widely used to manufacture the visible elements of our wind tunnel at Alpine,” notes Pat Warner. “Both the bodywork and many internal structures are produced using SLA and SLS technologies.”
Unlike FDM technology, SLA enables parts to be produced with complex geometries and a high level of detail, often meeting specific requirements. Patrick Warner points out that wind tunnel testing requires the manufacture of 600 parts per week via additive manufacturing, a volume that only a team of five specialist engineers can handle. He adds, “Traditional manufacturing methods would not be able to meet this demand.”
Additive manufacturing technologies using a powder bed, such as selective laser sintering (SLS) and laser melting (DMLS), are commonly employed in Formula 1. For example, in 2017, Ferrari used DMLS technology to create an aerodynamic element for its car. Unlike FDM or SLA methods, 3D printing using powder bed fusion offers several advantages, such as the ability to produce more isotropic parts, often without the need for supporting structures, which reduces post-processing time. The metal parts manufactured frequently include exhausts, engine components and suspensions.
The Benefits of Using 3D Printing in Formula 1
Additive manufacturing offers many advantages over traditional manufacturing methods, particularly in Formula 1, where the demands are particularly high. In Formula 1, one of the priorities is to reduce the weight of vehicles, which translates into a series of improvements: faster acceleration, increased top speed, better handling, more efficient braking, reduced fuel consumption and less tire stress. 3D printing is an ideal solution for achieving these goals, enabling the manufacture of lighter components.
Speed of part production is also important to remain competitive. If a part breaks or needs urgent modification during a race, 3D printing offers an immediate solution. It enables parts to be designed, produced and installed in record time, helping teams to quickly solve problems on the circuit or incorporate improvements for subsequent races.
It also offers great design flexibility. Engineers can experiment with complex geometries and innovative materials without the constraints of traditional manufacturing methods, such as molding or machining. It is possible to create components with complex internal structures, such as lattices or honeycomb structures, which are impossible to achieve with traditional methods.
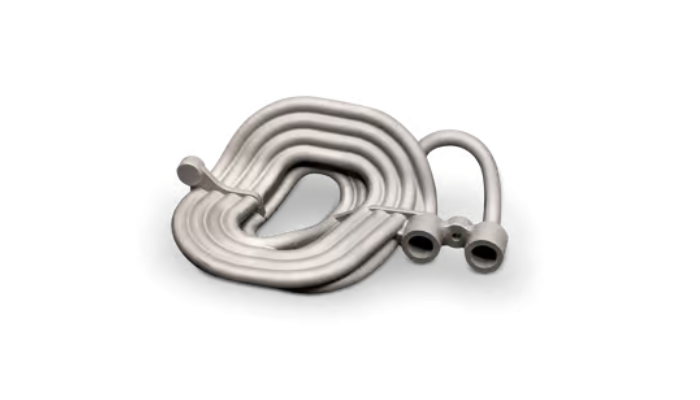
Additive manufacturing enabled the Alpine F1 Team to optimize the length of the shock absorber springs, while integrating all the necessary functionalities in a compact space (photo credits: 3D Systems)
Although additive manufacturing offers many advantages, it does not replace traditional manufacturing methods, but rather complements them. Indeed, the synergy between the two techniques can greatly optimize the production process. For example, critical or high-strength parts can be produced using conventional methods, while 3D printing can be used for complex components or rapid prototyping. This makes it possible to take advantage of the specific strengths of each technique.
For example, for plastic parts, injection molding often remains the preferred method due to its technological maturity and the variety of materials it offers. However, 3D printing has a distinct advantage: it requires no molds, making it easier to create complex parts. Often, it is the mold itself that is manufactured by 3D printing, before the final part is machined.
As Pat Warner points out, “Additive manufacturing does not replace injection molding or machining, but is an additional tool in the production arsenal. Each technology has its own role and works in harmony to produce the desired part.”
Towards an Eco-Friendly Formula 1?
On the environmental front, the growing adoption of 3D printing is in line with Formula 1’s goal of achieving zero emissions by 2030. Significant changes will also be implemented from 2026, including sustainability requirements on single-seaters. McLaren illustrates this trend through its partnership with Stratasys, using recycled materials as filaments to reduce waste. However, integrating 3D printing into Formula 1 is not without its challenges. Pat Warner explains: “We have a list of materials authorized for the car, established by the FIA. Although we can propose the addition of new materials to this list, this requires the agreement of all members. As a result, our options are somewhat limited.”
What do you think of the role of 3D printing in Formula 1? Let us know in a comment below or on our LinkedIn, Facebook, and Twitter pages! Don’t forget to sign up for our free weekly Newsletter here, the latest 3D printing news straight to your inbox! You can also find all our videos on our YouTube channel.
*Cover Photo Credits: Ferrari
No one covers the downside of 3D printing/RP
And in F1, in terms of getting the manufactured products from the point of manufacture, to the point of use, there are many. I.e. the cleansing, prep, finishing, and assembly process
I for one love the fact that it’s possible for me to create my own design on just about anything on my car, whether it be accessories or simply “patching” up missing parts. So in my opinion, Formula 1 can really benefit on 3d printing in many ways. And about the future of 3d printing, there’s a huge potential years from now. Trust me, it will!