Formnext Provides a Stage for the Applications and Potential of AM in Aerospace
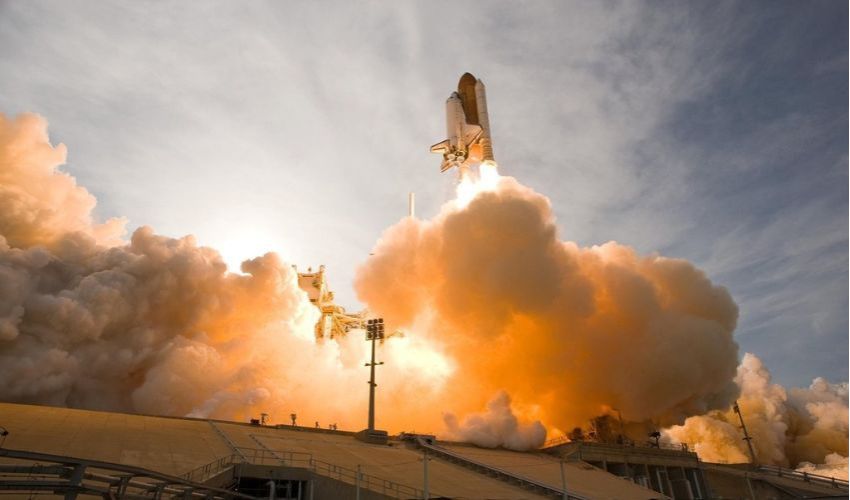
Like every year, Formnext 2024 was a snapshot of what is currently driving the AM industry and where trends will be heading. While last year’s focus was on automotive and sustainability, this year we saw an increased presence of 3D metal printing technologies and aerospace applications. This could be seen directly at the exhibitors’ stands through the use cases and innovative 3D printing systems presented. Additionally, this was evident in the numerous conferences and lectures dedicated to metal processing and aerospace. We have already highlighted the innovative metal applications at Formnext in a previous article, so in the following, we will discuss why AM is increasingly being used in aerospace, what challenges still exist and what solutions can leverage the potential of 3D printing in this field.
Additive manufacturing is primarily used in the aerospace industry for space vehicle components, including parts for rocket propulsion, combustion chambers, injector heads and pump systems. Part production in space, sometimes using space material, is another important area of the field. Examples include runways and building structures made from Martian or lunar regolith.
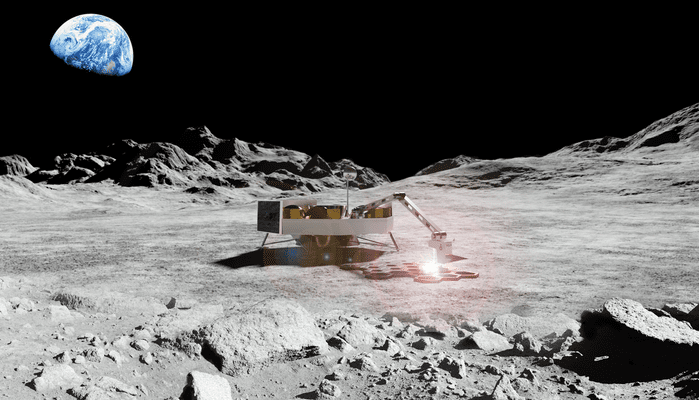
Photo credits: ICON
AM makes it possible to achieve intricate, complex designs and, in the case of rocket engines, to integrate cooling systems in a single production step. In many application examples, additively manufactured parts lead to increased performance. This is also because in some cases, customized materials with specific properties are used. The advantages mentioned apply not only to the components but also to in-space structures. Additive manufacturing is flexible and on demand. It also ensures high precision with low-to-medium energy consumption. The technology is valued for its material efficiency, as we learned in the presentation by Mohammad Azami from Concordia Aerospace Robotics Lab. Nevertheless, traditional processes such as casting and sintering of regolith concrete are still used to produce components with simple geometries thanks to their speed.
AM Processes for Space Travel and Current Challenges
Regarding additive manufacturing, we see that LPBF is the main method used, but more and more focus is being placed on DED. The Exploration Company, for example, is currently focusing on powder bed fusion but is considering DED for 2025. The German company ponticon manufactures industrial high-speed DED systems and its Dynamic Material Deposition process was used to make the jacket for the Ariane 6 engine. This process melts the powder while it is still in the air, achieving remarkable precision.
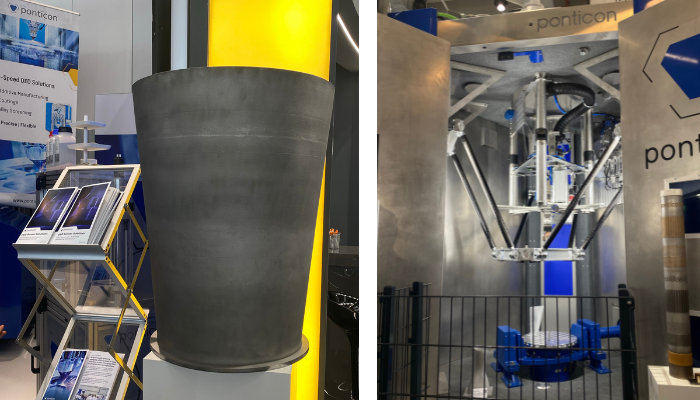
At the ponticon stand at Formnext. (Photo credits: 3Dnatives)
The DED process thus avoids a problem that is one of the biggest challenges in powder bed fusion in the aerospace sector: the depowdering of complex parts. Although internal cooling channels and sophisticated designs can be implemented using AM, cleaning these cooling lines properly is difficult. If powder remains in these channels, the fluids cannot flow and there is a risk that the engine will melt or be destroyed. “We are printing 100 cooling channels inside a part, with a 4 mm wall thickness. This is a real challenge,” says Maximilian Strixner from The Exploration Company, which developed Nyx, a modular and reusable space capsule.
Additive manufacturing in space involves different conditions than on Earth, so in-space applications face special requirements and problems. For instance, the moon has no constant temperature, and the extreme temperature fluctuations make it difficult to manufacture parts. In addition, low gravity affects part production and building structures.
Another challenge faced by users of additive manufacturing in the aerospace sector—whether on Earth or in space—is the cost. This is mainly due to the high material costs with their specific characteristics. Tobias Stiggen from ponticon GmbH explained in his presentation that around two-thirds of the total costs of the example shown (the jacket of the Ariane 6 propulsion system) are attributable to the material. The cost of the hardware, in this case a printing system from ponticon, was relatively low in comparison.
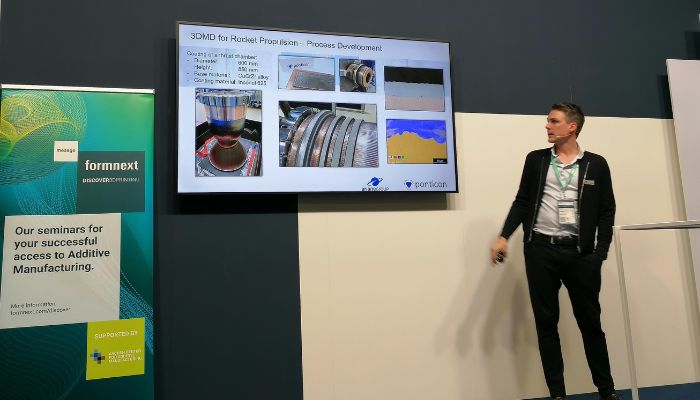
Tobias Stiggen explains the advantages of DED technology for rocket propulsion. (Photo credits: 3Dnatives)
Another reason for the high costs is that the aerospace industry focuses on high-performance and lightweight parts. While the automotive industry concentrates on cost optimization per part, the aerospace industry strives to reduce the weight of parts. Bill Bihlman of SAE International noted in his presentation on “Material Qualification for Aerospace and Automotive AM Serialized Part Production” that aerospace parts cost about ten times more than automotive ones!
High-performance Material Diversity for Aerospace Applications
Although price plays an important role, material performance and durability are paramount. We see various metals, alloys and newly developed materials and composites in space travel. The Exploration Company, for example, uses copper alloys for their thermal conductivity and nickel-based alloys for their mechanical strength and chemical resistance. SAE relies on alloys as well but uses aluminum and titanium for small series parts.
Space materials or composite materials are used for production in space. Concordia Aerospace Robotics Lab, for example, recommends a composite material made of PEEK and regolith. This meets NASA’s requirements regarding the exhaust gas quota and is highly resistant to radiation and chemicals. By incorporating regolith into PEEK, costs could also be reduced, as the results show. With 50% by weight of regolith in PEEK, the cost reduction was also 50%.
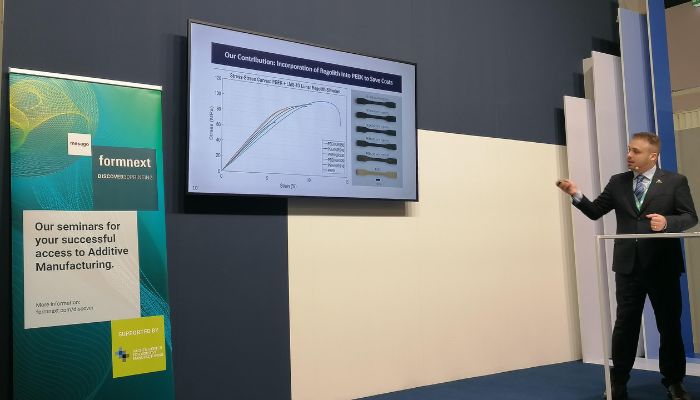
Mohammad Azami from Concordia Aerospace Robotics Lab (Photo credits: 3Dnatives)
There has been an increasing trend towards 3D printing with silicone throughout the AM industry over the past year. This material is also finding its way into aerospace. A separate presentation at Formnext 2024, “Transforming Aerospace with Silicone and Soft Composites 3D Printing,” focused on this material. Julien Barthes from 3DEUS DYNAMICS presented its powder process with silicone and how the company develops new soft composite materials during the printing process. The advantage of this is that conventional injection-molded silicone can also be used for 3D printing. Also, there is no waste because recycled powder can be reused. Barthes points out that the material can be changed during the AM process so that one part can be produced with two textures, customized mechanical properties and complex geometries. “You can add powder during the printing process, manipulate the material, and create composites during the process.” Barthes summarized. He explained that this was how the company created a new flame-retardant and soft composite material suitable for components exposed to fire, as is the case in aerospace.
A Look Into the Future
With the extensive range of applications and technical papers on aerospace, additive manufacturing will inevitably become more prevalent in this sector. While we have seen some remarkable innovations in aerospace this year—the launch of Ariane 6, the world’s largest metal-printed rocket engine from Eplus3D and LEAP 71 and more—some challenges remain, as we have seen above. Nevertheless, AM has considerable potential in space travel that has not yet been fully exploited. In addition to lightweight construction, highly complex geometries and high-performance new materials that make rockets faster, more efficient and more sustainable, we will also be hearing more about 3D printing in space in the future.
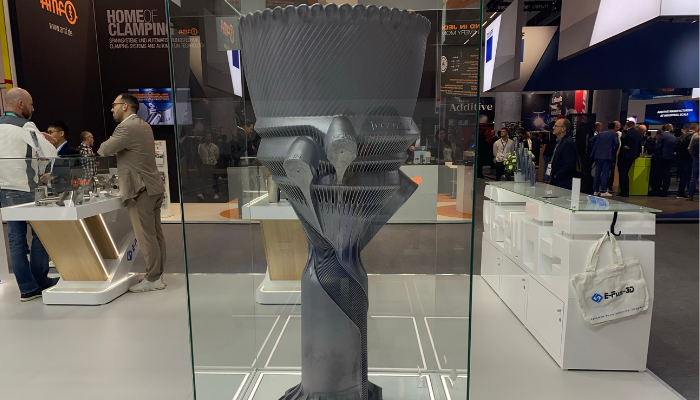
The world’s largest metal-printed rocket engine to date was presented by Eplus3D and LEAP 71 at Formnext 2024. (Photo credits: 3Dnatives)
What do you think of the future 3D printing for the aerospace sector? Let us know in a comment below or on our LinkedIn, Facebook, and Twitter pages! Don’t forget to sign up for our free weekly Newsletter here, the latest 3D printing news straight to your inbox! You can also find all our videos on our YouTube channel.