Ford Turns to SLA and SLS 3D Printing for the Electric Explorer
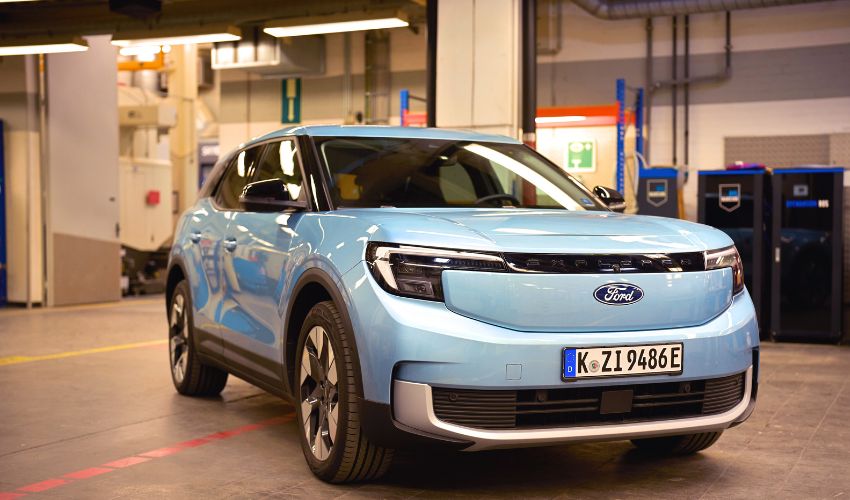
Ford, one of the largest car manufacturers in the world, has set itself an ambitious goal: The company is aiming to have an all-electric passenger vehicle lineup in the EU by 2030. Leading the way in this initiative is the new Ford Electric Explorer, whose prototypes were produced using SLS and SLA 3D printers from Formlabs.
More specifically, 3D printing was adopted at PD Merkenich’s Rapid Technology Center, which is responsible for the design of Ford’s passenger car models such as the Fiesta, Focus and Kuga, notably during prototyping. And it is here that the company used the Form 4 and Form 3L, among other Formlabs solutions, for the production of the Explorer, thus allowing different printing processes and materials to be used to produce prototypes of mirrors, handles, charging ports and parts of the dashboard.
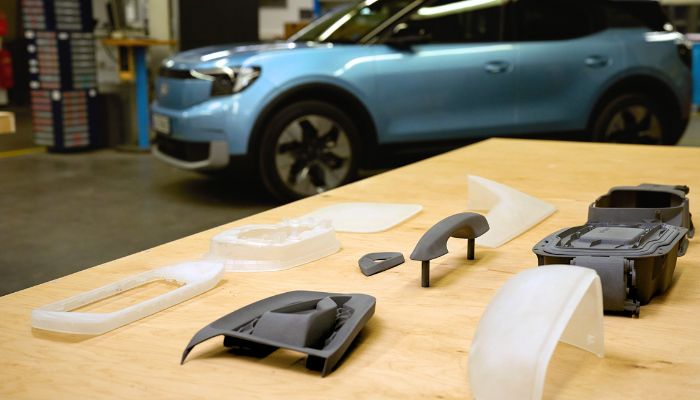
The 3D printed parts
Ford’s Rapid Technology Center produces full-size prototypes, which requires the use of various machines. For this reason, the center has injection molding machines, forming tools, various subtractive tools and, of course, 3D printers. Since 1994, when it was the first Ford plant to be equipped with an SLA printer, the use of additive manufacturing has rapidly expanded to include FDM, SLA, SLS and metal 3D printing. The first Formlabs printer in use was the Form 2, followed later by desktop printers, the large format Form 3L and finally the Form 4 MSLA printer.
Using 3D Printing for the Ford Electric Explorer
But how did this partnership between Ford and Formlabs work out? Well, it seems that Ford was particularly impressed by the speed of the Form 4. With this solution, prototypes could be produced and delivered faster, allowing more requests to be processed in less than a day. Bruno Alves, Development Engineer AM/IM at Ford Motor Company, further expanded: “Form 4’s speed and materials versatility enable us to create multiple prototypes and manufacturing aids every day. The printer has already changed the way we design and produce parts, helping us drive efficiency in our product development”.
However, the company also took advantage of other 3D printers. Namely, the Form 3L for larger parts, including for the exterior body of the vehicle and the Fuse 1+ for speed and ease of use, making a number of mechanical parts and assemblies. Additionally, the company tested the automated cleaning and polishing solution Fuse Blast-SLS Workflow, which significantly simplifies post-processing.
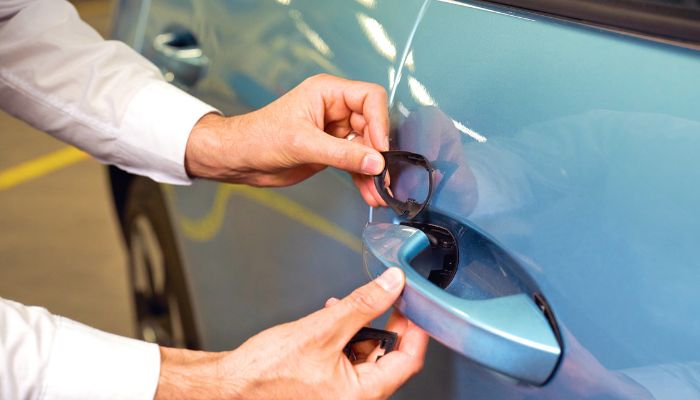
Each door handle has two rubber components for damping and insulation
And 3D printing truly did become integral to the process. For example, it was determined that the charging cover could only be made with the Fuse 1 + 300 W. “For this charging cover it was important to use SLS, based on the fact that we needed a functional part that would enable us to test the mechanisms. It’s a really complex design that we are not able to produce in any other way. We cannot mill this part. We cannot use injection molding to produce just some samples. So the best way is to print in a material that we can test physically,” confirms Alves.
In addition, Ford combines traditional manufacturing methods with 3D-printed tools to select the best process for each application and optimize material usage, cost, efficiency and speed. Rubber components for the Explorer’s door handle assembly were manufactured using 3D printed mold inserts and injection molding.
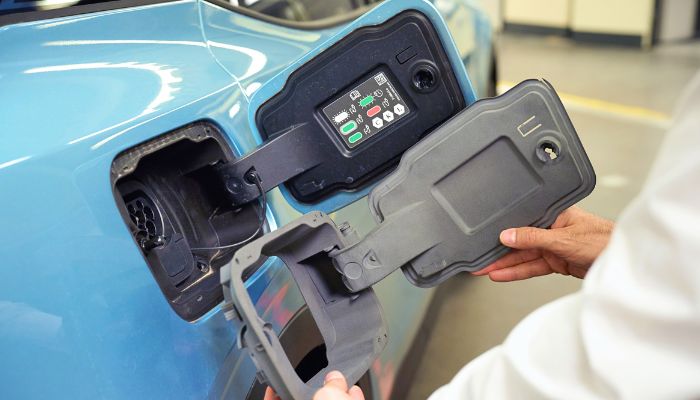
The charging port is too complex to prototype using any other method
Ford plans to continue testing new injection molding technologies and processes, including new materials, methods and machines. As competitors are constantly speeding up the development process, Ford sees the need to produce faster as well. Additive manufacturing thus plays a crucial role in keeping up with the competition and shortening development times.
What do you think of the use of additive manufacturing for the Ford Electric Explorer? Let us know in a comment below or on our LinkedIn, Facebook, and Twitter pages! Don’t forget to sign up for our free weekly newsletter here for the latest 3D printing news straight to your inbox! You can also find all our videos on our YouTube channel.
*All Photo Credits: Ford/Formlabs
Iam delighted in the progress Mr. Ford is making in the field of automobile industry and other areas of 3D printings .I wish to inform you that iam a student in the university of greater Manchester Bolton, I am Currently researching on the 3D printing particularly in this company but I do not have access on your process diagram and on that note I request if it can be send to via my email below . thanks.