Ford and Red Bull Powertrains Use 3D Printing to Optimize Vehicles for F1

In 2023, Ford Motor Company partnered with Red Bull Powertrains to race at Formula 1. It had been more than two decades since Ford has been on racetracks, and now, Ford and Red Bull Powertrains will develop the next-generation hybrid power unit for the Oracle Red Bull Racing and Scuderia AlphaTauri teams. Red Bull Racing’s cars will comply with the standards imposed by the FIA, i.e., the International Automobile Federation for Formula 1, which will come into effect in 2026. These come with several requirements, including that the cars be more aerodynamic and use carbon-neutral fuels. What interests us here is that Ford is using additive manufacturing to meet these demands.
For the past two years, Ford has been using 3D printing to enhance its race cars and adapt them to the new standards imposed by the FIA. So far, it has produced more than 1,000 3D printed components for Red Bull Powertrains. Currently, Red Bull Powertrains works with Honda, but from 2026 until 2030 Ford will become the new official partner. The two companies are working together to upgrade race cars for Formula 1 racing. Their goal is to recreate the power unit of Red Bull Racing team vehicles from scratch.
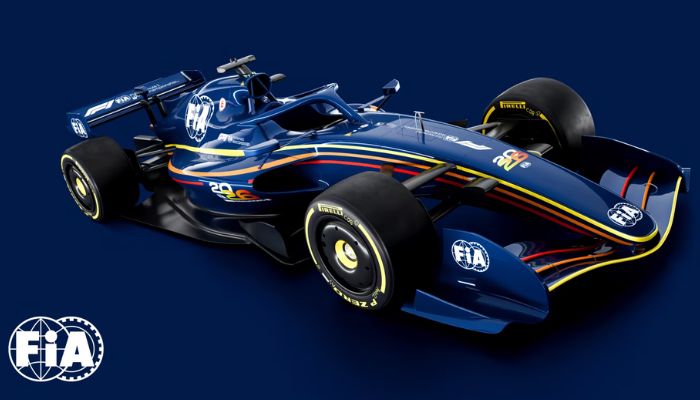
In 2024, FIA unveiled the new 2026 Technical Regulations and the first images of what the next generation of F1 cars should look like. (Photo credit: FIA)
FIA’s New Standards for Formula 1
To make racing more sustainable and in step with the demands of modernity, high standards have been set that each competing automaker must achieve by 2026. The cars will have to be, overall and compared to current measurements, 30 kg lighter, 20 cm shorter and 10 cm narrower. In addition, to aid overtaking, each car must be equipped with a dual system of active aerodynamics, both rear and front, which will replace the current drag reduction system (DRS). The fuels must also be sustainable, and the power units must reduce their endothermic power and increase their electric power. In summary, F1 wants to give its millions of spectators not only more exciting races (the increased demand for aerodynamics is meant to encourage overtaking even on city tracks such as those in Monaco and Baku), but also greener ones. So to meet the demanding requirements imposed by the FIA for F1, Ford and Red Bull Powertrains are collaborating and adopting advanced technologies such as additive manufacturing, Oracle’s cloud computing and Siemens Xcelerator industrial software suite to optimize processes.
X-ray and CT Scanning for Inspection Component Inspection
The 1,000 3D printed components that Ford produced for Red Bull are high-performance components, made of materials like metal and polymers. These must withstand speeds reaching over 300 km/h per hour and, consequently, intense heat. Therefore, the parts need to be tested for mechanical strength, hardness and geometric conformity. Ford has produced components such as battery cold plates and cooling plates for other Redbull Powertrains, systems which have been subjected to X-ray and Computed Tomography (CT) scans.
X-rays and CT scans are useful for making analytical evaluations of components in their innermost structures, because they create digital models of the parts with the data collected. In fact, CT scans make it possible to detect both the presence of voids within the printed part and any areas subject to delamination, where the layers created by printing separate from one another. These scans then allow for a more efficient treatment of any problems that may arise during the various mechanical tests to which parts are subjected and, as a result, optimize and speed up production. Additive manufacturing, thus combined with advanced 3D inspection procedures, allows for high-performance and safe part production. However, Ford uses scans and additional testing to inspect all manufactured parts, not just those that were additively manufactured.
Ford and 3D Printing Beyond Formula 1
Ford has been using additive manufacturing for various purposes for years. In 2023, the company opened the Cologne Electrification Center in Germany, specializing in 3D printing to support the production of the first series of 100% electric vehicles made in Europe. Twelve high-tech 3D printers are used at the Cologne Electrification Center to produce a wide variety of polymer and metal parts. These parts can start from a few centimeters in length and weigh as little as 30 grams, reaching 2.4 meters in length and weighing 15 kilograms.
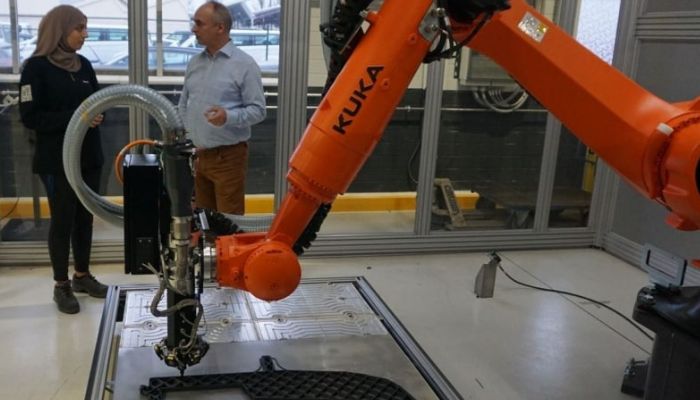
The Cologne Electrification Center, Ford’s plant in Germany. (Photo credit: Ford Media Center)
Ford’s German headquarters has been using 3D printing since the 1990s, when engineers at the Merkenich development center began 3D printing parts for test vehicles and prototypes. But that’s not all: In 2019 at the Ford Research and Innovation Center in Michigan, the largest metal part ever made using 3D printing was produced. The team reproduced an aluminum intake manifold for the engine of a Ford F-150. Furthermore, a catalog of 5,000 3D-printable parts was created at Ford’s Valencia, Spain, plant to provide innovative solutions for various stages of the plant’s production process. By 2021 alone, a total of 20,000 printed parts have been created. Finally, Ford is using 3D printing to automate production processes.
Now, we just have to wait until 2026 to see the cars born from Red Bull Powertrains and Ford speeding around the Formula 1 circuits. In the meantime, Ford will continue to leverage additive manufacturing for efficiency in developing high-performance parts.
What do you think of the collaboration between Ford and Red Bull Powertrains? Let us know in a comment below or on our LinkedIn, Facebook, and Twitter pages! For more on automotive 3D printing, click here. Don’t forget to sign up for our free weekly Newsletter here, the latest 3D printing news straight to your inbox! You can also find all our videos on our YouTube channel.
*All Photo Credits: Ford Media Center