Process planning for five-axis additive manufacturing
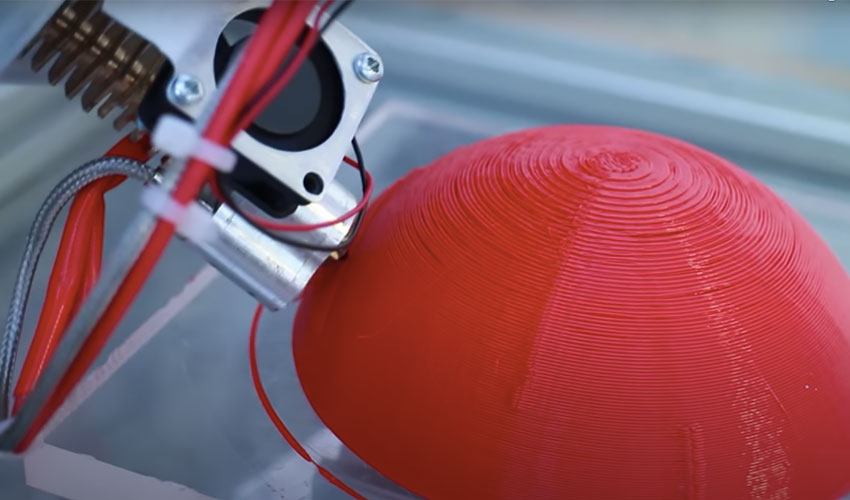
Xinyi Xiao, PhD in industrial engineering at Penn State, has published a research study in the Journal of Additive Manufacturing on five-axis additive manufacturing to build parts without printing support structures. The project involved designing automated process planning software for five-axis 3D printing solutions. The aim of the study is to find a viable solution to reduce costs, time and resources needed during the additive manufacturing production process.
Over the years, additive manufacturing systems have developed tremendously. However, software to support these solutions can quickly become outdated. Traditionally, 3D printing is a two dimensional layer-by-layer material deposition process – also known as three-axis additive manufacturing – which requires building the support structures along the build of the desired model. Five-axis 3D printers can move linearly along an X, Y, Z plane, but can also rotate on the A and B axis, thus having the potential to build structures without the need for supports. Despite the time and money savings of this technology, five-axis additive manufacturing lacks the same design planning and automation as three-axis machines, so creating planning software for this method is vital to support its full use in the industry.
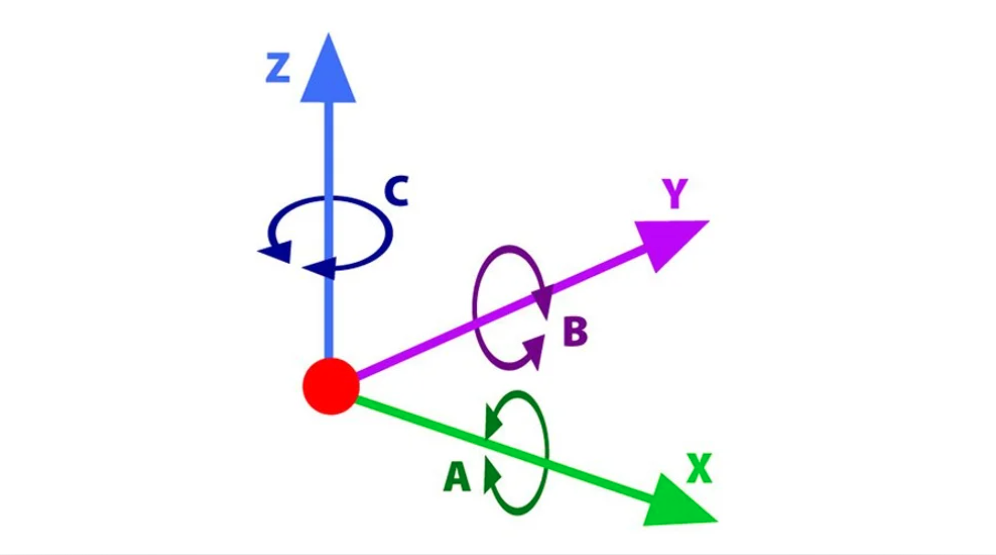
In this example, we have 6-axis. In the case of 5-axis, the 3D printer can move along the X,Y and Z plan, and rotate on the A and B axis.
How were the algorithms developed?
The author of the project, Xinyi Xiao, carried out the work as part of her curriculum, under the supervision of Professor Sanjay Joshi, a specialist in industrial engineering. The professor commented: “The idea of the software is to make five-axis additive manufacturing fully automated without the need for manual work or redesign of a product. Xinyi came to me when she needed guidance or had questions, but in the end, she led this project.” The study shows that the software’s algorithm was able to automatically reorient the part during the build using a five-axis machine.
The reorientations still allow the part to be built using traditional planar deposition but without the use of supports. This required that the part be decomposed into sub volumes, such that each sub volume has its build direction and can be built with planar layers. This paper presents algorithms to determine the sub-volumes, their orientations, and sequence, which form the major components of the process plan for manufacturing.
An added benefit of this algorithm is that it helps designers evaluate the feasibility of the parts, offering opportunities to correct and reshape the structures before 3D printing. And also providing information on on the support free manufacturability of the part. All these properties can reduce the risks as well as costs when using three-dimensional technology. Xiao says: “Large metal components, using traditional additive manufacturing, can take days and waste many materials using support structures. Additive manufacturing is very powerful, and can do many things because of its flexibility; however, it also has its disadvantages. There is still more work to be done.”
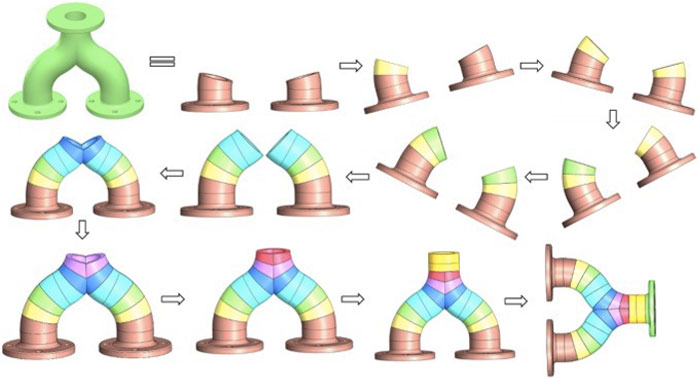
3D printing process without supports | Credits Xinyi Xiao, Penn State
The goal now is to continue researching these algorithms so that different industrial sectors, such as aerospace or automotive, can integrate advanced five-axis technology. You can find more information in the journal where the study was published HERE.
What do you think of this study? Let us know in a comment below or on our Facebook and Twitter pages! Sign up for our free weekly Newsletter here, the latest 3D printing news straight to your inbox!
*Cover Photo Credits: 5AXISMAKER