The first 3D Printed Cryogenic Tank for Storing Liquid Hydrogen
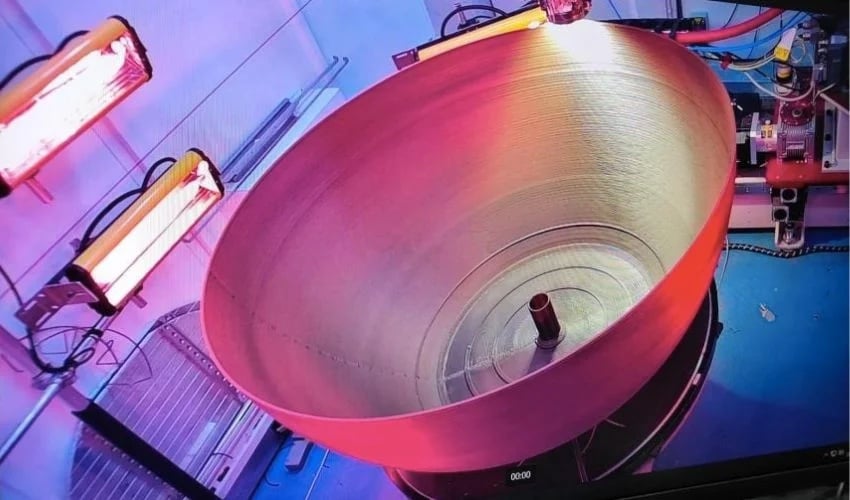
The AIMEN technology center recently completed the manufacture of a 3D printed cryogenic tank for storing liquid hydrogen, a world first. This innovation marks a key milestone for the aeronautical industry, which is faced with an ever-more urgent need to reduce its carbon footprint. Indeed, according to Our World in Data, aviation accounts for around 2.5% of global CO₂ emissions – a worrying figure, all the more so as this sector is among the most difficult to decarbonize, while experiencing constant growth in demand.
This tank is part of the European OVERLEAF project, led by the Spanish company ACITURRI. The aim: to develop sustainable, high-performance solutions for tomorrow’s aviation. The project aims to design a low-pressure liquid hydrogen (LH₂) storage system, based on state-of-the-art materials, leak detection sensors and manufacturing processes. Research and technology centers in France, Italy, Norway, Romania and Spain are collaborating on this initiative, with the ambition of rethinking aircraft architecture to incorporate clean, high-performance technologies.
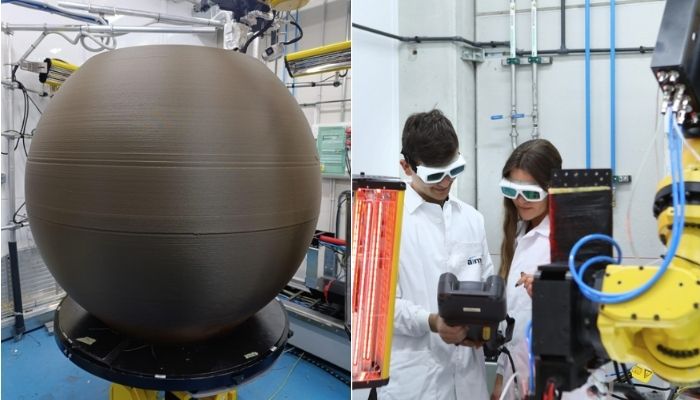
Photo Credits: AIMEN
AIMEN has succeeded in manufacturing a prototype cryogenic tank capable of storing liquid hydrogen at temperatures below -250°C, thus overcoming a considerable technical challenge. This type of tank is essential if hydrogen is to become a credible alternative to fossil fuels in the aeronautical sector, where storage conditions are particularly extreme. The main challenge was to design a structure that was both resistant to very low temperatures and light enough to meet the constraints of the aeronautical industry.
What Does a 3D Printed Cryogenic Tank for Storing Liquid Hydrogen Look Like?
The AIMEN-designed tank, which has a diameter of 1.5 meters, forms the central element of the liquid hydrogen storage system (LH₂). For its creation, the center used large-format, high-pressure additive manufacturing technologies. The structure is made up of two walls: an inner shell in high-performance thermoplastic, providing cryogenic insulation, and an outer layer in carbon fiber, providing the necessary mechanical strength.
The entire process took place in a robotized cell equipped with a state-of-the-art 3D printing system combined with infrared heating, guaranteeing optimum adhesion between the layers. The printing process lasted over 100 hours, under constant surveillance using thermal cameras.
Pablo Romero, head of the R&D group in additive composite manufacturing and coordinator of the OVERLEAF project at AIMEN, expands, “This breakthrough represents a real technological breakthrough in the manufacture of components for sustainable aviation. We have mobilized all our expertise in robotics, 3D printing and process engineering to meet a challenge of extreme technical complexity.”
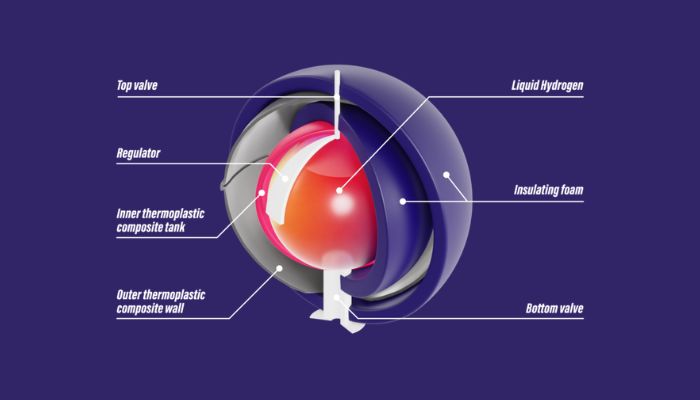
Architecture of the low-pressure liquid hydrogen storage system (image credits: OVERLEAF).
A key aspect of the reservoir’s development was the collaboration with the French technology center CANOE. Together, they developed a new composite material, combining a biosourced thermoplastic with reinforcing natural fibers. This innovative combination makes it possible to produce structures that are lightweight, robust and environmentally sustainable. It is a perfect illustration of the OVERLEAF project’s commitment to the objectives of the European Green Pact 2050, particularly in the field of sustainable aviation.
What do you think of the 3D printed cryogenic tank? Let us know in a comment below or on our LinkedIn, Facebook, and Twitter pages! Don’t forget to sign up for our free weekly Newsletter here, the latest 3D printing news straight to your inbox! You can also find all our videos on our YouTube channel. For more 3D printing news in the aerospace and defense sectors, check out our dedicated page HERE.
*Cover Photo Credits: AIMEN Technological Center