Ferrari Uses 3D Printed Metal Parts in New F80 Supercar
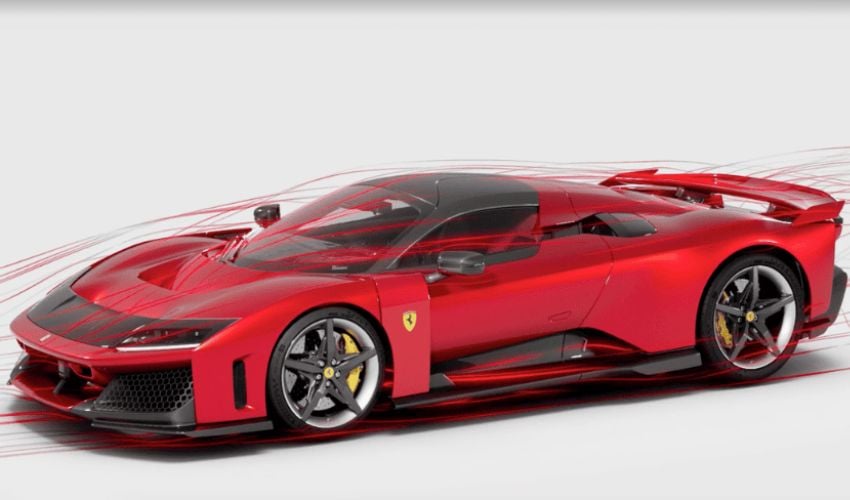
Ferrari, the iconic Italian luxury car and racing brand, unveiled its new limited-edition F80 supercar on October 17. Production of this model will begin in 2025 and run until 2027, marking the automaker’s 80th anniversary. A total of 799 models will be produced, all already sold at a unit price of 3.6 million euros. But what’s so special about this supercar? Ferrari has announced the integration of metal parts manufactured by 3D printing, a first for the brand, which has until now been discreet about its production methods, and the use of this technology in particular.
The F80 marks a turning point in performance, technology and engineering, and Ferrari stands out for its superior production capacity and wide range of users. This new supercar joins the line of iconic Ferrari models, such as the F40 and LaFerrari. It embodies excellence in internal combustion engine engineering while incorporating the latest generation of hybrid advances.
Which Parts of the F80 Are 3D Printed?
3D printing plays a key role in the F80’s active suspension system. This supercar features a fully independent four-wheel suspension, powered by four 48V electric motors and designed with a double wishbone system. The suspension incorporates active shock absorbers and suspension arms manufactured by additive manufacturing. In particular, the upper wishbones are made using metal 3D printing, a first for a Ferrari road-going model. The completely redesigned active suspension system is one of Ferrari’s major innovations for optimizing vehicle performance on both road and track. It manages to reconcile two often conflicting needs: it ensures stable driving on the racetrack by reducing height variations, while at the same time allowing effective absorption of road irregularities during everyday use on the road.
This approach offers several advantages, such as optimized configuration, precise wheel control, reduced unsprung weight, elimination of the stabilizer bar and precise camber angle adjustment. It is also important to point out that 3D printing offers numerous benefits in the automotive sector, such as weight reduction, design flexibility, rapid prototyping and production, and efficient use of materials. Although details of production techniques are not disclosed, this breakthrough marks an important milestone for Ferrari. The F80 offers a total power output of 1,200 hp, making it the most powerful Ferrari model ever designed for the road. It accelerates from 0 to 100 km/h in just 2.15 seconds and reaches a top speed of 350 km/h.
What do you think of the 3D printed metal parts for the new F80 supercar? Let us know in a comment below or on our LinkedIn, Facebook, and Twitter pages! Don’t forget to sign up for our free weekly Newsletter here, the latest 3D printing news straight to your inbox! You can also find all our videos on our YouTube channel.
*All Photo Credits: Ferrari