#3DStartup: Fabric8Labs and their metal 3D Printing without Heat, Powder, or a Laser
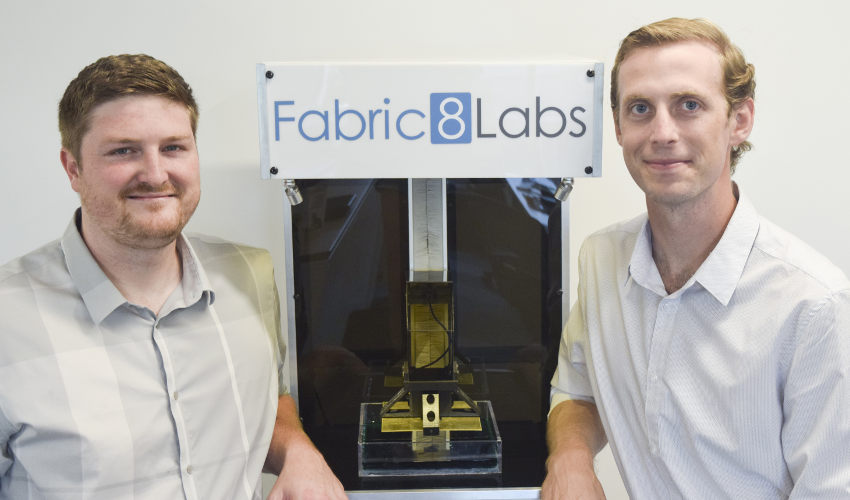
If you have kept up with the additive manufacturing industry through 2017, you’d know that metal 3D printing is all the rage. With over 20 major companies releasing metal 3D printers and hundreds of millions of dollars being invested, metal 3D printing certainly has a bright future.
This brings us nicely onto the topic of our recent interview with Californian-based startup Fabric8Labs. Fabric8Labs are a metal 3D printing startup with a difference – they don’t require lasers, powders, or even heat. Naturally, we had to find out more. Therefore, we spoke to Fabric8Labs about their technology, aims for the future, and more.
3DN: Tell us about your professional relation with the 3D printing industry and how the idea of Fabric8Labs came up?
Our founding team was working in environments where additive manufacturing in metal could make huge impacts but quickly realized that the technologies available to them at the time were just too expensive to make a business case for. Together, we set out to see if there was a better way of approaching metal additive manufacturing. After seeing how electrochemical deposition created high-quality metal deposits, the team conceptualized what our process is today.
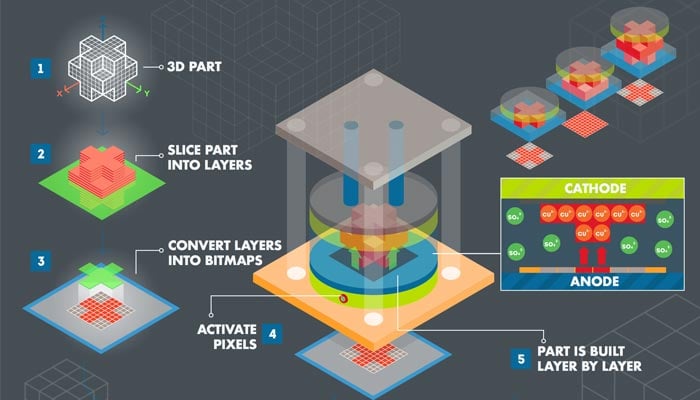
Infographic about the technology developed by Fabric8Labs.
3DN: Can you explain us your new technology Stereo-Electrochemical Deposition (SED)?
The process is based on localized electrodeposition. We use an array of electrodes that are submerged in an electroplating solution. We control each electrode to deposit precise amounts of material, layer by layer. This non-thermal manufacturing technique does away with the expensive metal powders and lasers to make both the equipment and feedstock materials significantly lower cost. Further, since materials are being deposited at the atomic level “atom by atom” rather than fusing powder, the deposits formed are almost fully dense and much higher quality.
3DN: Which compatible metals will be unveiled on your metal 3D printers?
We plan to enter the market first with copper and nickel alloys such as Nickel-Cobalt as well as several types of stainless steel.
Fabric8Labs are releasing two metal 3D printers, the Series 1000 with a capacity of 3081 cm³ offering a resolution of 100μm (Z) / 25μm (X, Y), as well as the Series 2000 with a maximum volume of 63713 cm³ for a resolution of 65μm (Z) / 25μm (X, Y). The site announced that compatible materials include: Copper, Nickel, Iron, Cobalt, Cobalt-Chrome, Pewter, Inconel, Zinc, Aluminum, Titanium, Stainless Steel, Silver and Gold.
Further, since materials are being deposited at the atomic level “atom by atom” rather than fusing powder, the deposits formed are almost fully dense and much higher quality.
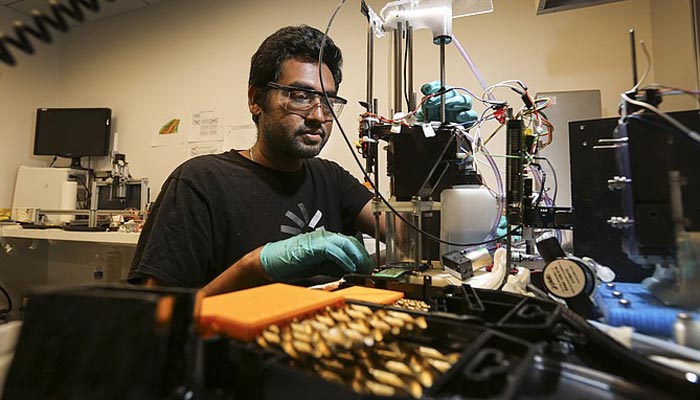
Shiv Shailendar, researcher on the Fabric8Labs project.
3DN: What is the target that Fabric8Labs aims to reach and why?
We are targeting applications in the medical device, aerospace, and communications industries primarily because the combination of material requirements, part complexity, and production volumes fit well with the technology’s capabilities.
3DN: How important do you think the metal 3D printing market will be in 2018?
2018 is going to define the metal 3d printing space. Many of the innovations in the space announced during 2017 brought a lot of attention to additive manufacturing – 2018 will see the focus of this attention turn to new and unique applications only enabled by these new technologies.
3DN: Do you have any last words for our readers?
We are actively seeking beta partners to test our production prototypes in mid-2018 and are continually looking for interesting applications for the technology.
What do you think of Fabric8Labs? Let us know in a comment below or on our Facebook and Twitter pages! Sign up for our free weekly Newsletter, all the latest news in 3D printing straight to your inbox!