Why you should integrate Powder Bed Fusion into your business: Experts give their advice!
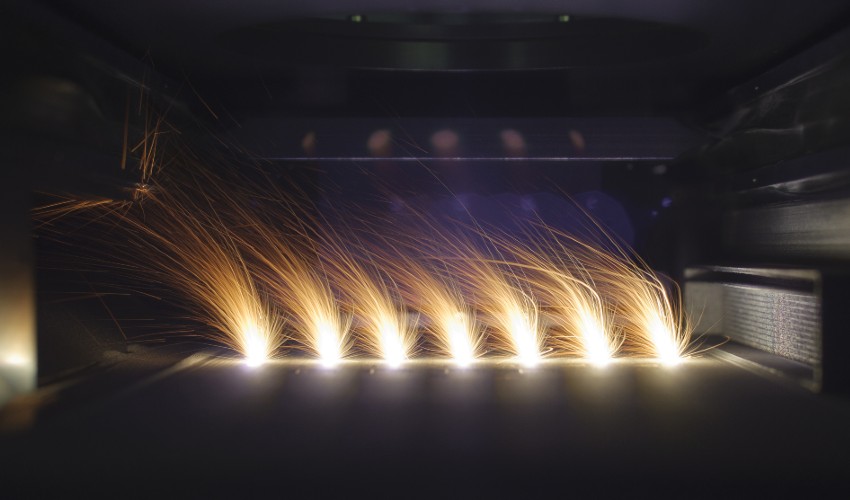
Powder Bed Fusion describes AM processes in which metals in powder form are fused with a heat source to manufacture a part. This heat source either be in the form of either a laser or an electron beam. An example of a technology that uses a laser is laser powder bed fusion (LPBF). Electron beam melting (EBM) technology uses an electron beam. The printing process for all Powder Bed Fusion technologies is very similar: a thin layer of metal powder is applied to the build platform and the laser or the electric beam fuses the powder together at the places where the part is to be created. Then the build platform lowers a little and another layer of powder is applied. This process is repeated over and over again. Thanks to this layer by layer process and due to the laser working point by point, the resulting piece can be much more precise than in other methods, allowing for greater design complexity. This is just one of the reasons why companies choose Powder Bed Fusion. Although there are other technologies for printing metal, such as Direct Energy Deposition (DED), we will focus on Powder Bed Fusion in this article. To learn more about why you should integrate Powder Bed Fusion into your business, we asked our three experts Dr. Yves Hagedorn, Dr. Elena Lopéz and Sadato Kobayashi for their advice.
Dr. Yves Hagedorn is the CEO of Aconity3D, a mechanical engineering company for special machines in the field of LPBF, founded in 2014. His goal is to provide flexible and open equipment technology to efficiently expand metal 3D printing towards industrialization. Dr. Elena Lopéz works as department head for additive manufacturing at the Fraunhofer Institute for Material and Beam Technology IWS in Dresden. In addition, she has been operationally leading the large-scale AGENT-3D project (€90 million/$109,292,400, 120 project partners) since 2014, where virtually all relevant AM processes for metals, ceramics and polymers are being further developed in over 35 research projects. Sadato Kobayashi is the department head for additive manufacturing at GF Machining Solutions Japan. He has been working with additive manufacturing users for 18 years.
- Dr. Yves Hagedorn
- Dr. Elena Lopez
- Sadato Kobayashi
When should a company choose Powder Bed Fusion over traditional manufacturing methods?
In order to answer the question of why you should integrate Powder Bed Fusion into your company, it is first necessary to clarify when it actually makes sense to use this technology over more conventional ones. While additive manufacturing definitely has its advantages, it is still not equally suitable for every company. Kobayashi says that it mainly depends on the company’s situation and business plans. He cites the following example as one motivation: “The need to replace a skilled but retiring production workforce is an important reason from an organizational perspective and in terms of business continuity.”
Dr. Hagedorn makes an assessment on whether to use this process based on the following four questions: “Can the component also be produced conventionally? Can a more complex design generate added customer value? Is the material to be used suitable for additive manufacturing? Can the component size in combination with the quantities to be realized be mapped using AM?” Dr. Lopéz emphasizes that the decision should not focus solely on one component, however: “Manufacturing one component using LPBF in the same way as with conventional production methods may not bring any advantage to the company, but the overall consideration of AM in the company does!”
So, in summary, one should look at the component level as well as the overall business plans to decide whether additive manufacturing is worthwhile for the company or not. There are a number of 3D printing service providers that specialize in helping other companies make this decision and, if necessary, assisting them with implementation of their projects.
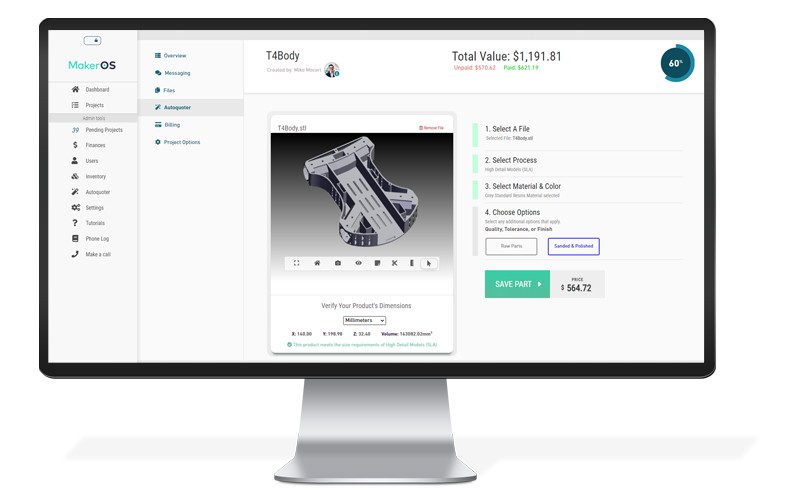
When deciding whether Powder Bed Fusion integration makes sense, one should look at the component level as well as the overall business plans to make a decision. (photo credits: GF Machining Solutions)
Powder Bed Fusion Integration: Advantages and Limitations
Of course, to figure out why a company should integrate Powder Bed Fusion, one must address the benefits it offers. Kobayashi does this by taking two different perspectives: “From a technical perspective, you can benefit from greater design freedom to better meet requirements that would otherwise be impossible or too costly to manufacture. From an operational standpoint, you can gain more control over the quality, cost, delivery date and traceability of traditionally cast and/or machined components. This leads to increased flexibility in your production and the ability to produce what you need, when and where you need it.” The design freedom gained can be found in dentistry, for example. There, metal printing is used to develop implants and crowns that are perfectly adapted to the patient. In addition, aerospace and aviation are also benefiting from it. Lufthansa, for example, uses 3D printing to make repair and maintenance processes more efficient internally through greater freedom to design parts or faster production.
Dr. Lopéz also acknowledges these advantages, but says that these are typical benefits of additive manufacturing in general and therefore also cites “topology optimization, increased complexity of internal structures, partially improved material properties through the use of innovative alloys” as LPBF-specific. In particular, topology optimization is a reason for the automotive industry to integrate powder bed fusion. To cite just one of the many examples: Porsche used topology optimization to optimally integrate the various components such as bearings, heat exchangers, etc. in its e-drive. The software was then able to calculate the loads and their trajectories to optimize the final part. As a result, honeycomb structures were developed that reduced the weight of the drive housing by 40% and the total drive by 10%. While Dr. Hagedorn also sees the advantages in design freedom and flexibility, he additionally cites the expansion of the material spectrum, sustainability through reuse of the powder, and consistent digitization.
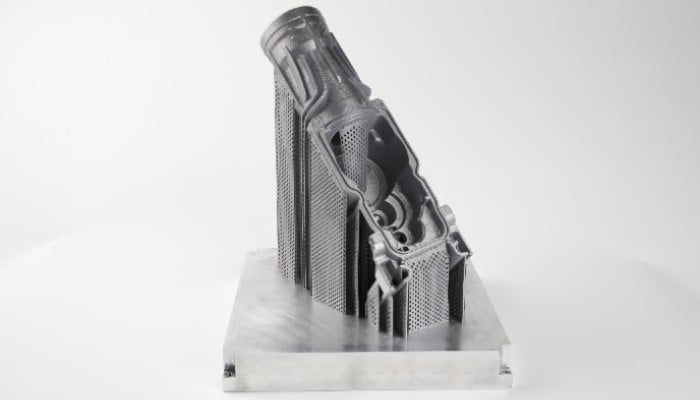
Powder Bed Fusion can be used to realize complex structures, as seen in this component. (photo credits: GF Machining Solutions)
However, even though the advantages sound very enticing, one must also consider the limitations of powder bed fusion. These include, according to Dr. Lopéz, “part size, repair of pre-existing and damaged parts, material turnover or reuse, and limited multi-material processing compared to nozzle processes.” In terms of material, it can also be said that previous powders were mostly not specifically designed for additive manufacturing. For this reason, Equispheres noted in a study that the choice of metal powder leads to more or less consistent problems, such as irregular mechanical properties for the final part, reduced production speed and therefore lower productivity, etc. Dr. Hagedorn cites another crucial point in addition to the lack of industrial standards, as well as design guidelines: “Probably the most important point is often the lack of competence in using the process. In contrast to conventional manufacturing, there is unfortunately still no apprenticeship for LPBF. As a result, machine tools are operated by engineers. The expectation is then often that the business case will fall out of the machine on its own.”
Kobayashi is also aware of these limitations, but at the same time he raises the point that they don’t have to be permanent limitations, “Personally, I think these are all valid points and there is a lot of room for improvement in all these areas. But these things are a function of development time and economic factors. As an industry, we are at a pivotal moment where vendors like myself need to engage with customers and support them in any way we can to help them succeed in their first round of implementations. Size constraints can be overcome with innovations in gas flow control, materials can be made available through material development combined with process parameter development, but there must be sufficient economic demand from users to accelerate this development.”
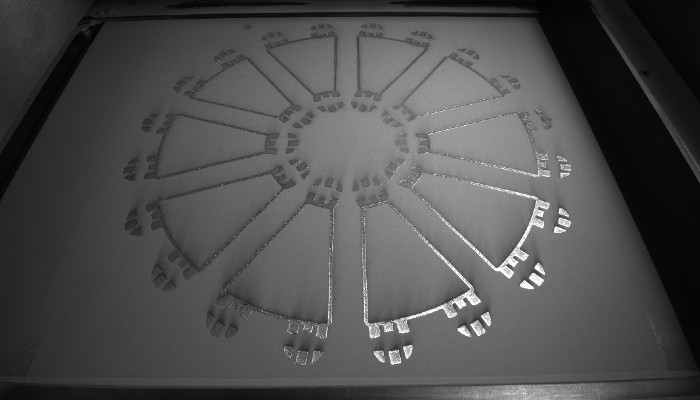
Powders need to be developed specifically for additive manufacturing to further improve part quality. (photo credits: GF Machining Solutions)
Necessary steps for successful integration
To maximize Powder Bed Fusion’s benefits to the company and to work around its limitations, successful implementation is critical. “Because it’s a relatively new technology, not many companies have a wealth of the necessary skills in-house,” Kobayashi explains. For this reason, he recommends taking on outside help to train employees. Dr. Hagedorn agrees with him on this point and adds: “When introducing LPBF as an industrial manufacturing process, it is always advisable to call in competent advice. This is particularly true since there are no trained LPBF personnel available on the free market. In particular, occupational safety in handling powder materials, quality assurance and application-dependent post-processing steps should be taken into account when introducing LPBF as a supplement to manufacturing capacities.”
Occupational safety in particular is of great importance, as metal powder carries certain health risks. For this reason, filling and sieving, as well as post-processing steps, must always take place in a closed environment, as the free powder is very fine and easily dispersed. In addition, in the case of LPBF, the lasers also represent a potential hazard (temperature control, laser radiation, wavelength, etc.), as well as the possible risk of explosions and fire hazards. Therefore, for integration, it is essential to have enough space to place the printer as far away as possible from other activities. It is also recommended to have a suitable filtration system and a fire extinguisher. In addition, only people who are familiar with the 3D printer and the regulations should have access to it. Employees can learn the handling and regulations in 3D printing courses or trainings.
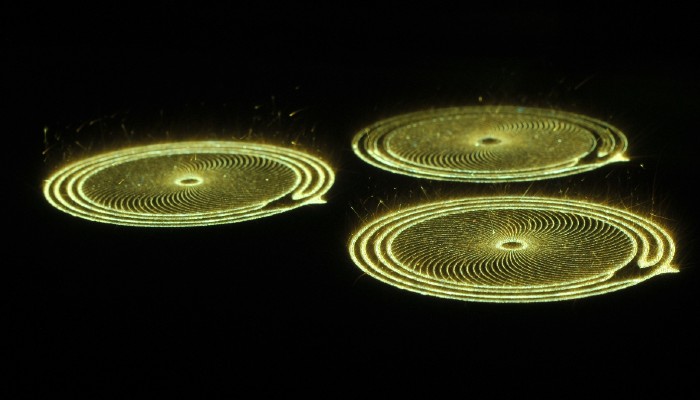
Powder Bed Fusion is not without danger and should therefore only be used in compliance with safety standards and by trained personnel. (photo credits: Aconity3D)
Dr. Lopéz also agrees with the other two experts on this point, adding that there is also “a need for systems engineering (not just the LPBF machine itself, but preparation, post-processing of powder and components, metrology, post-processing, etc..)”. Kobayashi elaborates on this statement, saying, “The printing process itself is heavily software-driven, which means you need to (re)think your digital strategy for managing all the data that is processed, stored and ultimately reused.” Dr. Hagedorn concludes, “The industrial and professional use of LPBF remains a craft that can be learned but must also be mastered in order to manufacture efficiently and economically.”
Powder Bed Fusion – The Future of Additive Metal Manufacturing?
Powder Bed Fusion offers some advantages that cannot be achieved with conventional manufacturing methods, such as design freedom, flexibility and short development times. At the same time, the technology is currently still facing some challenges, including the lack of skilled personnel, component size and unit quantities. However these challenges could perhaps disappear in the future as the technology is further developed and there is more widespread use. Nevertheless, Dr. Lopéz and Dr. Hagedorn agree that powder bed fusion will not replace conventional manufacturing methods. Dr. Hagedorn explains, “I personally don’t think LPBF will displace, or replace, conventional manufacturing methods. Rather, I think LPBF is a welcome extension and complement to conventional manufacturing methods, enabling exciting new high-tech applications. In particular, the need for conventional mechanical finishing of functional surfaces will remain a necessity for the foreseeable future.” Dr. Lopéz agrees, concluding, “LPBF will become an integral part of industrial manufacturing processes.”
Finally, a few last words from our experts:
Dr. Yves Hagedorn: “Additive manufacturing and especially L-PBF as an established process shows great potential to enable better products for tomorrow’s more demanding applications. I would like to take this opportunity to call for more dialogue between experts and users in order to exploit the full potential of this technology. The development impulse for success stories should therefore come from the user’s point of view and be developed jointly for success.”
Sadato Kobayashi: “I don’t think every company needs to integrate PBF into their organization, but every engineering and manufacturing company should at least consider how they can benefit from it.”
Dr. Elena Lopéz: “If you do not use LPBF or AM processes, you will lose competitiveness! AM is here to stay and will soon become an integral part of the production chain!”
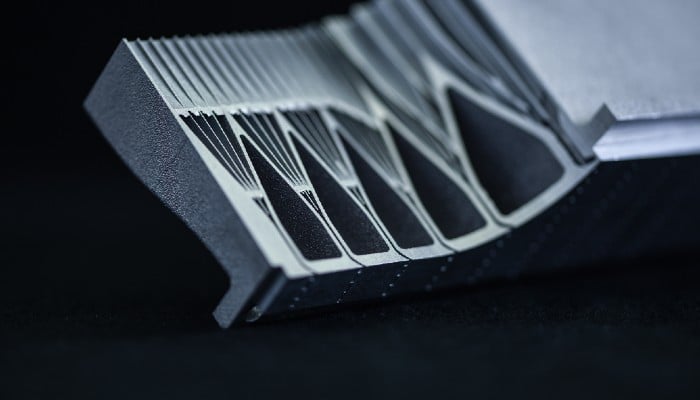
Powder Bed Fusion is an extension of traditional manufacturing methods that holds a lot of potential. (photo credits: Aconity3D)
What do you think about integrating Powder Bed Fusion into your business? Let us know in a comment below or on our Facebook and Twitter pages! Sign up for our free weekly Newsletter here, the latest 3D printing news straight to your inbox!