Evolve Additive Solutions on its STEP Technology for Agile Production
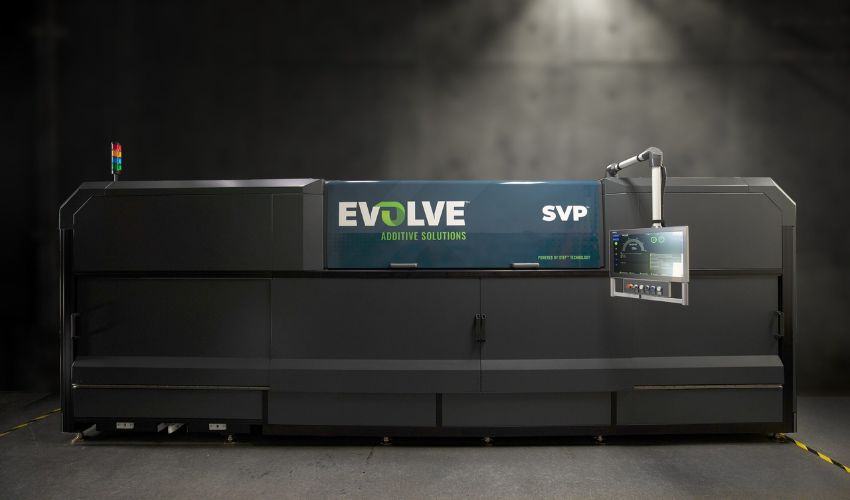
Among the well-known advantages of additive manufacturing is the digitization of production: the ability to quickly produce on-site and on-demand, with only the necessary material. This is also why AM is seen as a way to unlock Agile Manufacturing, i.e. a way of creating and producing things in a more flexible and adaptable way than traditional methods. To do this, companies must be able to change or alter the production process quickly and easily to better meet customer needs and demands. With this in mind, in 2017, the company Evolve Additive Solutions was born, first incubated in Stratasys before becoming an autonomous entity. With its innovative STEP (Selective Thermoplastic Electrophotographic Process) technology and 3D SVP™ (Scaled Volume Production) platform, Evolve aims to overcome the barriers still present in additive manufacturing to take it to the next level, achieving mass production and results comparable to injection molding. To find out more, we had the pleasure of interviewing Joe Allison, CEO of the company, who not only told us about Evolve and its mission, but also about his long journey in the world of additive manufacturing.
3DN: Could you introduce yourself and tell us about your background and your connection to 3D Printing?
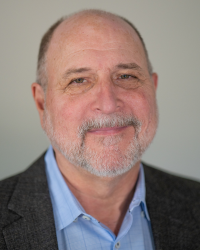
Joe Allison, CEO of Evolve Additive Solutions
Hello, my name is Joe Allison. I studied mechanical engineering and received my Bachelor of Science degree from the University of Southern California. Straight out of college I started working as a CAD/CAM applications engineer and after about four years doing that, the first 3D printer was introduced by 3D Systems. I was so intrigued and excited by the new technology at the time, I pursued a job there and worked as an R&D engineer for 3D Systems from 1988-1991.
In pursuit of an even greater career and life for myself and my family, I followed my entrepreneurial passions and founded Solid Concepts – one of the earliest, and over time one of the largest, 3D printing service bureaus in the world. I led Solid Concepts as its CEO for over 23 years before selling it to Stratasys in 2014. I have enjoyed dedicating more than 35 years now to spearheading the practical demonstrations of new software, printing and manufacturing processes, and materials to meet the requirements of new, challenging applications.
3DN: How did Evolve Additive Solutions come about? What is its mission?
What we refer to as our proprietary STEP technology today, was originally incubated within Stratasys. In 2017 Stratasys spun it off as its own new entity and thus the company Evolve Additive Solutions was born. Evolve has since commercialized both the SVP™ (Scaled Volume Production) 3D printer, as well as an on-demand parts production service called STEP Parts Now. Our mission is all about impact: to enable customers to create breakthrough solutions from prototype through production using genuine thermoplastic materials at best-in-class precision, quality and productivity. By delivering on that every day, we see a future where STEP becomes the pre-eminent digital plastics manufacturing technology.
3DN: When and how did you get connected to Evolve? And What keeps you most excited to lead Evolve as its CEO?
I sold my on-demand parts manufacturing company, Solid Concepts, to Stratasys in 2014, and continued to work at Stratasys as the CEO of its combined parts business for nearly four more years. During that time, I learned about and witnessed STEP Technology firsthand, while it was still being developed by Stratasys in a lab. I retired from Stratasys in 2018 and went on to co-found 3D Ventures, an informal group of seasoned entrepreneurs, investors, managers and operators each with decades of experience in additive or related spaces who coordinate regarding investments and other business opportunities.
By that time Stratasys had already spun off the technology under a separate and new entity, Evolve Additive Solutions, and because I remained amazed by Evolve’s technology and knew its founders and leaders, I eventually introduced my 3D Ventures partners to STEP and its unique capabilities. We ended up pulling together two years’ worth of funding for Evolve, and about a year after that in 2022 I accepted the position of CEO for the company.

Factory floor of Evolve SVP 3D printers
I finally found a plastics additive manufacturing technology that fulfills that agile production dream, and we have a passionate, inspiring team to bring it to market and finally deliver on decade-old promises of additive manufacturing. I couldn’t be more honored to finish my career by launching this truly differentiated additive manufacturing solution.
3DN: Could you tell us more about STEP Technology and how it works?
Evolve’s STEP Technology was developed specifically for production manufacturing. STEP stands for Selective Thermoplastic Electrophotographic Process, and it uses the proven, high-volume 2D printing process to create a 3D part using heat, pressure and cooling to fuse the part material together layer by layer. STEP leverages the Kodak NexPress™ print engine, the highest deposition 2D print engine in the world, to image each layer.
This use of electrophotography in additive is incredibly unique, and it is what enables STEP to produce such high-fidelity parts. What’s more, STEP has the ability to lay down particles in a very precise way and place two separate voxels of 2 different materials, side by side in the same layer (part and support).
3DN: What advantages does STEP Technology offer? What markets are you targeting?
We believe STEP Technology is the only viable additive manufacturing alternative to injection molding in the market today. With other additive processes, you have to make sacrifices – either in resolution and feature fidelity, or in mechanical properties, or in aspects of quality and repeatability. With STEP you don’t have compromise in these areas. Ultra-thin layers, the smallest of particles, real engineering-grade thermoplastic materials such as ABS, Nylon PA-11 and others, and a closed-loop printing process all combine to deliver strong, fully dense parts, with unmatched fidelity and near injection molding surface finish and mechanical properties.
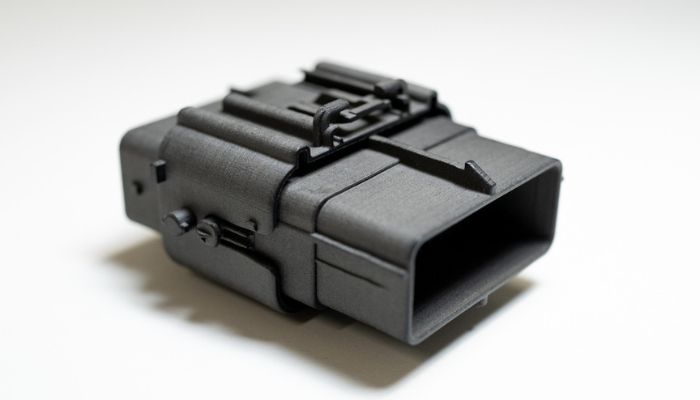
Electrical connector 3D printed using STEP Technology
As for target markets, the opportunities are endless. We are in a stage where we discover and learn about new best-fit applications every day from our customers – especially with the increase in part production orders we’ve been getting through our new on-demand parts service, STEP Parts Now. Customers are turning to STEP for prototype parts, bridge production, and end-use applications, as they realize the value and risk mitigation in being able to leverage a single manufacturing technology from design through production. STEP is uniquely positioned to deliver on challenging applications such as fluid and airflow components, electronic interconnect housings, badging, plating and more.
3DN: You have recently opened up to Europe. What does this step mean for you, and what projects can we expect from Evolve in the future?
The launch of our on-demand parts production service, STEP Parts Now, as well as the introduction of our partnership with alphacam Gmbh to service Europe, is all about lowering the barrier to entry in trying this relatively new technology, and providing greater and easier access to STEP around the world. With this we gain an even greater understanding of suitable applications – and at larger volumes – for STEP.
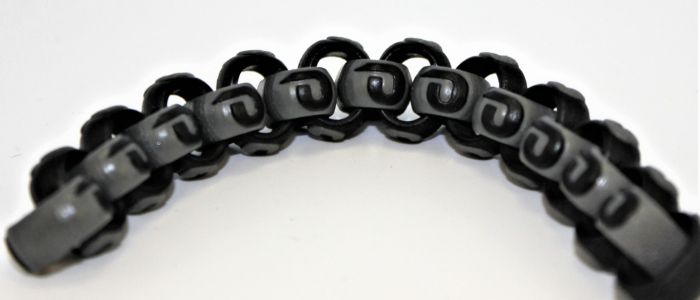
Co-printed chain in Black and Gray ABS using STEP Technology
As for ongoing projects, we believe the future lies in the expansion of our materials offering. We remain focused on developing that out to include polycarbonates, TPEs, and additional flavors of Nylon and ABS, such as fire-retardant. Additionally, with its four print engines, we’ve demonstrated that the SVP can print multi-colors and multi-materials (co-printing) within a single part and build. I believe we’ll see more applications demanding this unique and impressive capability as we bring it to market.
3DN: What do you see as the next big opportunities for the 3D printing industry?
My vision for 3D printing is yet to be fulfilled. Early in my career I helped champion some of the first additive technologies for simple prototyping. But the greatest value from 3D printing is only realized when you can print production parts, anywhere in the world without breaking down one production line and having to set up another. When you can just print what you want, where you want it, and when you want it – I call this Agile Production. Metal 3D printing technologies are pioneering this path now, but there are too few plastic 3D printing technologies that have both the fidelity and material choices to provide these benefits. Evolve is addressing that gap.
3DN: Any last words for the readers?
At Evolve we know we have the ability to produce tough, functional and beautiful plastic additive manufactured parts straight off our SVP printer (without any post-finishing required). But with any new technology like this on the market, we understand that seeing is believing, and so we need to continue to get more STEP parts out into more hands in order for many more companies and individuals to realize the difference and value from STEP for themselves. If you’re at all curious, please reach out and inquire. We’d be happy to send you a free sample, or print a custom part for you!
What do you think of Evolve Additive Solutions and its innovative STEP technology? Let us know in a comment below or on our LinkedIn, Facebook, and Twitter pages! Don’t forget to sign up for our free weekly newsletter here, the latest 3D printing news straight to your inbox! You can also find all our videos on our YouTube channel.
*All Photo Credits: Evolve Additive Solutions