Everything You Need to Know About Wax 3D Printing
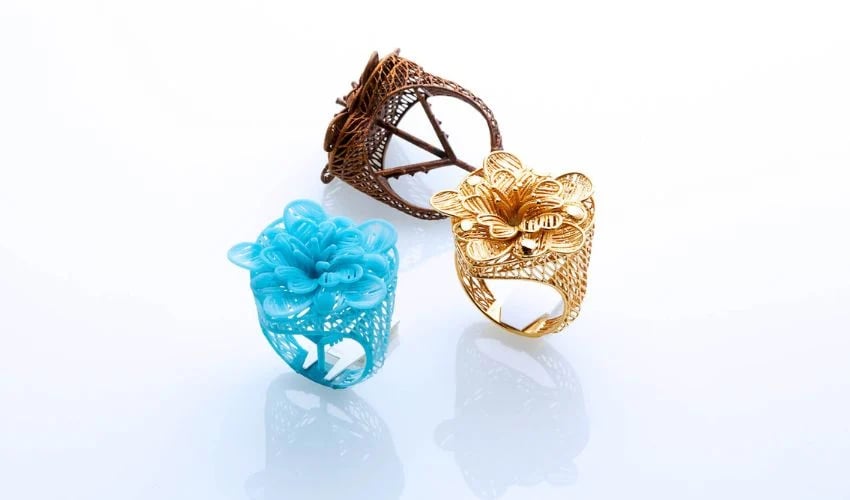
The term wax 3D printing is somewhat misleading, as in fact should be considered indirect 3D printing. In other words, 3D printing is not used to manufacture the final part, but as a step in the process. Wax 3D printing for example makes it possible to produce wax molds that serve as models for the final part. Wax is not the material of the final part. It is simply used to create the shape and is then melted. As the shape of the wax does not ultimately exist and is “lost”, it is often referred to as lost-wax casting.
As you may have guessed, the lost-wax process is a casting process which enables small, identically cast parts to be produced with few finishing steps. It is traditionally highly valued for its dimensional accuracy, detail and surface quality. Wax 3D printing has the same objectives, but the difference is that the mold is 3D printed rather than hand-made.
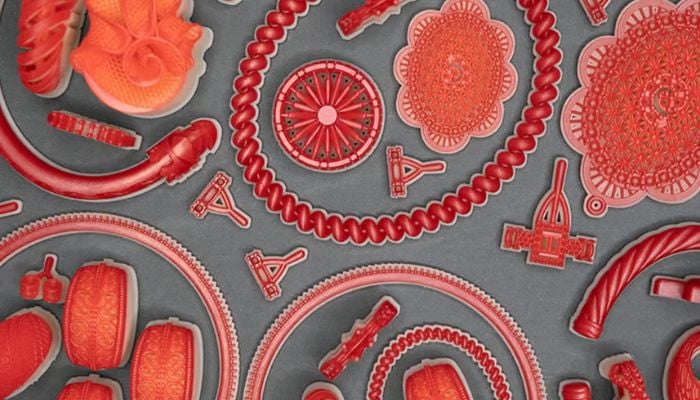
3D wax printing was originally based on the lost-wax principle (photo credits: 3D Systems).
As mentioned, wax 3D printing is primarily used to make molds, which are then used as a form for metal objects, precious or otherwise. The advantage of wax is that it burns with almost no residue, and does not require complex mold processing. In addition to special printing wax, there are also burnable filaments and resins for the same purpose. 3D technology makes it possible to print almost any design and combine cast-iron quality with complex structures. So let’s take a closer look at the process.
How Does Wax 3D Printing Work?
The first step is to design the final part. This is done using 3D modeling software or scans of objects to be reproduced identically. Next, the model is printed from a wax-like plastic material. This requires a special wax 3D printer that can process this material.
Print supports may be required if the design is very complex, featuring overhangs and bridges for example. These structures must be removed after printing and the model cleaned. Small surface irregularities may need to be smoothed out. Unlike 3D wax printing, the model is designed and crafted by hand in traditional lost-wax casting. The other steps are no different.
Once the wax model has been printed and cleaned, the operator attaches it and other models to a “casting tree.” This is a hollow bar with several fixed elements, which are immersed in a liquid mass. This may be ceramic, clay or plaster, and serves as the outer shell and, ultimately, the casting mold. Wax models are surrounded by thin layers of the relevant material, which is injected using casting funnels. The layer of material surrounding the wax model must then be dried or fired in an oven.
The wax or wax plastic melts, flows or burns off, leaving only the green shape of the final molded part. The molten final material is then inserted into this detailed impression of the construction or final part. Once this has solidified, the mold is broken. The finished object is then held in your hands. Depending on the application and the material, it must then be reworked in more or fewer stages.
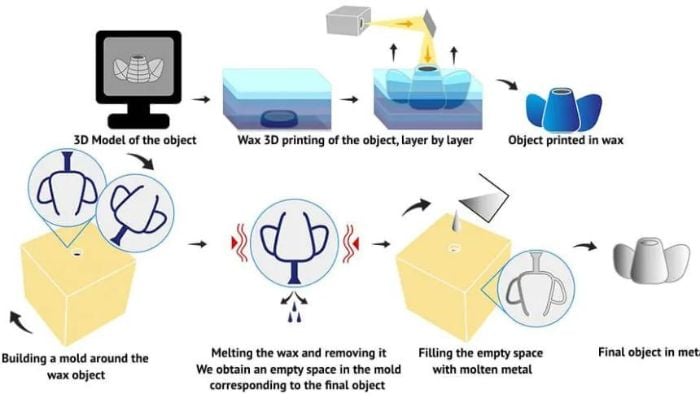
This graphic illustrates the wax 3D printing process (photo credits: Sculpteo)
Advantages and Limitations of Wax 3D Printing
Wax 3D printing achieves high resolution, with an accuracy of around 25 μm. However, accuracy also depends on the 3D printing process chosen and cannot be generalized. Although 3D wax printing can achieve a low tolerance margin for parts, the relevant standards, such as the VDG standard (which includes construction guidelines for the design of castings in cast iron materials) or the relevant DIN ISO standards for casting, must be taken into account here too. Meeting them can be a challenge.
The technology is also attractive for its value for money. 3D printing makes it possible to produce prototypes and small series at lower cost. It also offers advantages in terms of time. Analog molds made to order take between two and twelve weeks to manufacture and deliver. 3D printing takes just a few hours, depending on the model, and can be carried out directly on site. The fact that a model can be reworked quickly means that difficulties can be addressed immediately: 3D printing makes it easier to iterate.
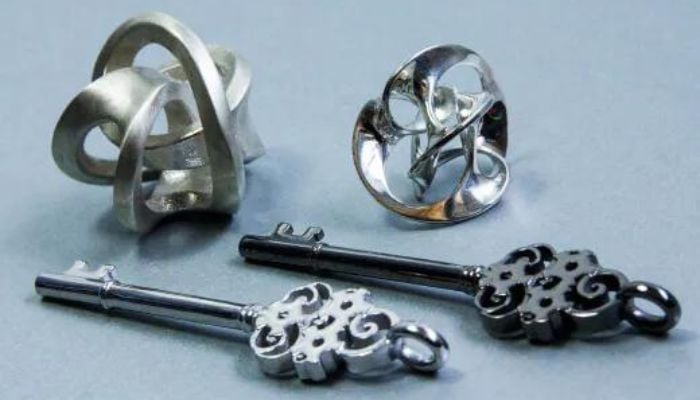
Wax 3D printing allows design freedom and rapid adaptations for prototypes and small series (photo credits: Sculpteo)
The process also scores points in terms of sustainability. In 3D printing, only the materials required for the model are printed, so there is virtually no waste. Wax waste is either incinerated without leaving a trace, or reused in other areas.
If you opt for this process, be aware that it requires a little patience and is not suitable for large models. It’s an indirect manufacturing method, which will require more time than other 3D printing processes where you can obtain your part directly.
Where Is Wax 3D Printing Used?
When it comes to applications, there are many areas in which wax 3D printing is used. These are mainly applications where accuracy, precision and detail are required. For example, the process is often used in dentistry to create dental impression materials. Another example in the medical field is the manufacture of acetabular cups as implants. Acetabular cups consist of a shell-shaped head whose surface contains hundreds of tripods, i.e. cross-shaped filigree anchors.
Wax 3D printing is also used to manufacture cast-iron models or original models in mechanical engineering. In addition to mold making, this process is also used in the field of model making. This makes it possible to produce collector’s items and miniature editions.
But it is above all in the jewelry sector that 3D wax printing has proved its worth. Jewelers use wax prints as models for molds. In this way, they can create prototypes and produce pre-series, then use the models as molds which they fill with precious metals to make the final piece of jewelry.
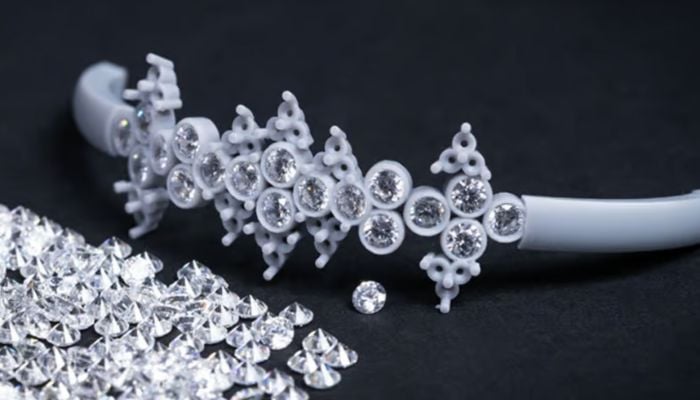
Photo Credits: 3D Systems
Technologies, Manufacturers and Materials
There are several processes involved in creating the model. If a wax-like filament is used, FDM technology can be employed. However, SLA and material jetting technologies are much more commonly used. In the case of stereolithography, a wax-like resin is used to print the mold. 3D Systems had developed an SLA process called QuickCast, designed for printing models and molds in the aerospace industry. The company also has another wax 3D printing process, MultiJet Printing.
Prodways was another important manufacturer in the wax 3D printer market with its Solidscape solutions, which work with Drop-on-Demand technology. However, the company recently announced that it was discontinuing its activities in this segment. Binder jetting is also suitable for wax 3D printing. For example, Voxeljet’s printer portfolio includes the VX1000, which prints wax, ceramic and sand.
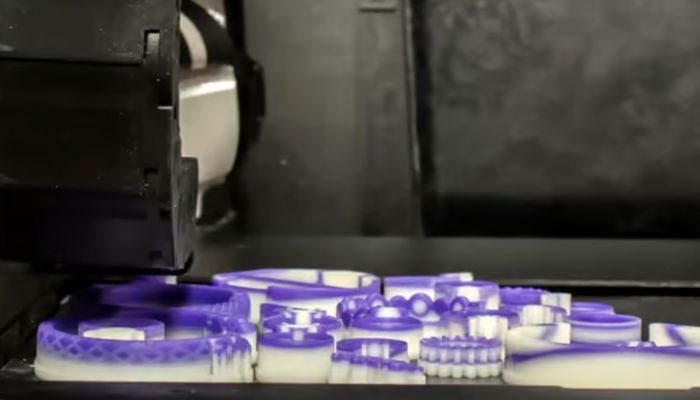
3D Systems offers several printing solutions for 3D wax printing (photo credits: 3D Systems)
So it makes sense that the various manufacturers of printing solutions also offer materials for this purpose. Wax for 3D printing is, as we mentioned at the beginning, a wax-based plastic material. In general, waxes can be classified into three categories: natural waxes (e.g. beeswax, soy wax), mineral waxes obtained from fossil fuels (e.g. kerosene wax, lignite wax) and synthetic waxes (polyolefin wax for creams, hydrosil wax). The latter are used for 3D printing.
If printing supports are required, two different types of wax must be used. The support wax must have a lower melting point, so that the supports can be melted away, but the wax model remains intact. Manufacturers include 3D Systems, Polymaker and Formfutura.
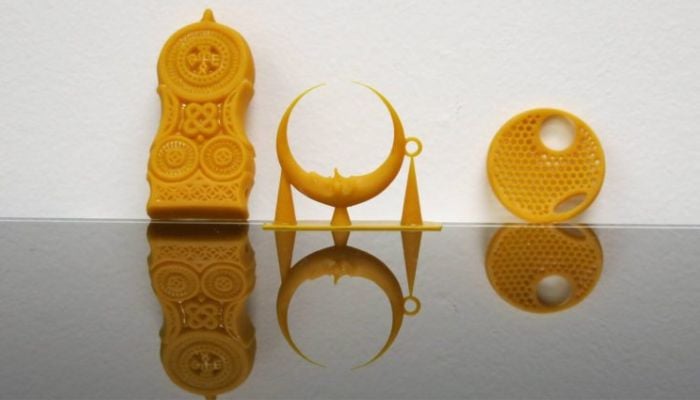
3D-printed wax parts (photo credits: Sculpteo)
Waxes and wax 3D printing may represent a niche within additive manufacturing technologies and applications, but they offer solutions that other processes and materials cannot achieve. Wax 3D printing is particularly popular in jewelry and other sectors where intricate part details and structures are required, and offers a wide range of possibilities.
Do you use wax 3D printing? Let us know in a comment below or on our LinkedIn, Facebook, and Twitter pages! Don’t forget to sign up for our free weekly newsletter here, the latest 3D printing news straight to your inbox! You can also find all our videos on our YouTube channel.
*Cover Photo Credits: MOIIN