Everything You Need To Know About Cold Metal Fusion
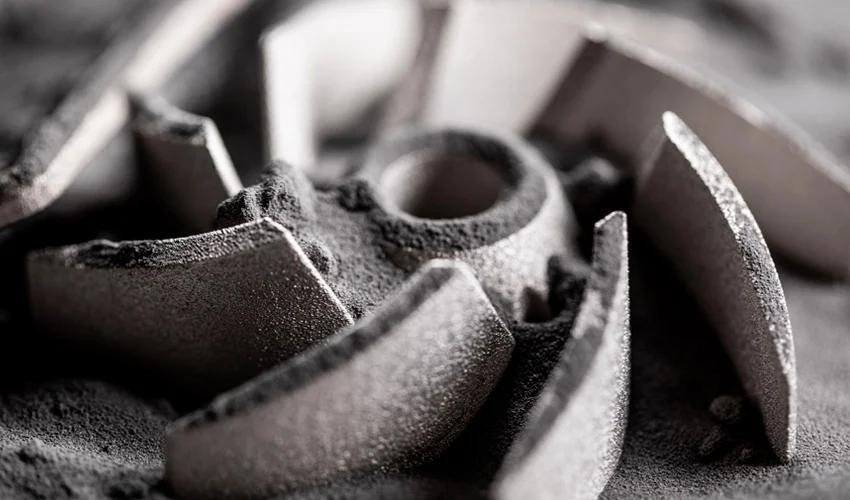
Today, the manufacturing industry is increasingly moving towards metal additive manufacturing solutions. However, these machines are often expensive for companies entering this field. Consequently, the cost of metal 3D printers can be a major barrier to market entry. Luckily, there is a promising trend emerging in the development of polymer powder-based additive manufacturing solutions, which are becoming increasingly affordable. Among these, Selective laser sintering (SLS) technology stands out as a compelling alternative for producing final polymer parts across a wide range of applications. But what if the advantages of metal 3D printing could be combined with the low-cost solutions of SLS manufacturing? This is now possible thanks to Cold Metal Fusion technology.
Developed by German company Headmade Materials, Cold Metal Fusion (CMF) 3D printing is a method of indirect metal fabrication. Specifically, the company focuses on the development of powder materials compatible with this system, with no immediate plans for manufacturing 3D printers—at least for the time being. These materials are comprised of metal particles encased within a polymer binder layer. Based on a powder bed process, the CMF system enables those with SLS machines to create final metal parts. Let’s delve deeper into the properties of this technology and explore the advancements it introduces to the additive manufacturing industry.
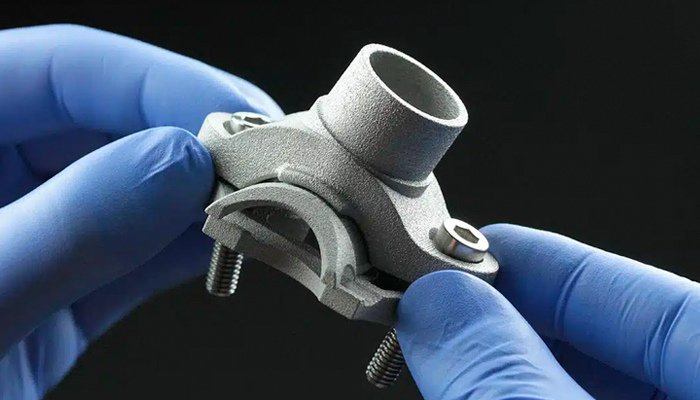
A titanium part 3D printed using Cold Metal Fusion technology.
How the Cold Metal Fusion Process Works
As with any 3D printing process, it all starts with designing the models in CAD software. An important aspect to remember when designing parts for CMF (and in general for any sintering-based process) is that parts can shrink during fabrication. In the CMF process, parts achieve a high density, minimizing the shrinkage that occurs during sintering. When utilizing metal powder as a raw material, parts may uniformly shrink in all directions (XYZ) by approximately 14%. These few millimeters of shrinkage must, therefore, be taken into account. The digital file is then sent to the slicer to segment the part and define the manufacturing parameters.
Once the design and slicing processes are done, we can move on to creating the parts. Materials compatible with this technology include 316L stainless steel, cobalt-chromium, Ti6Al4V titanium, and tungsten. Other materials still under development include Inconel, aluminum, and tool steel. When considering 3D printing, a common question that arises regarding CMF technology is: how can it be deemed a ‘cold’ method while requiring hot sintering? In essence, during the printing process, the plastic binder is melted at low temperatures (up to 50°C/122°F), achievable through the power range of low-power polymer sintering systems. Thus, despite involving sintering, it qualifies as a ‘cold’ process due to the relatively low temperatures involved.
As with all SLS 3D printing processes, a laser is used to sinter the powder particles deposited on the printing plate, layer by layer. Additionally, as it is a powder bed-based method, no printing support is required since the powder itself serves as the support. This method also facilitates a process known as ‘stacking’, enabling the superposition of multiple parts within the same manufacturing process. In this case, with the metal particles protected by the polymer particles, they are not exposed to air, preventing oxidation of the metal. Additionally, the cold process has no thermal impact on the unsintered powder, which enables its reuse in future prints.
The Importance of Post-Processing
When using Cold Metal Fusion technology, post-processing is a key step. After removing the “green” parts from the SLS printer, the plate is cleaned to remove unsintered powder. This step can be carried out using pressurized air or a water jet, given the high stability of green parts. Next comes debinding, a process during which the models are immersed in a solvent to remove the sintered plastic from the metal structure. The resulting parts are ready for the final stage – the actual sintering of the metal.
During this final stage, the parts are placed in an oven, which heats them and removes any remaining binder inside. The remaining metal particles are then sintered to form the final metal parts. It should be noted that a specialized oven capable of reaching metal sintering temperatures is required for this final stage.
Industry Advantages and Applications
The main advantage of cold metal melting technology is the ability to create final metal parts using SLS 3D printers. These machines are more widely available on the market, and they’re generally much more affordable than laser powder bed fusion (LPBF) solutions. In fact, CMF 3D printing can be performed on basic SLS machines such as those from Sintratec, further minimizing the initial investment cost for businesses. The Headmade Materials website adds, “This is the lowest investment cost of any metal 3D printing process for mass production of up to 100,000 parts.” This assertion suggests that CMF 3D printing presents a more cost-effective option compared to MIM (metal injection molding) or die casting.
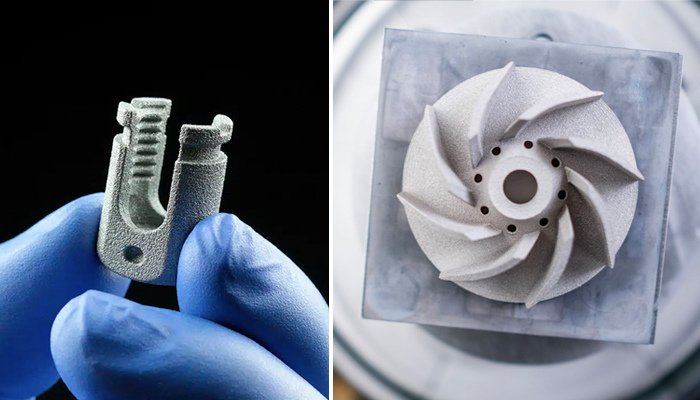
Examples of parts created using the CMF process.
This manufacturing method is also an alternative to binder jetting 3D printing, which is also capable of creating metal parts. As such, many applications will be similar to those of LPBF and binder jetting technologies. Industries that will benefit most from this manufacturing method include automotive, aerospace, medical and consumer goods.
To cite a few examples, Sturdy Cycles has opted for CMF 3D printing for its production of titanium parts. This has improved the efficiency of sports equipment development, reduced costs and enabled on-site manufacturing. Another success story can be found in the international Formula Student competition, where Headmade Materials sponsored one of the participants. Specifically, the team representing Esslingen University of Applied Sciences (Germany) received an air/oil separator created by Cold Metal Fusion. The component, made from Ti6Al4V titanium alloy, features optimized weight and high load-bearing capacity. Lastly, German tool manufacturer Utilis AG also turned to CMF. It has developed a steel cutting tool holder with a unique internal cooling channel capable of increasing cutting tool performance by 185%.
The Future of 3D Printing CMF
While Cold Metal Fusion technology is relatively new, its uptake is rapidly expanding across various industries. The idea of a selective metal laser sintering process is becoming increasingly popular on the market, and many companies are already considering adopting it. Notably, this manufacturing system is promoted by the “ColdMetalFusion Alliance”. This is an initiative by Headmade Materials after the startup emerged as part of the AM Ventures venture capital fund, owned by EOS. Several industrial companies have joined the alliance, including mimPlus, Element22, and Miba, as well as 3D printer manufacturers such as Farsoon Technologies (developer of SLS solutions).
The aim of the ColdMetalFusion Alliance is to industrialize the technology through common standards between sintering and additive manufacturing. Member companies share not only standards, but a similar culture and mindset. The continuing progress of this system and the compatible materials to come will enable this technology to extend to many more industries and applications.
Did you know the Cold Metal Fusion process? What do you think of its advantages? Let us know in a comment below or on our LinkedIn, Facebook, and Twitter pages! Don’t forget to sign up for our free weekly newsletter here, the latest 3D printing news straight to your inbox! You can also find all our videos on our YouTube channel.
*All Photo Credits: Headmade Materials
we are finalizing a research to use CMF to produce medical devices.
We have a key question: what data are available about the FULL removal of polymer from the printed parts after debinding and sintering?
Which tests could detect any residual polymer parts in the medical devices, especially those with surface 3D net?
Thanks