What is the environmental impact of metal additive manufacturing?
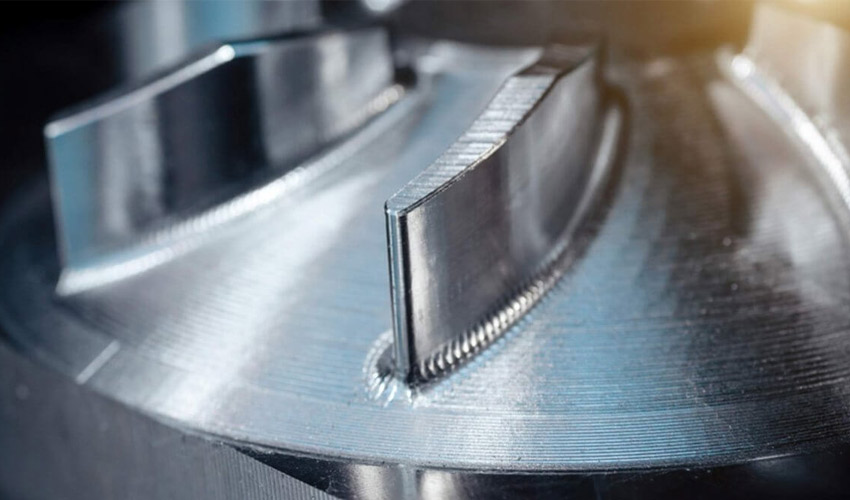
Not so long ago, the Additive Manufacturer Green Trade Association (AMGTA) released its report on the environmental impact of metal additive manufacturing. Conducted by Jeremy Faludi of Delft University of Technology and Corrie Van Sice of Dartmouth College, the study compares metal printing processes with traditional methods and asks whether they ultimately offer environmental benefits, in addition to the economic and functional benefits they offer in some cases. By conducting this survey, the AMGTA aims to elevate the debate: can companies plan responsible additive manufacturing strategies? Do metal 3D printing technologies offer a more sustainable future?
It is certainly a growing process: according to a Grand View Research study conducted this year, metal 3D printing is estimated to be worth $1 billion by 2020, experiencing a yearly 27% growth rate over the next few years. Combining different processes such as Laser Powder Bed Fusion, Directed Energy Deposition or EBM, metal additive manufacturing offers multiple advantages in production: design freedom, reduction in the total number of components and assembly steps, reduction in the weight of parts, personalization, etc. In some cases, and particularly for the design of small production runs, it has become an obvious alternative to traditional processes (as manufacturers are freeing themselves from the need to produce an expensive mold). But it is still a manufacturing method that is less well known, with challenges that still need to be established.
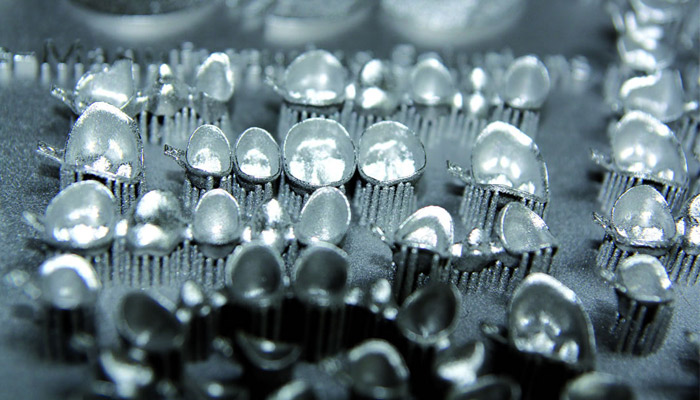
Metal additive manufacturing is particularly popular in the medical sector | Photo Credits: EOS
The environmental impact is one of them, and that is the focus of this study. The AMGTA states that it was carried out to “summarize current knowledge and identify areas where information is scarce, unclear and much needed“. The authors came to compare metal 3D printing and conventional manufacturing for each stage of a part’s life cycle, looking in particular at the impact of materials (especially stainless steel, aluminum and titanium) or their transformation. They also made this comparison by sector of activity, namely aerospace, automotive and medical, three industries for which metal AM has disrupted production processes.
The environmental impact of metal 3D printing is heavier
In conducting their study, the authors came to one conclusion: metal additive manufacturing has a larger carbon footprint per kilogram of material processed compared to traditional fabrication methods. This suggests that additive manufacturing is generally a less sustainable choice – so situations must be found where it brings other benefits. This is where the geometry of the part to be produced has a major impact: it would be preferable to machine a solid cube, but 3D printing is preferable to produce a lattice structure or a hollow shell.
Sherry Handel, Executive Director of the AMGTA, explains: “No one should expect additive manufacturing to be a more sustainable way of producing basic metal parts given the focused energy inherent in laser fusion, but it should provide a more sustainable path for the manufacture of finished precision components.“
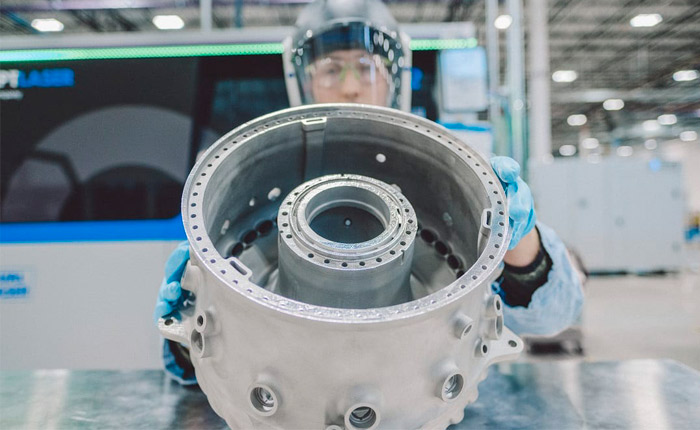
Metal additive manufacturing is attractive for reducing the number of components. In this case, GE Additive has gone from 855 parts to 12 in the manufacture of this engine component | Credits: Nick Hurm, GE Additive
The authors note, however, that more comparisons need to be made to be more accurate. They explain that they are currently lacking data, as the literature is not very extensive. Ideally, future assessments should also look at the full product life cycle, as processes such as raw material extraction, gas atomization and logistics will undoubtedly have a major impact on the resulting carbon footprint. Elements such as fail rates in 3D printing and post-processing will need to be closely studied, as they also impact the carbon footprint.
To conclude, the carbon footprint per kg of material in additive manufacturing seems to be about ten times higher compared to more traditional direct manufacturing processes, but where 3D printing saves a large mass of material, it can have lower manufacturing impacts than machining, especially for materials with environmental impact such as titanium. Finally, the AMGTA provides some recommendations for lowering the carbon footprint of additive manufacturing: it encourages users to optimize printer usage, whether by sharing printers or reducing unused build plate space; users can also choose metals that minimize processing energy, using factors such as melting point, reflectance and thermal conductivity. You can find the entire study HERE.
What do you think is the environmental impact of metal 3D printing? Let us know in a comment below or on our Facebook and Twitter pages! Sign up for our free weekly Newsletter, all the latest news in 3D printing straight to your inbox!