The Complete Guide to Electron Beam Melting (EBM) in 3D Printing
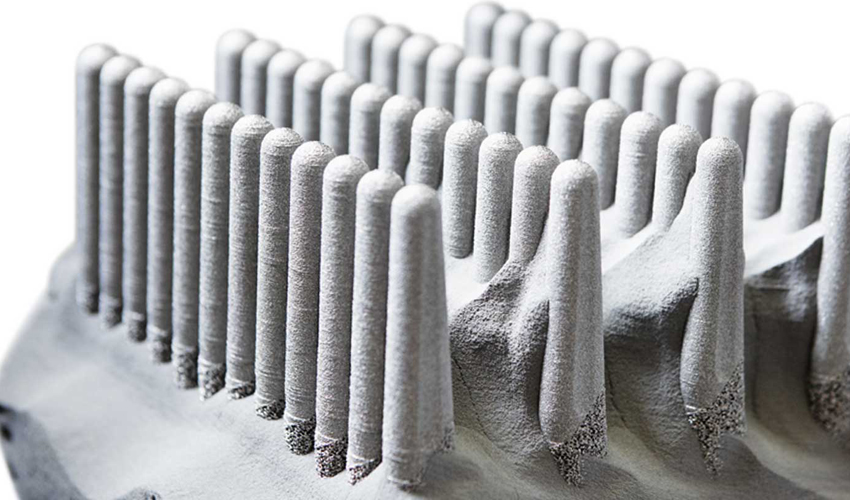
Electron Beam Melting (EBM) is part of the powder bed fusion family. Unlike Laser Powder Bed Fusion (LPBF), it uses, as its name suggests, an electron beam to fuse metal particles and create, layer by layer, the desired part. Marketed by the Swedish company Arcam in 2002, this process enables the creation of complex and highly resistant structures. Note that Arcam was acquired by GE Additive in 2016 and is the only one to market machines based on this process as of today.
The main difference with LPBF technology is therefore the heat source used. Here, EBM technology uses an electron beam produced by an electron gun. The latter extracts the electrons from a tungsten filament under vacuum and projects them in an accelerated way on the layer of metallic powder deposited on the building plate of the 3D printer. These electrons will then be able to selectively fuse the powder and thus produce the part.
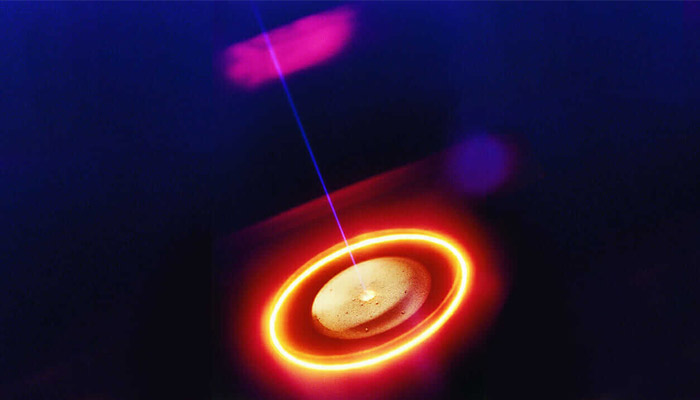
The EBM technology uses an electron beam | Credits: Arcam
The Electron Beam Melting process
Everything starts with the 3D modeling of the part you wish to create. You can model it using CAD software, obtain it by 3D scanning or download a model of your choice. The 3D model is then sent to a slicing software, also called slicer, which will cut it according to the successive physical layers of deposited material. The slicer will then send all this information directly to the 3D printer, which can then start its manufacturing process. The metal powder can be loaded into the tank within the machine. It will be deposited in thin layers that will be preheated before being fused by the electron beam. In particular, this step provides more support to the cantilever areas of the part being 3D printed. The machine then repeats these steps as many times as necessary to obtain the entire part.
Once the manufacturing process is complete, the operator removes the part from the machine and ejects the unmelted powder with a blowgun or brush. Following this, it’s possible to remove the printing supports (if any have been used) and to detach the part from the build plate. The post-printing steps can include machining of surfaces in contact with other parts, polishing, etc. In some cases, it may be necessary to heat the part in an oven for several hours to release the stresses induced by the manufacturing process.
Note that all manufacturing must take place under vacuum to properly operate the electron beam. This also prevents the powder from oxidizing when heated. At the end of the production process, a large part of the unmelted powder can be reused almost directly. It is easy to understand the interest that this represents for manufacturers, particularly in the aeronautics sector where it often happens that only 20% of the purchased material is actually used to produce the final part, the rest being removed by machining and sent for recycling.
Materials and Applications
As the process is based on the principle of electrical charges, the materials used must be conductive. Without this, no interaction can occur between the electron beam and the powder. The manufacture of polymer or ceramic parts is therefore technically impossible with an electron beam and only metals can be used. Today, titanium and chromium-cobalt alloys are mainly used – Arcam has restricted the range of compatible materials. In fact, to be allowed to use or test another material, users must undertake paid training and obtain an authorization to use the machine as they see fit.
EBM technology is mainly used in aeronautics and medical applications, particularly for implant design. Titanium alloys are particularly interesting because of their biocompatible properties and mechanical properties, they can offer lightness and strength. The technology is widely used to design turbine blades, for example, or engine parts. Electron Beam Melting technology will create parts faster than LPBF technology, but the process is less accurate and the finish will be of lower quality because the powder is more granular.
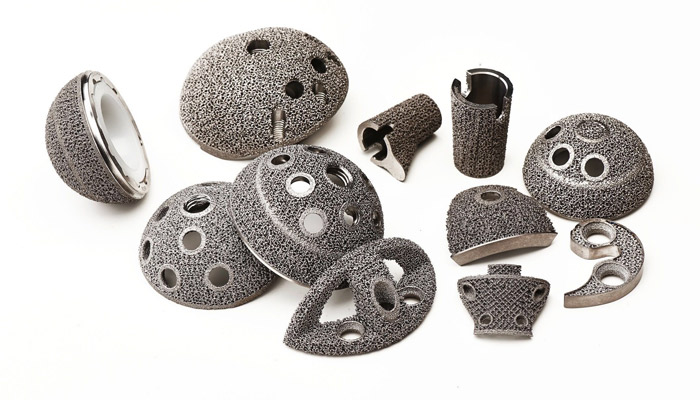
3D printed implants using an Arcam machine | Credits: Arcam
Laser or Electron Beam?
The question is regularly asked by manufacturers who are interested in metal 3D printing. The answer depends mainly on what applications you are interested in, because each process comes with benefits and limitations.
Strengths
- Manufacturing speed. The electron beam can separate to heat the powder in several places simultaneously, which significantly speeds up production. On the other hand, a laser must scan the surface point by point.
- Pre-heating the power before it melts limits the deformations and thus reduces the need for reinforcements and supports during manufacturing.
Weaknesses
- Precision. At the powder level, the electron beam is a little wider than the laser beam, which reduces the accuracy.
- The size of the parts that can be manufactured. Arcam’s largest build volume (on the Q20 machine) represents a diameter of 350 mm for a height of 380 mm. On the other hand, laser machines (such as the X-Line of Concept Laser) offer manufacturing volumes at least twice as high.
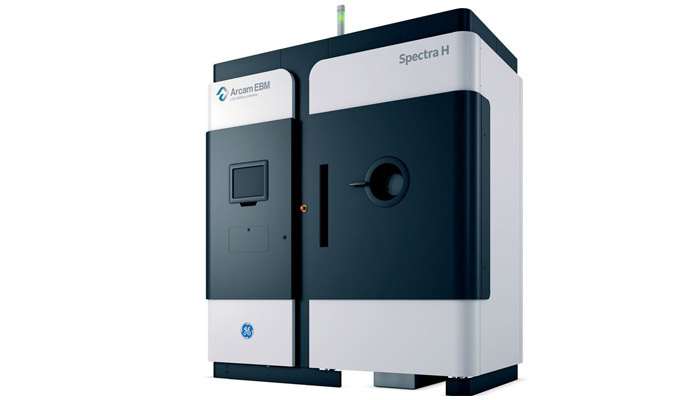
Arcam is the only manufacture of EBM 3D printers
that is very interesting but i want to know about its welding metallurgy ?
i want to know about its cooling behaviour
It is the only PBF process that can produce 100% parts, this is usually only achievable with DED processes
The demand for electron beam machines is estimated to grow in the coming years on account of an increasing need for advanced machines with greater accuracy in order to meet the stringent product quality and industry regulations and standards.