The ELAINE Project Is Researching Bioactive Bone Implants Made With 3D Printing
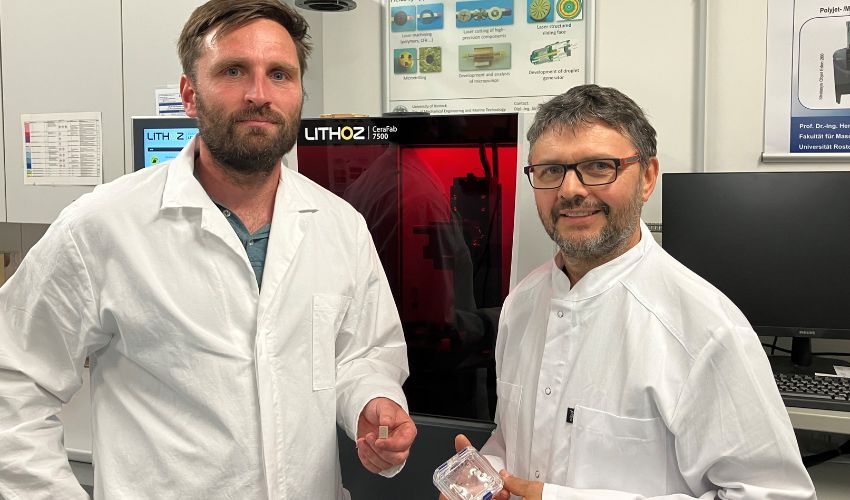
Bones have a high degree of self-healing capacity. It is for that reason that with bone fractures, which may come about after a skiing accident, bicycle fall or mishap, the bones are usually able to grow back together themselves. Although how long that may take varies depending on age and severity of the fracture, among other factors. However, if larger bone defects occur as a result of tumors, the bone can no longer regenerate itself. In this case, implants are used, usually made of titanium or the patient’s own bone material from other parts of the body. Now, 3D printing is the latest technology to be used. At University of Rostock, one research project is looking into the production of bioactive bone replacement structures. Specifically, this is the ELAINE – Electrically Active ImplaNtatE – project from the Collaborative Research Center 1270 headed by Prof. Dr. Hermann Seitz. As part of this project, scientists are experimenting with the production of bioactive bone implants by 3D printing.
Until now, titanium has often been used as a substitute material for bone. However, this can be difficult to adapt to individual anatomical conditions. In addition, titanium implants can loosen easily and thus cause long-term problems. An alternative therapeutic approach, is to remove bone material from the pelvis and transplant it to the damaged area. “But that is then additionally associated with another defect,” Seitz cautions. To be able to guarantee better implants with fewer side effects and better adaptation in the future, the ELAINE research group is making use of additive manufacturing and is on the way to treating bone defects with 3D printing technology.
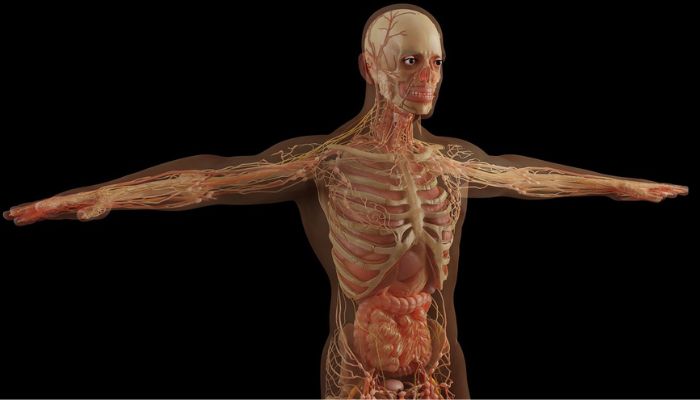
Bones have a high degree of regenerative power. For larger defects, however, the use of an implant is necessary. ELAINE is researching the production of bone implants using 3D printing (photo credits: Pixabay)
The ELAINE research group is working on the production of electrically active implants that behave similarly to bone structures themselves. The scientists are guided by the physiology of bones and use the known knowledge about the piezoelectricity of bones. Piezoelectricity occurs when solids are subjected to mechanical deformation and stresses occur there. When a bone is mechanically loaded, electrical signals are delivered to the tissues, stimulating growth. “Piezoelectricity is a key factor in continuous bone remodeling in the organism,” says Christian Polley, a doctoral student in Collaborative Research Center 1270 at the Department of Mircofluidics. “This so-called piezoelectric effect ensures that cells are stimulated to grow.”
Based on this knowledge, the research group created implants from piezoelectric ceramics, specifically barium titanate, using 3D printing and also worked closely with the Chair of Biomaterials at the Friedrich Alexander University of Erlangen-Nuremberg to do so. Barium titanate, is a piezoelectric ceramic that also generates voltage potentials under pressure. In ELAINE’s research approach, the barium titanate is combined with bioactive glasses. When in contact with bodily fluids, the material releases ions and thus unfolds its bioactivity. The bioactive material is then manufactured into an implant by 3D printing.
3D Printing Bone Implants That Mimic Real Bones
The advantage of 3D printing is that after digital reconstruction, the implant can be made to fit precisely in the 3D printer and the desired implants can be produced individually for each patient. “We know beforehand exactly what the puzzle piece has to look like,” says Polley. The 3D process used is LCM (lithography-based ceramics manufacturing) technology from Lithoz. In the case of ELAINE, the photosensitive polymer is loaded with the piezoceramic particles and then fed into the printer, where a filigree structure is created via light curing. In the course of thermal post-processing, the printed part is sintered. Although 3D printing itself takes only a few hours, post-processing takes place overnight. Due to the manufacturing process, the implants are sterile and biocompatible and could then be inserted into the patient.
“We are already successfully testing with simulation chambers in which the pressure in an organism can be faithfully mimicked,” said Seitz of the University of Rostock. “We want to have an implant that responds piezoelectrically to mechanical stimuli and is bioactive at the same time.” The goal is to have bone cells from adjacent tissue migrate into and colonize the porous implant. If the colonization and the formation of vessels are successful, the implant remains in the body.
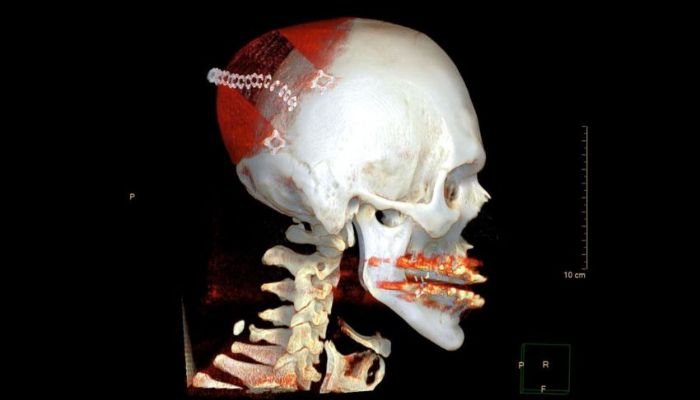
In the future, larger implants, such as those used to reconstruct the skull, could be made using a bone implant from the 3D printer (photo credits: Uniklinikum Salzburg)
Although ELAINE is well on its way with the results of the collaborative research center so far, a lot of basic research still needs to be done before these implants can actually be used. “This is because the underlying mechanisms must be understood down to the smallest detail,” Seitz explains. According to him, it is quite possible that another ten years will pass before these implants actually reach everyday clinical use. However, it is already clear that 3D printing will play a significant role in shaping the medicine of the future. You can find out more about ELAINE HERE.
What do you think about these bone implants created by 3D printing? Let us know in a comment below or on our LinkedIn, Facebook, and Twitter pages! Don’t forget to sign up for our free weekly Newsletter here, the latest 3D printing news straight to your inbox! You can also find all our videos on our YouTube channel.
*Cover Photo Credits: Joachim Mangler/Universität Rostock: Christian Polley (left) and Hermann Seitz (right)