Customised and 3D Printed Insoles from ECCO
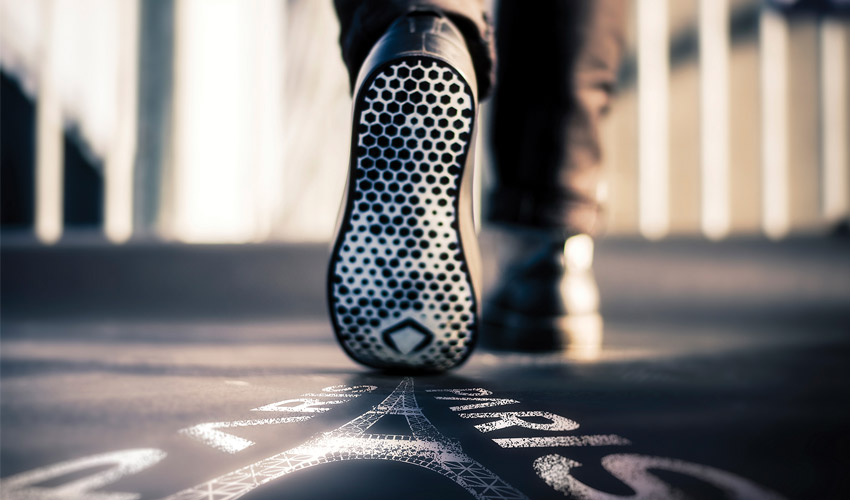
The Danish shoe manufacturer, ECCO showcased its customised shoes at Bon Marché Rive Gauche in Paris. For the first time in Europe, visitors will be able to test QUANT-U, a project in collaboration with Dassault Systèmes, which aims to create a sole entirely adapted to the morphology of each foot and the wearer’s walking parameters. 3Dnatives was able to test the device in one of the brand’s stores: results are very promising for the shoe industry!
We reported in March 2018 that ECCO opened its concept store in the Netherlands; the QUANT-U experience should open more doors in terms of product personalisation. The process of personalisation is divided into three steps: real-time data capture, sole modeling and localised 3D printing. A procedure that only takes an hour to be completed.
A three step experience
It all starts with a real-time analysis and digitisation of the foot. The wearer climbs barefoot on a kind of scale that scans his foot to generate a profile (length of the foot, width, shape, etc.) in a few seconds. More than 24 measuring points are present on the device. In order to obtain a more accurate result, the user then walks on a mat to measure the walking parameters: how the foot rests, what are the support points, etc.
All this data is then analysed by a learning algorithm that will allow the development of a numerical model using Dassault Systèmes’ 3DEXPERIENCE platform. The software expert explains: “The automatic learning and structural simulations will generate the digital configuration and test the physical constraints and strength of the material used for the midsole before validating and optimising it for 3D printing.
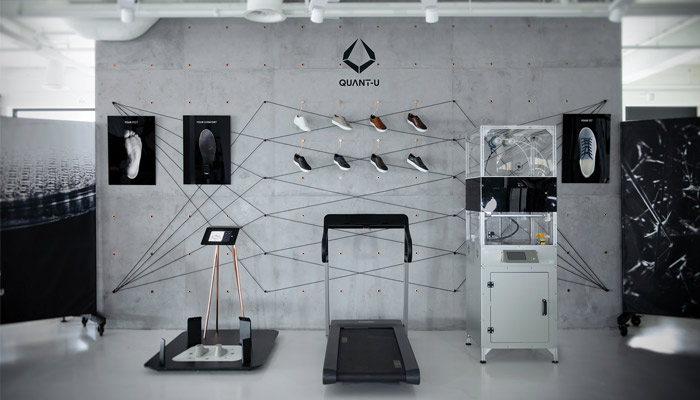
The person first needs to step onto the scale (left) and then walk on the ‘treadmill’
The last step corresponds to the printing of the sole. This is done on a German RepRap machine using high quality silicone. The soles can be printed in 3D anywhere and ready to be picked up in the store or delivered worldwide. Teo Pazanin, Resarch and Communications at ECCO, says: “We chose silicone because it is a material that is adapted to viscoelasticity parameters while offering durability, antibacterial properties and temperature stability. The 3D printed midsole is customised to meet individual needs for cushioning, stability, adjustment and energy feedback. The result is a customised comfort and fit.”
Each user will have access to his personal measurement data for future use. In the long term, ECCO wishes to offer different types of insoles, plus access to performance and health for example.
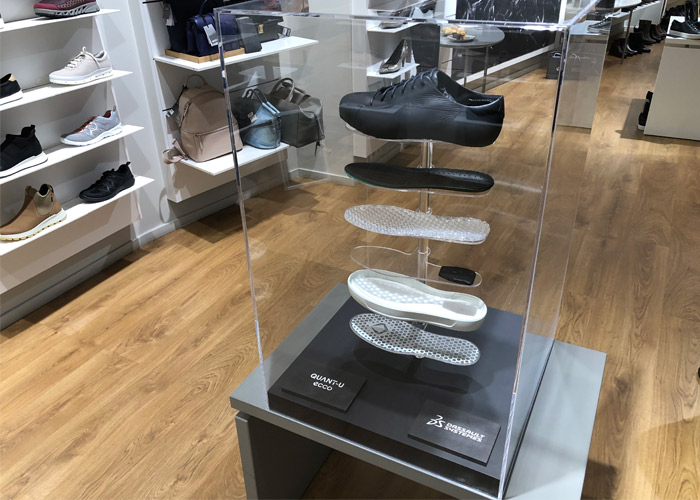
Photo Credits: 3Dnatives
The QUANT-U experience is currently being presented at the Bon Marché Rive Gauche as part of the exhibition “Geek mais Chic: Le shopping du troisième millénaire” until April 22nd. You can find more information on the official website of the ECCO experience HERE.
What do you think of this new shopping experience? Let us know in a comment below or on our Facebook and Twitter pages! Don’t forget to sign up for our free weekly Newsletter, with all the latest news in 3D printing!