EBM vs L-PBF: Which Metal Powder Fusion Process to Choose?
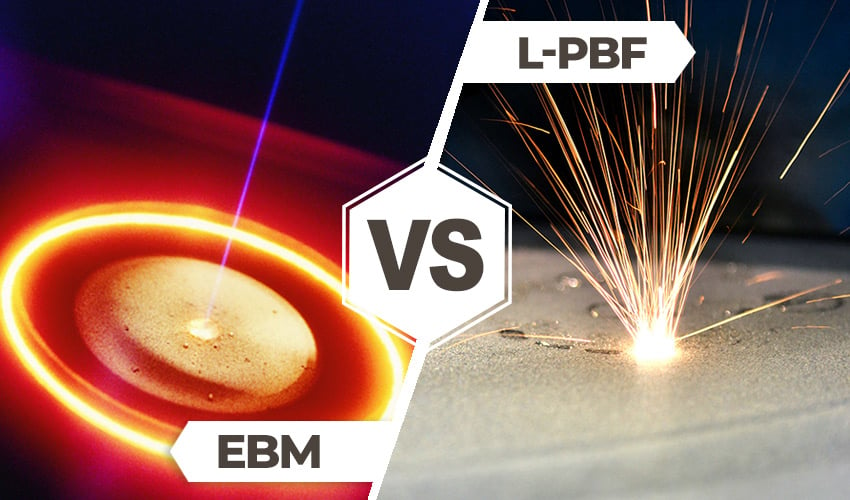
Metal additive manufacturing has grown by leaps and bounds in recent years, making it possible to create complex shapes with enhanced performance and quality. The processes that offer these possibilities are numerous: powder bed fusion, directed energy deposition, binder jetting, and so on. And powder bed fusion is one of the most widely used.
Two separate techniques fall under this umbrella, which differ mainly in the heat source used: laser powder bed fusion (L-PBF) and electron beam melting (EBM). The principle between the two remains the same: fusing metal particles spread out on a printing plate, layer by layer, to create the desired 3D model. But using a laser to perform this operation or an electron beam is obviously different.
So which process should you adopt? What are the characteristics of these two techniques? What do they have in common? We took a closer look.
L-PBF and EBM Technologies
As the name suggests, both technologies involve the fusion of metal powders via a heat source. This process takes place in a closed machine and produces solid, dense parts. It is the heat source employed that differs.
In the case of the laser powder bed fusion, it is important to clarify the names given to this process and the various acronyms. We often hear SLM or DMLS, or even L-PBF. The principle behind them remains the same: the term SLM (Selective Laser Melting) comes from the Fraunhofer Institute, while DMLS (Direct Metal Laser Sintering) comes from the manufacturer EOS. Here, we use the more generic term L-PBF.
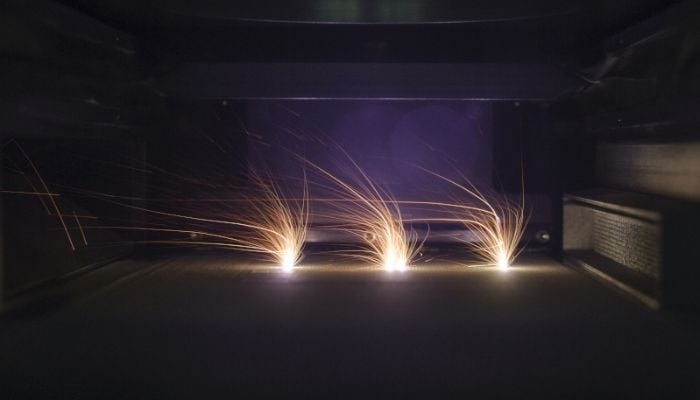
The L-PBF process (photo credits: Schmitz Metallographie GmbH)
An L-PBF 3D printer uses one or more lasers – nowadays, machines with 12 lasers can be found. In terms of process, it begins by creating an inert atmosphere in the closed chamber and heating it to the desired optimum temperature. A first layer of metal powder is then deposited on the plate. The laser then fuses the powder particles into the desired shape.
The intensity of the laser is determined according to the metal used: the aim here is to reach the material’s melting point, so that it melts completely as the laser passes over it, and solidifies as soon as it cools. The process is repeated layer by layer.
Turning now to electron beam melting, it is essential here to employ a vacuum chamber to prevent oxidation of the metal powder.Once this environment has been created, the material – which must be conductive – is placed on the plate, and an electron gun emits a beam. Guided by a magnetic field, the electrons produced fuse the powder particles together, layer by layer, to create the desired part.These electrons can reach temperatures of up to 2,000°C and ultra-high speeds.
Technical Specifications
The choice between laser or electron beam fusion will depend on the user’s needs: is high part quality required? What volume is required? Is the project urgent? As you can see, many criteria influence the final decision, so we decided to take a look at the main differences in terms of technical characteristics, to help you make the right choice.
Printing Quality
Printing quality is a decisive factor, especially when it comes to finished parts. Whether in L-PBF or EBM, the result is generally precise, dense and solid parts. However, the finish is not the most polished and the parts are rough. Metal additive manufacturing often requires post-processing steps to achieve a smoother, more finished surface.
That being said, it is worth noting that the use of a laser enables greater precision to be achieved. This is because the powder particles are fused more finely, enabling us to design parts with a less coarse surface finish than with the EBM process. What’s more, the powder particles used in L-PBF are finer, as are the layer thicknesses. This contributes to better print quality than with EBM.
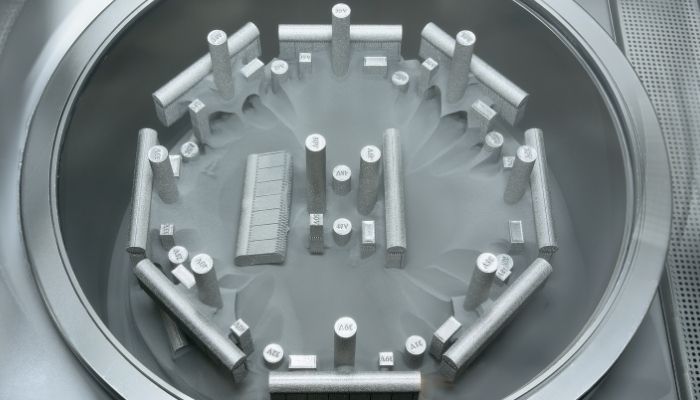
3D printed parts made using EBM (photo credits: Colibrium Additive)
Printing Speed
In general, electron beam fusion is faster than laser fusion. Numerous electrons are emitted at once and these are capable of fusing particles simultaneously, as the beam emits energy over the entire printing plate. A laser, on the other hand, has to fuse particles point by point, which takes much longer. L-PBF solutions use a galvanometer, i.e. an assembly of movable mirrors to direct the laser along the printing plate.
Of course, printing speed will depend on the number of lasers the L-PBF machine has, and their power – as you’d expect, a single-laser 3D printer will be less efficient than one with 12. The 3D printer’s preheating and cooling must also be taken into account when estimating manufacturing times.
Printing Volume
Metal powder bed fusion is not particularly well known for high-volume production – for this, users tend to turn to directed energy deposition (DED). Indeed, the larger the machine, the longer the material preheating time and the greater the energy required, which is not necessarily an advantage. However, generally, L-PBF offers more generous volumes.
Why? Well, first of all, there are more laser powder bed fusion machines on the market, which means a wider choice in terms of print bed sizes. For example, one of the largest solutions offers a volume of 9 tons, while the most common are more around 250 x 250 x 300 mm.
On the EBM side, the choice is much more limited, as there are very few 3D printers on the market. The volume on offer doesn’t match that of the L-PBF – we’re talking more about 200x200x200 mm, with the option of going up to 300 x 300 x 450mm.
Materials
It is very important to note that electron beam melting is only compatible with conductive metals. The very principle of the process relies on an electrical charge, and must work with a material that lets it through. This means that parts can be printed in chrome cobalt, copper, titanium, stainless steel or even nickel alloys. Note that the powder not fused by the beam can be reused, which can represent considerable savings in terms of resources.
For L-PBF, the range of compatible materials is much wider. The most commonly used metals are aluminum, titanium, steel and various alloys, as well as cobalt-chromium and copper. In both cases, powder handling must be carried out with the utmost care, using the necessary protective measures (masks, gloves, goggles). The finer the powder particles, the greater the precautions to be taken. The risk is therefore greater with L-PBF.
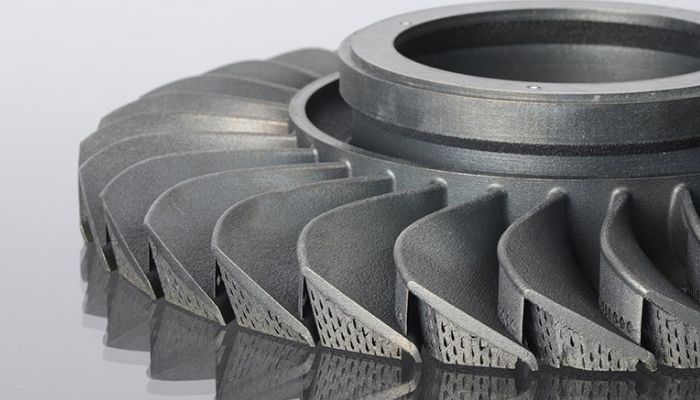
Blades made using laser powder bed fusion (photo credits: Fraunhofer IPT)
Post-Processing
Once printing is complete, both processes require the part to be cleaned. Excess powder that has not been fused must be removed. Depending on the shape of the part, the depowdering process may take more or less time. Specific equipment, such as sandblasting stations, is often used.
Then comes the step of removing support structures. Electron beam melting generally requires fewer of these. The use of a vacuum chamber and controlled pre-heating of each layer limit distortion and reinforce the parts, thus limiting the need for reinforcements during printing.
With L-PBF, supports are necessary not only to avoid warping due to high temperatures, but also to promote heat dissipation and reduce stresses as the material cools. Depending on the geometry of the part, the number of supports will vary. They can be removed by machining, cutting or wire EDM.
As explained above, the two metal additive manufacturing processes are not particularly renowned for their aesthetic quality. If you want a smooth surface, a user will need to go through a number of post-processing steps, including polishing. This is particularly true of the EBM process, where the surface finish is particularly poor.
Finally, heat treatment, i.e. the various methods used to improve the mechanical properties of parts, is rarely necessary for EBM. If you opt for L-PBF, it may be worth using techniques such as hot isostatic pressing to eliminate all internal voids and remove residual porosity.
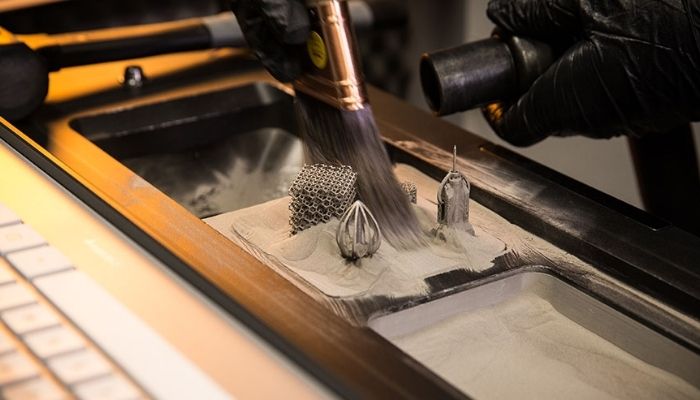
L-PBF parts cleaning (photo credits: Protolabs)
Main Applications of EBM and L-PBF Processes
Both technologies are used in high-performance industries, but their applications differ according to their unique processing characteristics. Electron-beam melting stands out for its ability to process difficult-to-machine materials and manufacture high-strength parts. Historically, electron-beam melting has appealed to two sectors: aerospace and medicine.
In aerospace, it is most often used to produce turbine blades. Colibrium Additive, for example, vacuum prints thousands of titanium turbine blades for GE Aerospace’s GE9X engine. In medicine, EBM 3D printing has been widely used in the production of orthopedic implants, such as acetabular cups for hip prostheses. The porous design offered by this process facilitates bone growth in the cup, which in turn facilitates implant fixation.
L-PBF technology, meanwhile, is widely used in aerospace, automotive, medical and dental applications, as well as in turbomachinery. In the automotive sector, this process is used in a variety of car parts, from engine and transmission components to interior fittings. In turbomachinery, this technology is essential for the production of blades, impellers and fuel injectors, where its ability to create internal channels and cooling structures improves component efficiency and service life. In the medical and dental sectors, L-PBF is mainly used for the manufacture of surgical tools and dental implants.
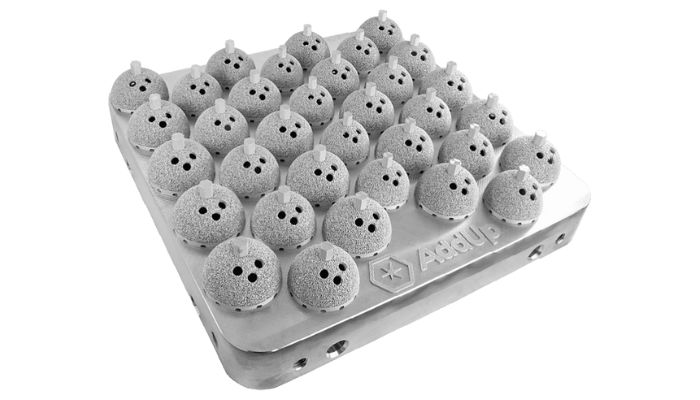
Acetabular cups for hip prostheses (photo credits: AddUp)
Finally, it is worth mentioning that the use of these two technologies in the medical sector is strongly influenced by the possibility of using materials such as titanium and stainless steel. Titanium is a biocompatible material with good mechanical properties, making it suitable for implants, for example. As for stainless steel, its characteristics make it perfect for the production of tools and medical equipment. Both metals benefit from the processes and their sealed chambers to produce parts without the risk of contamination.
Main Manufacturers of EBM and L-PBF 3D Printers
For many years, the electron beam melting (EBM) market was dominated by Arcam, the Swedish company that first developed and commercialized this technology. In recent years, this branch of the industry has expanded, with new companies entering the market.
Today, Colibrium Additive, a GE Aerospace company, is the most influential player following the acquisition of Arcam in 2016. The company led the mass production of aerospace and medical components within General Electric. Since acquiring Arcam and other companies specializing in metal additive manufacturing, such as Concept Laser, Colibrium Additive has optimized the technology with innovations such as automatic beam calibration and more precise thermal control.
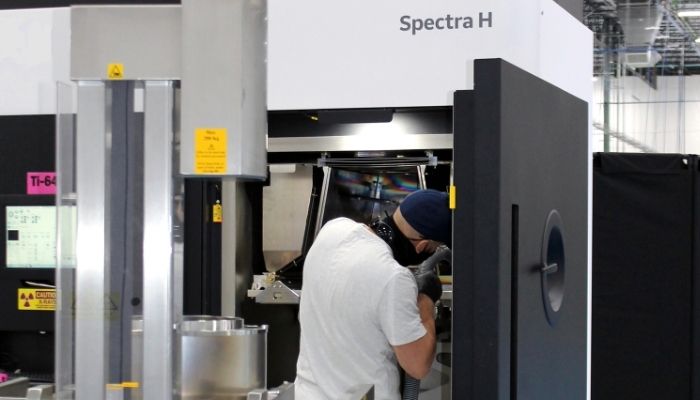
An EBM 3D printer (photo credits: Colibrium Additive)
Furthermore, since this evolution of the EBM technology market, new manufacturers have appeared, including Wayland Additive, which, with its NeuBeam process, seeks to improve the stability and flexibility of electron-beam fusion. Founded in 2017 by former Arcam engineers, Freemelt also offers electron-beam printers, and some are even open source.
Other new entrants to this market include Asian manufacturers QBeam, Xi’an Sailong Metal and JEOL. They stand out for their experience in other electron-beam technologies, which they have adapted to additive manufacturing. That being said, sales of these printers remain concentrated in their home countries.
In the field of L-PBF technology, the German company EOS is the leading player, with over three decades of experience in the production of metal printers based on L-PBF technology and its materials. Additionally, there are a large number of other companies using the L-PBF process: Nikon SLM Solutions, Renishaw, Farsoon Technologies, Additive Industries, 3D Systems and AddUp are just a few examples.
Over the years, these companies have fine-tuned their offerings by proposing printers that meet the needs of particular sectors. Printers from Farsoon and Additive Industries, for example, stand out for their multi-laser and large-format capabilities. Renishaw and 3D Systems printers are often used in research. Finally, manufacturers Nikon and AddUpp offer solutions for general industry and mass production. It should be noted that the offerings of the above-mentioned manufacturers are not limited to these applications, but are some of the most important.
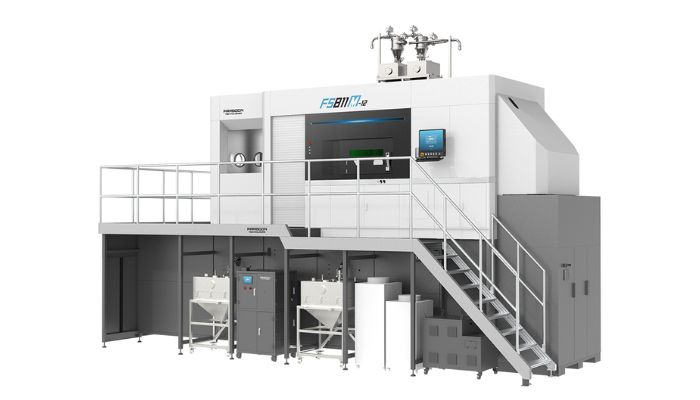
FS811M large-format 3D printer (photo credits: Farsoon Technologies)
Price
3D printers using the EBM and L-PBF processes represent a significant investment, with prices varying according to model, print volume, inert media required and the specific features of each device. However, the price of EBM printers is much higher than that of L-PBF printers. This is due to the limited supply of EBM machines compared with L-PBF solutions.
In the case of electron beam melting, costs are estimated at between $500,000 and $1,000,000. This high cost encompasses not only the printer itself, but also the infrastructure required to operate the machine, including post-processing equipment and specialized materials. In addition, the EBM process requires highly skilled professionals to operate it, which has a significant impact on costs and the availability of talent.
By contrast, L-PBF offer a wider price range, depending on their print volume. Models such as 3D Systems’ ProX 100, with a print volume of 100 x 100 x 180 mm, are estimated at $250,000. More advanced options, such as the EOS M400, with a print volume of 400 x 400 x 400 mm, reach $750,000. In addition to the cost of the machine, investment in post-processing equipment and the purchase of metal powders must also be taken into account. In short, to find out the precise cost of printers, it’s best to contact manufacturers or distributors for a quote.
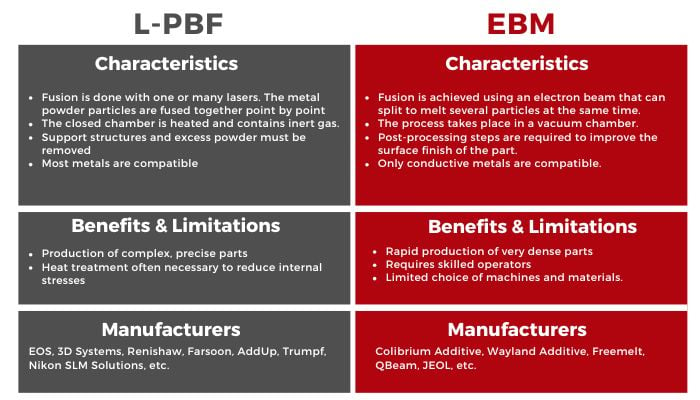
Image Credits: 3Dnatives
Which process do you use EBM or L-PBF? Let us know in a comment below or on our LinkedIn, Facebook, and Twitter pages! Don’t forget to sign up for our free weekly Newsletter here, the latest 3D printing news straight to your inbox! You can also find all our videos on our YouTube channel.