#3Dstartup: dp polar develops AM system with continuously rotating platform
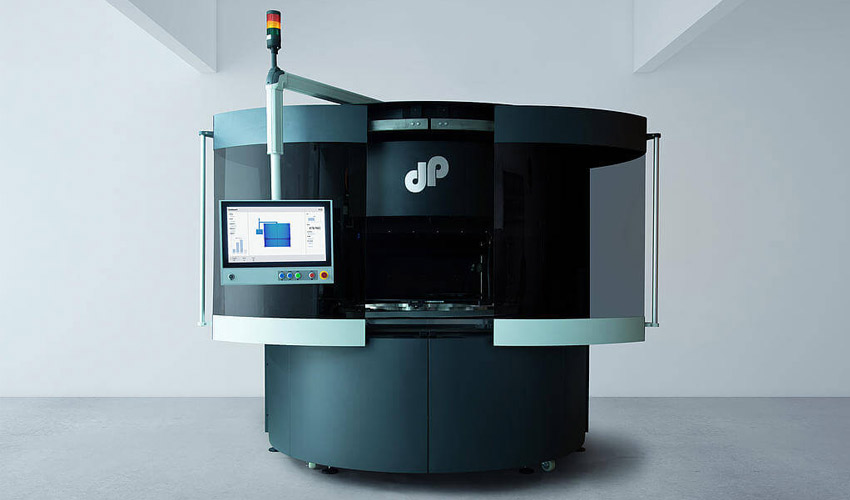
Based in Germany, our startup for June is dp polar! The company has developed the first industrial 3D printer with a rotating printing build plate. Instead of having a print head that moves to deposit the material layer by layer, the build plate rotates around it, offering greater productivity and above all, high repeatability. Called AMpolar® i2, the machine is also capable of combining several materials at the same time, thus multiplying the possibilities and final properties of the end part. We met with Florian Löbermann, Managing Director of dp polar, to learn more about this automated industrial production system and the future developments of the start-up.
3DN: Can you introduce dp polar and its link with 3D printing?
At dp polar, we have developed the world’s first AM system with a continuously rotating print platform – Made in Germany. Our patented system combines unparalleled productivity with high precision and thus paves the way from rapid prototyping to industrial series production. We are convinced that just having a productive printing system is not enough. The current lack of material properties is definitely hampering the adoption of 3D printing for industrial applications. Therefore, we are partnering with leading chemicals companies to develop materials for our AM system that can deliver large quantities of high-performance parts.
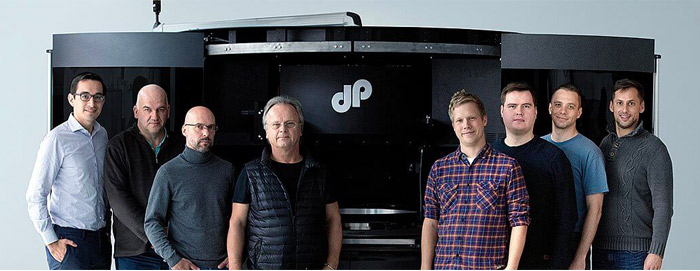
The dp polar team
3DN: How and when was the company launched?
dp polar was founded in 2014 by a successful serial entrepreneur with over 20 years of experience in digital printing for the pharmaceutical packaging industry. While digital printing is now mainstream for industrial production in the graphical industry, 3D printing is still mainly used for rapid prototyping applications or small production batches, because existing technologies lack productivity, cannot be easily automated, are not scalable and ultimately do not deliver the cost-per part required for large scale industrial production. This motivated us to develop a technology platform addressing all these issues and thus paving the way from rapid prototyping to automated industrial series production.
3DN: What are the benefits of such a 3D printing process and how does it differ from other technologies?
To make 3D printing really a useful production technology, we need to produce several ten thousand parts per week with one machine. Scaling production by putting more machines is not really an option for widespread adoption, since costs and complexity scale with productivity. Additionally, the production process needs to be extremely reliable, automated and most importantly deliver a homogenous and repeatable part quality. Due to the narrow process window of a complex process such as 3D printing, there are currently serious limitations to the materials that can be processed in AM.
Advances in material development will be able to narrow the gap between AM materials and traditional materials, but it will be extremely challenging to make a high-performance end-use part with just one material. We strongly believe that the combination of multi materials in one part will be necessary to get a part quality acceptable for demanding industrial customers. Not only can more complex parts be realized, but also the material properties can be put into the exact location within the part, where they are needed. For example a high-temperature material, which is typically more brittle, can be deposited at the temperature hot-spot, whereas a more mechanically strong material can be used for the area, where the part is joined by a clip or screw.
Ultimately, adoption of AM by the manufacturing industry will be driven by favorable economics. By increasing productivity of the system and the complexity of the printed parts, we can push the economics in favor of AM. Thus, it is important to integrate hybrid workflows that can manipulate the part during the printing process, as this enables the series production of functional, integrated parts. An example of this multi-process ability could be the integration of electronics or sensors in a printed part by integrating a pick-and-place process into the AM process.
With all these requirements and challenges in mind, we have designed our break-through High-Speed Rotative AM (HSR AM) process, which addresses these issues critical for industrial series production. Our printing process combines high productivity with multi-material and multi-process ability.
AMpolar® i2 is the world’s first 3D printing system with a continuously rotating print platform. In contrast to previous processes, it is not the print head that moves, but the area on which printing takes place. This produces high-precision components up to 20 times faster in larger quantities and with a build volume of approximately 700 liters. In addition, a wide variety of customer-specific materials can be processed in a single pass using the Multi Material Jetting process. The technology also makes it possible to equip parts produced in this way with electronic components without interruption if required (pick and place process). This combination of properties is unmatched in 3D printing. The AMpolar® i2 thus points the way from prototyping to industrial series production.
3DN: Which sector or applications do you target?
We design, develop, and deliver 3D printing systems for industrial series production to the automotive, life sciences, aerospace, mechanical engineering, and consumer industries. Our cutting-edge additive manufacturing solutions address the requirements for series production of components and systems, improving supply chain efficiency and reducing total cost of ownership. We strive to succeed in the value chain as a reliable partner in the AM ecosystem.
3DN : What are the future developments of dp polar?
We are continuously innovating around our patented High-Speed Rotative (HSR) AM process. We are not only looking to bring new materials on our platform, but also develop automation solutions to embed 3D printing in an industrial environment.
3DN: Any last words for our readers?
If you have great ideas what you can achieve with our product or just want to learn more, please do not hesitate contacting us any time.
What do you think of our startup of the month? Let us know in a comment below or on our Facebook and Twitter pages! Sign up for our free weekly Newsletter, all the latest news in 3D printing straight to your inbox!