Diebold Nixdorf Adopts FFF 3D Printing for Cutting-Edge Banking Solutions
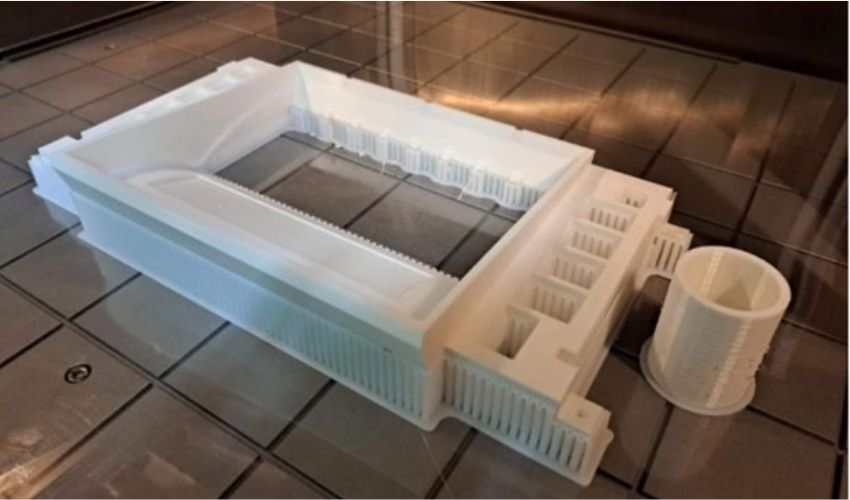
When thinking of banking equipment, most people conjure an image of old-fashioned money-counting machines or tools used by tellers sitting behind their counters. But as one of the oldest professions, dating back to records from around 2000 BCE in ancient Mesopotamia, it stands to reason that banking and its institutions are constantly looking to innovate. As banking industry evolves from its ancient roots, institutions like Diebold Nixdorf are at the forefront of innovation, leveraging cutting-edge technologies to revolutionize their operations. A notable leap in this journey is the integration of 3D printing into their manufacturing processes, and more specifically of INTAMSYS 3D printing solutions.
Diebold Nixdorf is an American multinational company, leader in the production of innovative banking solutions and retail technology. In particular, the company specializes in banking automation, producing ATMs, smart safes, and inquiry terminals. Since October 2020, Diebold Nixdorf has partnered with FPFTech (Fundação Amazônica for Support to Research and Technological Development Judge Paulo dos Anjos), a non-profit Research and Development institution, to adopt additive manufacturing in its production processes, with the support of INTAMSYS.
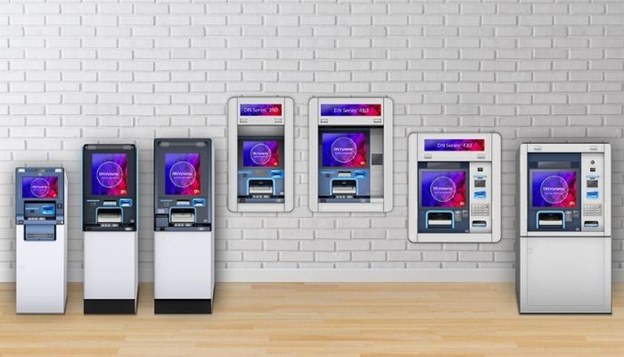
Diebold Nixdorf is known for its automated banking solutions (photo credits: Diebold Nixdorf)
Why Did Diebold Nixdorf Turn to 3D Printing?
Though banking solutions may not be what we most hear about when it comes to applications where 3D printing is useful, in the case of Diebold Nixdorf, it seems to have become an integral part of production. Diebold Nixdorf chose two 3D printers to meet their production needs. This includes one from INTAMSYS, the large build volume FFF 3D printer FUNMAT PRO 610HT for large parts and more material choice (notably with high-performance filaments).
But why exactly did Diebold Nixdorf turn to 3D printing? Well, it is a story we have heard time and again, the adoption of additive manufacturing, notably through INTAMSYS has enabled the production of conceptual and functional prototypes with unprecedented precision and quality. All while also offering significant cost and time savings.
Julio Pinheiro, project supervisor at Diebold Nixdorf further explains, “The decision to use 3D printing came from the need to bring more agility and flexibility to the development of our products. It allows rapid prototyping of complex components that previously required much more time and resources. Previously, we relied heavily on machining and building physical models, which honestly slowed down the development cycle. With 3D printing, not only have we accelerated this process, but we have also significantly reduced the associated costs.”
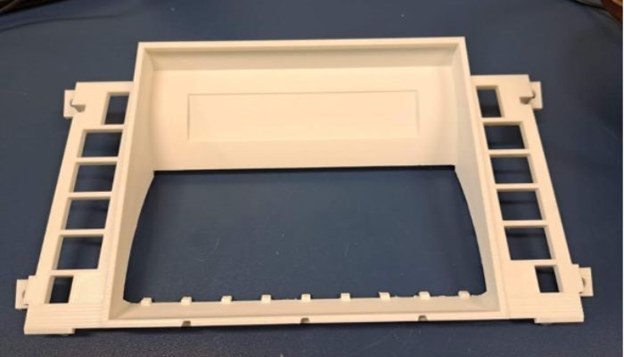
A front panel made using the INTAMSYS FUNMAT PRO 610HT with support material removed (photo credits: INTAMSYS)
The Choice of Printer
It was no accident either that the company turned specifically to the INTAMSYS FUNMAT PRO 610HT, which has become the true workhorse of Diebold Nixdord. As demand for 3D printing has proven high at the company, the machines are running 24/7 all while ensuring precision, something for which the FUNMAT PRO 610HT large-format 3D printer is well-known.
Furthermore, with the FUNMAT PRO 610HT it was possible to ensure a superior surface finish for complex geometries. Thus helping Diebold to achieve more refined finishes that resemble injected parts to meet project specifications. High fidelity was also key with tolerance down to tenths of a millimeter, ensuring that parts not only fit perfectly, but also functioned as expected.
For this reason, materials were also crucial. FUNMAT PRO 610HT stood out for its ability to work with a wide range of materials, for the printing volume that fits perfectly into their projects and for not working with closed material cartridges, as it works with any brand of filament.
Pinheiro expands, “ABS is our material of choice most of the time for its strength and ease of use. However, we are always evaluating other materials that can meet the needs of each project. This is the advantage of the FUNMAT PRO 610HT, it is a machine that accepts a wide range of materials.”
Last but not least, with the FUNMAT PRO 610HT, Diebold was able to work with a wide range of sizes. For example, some projects required small parts, but there was also demand for large components. One such example is the front panel part of an ATM that was able to take advantage of almost all of the available printing volume of the FUNMAT PRO 610HT (610 x 508 x 508mm).
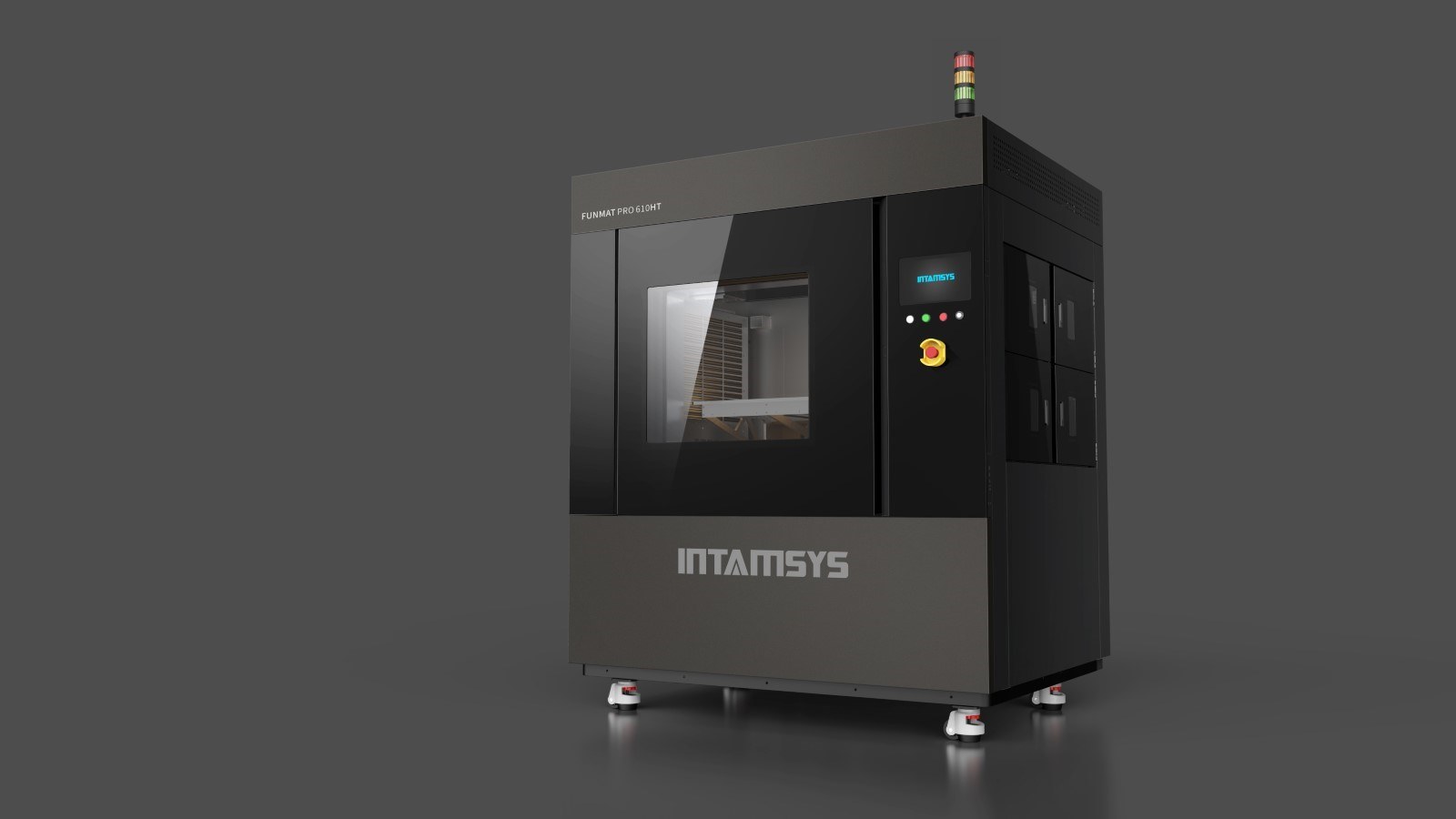
The FUNMAT PRO 610HT (photo credits: INTAMSYS)
In any case, the use of FFF 3D printing has been a huge success at Diebold Nixdorf. The company further notes that the production capability they have achieved with AM adoption has allowed them to stay competitive while meeting tight deadlines. Especially considering the reliability of continuous printing with the FUNMAT PRO 610HT. You can learn more about INTAMSYS 3D printing solutions HERE.
What do you think of Diebold Nixdorf’s decision to turn to 3D printing for their automated banking solutions? Let us know in a comment below or on our LinkedIn, Facebook, and Twitter pages! Don’t forget to sign up for our free weekly newsletter here for the latest 3D printing news straight to your inbox! You can also find all our videos on our YouTube channel.
*Cover Photo Credits: INTAMSYS