Researchers develop defect-resistant Nickel-based superalloys for 3D printing
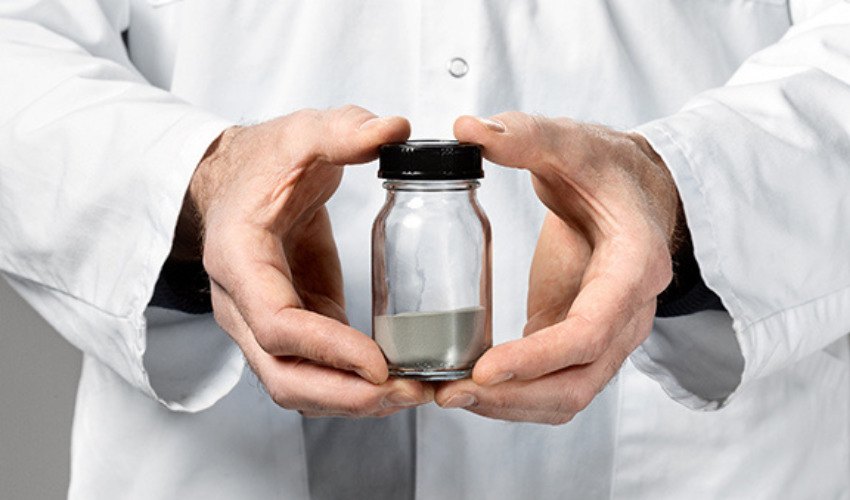
At UC Santa Barbara and Oak Ridge National Laboratory, a team of researchers have developed new defect-resistant high-performance alloys for metal 3D printing. The researchers explain that designing alloys that are compatible with the unique additive processing conditions while offering high-performance properties for applications in energy, space and nuclear, remains a challenge. Nevertheless, the team developed a class of high strength, defect-resistant 3D printable nickel-based superalloys containing approximately equal parts of Co (Cobalt) and Ni (Nickel) along with Al, Cr, Ta and W. Their aim is to support the production of high economic value metal materials for the additive manufacturing process, enabling innovative, geometrically complex designs with minimal material waste.
The Nickel-based superalloys reportedly overcome the issue of cracking, which usually affects parts fabricated with high-temperature Powder Bed Fusion technologies like LPBF and EBM. During these processes, metal powder is melted layer after layer using a source of energy such as a laser or beam of electrons, to form the part. Therefore, this class of superalloys possess strengths in excess of 1.1 GPa in printed and post-processed forms, and tensile ductility of > 13% at room temperature. The scientists believe that their material holds a lot of promise for high-stress applications, including critical aerospace engine components and chemical-containing nuclear components.
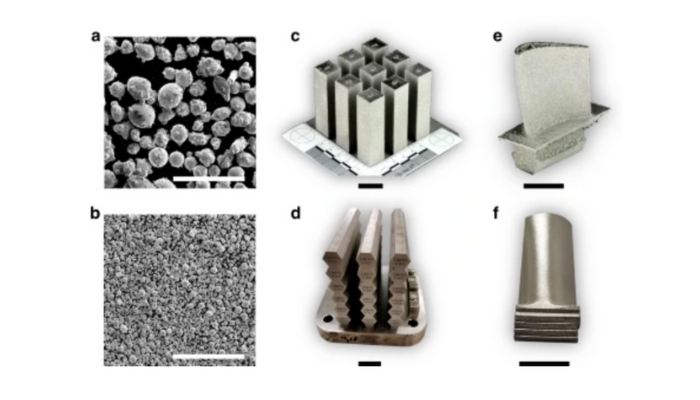
a. EBM and b. SLM printing trials c. and d. Simple bar geometries have been printed for uniaxial tensile testing e. Internal cooling channels f. thin, over-hanging platforms | Figure taken from research paper.
Currently, many advanced metallic alloys used in extreme heat-intensive and chemically corrosive environments are not compatible with additive manufacturing. “Most very high-strength alloys that function in extreme environments cannot be printed, because they crack,” explains Tresa Pollock, Professor of Materials at the College of Engineering at UC Santa Barbara, and part of the research project. However, new designs using additive manufacturing could increase performance and energy efficiency tremendously in a multitude of sectors. Pollock adds: “Alloys can crack in their liquid state, when an object is still being printed, or in the solid state, after the material is taken out and given some thermal treatments. This has prevented people from employing alloys that we use currently in applications such as aircraft engines to print new designs that could, for example, drastically increase performance or energy efficiency.”
Advances in materials certainly play a role in the potential of 3D printing. For example, we introduced the startup 6K on 3Dnatives last year, which has been working on exactly this. The company identified the growing demand for metal powders for sectors like aerospace, medical, or automotive. Therefore, it developed a technology called UniMelt to enable the creation of alloys that are compatible with the AM process: truly spherical, void of porosity and satellites, offering better flowability and overall performance. While material development in additive manufacturing is key, there are other methods to produce defect-free parts, including monitoring printing speed and using machine learning and artificial intelligence to detect and correct defects in real time.
You can learn more about UC Santa Barbara and Oak Ridge National Laboratory research project and results HERE. What do you think of material developments in the metal AM market? Let us know in a comment below or on our Facebook and Twitter pages! Sign up for our free weekly Newsletter, the latest 3D printing news straight to your inbox!
*Thumbnail Photo: Osprey® metal powder produced at Sandvik’s powder plant for titanium and nickel-based superalloys (Courtesy Sandvik Additive Manufacturing)