Daimler Truck & Buses: Making Additive Manufacturing a Strategy for the Future
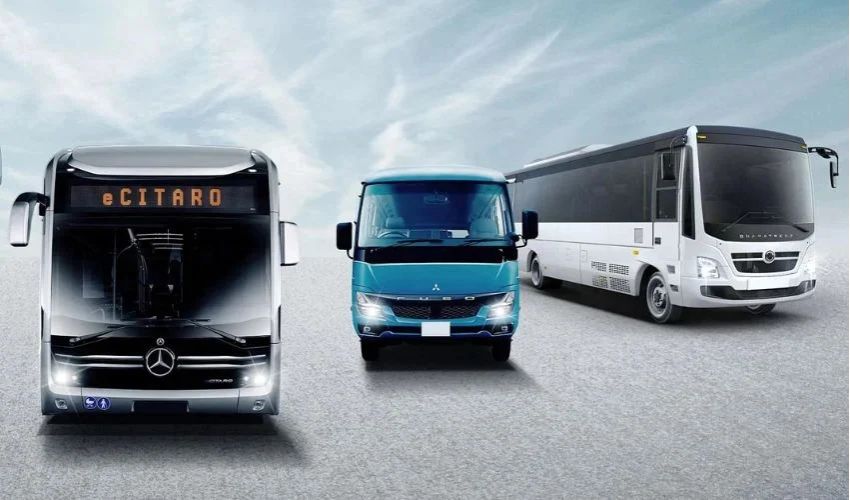
Additive manufacturing is becoming an increasingly popular production method in the automotive and transportation sectors. Many automotive manufacturers have already firmly anchored 3D technologies in their corporate structure, and the railway industry is also increasingly relying on parts created using a 3D printer. And it is not just used for prototyping, either. Companies are using AM to manufacture individual parts, tools and systems, as well as mass production of specific components. For some companies, additive manufacturing has been a game-changer, enabling flexible, demand-driven production and bold innovation. Other companies have reservations about 3D printing and have not yet leveraged its potential.
Daimler Truck & Buses is one of the companies that has recognized the benefits of additive manufacturing, actively employing it for its own needs. It is now an integral part of the company’s strategy and a cornerstone of implementing a digital business model. In this interview, Daniela Rehm and Ralf Anderhofstadt from Daimler Truck & Buses tell us about their journey to implement 3D printing within the company, the milestones they have achieved and their next big goals.
3DN: Can you introduce yourselves and explain your work at Daimler Truck & Buses?
Daniela: My name is Daniela Rehm. In our 3D printing technology center, I head up product management and marketing activities for additive manufacturing within Daimler Buses. In our consulting unit, I coordinate key account management for central sales activities.
Ralf: My name is Ralf Anderhofstadt. I manage our 3D printing technology center and our external consulting unit AMS – Additive Manufacturing Solutions Daimler Truck. In this role, my team and I guide all topics related to additive manufacturing, both inside and outside Daimler Truck & Buses, to develop this exciting technology into a new, digital, future-oriented business model. At the same time, I have written two editions of the book “Disruptive 3D Printing,” and actively participate in numerous expert committees and on the advisory board of the 3D Printing Association.
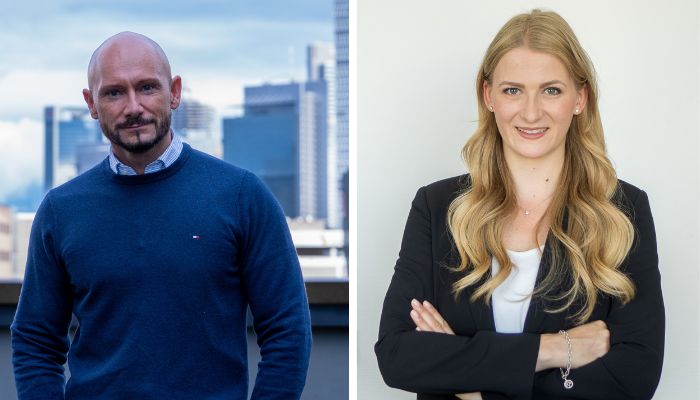
Ralf Anderhofstadt, Head of the AMS 3D Printing Technology Center and Consulting Unit (left) and Daniela Rehm, Head of Product Management and Marketing for 3D Printing (right).
3DN: How and why is Daimler Truck & Buses using 3D printing?
Ralf: We’ve been successfully using 3D printing in our company for many years, if not decades. Initially, the focus was on prototyping and design. It wasn’t until 2015, during the cross-functional “CSP 3D Printing” project, that the transition to series production was considered. This was the starting signal for the first 3D-printed parts in the spare parts and series sectors. This opened up new potential for our company. Today, after many necessary adaptations, the development of technical and quality approval processes, and countless product tests and inspections over the last few years, we are involved in 3D digital printing, among other things.
Daniela: As a large company, Daimler Truck & Buses is always on the lookout for market events and developments. For example, as Ralf mentioned, additive manufacturing emerged in 2015 as a key aspect of our company’s future competitiveness. In 2016, the topic of 3D printing was established as a project to fundamentally examine the technology’s potential and added value for our company as a first step. The first positive effects in terms of monetary and process efficiency were quickly realized, meaning that additive manufacturing has become a pillar of our future strategy.
In terms of technologies, in addition to powder-bed processes, we now use all the printing technologies that enable us to fully guarantee the quality requirements for mass-produced components. Plastic components are our biggest advantage, but we also do a lot of work in the metal and silicone sectors. In the metal sector, in particular, we foresee great potential in the near future, which can be effectively exploited thanks, among other things, to our in-house developed metal material.
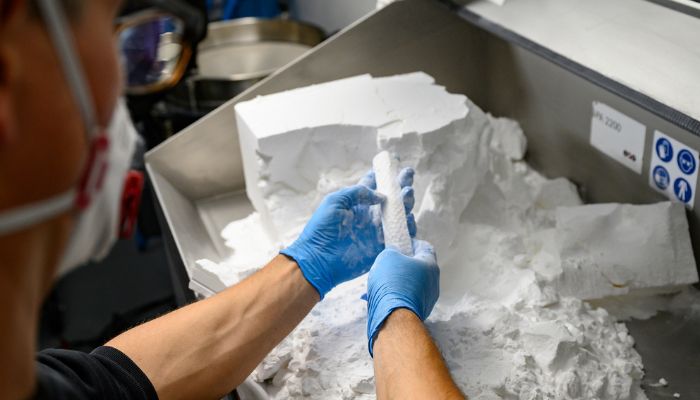
Bei Daimler Truck & Buses uses various 3D printing processes
3DN: How did you integrate 3D printing sustainably, what were the key milestones and what has changed since you started using 3D printing in your business?
Daniela: In general, mental barriers, combined with a lack of knowledge and a fear of new or bad experiences from the past, are the biggest obstacles to implementing additive manufacturing in a company. When integrating industrial additive manufacturing, it was very important for us to take a global view of the technology from day one. All specialist departments were involved in the initial project. This helped to create a long-term global understanding. As the first positive effects of using the technology were realized, not only were the initial foundations laid for confidence in 3D printing, but partnerships were gradually established on this basis too.
Ralf: In fact, we produced the first approved replacement parts in 2017. The basic requirements were and still are reproducibility and high-quality standards. This has remained unchanged to this day in the production of serial parts using 3D printing. We have now approved over 600 different series and individual parts, with a total of over 100,000 already installed in our vehicles. The potential has expanded considerably since 2017. On the one hand thanks to newly developed materials, but also thanks to 3D printing processes approved through our implemented 3D printing license management and our highly successful digital warehouse, in which several thousand digital twins of our products are stored for immediate “on-demand” production.
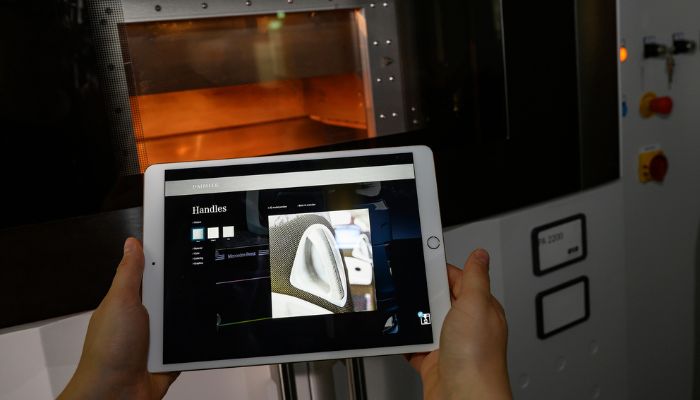
Digital twins enable on-demand production, right where the final part is needed.
3DN: What are the requirements for on-demand production?
Ralf: After deciding to create a 3D printing license management system, it was extremely important, in the context of decentralized production, to implement parts on certified 3D printers, including systems, and with qualified processes. Our mobile 3D printing units are an essential element for printing parts directly at the point of sale or production. In addition to these, we also work closely with our external organization and with logistics and printing service providers to further develop the decentralized 3D printing business with all its economic and ecological benefits.
3DN: What are some of the projects you’ve completed using additive manufacturing?
Daniela: We’ve done some exciting projects in the past. When considering the implementation of components in series production, the additive manufacturing of the cockpit control panel for eight coaches was certainly a milestone. Within a few weeks, the components were manufactured in compliance with all quality requirements and approval processes, and vehicle delivery was guaranteed.
The launch of the 3D printing license stores mentioned by Ralf in June 2022 was also a great success. Since then, our customers have been able not only to purchase physical spare parts but also to obtain 3D print data sets of the components required for production directly at the point of use.
Ralf: Yes, the projects Daniela mentioned are some of the highlights. I could certainly name many more, but if I had to mention just one, it would be the launch of our external consultancy unit AMS – Additive Manufacturing Solutions Daimler Truck. This was a great moment, as we received the first requests directly from external companies to jointly pilot industrial 3D printing. Today, we work with many companies to realize the potential of the industry.
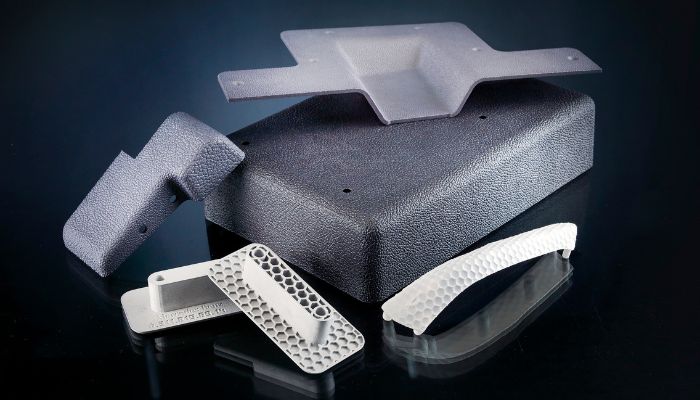
Prototypes, spare parts and production parts are designed using 3D printing at Daimler Truck & Buses.
3DN: Any last words for our readers?
Daniela: The fact that additive manufacturing will not only ensure more efficient developments in product development and prototyping but will also take its place in series production in particular, has already manifested itself in some people’s minds. The digital potential of additive manufacturing will undoubtedly bring exciting changes to the transportation industry. Possibilities such as decentralized production, i.e. manufacturing components directly at the point of sale, have a disruptive effect on existing logistics concepts and component sourcing possibilities. The 3D printing market is constantly on the move, which is why every day in this field is exciting and fun for observing developments or even being part of them.
Ralf: Apart from the fact that there are certain technical challenges, such as achieving the same quality on different 3D printers or various intellectual property issues, the biggest remains the mindset and open-mindedness of the people involved in 3D printing. Unfortunately, there is often an experience or image of 3D printing that doesn’t match reality. As a result, erroneous patterns of reasoning still prevail, and this technology of the future is perceived only from a very narrow angle. Putting an end to this and broadening our perspective is a major challenge that opens up enormous business potential.
I’m very proud to be able to advance the subject of additive manufacturing in our company and in the industry with a great team, and I hope that other companies will also have the courage to adopt a global vision of this technology. Only then will unimaginable potential emerge.
You can find out more about the group HERE. What do you think of Daimler Truck & Buses’ use of 3D printing? Let us know in a comment below or on our LinkedIn, Facebook, and Twitter pages! If you are interested in more automotive 3D printing applications, click here. Don’t forget to sign up for our free weekly Newsletter here, the latest 3D printing news straight to your inbox! You can also find all our videos on our YouTube channel.
*All Photo Credits: Daimler Truck & Buses