Time to think composite: How can you benefit from switching to continuous fiber 3D printing?
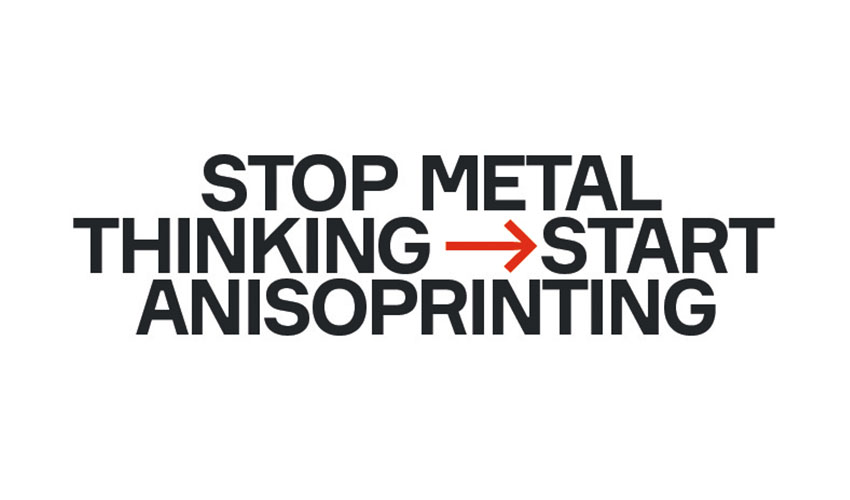
It’s no secret that additive manufacturing has been changing and will continue to change our creation and manufacturing processes. In opposition to subtractive manufacturing, objects are conceptualised, designed and then created layer by layer. Such an approach has meant that objects can be optimized: their weight, lead times and cost is considerably reduced. In terms of design, complex shapes can be created, which not only increases their mechanical properties but also saves material. All in all, 3D printing technologies offer benefits that most industries have understood will change the entire manufacturing supply chain. However, limitations to this process still exist. One of the main limitations relates to the availability of materials. There are plastics, there are metals, but is that it?
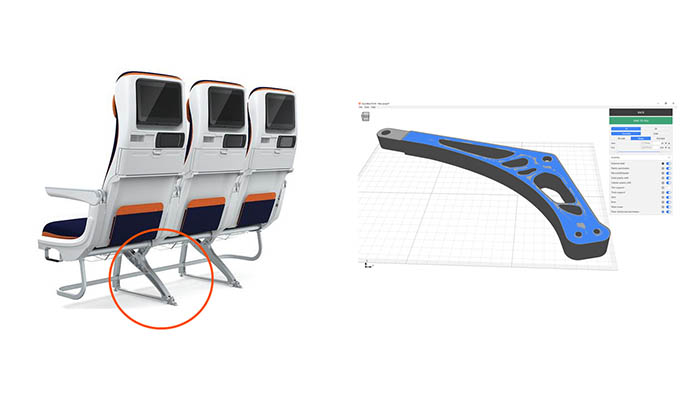
An aircraft seat support piece has been optimized thanks to topology optimization
Plastic or Metal – is there more?
A company that wishes to take on additive manufacturing is faced with two choices: plastic or metal. However, both have their limitations. Plastic 3D printing is typical for prototyping, it’s easy, cheap, and many companies are familiar with the technology. In most cases, end-use parts that require higher mechanical properties are made out of metal. Machines and materials for metal 3D printing are expensive and the process is not so easy itself.
Are composites the solution?
Composite materials can produce functional, load-bearing parts that are easy to produce and affordable at the same time. When people hear about composites, they imagine polymers filled with short/chopped fibers. These are indeed composites too but they will not solve the issues mentioned above. In fact, composites with short fibers are about 2 times stronger than plastic so they shouldn’t be used for end-use parts. However, composites reinforced with continuous fibers are up to 20 times stronger than pure plastic and comparable or even stronger than metals. They are also several times lighter and cheaper than the latter.
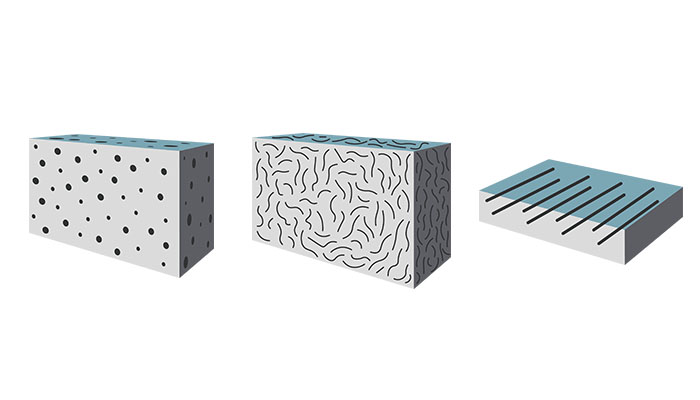
From left to right: composite with particles, composite with short/chopped fibers, composite with continuous fibers
What is Anisoprinting?
Anisoprinting aims to be the solution to achieve both design freedom and material choice to enable part optimization. More precisely, it’s the technology of producing optimal composites through continuous fiber 3d printing from Luxembourgish-Russian technology startup, Anisoprint. Through anisoprinting you can design and produce end-use composite parts that are as strong as their metal counterparts (up to 860MPa) but lighter (up to 7 times lighter than steel), easier to produce and eventually cheaper.
The parts are manufactured through a one-stage fully automated process on Anisoprint’s composite 3D printer, the Anisoprint Composer. Its open material system gives more freedom in terms of parts’ properties. For anisoprinted composites you can use any plastic as a matrix including PLA, PETG, PC, Nylon, TPU, etc. to get parts with your required chemical, weather, impact resistance, heat, etc. properties.
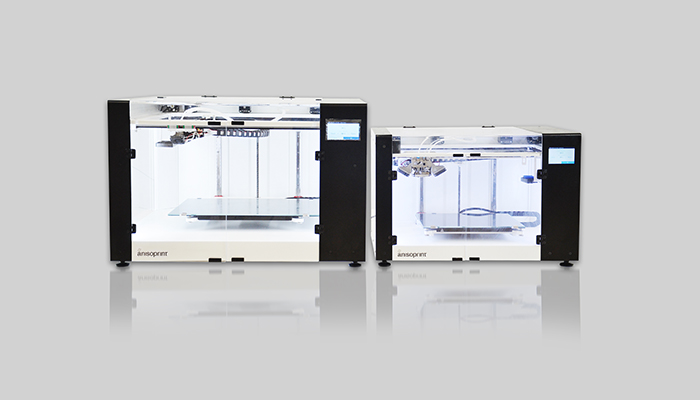
Anisoprint’s composite 3D printers: the Anisoprint Composer A3 (460mm x 297mm x 210mm build plate) and A4 (297mm x 210 mm x 140 mm build plate)
Moreover, Anisoprint’s technology enables to 3D print lattices, which are actually considered to be the optimal structures for composite 3D printing. This is because composites are anisotropic which means that all their strength and stiffness is along the fibers but not across. Therefore, they work best in one-dimensional structures, which is essentially the case of lattices since they consist of a multitude of one-dimensional ribs.
This is not the only benefit of composite lattice structures. Anisoprint explains that parts with such structures can bear the same load as their metal counterparts but are also lighter and cheaper because they use less material. In other words, objects are optimized in terms of shape and material.
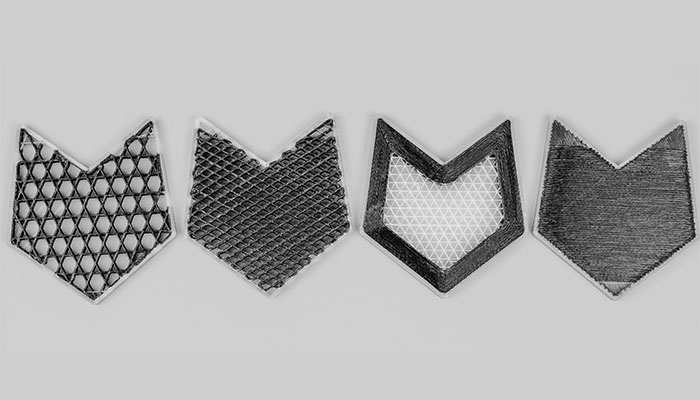
4 types of reinforcement using Anisoprint’s Aura software: anisogrid reinforced infill, rhombic reinforced infill, reinforced perimeters, solid infill
For those who are ready to start thinking composite, Anisoprint will be at Formnext on 19th of November (Booth: G58). According to their website, you can expect the arrival of a solution to take continuous fiber 3D printing to the next level. Find out more information for now HERE.
Are you ready to make the switch to continuous fiber 3D printing? You can leave a comment in the section below or on our Facebook and Twitter pages! Sign up for our free weekly Newsletter, to receive all the latest news in 3D printing straight to your inbox!