A Closer Look at 3D Printing Materials: Composites
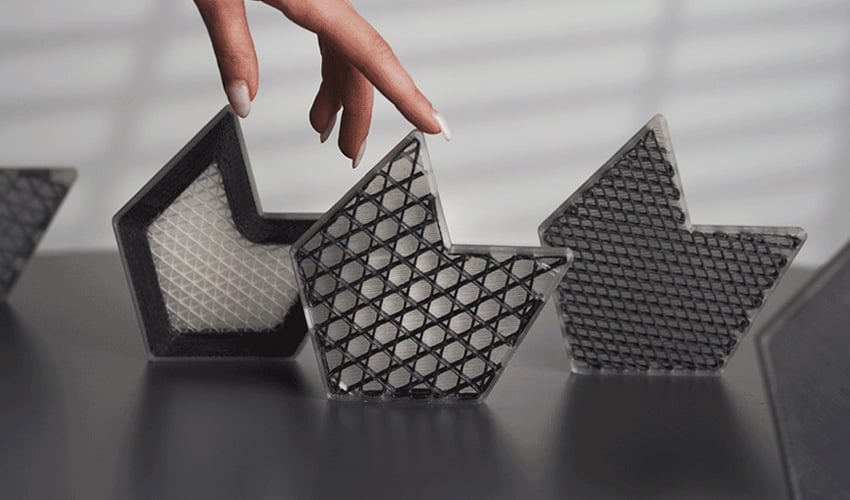
In recent years, composite 3D printing has become increasingly popular. One of the youngest branches of 3D printing, this technology is now used by many players in additive manufacturing, such as Impossible Objects, a company specializing in the field. In fact, it has become so popular that some studies estimate that the composite 3D printing market will reach $1.73 billion by 2030. Logically, when we talk about composite 3D printing, we think of composite printers, but also of composite materials, which are at the heart of this process. Composite materials are made of at least two components and have special properties, making them uniquely suited to various industries that use 3D printing.
Most of the time, in order to manufacture these materials, it is necessary to mix a plastic, which we will call the matrix, with fibers. Today, there are many different kinds of fibers, but three are mainly used for 3D printing: carbon fiber, which is probably the most popular, fiberglass, and PPD-T, also known as Kevlar. Depending on the requirements, either short or long fibers can be used. Short fibers are integrated into the entire matrix and will reinforce the entire part; this type of material is compatible with a wide variety of 3D printers. Long fibers are placed during the printing process itself and are not cut into small pieces, allowing reinforcement only where it is needed. They are only compatible with certain machines at this point in time.
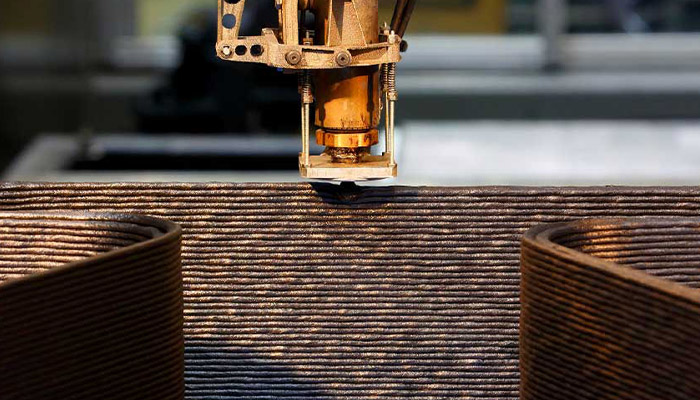
Printing a composite material (photo credits: SABIC)
Carbon Fiber Reinforced Materials
As previously mentioned, carbon fiber reinforcements are commonly used in additive manufacturing of composite materials. Originating in 1860 by chemist Joseph Swan, carbon fiber is composed of interconnected carbon atoms forming a crystalline structure aligned in strands, providing remarkable stability under tension. Recognized for its exceptional strength-to-weight ratio (twice that of aluminum), it holds significant value in crafting lightweight yet sturdy end parts. Moreover, materials infused with carbon fiber exhibit high stiffness, robust tensile strength, and effective chemical resistance.
However, employing carbon fibers in 3D printing demands specific considerations. For instance, using a hardened steel print nozzle is crucial to ensure high-quality part production. Similar guidelines apply to the matrix material integrated with carbon fiber reinforcement. Various matrices like PLA, PETG, nylon, ABS, or polycarbonate can become stronger and lighter with the addition of carbon fibers. These fibers not only harmonize with thermoplastics but can also be blended with ceramics, facilitating the creation of novel applications. Industries ranging from aerospace and automotive to construction benefit from carbon fiber-based composites, harnessing their unique properties.
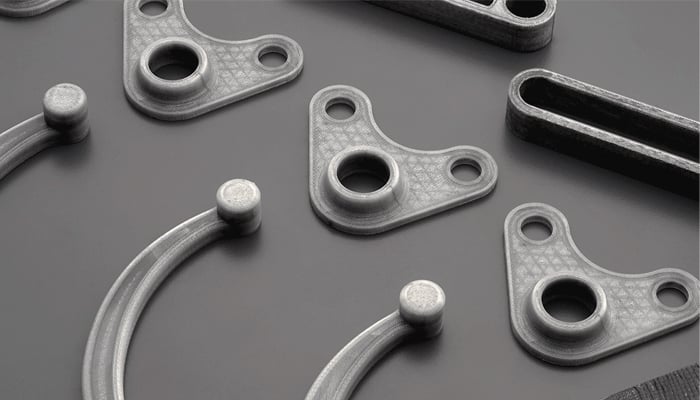
Photo credit: Anisoprint
Fiberglass Reinforced Composite Materials
Introduced in 1930, fiberglass material serves as a reinforcement for numerous thermoplastic polymers. When applied to the appropriate base material, it can yield parts ten times stronger than ABS. In contrast to carbon-integrated materials, fiberglass composites exhibit less rigidity and brittleness. These characteristics, along with cost-effectiveness, distinguish fiberglass composites. Glass fibers boast commendable mechanical properties, act as effective electrical insulators, and feature low thermal conductivity. The material is available in various colors and boasts low shrinkage, minimizing the risk of warping. Similar to carbon fibers, filament reinforced with glass fibers is abrasive, necessitating the use of a nozzle suitable for such materials.
Fiberglass-reinforced 3D printing filaments prove valuable for engineering prototypes and end-use parts demanding robust mechanical and thermal resilience. From construction to marine and sports applications, this composite material has gained widespread acceptance. Noteworthy instances include Moi Composites, in collaboration with Autodesk, Catmarine, Micad, and Owens Corning, creating the MAMBO boat through 3D printing with fiberglass. Additionally, Dutch company MX3D employed this material to 3D print a reinforced bridge.
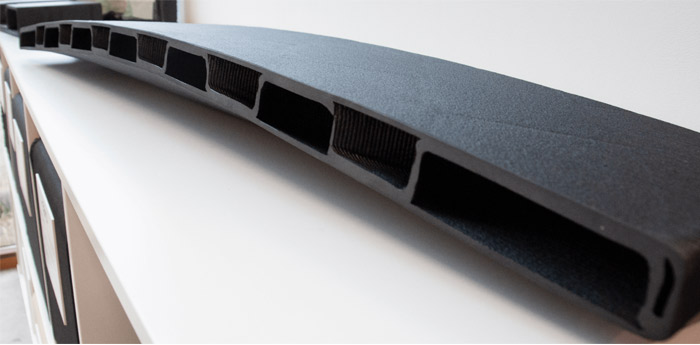
Prototype of a bridge part printed using fiberglass (photo credits: CEAM)
Kevlar Reinforced Materials
Kevlar, a trademark owned by DuPont de Nemours and introduced in 1971, was pioneered by Stephanie Kwolek. Classified within the aramid fibers category, it stands as one of the most durable materials. This material is achieved through polymerization, a process of linking long chains of molecules. Kevlar fibers are meticulously arranged in parallel rows, attributing to their robust properties. Similar to other fibers, Kevlar is frequently combined with diverse plastics for composite creation. Demonstrating commendable mechanical traits in tensile and fatigue strength, Kevlar is primarily employed for crafting components enduring intense vibrations and requiring abrasion resistance. Notably, it surpasses steel with a fivefold strength-to-weight ratio and exceptional heat resistance up to 400°C.
Kevlar also boasts attributes like low density, versatile applications, and a uniform molecular structure that facilitates the 3D printing of exceptionally polished and high-caliber parts. Numerous industries embrace additive manufacturing with Kevlar. Notably, the automotive sector finds value in its application for manufacturing a wide range of components. A compelling instance is US-based Aptera Motors using this composite material to 3D print a car segment, underscoring the potential of reinforced materials in contemporary manufacturing.
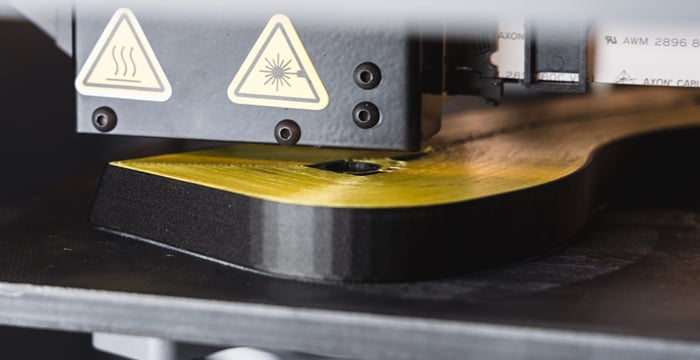
3D printing of a Kevlar composite material (photo credit: Markforged)
What do you think of these composite materials? Let us know in a comment below or on our LinkedIn, Facebook, and Twitter pages! Don’t forget to sign up for our free weekly Newsletter here, the latest 3D printing news straight to your inbox! You can also find all our videos on our YouTube channel.
*Cover photo credits: Anisoprint