The Top Composite 3D Printers on the Market in 2025
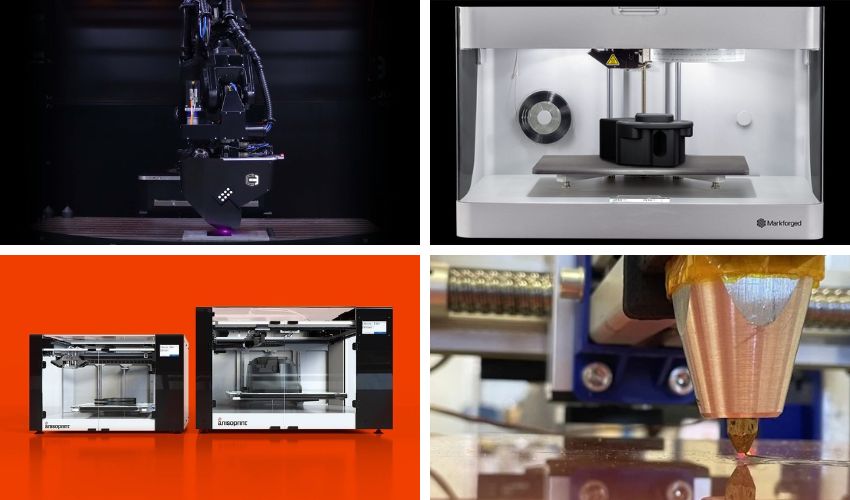
In the 3D printing sector, manufacturers are increasingly looking for composite materials because they offer more interesting mechanical properties, particularly in terms of resistance. Here, the material in question, includes a “matrix” (most often a thermoplastic) that is reinforced with fibers – carbon, aramid, glass – thus increasing the strength of the final part, reducing its total weight and even replacing the use of metal. Today, most desktop FDM 3D printers can print composite filaments as long as they have a hardened steel nozzle. However, these machines do not allow the fibers to be deposited directly into the matrix material during printing. Still, there are a number of manufacturers that have developed solutions capable of extruding both the matrix and the fibers to obtain even stronger parts. We have therefore selected a few composite 3D printers based on different technologies, capable of mixing two materials during printing – they are sorted by alphabetical order.
9T Labs and its Red Series Solution
Founded in 2018, 9T Labs is a Swiss manufacturer specializing in composite 3D printing. Its process, Additive Fusion Technology, enables continuous carbon fibers to be deposited in a polymer matrix in an automated, controlled manner. This is achieved via the Red Series, which comprises the print unit, Build Module, and the post-processing machine, Fusion Module. The 3D printer is capable of placing continuous fibers according to the orientation and trajectories chosen by the operator in the design and 3D file preparation phase. This optimizes the weight and cost of the part, and guarantees optimum solidity. If certain parts of the part do not require continuous fibers, the 3D printer fills them with a conventional polymer, or even a short-fiber-reinforced plastic. The machine is equipped with several sensors to monitor the entire printing process, as well as a temperature management system to minimize moisture build-up and ensure good adhesion between layers. Finally, if we turn our attention to the Fusion Module, the machine enables compression molding to achieve the best performance in terms of surface finish, consolidation and part quality. If you’d like to find out more about 9T Labs’ manufacturing process, take a look at the video below:
Anisoprint and its Desktop and Industrial Composite 3D Printers
When you think of turnkey continuous fiber 3D printing solutions, both desktop and industrial, Anisoprint is inevitably one of the main companies that comes to mind. Lead by Fedor Antonov and currently based in Singapore, the manufacturer has been dedicated to the goal to “introduce a new globally demanded industrial manufacturing technology for optimized structures made of composite materials.” To do this, Anisoprint uses its patented Composite Fiber Coextrusion (CFC) technology, which adds continuous fibers to a base thermoplastic including PLA, ABS, PETG and Nylon, among others. For its desktop solutions, the A3 (460 x 297 x 210 mm build volume) and A4 (287 x 210 x 140 mm build volume), it is possible to work with composites of up to 900 MPa. Meanwhile, the PROM IS 500 is the industrial solution from the company and is compatible with high-temperature plastics (up to 410°C) like PEEK and PEI with a build volume of 600 x 420 x 300 mm. What also makes the manufacturer standout is the fact that users can modify the density of the composite filler or vary the direction of the fibers to obtain optimal parts, what Anisoprint calls “anisoprinting.”
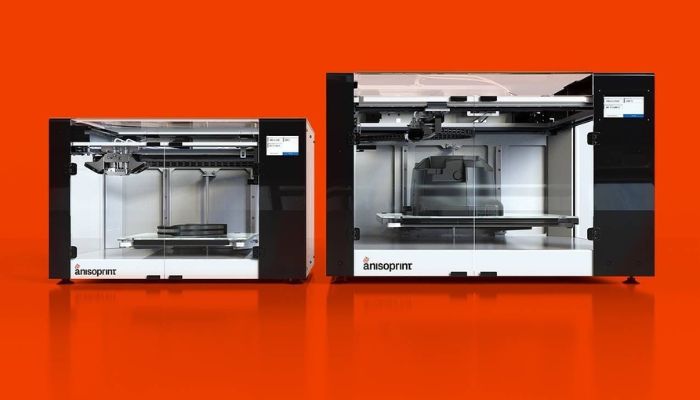
The two desktop solutions from Anisoprint, the A4 (left) and A3 (right)(photo credits: Anisoprint)
Continuous Composites
Founded in 2015, Continuous Composites is a company that promotes the development of innovative technologies for the industry. In order to solve slow speed, weak materials and small manufacturing volumes, they created the CF3D® solution. This automated manufacturing process starts with a continuous dry fiber that is impregnated with a fast curing thermosetting resin, which is deposited by the printhead. The method eliminates the need for molds, ovens and autoclaves, providing high material yield at a lower cost. The use of lightweight composite materials gives additive manufacturing a high level of performance and functionality. In addition, CF3D® technology can print structural and functional fibers in a single step process.

Photo Credits: Continuous Composites
Impossible Objects’ Industrial Composite 3D Printers
American company Impossible Objects has developed CBAM 25, a 3D printing technology specially designed for composite materials. This innovation is optimized for working with materials such as carbon fiber and fiberglass, combined with high-performance polymers like nylon and PEEK. Designed to meet the demanding needs of industrial environments, the CBAM 25 aims to transform additive manufacturing by delivering high performance in terms of speed and precision. This technology is capable of printing each layer in less than four seconds, enabling the production of parts up to 15 times faster than competing solutions on the market.
Markforged, an All-American Producer of Composite 3D Printers
Well-known American 3D printer manufacturer Markforged uses continuous filament fabrication (CFF) technology to extrude continuous fiber layer by layer. For this purpose, Markforged offers four types of reinforcement: carbon fiber, glass fiber, Kevlar and HSHT glass fiber. The composite materials are compatible with several of Markforged’s 3D printers, including the Desktop series (Onyx Pro and Mark Two), which combines industrial quality and affordability, and the Industrial series (X7, FX10, FX20) for robust and reliable parts even in large-scale, high-performance materials.
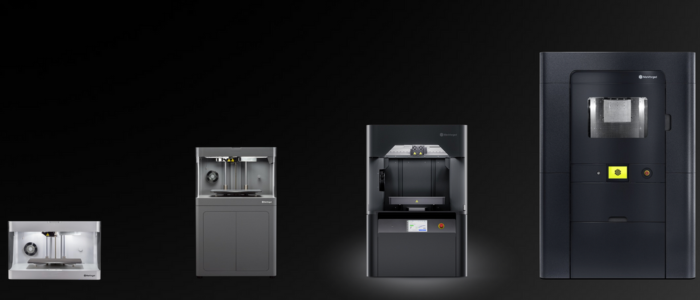
Photo Credits: Markforged
Moi Composites and its CFM technology
Moi Composites is a spin-off of Politecnico di Milano created in 2018 that has created its own patented technology, Continuous Fiber Manufacturing (CFM). This 3D printing method, as the name suggests, uses continuous fiber composite materials. Unlike the other solutions on this list, CFM consists of a print head that can be integrated into any CNC machine with more than four axes. The head can work with composite materials with carbon fibers, aramids, glass, materials of bio/natural origin, etc. Moreover, the company has customized software that helps optimize both design and production through intelligent generative algorithms. The program manages robotic machines, controls print quality and calculates the path of the entire process, from CAD design to 3D printing. The applications of CFM technology are wide-ranging. The company recommends its solution for creating products that require high mechanical performance, durability and functionality. As examples, the sectors that can benefit most from it are energy, aerospace, construction, sports and maritime.
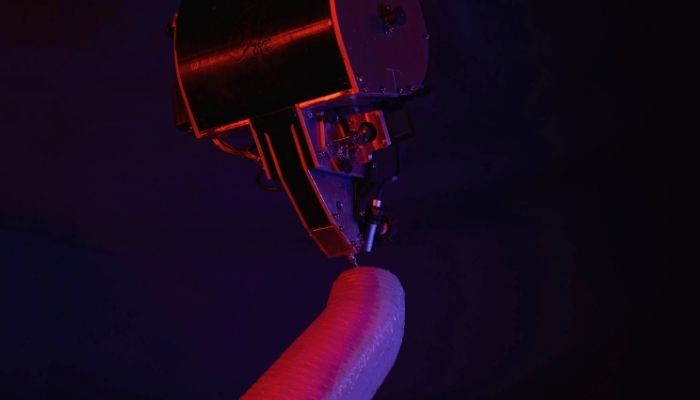
Photo Credits: Moi Composites
SphereCube’s Thermal Laser Curing for Composite 3D Printers
SphereCube is an Italian company involved in the manufacture of high-performance composite components. The company does not use molds and works to reduce environmental impact. Their technology, Thermal Laser Curing, allows them to create high-performance composite parts with continuous fiber reinforcement and thermoset matrix, thanks to their composite 3D printers’ extrusion head and 5-axis system. The printer is able to extrude the two materials with two different physical states: the polymer matrix in a viscous fluid state and the reinforcement material in the form of continuous fiber. When the extrusion is complete, a heat source is used to partially or fully cure the composite material. Usually, a UV source is used for solidification of these composite materials. Thermal Laser Curing also makes it possible to process different types of thermoset matrices and to make use of any type of continuous reinforcing fibers. These can also be of natural and plant origin, such as flax and hemp. In addition, SphereCube has patented its own method of preparing the reinforcing fiber, making use of a binderizing machine. Thanks to its brilliant work, SphereCube was selected as one of the winners of the Formnext Startup Challenge 2022.
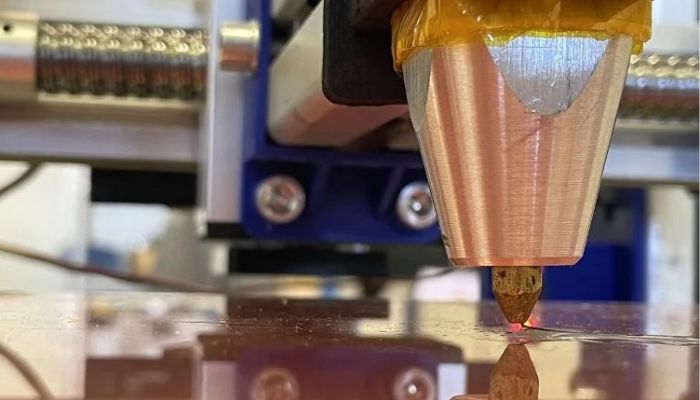
Photo Credits: SphereCube
What do you think of these composite 3D printers? Let us know in a comment below or on our LinkedIn, Facebook, and Twitter pages! Don’t forget to sign up for our free weekly Newsletter here, the latest 3D printing news straight to your inbox! You can also find all our videos on our YouTube channel.