The Complete Guide to 3D Printing Composites
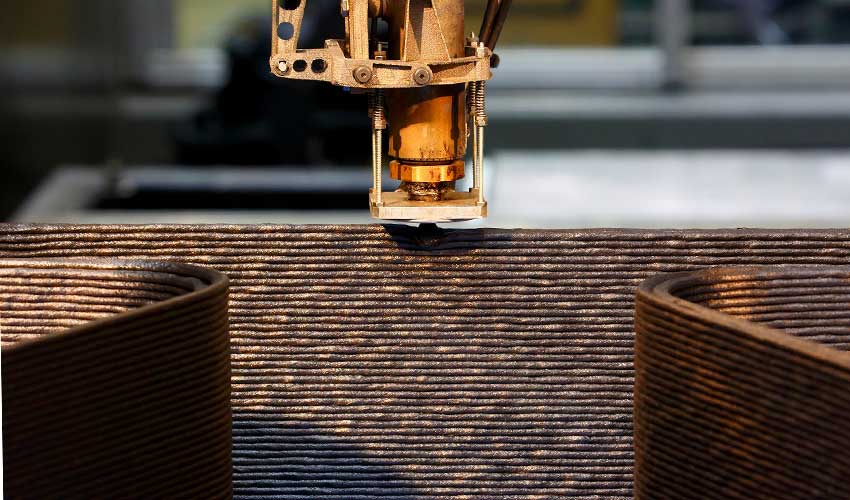
In recent years, composite 3D printing has grown rapidly in popularity. In a composite material, at least two different materials are joined together with separate purposes. One material serves as the matrix and is intended to maintain the structure, while the other provides additional properties as a reinforcing material. In fact, the goal of composites in general is to add new properties or characteristics while also overcoming certain drawbacks of the original material (which is the matrix). For example, it is possible to give the material better mechanical properties, flame retardancy, more stability, resilience, etc. Composites can be distinguished as a whole on the basis of their material characteristics (metallic, mineral, ceramic, organic) or on the basis of their geometry.
There are a few different forms of composites including: particle composites; fiber composites (short fiber, long fiber, continuous fiber ); layered composites; and impregnated composites. Out of these, fiber composites are those most often seen in 3D printing. Fiber composites are particularly popular in materials engineering because they allow materials to be reinforced in certain directions. Probably the most popular on the market is carbon fiber, followed by glass fiber, which are also the most commonly used in additive manufacturing. Carbon fiber’s popularity as well stems from the fact that it has one of the highest strength-to-weight ratios. This allows for strong but light parts, ideal for industries like aerospace.
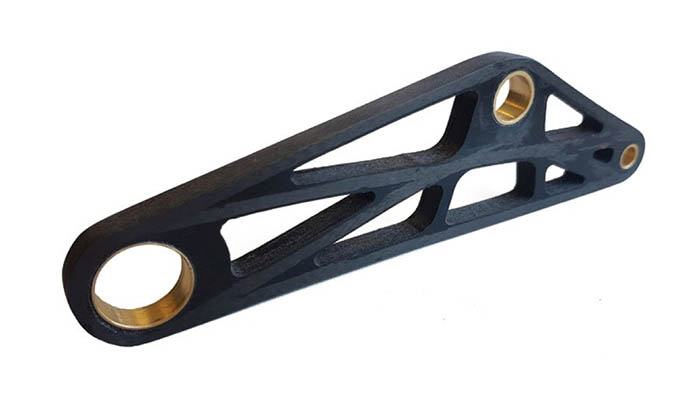
A 3D printed part using carbon fiber reinforcement, resulting in higher strength-to-weight ratio and less material consumption (photo credits: 9TLabs)
Properties of Composite Materials in 3D Printing
Composites are extremely beneficial when making lightweight yet strong parts. The fibers add strength to a part without adding weight. As mentioned, there are two types of reinforcements, short fiber or continuous fiber. In the first case, chopped fibers, which consist of segments less than a millimeter in length, are mixed into traditional thermoplastics to increase the stiffness and to a lesser extent the strength of components. Chopped fibers can be mixed with thermoplastics such as nylon, ABS or PLA. Every manufacturer will add and blend a different amount of short fibers to its plastic polymer, resulting in filament spools of different strengths. You should also be aware that print quality will be impacted by the quantity of chopped fibers. Above a certain threshold, the 3D printed part will lose in surface finish.
The highest performance comes from continuous fiber reinforcement. The process for making continuous fiber composites parts is not as easy as short fiber composites parts because the fibers need to be integrated into the thermoplastic continuously as the thermoplastic is being extruded. The fibers can also be deposited according to design techniques that optimize a part’s strength to weight ratio and material consumption, also known as DfAM (Design for Additive Manufacturing) techniques. Manufacturers claim that thanks to continuous fiber reinforcement you can create parts as strong as metal.
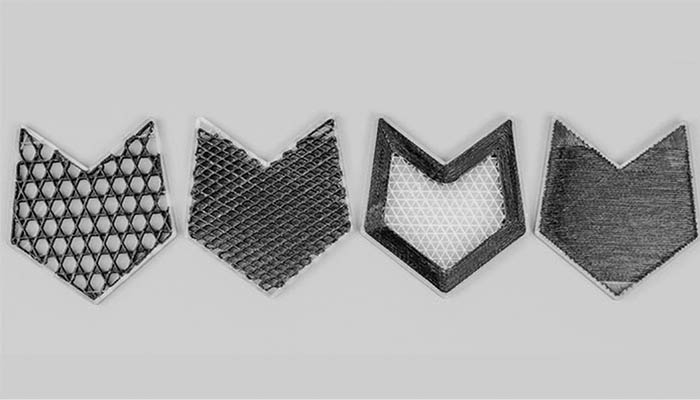
Anisoprint’s software can generate different types of continuous fiber reinforced infills (photo credits: Anisoprint)
In terms of available fibers on the market, carbon fiber is without a doubt the most popular. Fiberglass, a common type of fiber-reinforced plastic using glass fiber and Kevlar, a heat-resistant and strong synthetic fiber, are also widely used in the industry. Fiberglass is a cost-effective material for adding strength to plastics and Kevlar has high shock resistance as it bends instead of breaking. There are also some composites that are more aesthetic. For example, wood fibers, ceramic particles and vegetable fibers can also be found in combination with PLA.
Composite 3D Printing Technologies
In additive manufacturing, composite materials are mainly in the form of filaments and are therefore primarily used in FDM printing. However, approaches for metal composites in the laser process, such as LPBF, also are making headway. For example, Fraunhofer has develped a process to use laser deposition welding (LMD) with metal composites. This underscores the trend that composite additive manufacturing is gaining traction in the market and more technologies are expected to enable composite 3D printing in the future.
Essentially, composite 3D printing technologies differ according to the type of composite used. Short fiber composites can be extruded in the normal FDM process since the filament already contains the fiber. Furthermore, print quality can be affected by the quantity of shredded fiber in the matrix. Short fiber composites uniformly reinforce the entire part. Above a certain threshold, however, the 3D printed part loses surface quality. On the other hand, continuous fiber 3D printing is a trickier process that requires two nozzles to print at the same time. Usually, one nozzle will extrude the thermoplastic and the other the fiber. One printer that makes this possible is the Markforged Mark Two. The latter inserts the long-fiber materials into parts that he creates using the FDM process. In this way, the parts are only reinforced where it is actually required and desired.
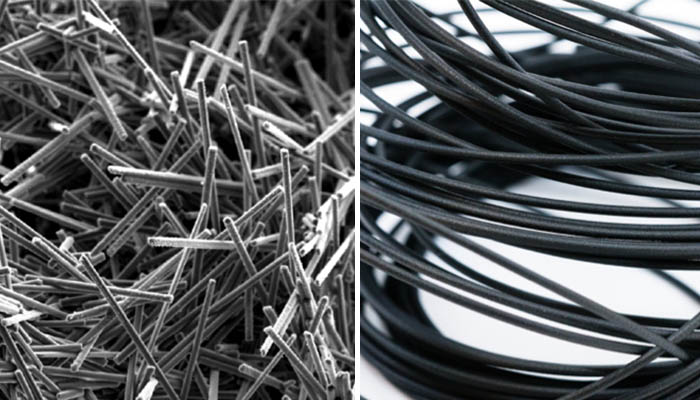
On the left you can see short fibers, which consist of segments less than a millimeter in length. On the right the filament has been reinforced by these short fibers. (photo credits: Markforged)
One thing to note about FDM printing with composites is that they often require a larger nozzle diameter. As a rule, the manufacturer specifies which setting must be made. For fiberglass, the nozzle should be set to a minimum diameter of 0.6 mm, for carbon fiber, 0.4 mm and for Kevlar, start with 0.6 mm and then gradually decrease to 0.4 mm. If the composite has wood particles, it is necessary to set the diameter between 0.6 mm and 0.8 mm.
In addition, it should be noted that composite filaments can lead to increased wear on the hot end and extruder components. To prevent this, it is advisable to use hardened nozzles, especially with carbon, fiberglass and Kevlar filaments. It is also important to position the spool well during the printing itself in order to optimize the path to the extruder so that it is not too long. In addition to these precautions, the printing speed should also be reduced due to the higher viscosity of the composite material filaments and the recommended speed for the base material should not be used. In contrast to the requirements for the pressure settings, however, composite materials offer the advantage
Applications With 3D Printed Composites
Being able to print with reinforcement materials has been a goal of a number of startups in the 3D printing sector. In recent years we have noticed a growing number of machines and technologies being launched on the market to enable new applications, especially in industrial sectors such as aerospace and automotive. Carbon fiber filled materials are the most widespread composites in the 3D printing industry, especially for demanding applications such as functional prototypes, automotive parts, lightweight components, etc. Carbon fiber composite is also becoming more and more popular in the sports sector. Top athletes are turning to carbon bikes for lighter and therefore faster bikes, and Formula 1, motor sports and even tennis and rowing are also making use of these advantages.
Indeed, the market for composites is growing, and new material combinations will enable new applications. They are also being added to technical materials, for example last year researchers in China were studying the benefits of adding carbon fiber to high performance thermoplastics such as PEEK. Another example comes from Sandvik who created the first diamond composite. Usually diamond is impossible to use in additive manufacturing because it is too hard, however by creating a diamond composite, the material’s properties can be used for many resistant tools (mining, drilling or machining) and also medical implants!
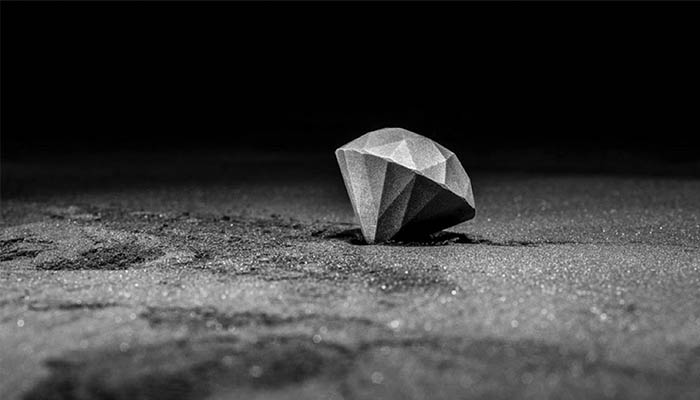
The diamond composite created by Sandvik (photo credits: Sandvik)
Manufacturers of 3D Printers and Filaments
Not surprisingly, composites are often more expensive than the individual materials, and prices vary by manufacturer and composite used. The coils are therefore at a wide price gap between $150 and 500. Also worth noting that these special materials also requires a printer with specific properties. A printer with these specific requirements is often accompanied by its own technology, which the manufacturers call and market differently.
Of course, you will have heard of the main actors in the sector including CEAD, Markforged, Anisoprint or Roboze. For short fiber composites, filament manufacturers include Roboze, 3DXTech, ColorFabb, etc. New actors are also emerging rapidly on this market, for example the young 9T Labs, based in Switzerland has created an add-on system for ordinary 3D printers to enable continuous fiber 3D printing. They call this 3D printing process Additive Fusion Technology (AFT); the reinforcement is made from a carbon-filled material, not exactly pure carbon fibers.
In terms of names for processes among the major manufacturers, Markforged calls it Continuous Filament Fabrication (CFF), whilst Anisoprint calls it Composite Fiber Coextrusion (CFC). Another interesting technology is AREVO’s proprietary process based on Directed Energy Deposition technology, in which a laser is used to heat the filament and carbon fiber at the same time as a roller compresses the two together. Impossible Objects has also added systems for continuous fiber 3D printing to their range of machines, the technology however differs a bit. They weave in sheets of carbon fiber into a print by using a lamination process. Last but not least, Continuous Composites uses a hybrid technology where the strand of fiber is soaked with resin and then hardened using UV light, similarly to SLA 3D printing.
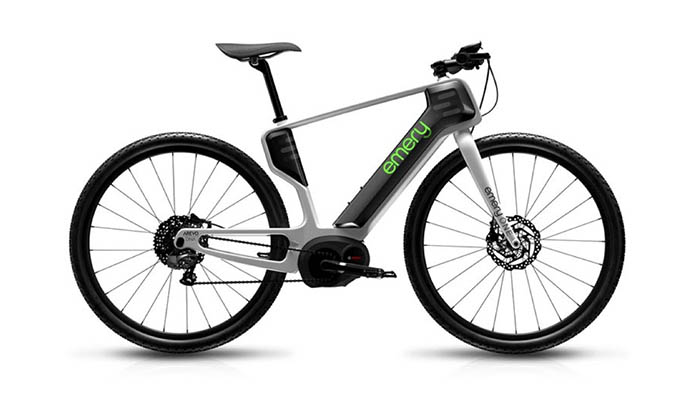
AREVO’s bike frame has been created using continuous fiber 3D printing | Credits: AREVO
What composite will be used for 3D printing next? Will their adoption expand to series production? Let us know in a comment below or on our Facebook and Twitter pages what you think! Don’t forget to sign up for our free weekly Newsletter, with all the latest news in 3D printing delivered straight to your inbox!
*Credits Cover Image: SABIC
Hello, can the variable stiffness laminate be processed?
(composite laminate with curvilinear fiber path layup)