Cognitive Design, the Software That Optimizes Design and Ensures Part Manufacturability, Whatever Their Complexity
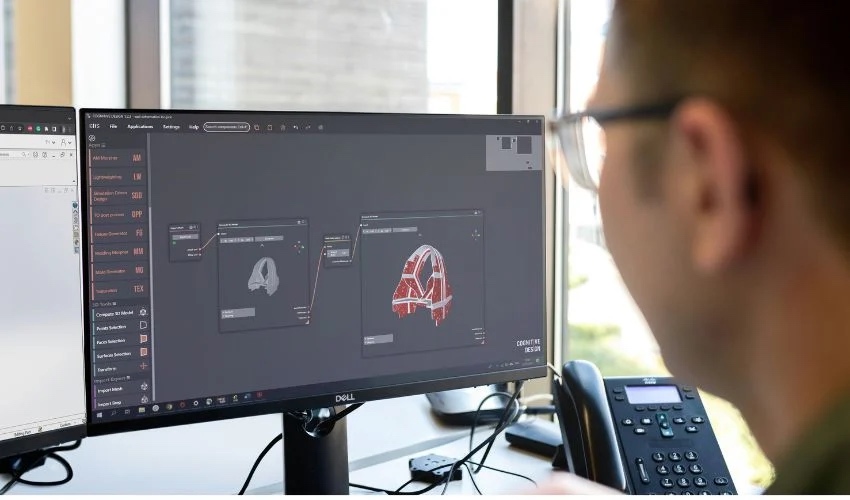
Engineers are always looking for reliable solutions to optimize their designs and ensure that they can be manufactured in the best possible way, whatever their complexity. However, most of these solutions often involve a lot of back-and-forth between design, simulation, manufacturing and analysis teams, adding to lead times and costs.
To overcome this problem, Cognitive Design Systems has launched a new software package: Cognitive Design, which was designed to improve the design process for high value-added parts. Thanks to a single tool, CAD engineers will be able to optimize designs that meet all end-user requirements, obtain the best performance through optimized geometries and, above all, ensure the manufacturability of their design.
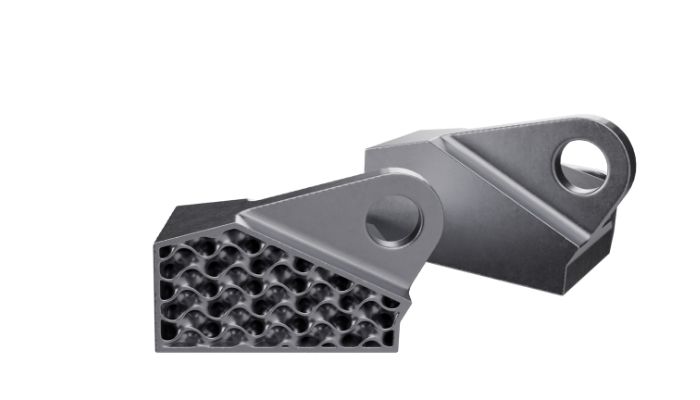
Optimized parts thanks to TPMS filling
The Challenges of Additive Manufacturing Design
Additive manufacturing has opened the door to unprecedented geometric freedom, freeing us from the constraints inherent in conventional manufacturing processes. For example, it is now possible to use architectural materials, such as lattice structures, or to produce organic structures derived from topological optimization or biomimetics, such as the porosity of a bone body. But traditional design tools are limited in their ability to support these new design freedoms, and to easily integrate data from simulation or feasibility analysis.
Most design engineers have extensive knowledge of conventional manufacturing processes and the associated business rules. As additive manufacturing is a new technology, it implies a new way of thinking about design, and the need to take into account new business rules of manufacturability. The ability to educate engineers in these new practices is increasingly being raised as one of the key components in the adoption of 3D printing, particularly within large corporations.
One of the advantages of additive manufacturing is the ability to test different designs through iterations that are less costly than injection molding, for example. However, design optimization is not an obstacle-free process. Changes in part design require testing and analysis. What’s more, there’s no guarantee that the new design can be 3D printed without difficulty. This means more tests, longer lead times and additional resources. Furthermore, this design optimization and its manufacturability are not evaluated in the same software, creating silos in the process and therefore potential complications.
CAD engineers then find themselves with multiple data sets and numerous adjustments to make, usually manually. They are faced with additional challenges, and have to manage a multifaceted project. This is especially true when the part geometry is complex. The whole design and manufacturing process is lengthened, and the likelihood of errors increases considerably.
The Main Benefits of Cognitive Design
Given these constraints, Cognitive Design Systems has developed a new software solution to simplify design optimization and guarantee the manufacturability of any part. This software is based on an innovative geometric engine developed in-house, bringing a new dimension to optimization, both in terms of capacity and ease of implementation, while ensuring unrivalled robustness.
One of the software’s first key features is the ability to achieve maximum performance quickly. In concrete terms, the user can semi-automatically identify and implement all possible geometric optimizations on the analyzed design, without any conventional CAD limitations. This translates into options for reducing the weight of the part by playing on the filling or integrating lattice structures or ribs. These geometric changes can be dictated by input data from the user’s own simulation software, as part of a Simulation-Driven Design workflow. In so doing, Cognitive Design ensures interoperability with the existing digital chain, and optimized geometry in line with the certified solutions of the engineer’s environment.
In addition to the topological optimization commonly used for performance research, advanced capabilities such as variable thickness modification and adaptive filling contribute to the achievement of optimal geometry. Based on simulation results, Cognitive Design ensures increased part performance without the risk of counter-productive modifications such as excessive material removal, which would alter mechanical properties.
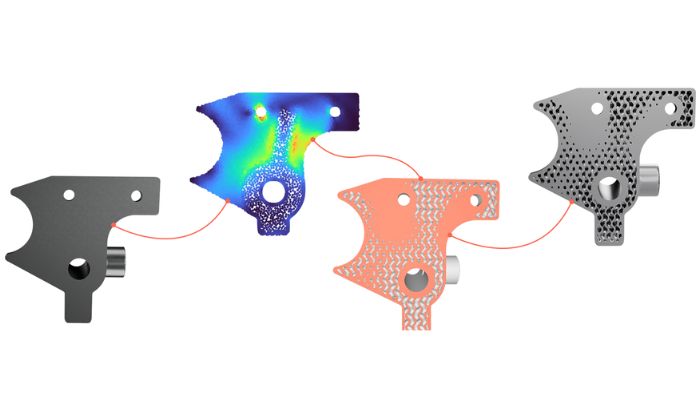
Optimization process using a simulation-driven design approach
Cognitive Design can also be used to generate designs that can be 3D printed, and to liaise with production teams. In fact, the software is capable of identifying manufacturing defects right from the start of the design cycle, thanks to its manufacturability analysis tools. Using different strategies, it offers precise adjustments to part geometry, rib thickness, thermal concentration and parameters for removing excess powder, for example.
Not only is the software able to provide the user with all this information, thus streamlining the design process by reducing the number of iterations, it is also capable of automatically making the geometric modifications required to improve feasibility. This manufacturing-driven design methodology is essential for reducing the development cycle and ensuring the manufacturability of a part, whatever its complexity.
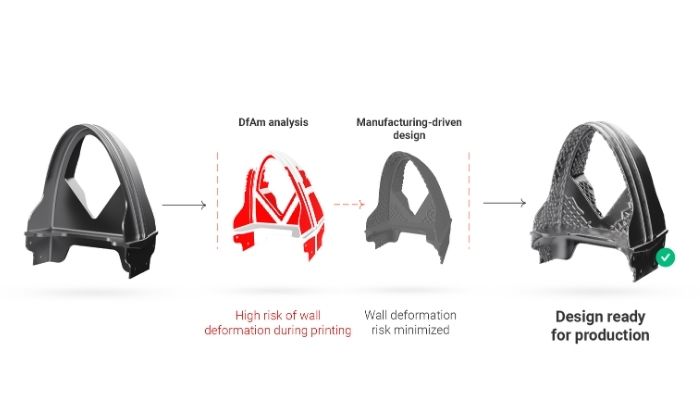
Geometric modification process based on feasibility analysis using Cognitive Design software
Finally, the software accelerates advanced engineering and innovative product development by creating fully customized workflows. The solution also includes pre-built optimization workflows whose components can be fully modified by the user. Parametric design makes it easier to multiply iterations and obtain optimized, reliable designs. Engineers seeking for performance are now able to quickly generate several versions of their design to identify the best iteration, and then re-use their workflow on a new part, thus ensuring the re-use of a proven design strategy with new ease.
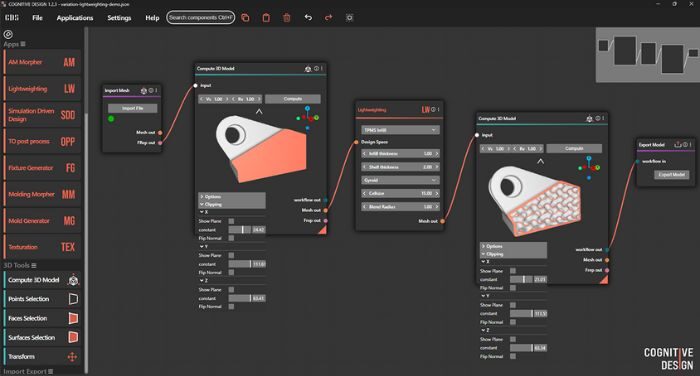
Cognitive Design interface overview: the lightweighting workflow
Cognitive Design is a complete software package that enables you to produce optimized designs, whatever their geometric complexity. It’s a solution that also guarantees the manufacturability of these designs, without the need for time-consuming steps or other tools. To mark the launch of Cognitive Design, you can take advantage of a 60-day free trial of the software. Click HERE to find out more
What do you think of Cognitive Design Systems’ software solution? Let us know in a comment below or on our LinkedIn, Facebook, and Twitter pages! Don’t forget to sign up for our free weekly newsletter here for the latest 3D printing news straight to your inbox! You can also find all our videos on our YouTube channel.
*All Photo Credits: Cognitive Design Systems