Closed-Loop Additive Manufacturing Could Be Possible Thanks to ORNL Research
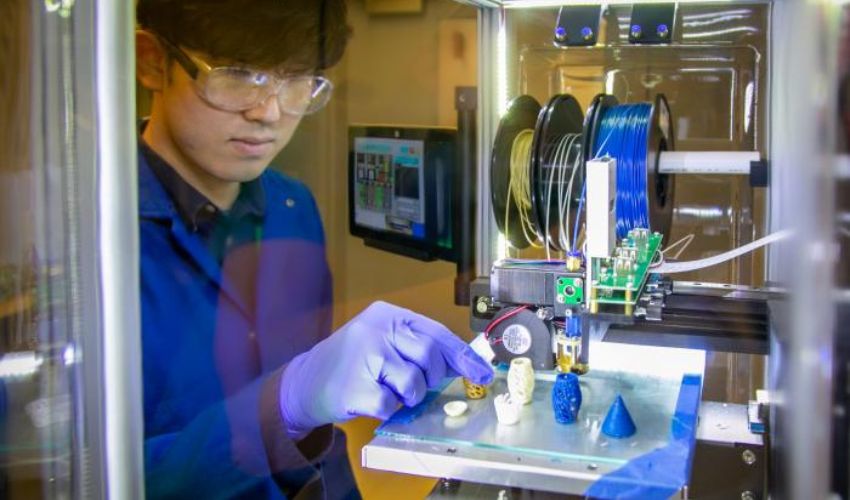
As the climate crisis becomes more and more evident, sustainability has become a key driver of innovations in technologies. And additive manufacturing is certainly no different. Most recently, researchers at the Department of Energy’s Oak Ridge Laboratory have developed an upcycling approach that allows for discarded plastics to be reused in FFF 3D printing. This thus would allow for fully closed-loop additive manufacturing, officially ensuring that there is no waste in the process. The team hopes that this easily-adoptable and scalable method will lead to a global reduction of plastic waste as well as cut carbon emissions from plastic production.
The ORNL is one of the leading institutes that is researching the usage of additive manufacturing, namely for more effective energy policies in the USA. Previously, we also told you about another of their projects for 3D printed solar batteries. This latest research, shows as well their drive not only to adopt 3D printing for more sustainable policies, but to make AM itself more sustainable. The results were published in the article “Closed-loop additive manufacturing of upcycled commodity plastic through dynamic cross-linking” in Science Advances and were written by Tominori Saito, Sungjin Kim, Anisur Rahman, Arif Arifuzzaman and Edgar Lara-Curzio.
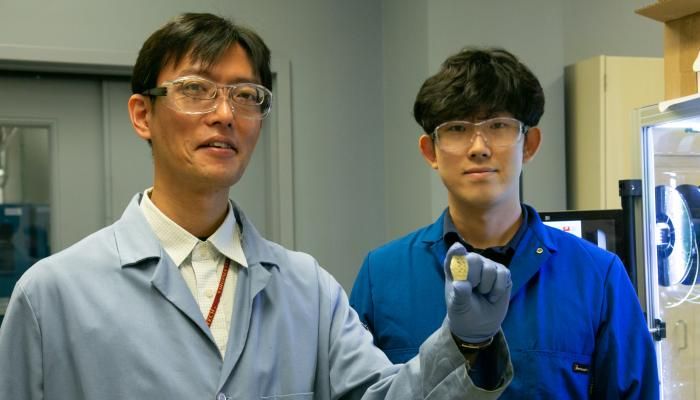
ORNL polymer scientists Tomonori Saito, left, and Sungjin Kim (photo credits: Genevieve Martin/ORNL, U.S. Dept. of Energy)
This topic especially has been of particular interest within the AM industry. Notably, how to use AM to promote the idea of a circular economy, a model of production and consumption which aims to reuse, repair and recycle products for as long as possible, reducing waste to a minimum. 3D printing is often chosen as a key technology for a circular economy as during production, depending on the technology used, it does not generate waste. The lead author, Tomonori Saito of ORNL’s Chemical Sciences Division, commented on the importance of the work, noting, “This effort demonstrates a closed-loop for manufacturing plastic items, potentially with higher value and performance, using only existing plastic waste in one of the most accessible areas of additive manufacturing.”
How Does Closed-Loop Additive Manufacturing Work?
For this project, the team upgraded acrylonitrile butadiene styrene, better known as ABS, which is one of the most popular 3D printing materials available. The thermoplastic is also a popular choice for many everyday projects however, including LEGO blocks, tennis balls and even auto parts. It is thus, a good choice for upcycling. The problem, however, is that when products are recycled into something new, the material loses key mechanical properties.
In this case, the researchers sought to not only successfully keep the properties of ABS, but to actually make it stronger during the upcycling process. Saito expanded on this, stating “We will need fundamental discoveries to overcome the challenges of increased costs and deteriorating material properties associated with recycling. Our goal was to develop an easily adoptable strategy that reuses plastic waste to create a more valuable material instead of generating fresh plastic.”
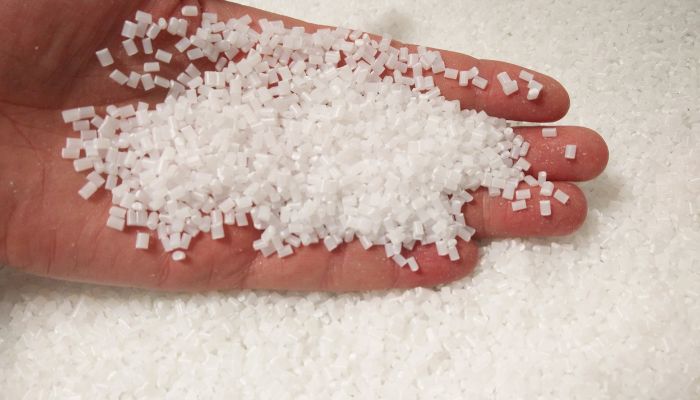
ABS, shown here in granular form, is a commonly used thermoplastic in both 3D printing filaments and everyday objects (photo credits: Jacorna, CC BY-SA 4.0, via Wikimedia Commons)
And it is safe to say that they succeeded in their goal. The final results showed that the upcycled ABS had achieved about double the toughness and strength of standard ABS, with enhanced solvent resistance. This was done through the use of “click” chemistry to convert the chemical makeup of ABS into a virtimer, a polymer combining thermoplastics and thermosets, which often are not compatible with FF. Essentially, this allowed them to have the best of both as the resulting material had the processability and recyclability of a thermoplastic as well as the superior mechanochemical properties of thermosets. To create it, medical compounds were mixed before being cured.
The hope is that with projects such as these, it will be possible to truly reuse and recycle the 400 million tons of plastic waste generated each year. Of which only 10% is ever recycled. Another of the researchers on the project, ORNL’s Sungjin Kim concluded, “Developing new, recyclable materials with superior properties for FFF creates opportunities to make a big impact on plastic production and expand additive manufacturing capabilities that have the potential to reduce our carbon footprint.”. You find more information on the ORNL website HERE.
What do you think of this closed-loop additive manufacturing project from the ORNL? Let us know in a comment below or on our LinkedIn, Facebook, and Twitter pages! Don’t forget to sign up for our free weekly Newsletter here, the latest 3D printing news straight to your inbox! You can also find all our videos on our YouTube channel.
*Cover Photo Credits: Genevieve Martin/ORNL, U.S. Dept. of Energy