Chopped or Continuous Fibers: Which Reinforcement to Choose for Composite 3D Printed Parts?
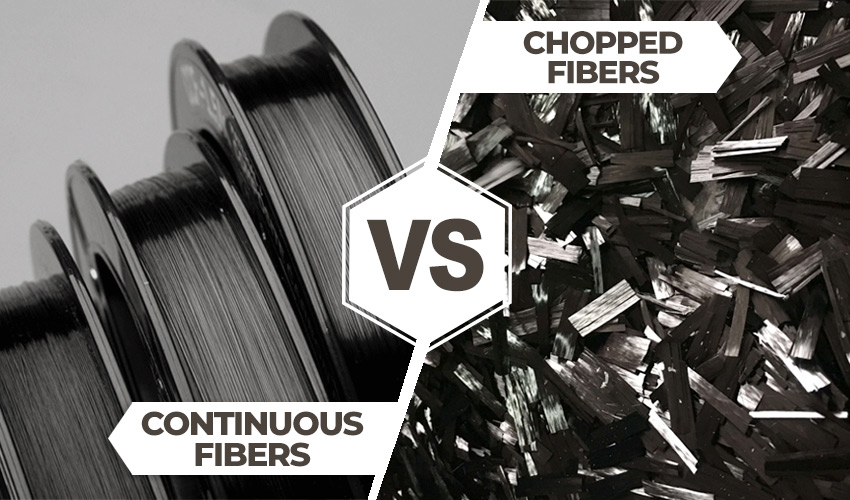
When specific or superior properties are needed in 3D printed parts, composite 3D printing is often used. The resulting parts are stronger than certain metals and offer high performance. Composites are defined as two materials that are combined to achieve new or improved properties as compared to those of the starting materials. As such, there are numerous composite materials, although in this case, the focus will be on composite materials that are formed by a polymer matrix and fiber reinforcement. In the 3D printing industry, carbon fiber, glass fiber and Kevlar are three of the most common fiber materials used for composites.
In this article we will look at 3D printing of chopped and continuous fiber reinforced composites.These two techniques give different results and are done with different technologies. Although, for both, the most popular material extrusion and therefore is the technology that will be most emphasized.But what, then, are the similarities and differences between these two techniques and how to choose the most suitable type of reinforcement for a specific application? Let’s take a closer look.
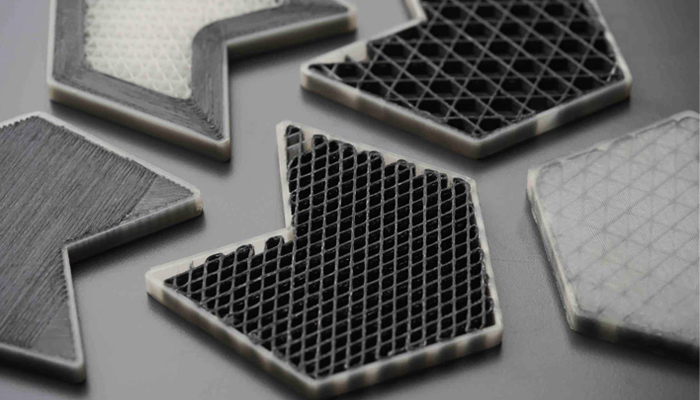
Photo Credits: Anisoprint
Characteristics of Chopped and Continuous Fiber Composite Materials
By chopped, or short, fibers we mean smaller pieces of fibrous material, the length of which can vary from centimeters to millimeters or even less. This is a process similar to that used to reinforce concrete with pieces of reinforcement. The fibers are dispersed in the plastic matrix and act as reinforcement throughout the material.
Continuous, or long, fibers, on the other hand, are long strands that extend the entire length of the composite part. These fibers are integrated into a plastic matrix through the 3D printing process, creating a composite material that combines the properties of both. Before moving on to the additive manufacturing process itself and the points to consider when creating these parts, it is important to know the characteristics of both.
In both cases we find the same composition: a reinforcement (fiber) and a matrix (polymer). The former provides the mechanical properties, while the latter acts as a container and, with the help of a resin, ensures that the two elements are held together. That is, the fiber adheres to the material during production. Once the matrix compounds (common polymers include PLA, ABS, polypropylene, HIPS, PETG, etc.) and the reinforcing fibers (glass, carbon, or aramid) are chosen, they are combined into a single material.
Chopped fibers can be obtained by an extrusion process: the mixture of fiber and matrix is melted and extruded to form a single filament. During this process, temperature and speed can be controlled to ensure good fiber distribution.
Continuous fibers, on the other hand, when forming filaments, can be coextruded with a special resin through a process in which the blend is mixed, cured and solidified with the resin. In some cases, there are production systems that directly mold the matrix and reinforcement at the same time during the deposition of successive layers, but more on this later. In either case, the chopped and continuous fibers must be clean and free of contaminants to ensure good adhesion to the polymer matrix.
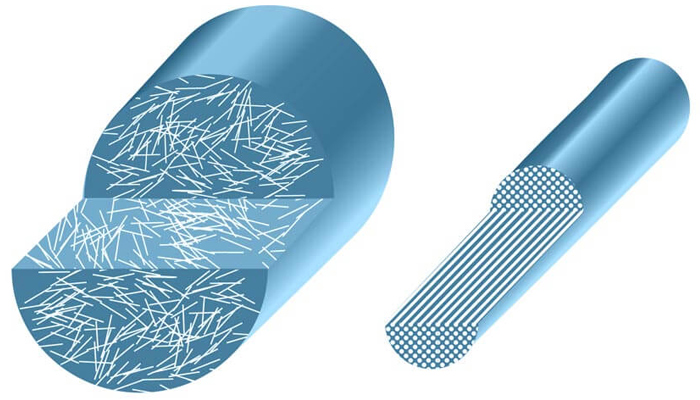
Difference of the arrangement of chopped and continuous fibers in the matrix (photo credits: Coperion)
If we focus on the properties of the reinforced materials themselves, we see that they differ greatly depending on the polymer used as a matrix and the choice of fiber type. Obviously, if the base plastic material is a technopolymer, the composite will have more advanced properties than those of standard matrix plastics.
For example, if a composite has polypropylene as its matrix polymer, it will have good basic wear resistance, impact-absorbing capacity, and greater toughness and flexibility. On the other hand, if PLA is used, the composite will be easier to print, but will have a greater tendency to break due to the low strength of the material.
As mentioned, there are three main types of fibers, both chopped and continuous: carbon, glass, and aramid (Kevlar). Carbon fibers are the most widely used in the manufacturing industry because of the high strength and stiffness they offer the final parts. Glass fiber reinforcements are generally more affordable and also offer good strength, although not as much as carbon. Finally, Kevlar fibers are often used in bulletproof vests because of their high impact and impact resistance. In any case, the purpose of using chopped or continuous reinforcing fibers is to make strong, lightweight parts.
3D Printing Processes for Chopped and Continuous Fibers
Most 3D printers capable of processing composite materials use extrusion. As for chopped fiber FFF 3D printing, the process is the classic one. Short fibers cut into small pieces are mixed with plastic material to form a spool of filament that can be used with FFF 3D printers. In this case, the fibers are simply suspended in the thermoplastic, which is heated and extruded to form the part layer by layer just like any other part made with this technology. However, a hardened nozzle will be needed to resist the abrasive fiber strands.
In contrast, 3D printing of continuous fiber composites is more complex; in the material extrusion process, a second nozzle is often needed to separately deposit the matrix and continuous fiber strand. Alternatively, the single nozzle head must have a specific construction to mix the fiber with the matrix. The process involves arranging continuous fibers with a specific direction within the matrix. The latter acts as a casing that contains the reinforcing fibers.
To ensure adhesion of the fibers with the matrix, a thermosetting resin-based matrix or filler is usually used. This is then cured by UV light or heat source to fuse the layers and materials together. The description of the process is intentionally generic, as there are numerous proprietary technologies for 3D printing continuous fiber composites that differ, albeit minimally, from one another.
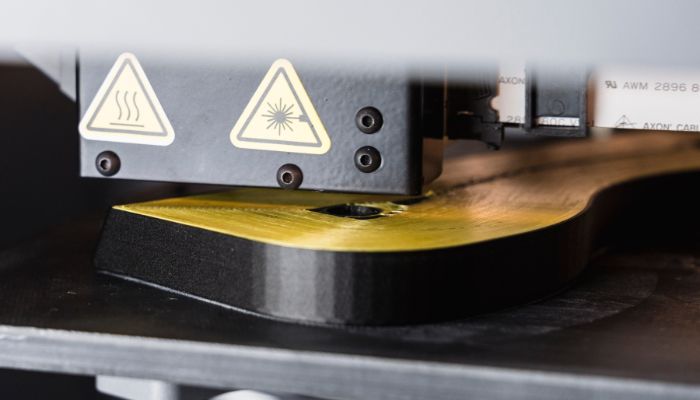
3D printing of a polymer matrix and Kevlar fiber reinforcement.(Credits: Markforged)
An important aspect when printing with fibers, especially continuous fibers, is the use of finite element analysis (FEA) software, which is a computerized method of predicting how a product will react to external forces and stimuli. This makes it possible to analyze material characteristics and precisely define the pattern according to which to arrange continuous fibers in the matrix. However, it also requires some design limitations in order to prioritize the correct placement of the fibers and thus the performance of the part. Specific material properties will thus be defined according to a controlled process. This is the same for composites reinforced with chopped fibers, since in these it is not possible to control the amount and position of the deposited fibers, representing them as one with the matrix.
Benefits and limitations
As we know, some of the main advantages of 3D printing with composites include increased flexibility and speed of production, as well as the ability to create complex parts compared to more traditional methods. Also, as just mentioned, an important advantage that can be found with this technology, as long as continuous fibers are used, is that it allows you to control the deposition process and decide where and how to place reinforcement for the final parts.
If we focus on the advantages of chopped and continuous fibers as reinforcements in 3D printing, we can find some commonalities. Both types of fibers offer superior mechanical strength compared to unreinforced plastics. In particular, they improve the stiffness of the material and increase its fatigue and impact resistance. In addition, fibers such as carbon fibers are very light, which helps to keep down the weight of parts where this plays a key role.
Likewise, both chopped and continuous fibers have some limitations. For example, the need for specific 3D printing equipment to produce them. In addition, there are many aspects to consider when processing composite material, such as adhesion between the fiber and the plastic matrix, which can be a challenge.
Nevertheless, there are some ways in which the two types of fibers differ. The main limitation of chopped fibers compared to continuous fibers is that they provide less effective reinforcement. This is because the orientation and distribution of chopped fibers along the composite are more random, whereas continuous fibers are constant. Therefore, the reinforcement effect with chopped fibers is less pronounced, which may not be sufficient for applications requiring high strength. However, a key advantage of chopped-fiber composites is that they are easier to process and generally cheaper than continuous-fiber composites, making them more affordable. In addition, chopped fibers can be used with a wider variety of plastic materials, allowing for high design flexibility.
Applications
The choice between continuous and short fibers, as well as the polymer matrix, will depend on the type of application and performance required. Continuous fibers are ideal for applications that require high strength and stiffness, while short fibers are more suitable for projects that require ease of processing and lower cost.
For this reason, continuous fibers are most commonly used for structural components in advanced industries, such as automotive (chassis reinforcements or interior components) or aerospace (support structures and aircraft components). They can also be implemented in consumer products that require high strength, such as bicycles or sports equipment.
Meanwhile, 3D printed short fiber composites are also commonly used to produce prototypes. They are also often used for parts in the packaging industry, robotics, consumer products, and other components that do not require high tensile strength.
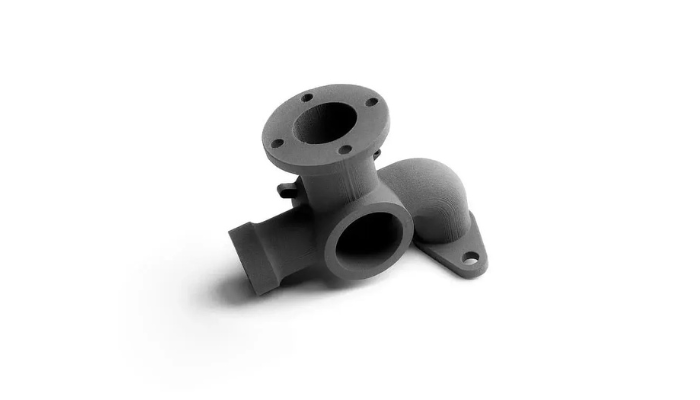
Piece made of PEEK carbon fiber (photo credits: Weerg)
Manufacturers and Prices
3D printing solutions for short and continuous fiber composites, while not as numerous as those for standard polymers and metals, are quite varied ranging from robotic arms, to industrial printers, to desktop solutions. Among the providers of continuous fiber 3D printing solutions, Markforged offers Continuous Fiber Fabrication (CFF) technology and a range of desktop and industrial solutions. These are capable of printing PLA, TPU, White Nylon, Onyx™ and ULTEM composites reinforced with carbon fiber, Kevlar or fiberglass. Anisoprint also offers solutions for 3D printing with continuous fiber via Composite Fiber Co-extrusion (CFC) technology.
Desktop solutions offer wide flexibility in material selection with an open system, while the ProM IS 500 industrial solution is compatible with high-performance plastics such as PEI, PEEK, PEKK and others. Other companies that provide continuous fiber 3D printing solutions are Continuous Composites or CEAD, which offers an LFAM solution.
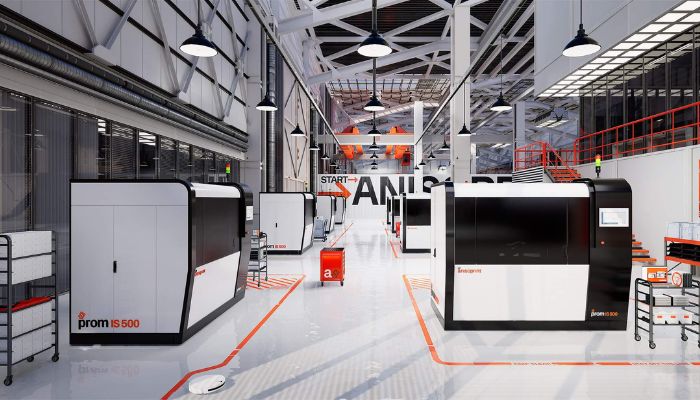
Photo Credits: Anisoprint
In addition, as mentioned, more and more startups are studying and patenting new 3D printing processes for continuous fiber composites. These include Moi Composits, SphereCube, Fabheads, 9T Labs and Arevo, among others.
It is worth mentioning that there are not only technologies for continuous fiber reinforcement during the manufacturing process. For example, Spanish startup Reinforce 3D has come up with CFIP (Continuous Fiber Injection Process) technology for reinforcing parts with continuous fibers at the post-processing stage, following additive manufacturing.
As for manufacturers of 3D printers for chopped fiber composites, we find mainly manufacturers of FFF machines capable of processing high-performance materials reinforced with carbon fiber or other fibers.These include Roboze, Stratasys, 3ntr, miniFactory, BigRep, WASP or Creality (although this list is not exhaustive).
If we look at prices, the main difference is related to the type of machine used .For both chopped and continuous fiber 3D printing, the price is generally high for industrial solutions because these are materials that require special printing conditions, such as high temperatures for the nozzle, chamber, etc. Desktop machines for 3D printing of short fiber composites can be priced from $400, while those for continuous fiber 3D printing start at around $9,000.
As for industrial solutions, manufacturers do not always make prices public, which can run to several hundred thousand dollars depending on the process and size. In that case, you can request quotes directly through official websites.
What do you think of our comparison of chopped and continuous fibers for 3D printing? Let us know in a comment below or on our LinkedIn, Facebook, and Twitter pages! Don’t forget to sign up for our free weekly newsletter here for the latest 3D printing news straight to your inbox! You can also find all our videos on our YouTube channel.