Exploring jewelry making using 3D printing with Caroline Auraix
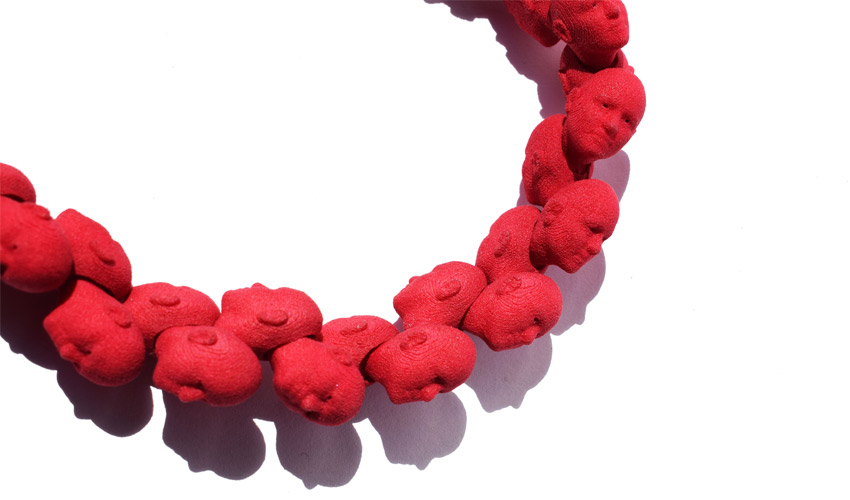
In the jewellery sector, additive manufacturing has many benefits, especially in terms of creativity. It enables designers to design complex shapes that are impossible to obtain using traditional manufacturing methods. It also offers greater scope for personalization, satisfying consumers looking for new and original jewelry. 3D printing technologies are mainly an additional tool for these artists who want to express their imagination, in addition to using traditional techniques. Caroline Auraix is one of those French designers who uses 3D modeling and printing to produce unique pieces with surprising shapes. We met her to learn more about her creative process, her inspirations and the technologies she uses today.
3DN: Can you introduce yourself and your link to 3D printing?
I am a visual artist, and I live in Paris. I worked for 10 years as a collection director and workshop manager alongside designer Tzuri Gueta, known for his silicone fashion accessories. This long collaboration ended at the end of 2016, I left my job to tell my own stories. I was set on orienting my work towards the “human”, my main source of inspiration, I create jewellery sculptures with surrealist, metaphysical accents, which question our relationship to reality. I have always been fond of synthetic materials, from plastics to resins, including silicone. I sublimate them in “trompe l’oeil” compositions where the senses are disturbed.
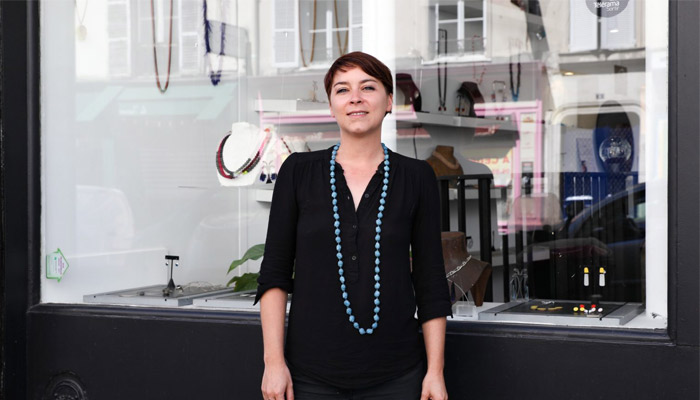
Caroline Auraix
The first time I heard about 3D printing was many years ago, I was literally fascinated by the infinite possibilities that this technique could bring to the world: finally, reality was catching up with fiction! At the time, I had no knowledge in the field of modelling. I saw this advance as something inaccessible, and reserved for a scientific elite, engineers, programmers, and other high-flying computer scientists. Until the day I decided that I too could, at my humble level, use this technology to serve my creation. So, the 3D adventure began!
3DN: Why do you use 3D technologies in your work?
When I started as an artist, I was immediately confronted with the time factor! Creating, manufacturing, selling, promoting, communicating, managing… So many stages, each more time-consuming than the next; it was necessary to find a solution to make possible this project that was close to my heart, and for which I had given up everything. That’s how 3D printing came to me. Thanks to this process, I have saved time on the production of my work, and I can offer them at much more affordable price than if they had been produced in the traditional way. All this contributes to my desire to democratize art so that everyone can afford an artist’s piece without spending an unreasonable amount.
3DN: How do you use 3D technologies in your work?
I work mainly on Rhino3D, it is the reference software in the jewellery industry. I learned the mechanics of this software during a one-week internship and I trained myself for the rest. I also found free modelers, where I can switch my models for “modeling pastes” effects, which take longer to create with Rhino. I also work with character generators, which reminds me of the long hours I spent on my video games customizing my players.
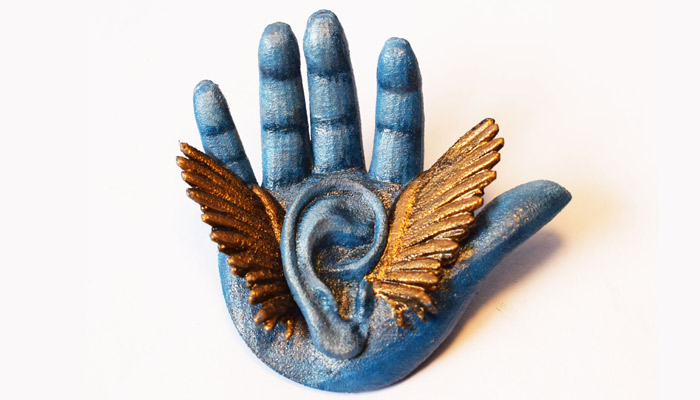
A pin designed thanks to 3D printing | Credits: Caroline Auraix
Once I have made a composition that I like (it can take days…), I use a service provider for printing. I work a lot with Shapeways, which I find quite good in the quality/price ratio even if we are limited to a 64 MB file. Which in some cases can be painful, when working with very large files. They must be reduced, and in doing so, the definition is no longer there.
3DN: What technology do you use?
I have tried several materials with different 3D printing providers (not yet having my own printer). What lends itself best to my work is SLS technology with nylon. I found that its porosity allowed incredible dyeing effects. In addition, in a very thin layer (0.60 mm) it allows light to pass through, which makes it perfect for making luminaires. Its solidity and lightness make it an ideal material for jewelry.
I voluntarily choose white, this allows me to customize my creations at will, and to give a unique character to each of them. I achieve material effects by painting them by hand with a ceramic paint that offers a more intense rendering than acrylic for example. I have tried metal sintering with several renderings (bronze, silver…) but this solution is not durable for jewellery because with friction, the plating disappears quite quickly. Nevertheless, this technology offers great possibilities for small decorative objects.
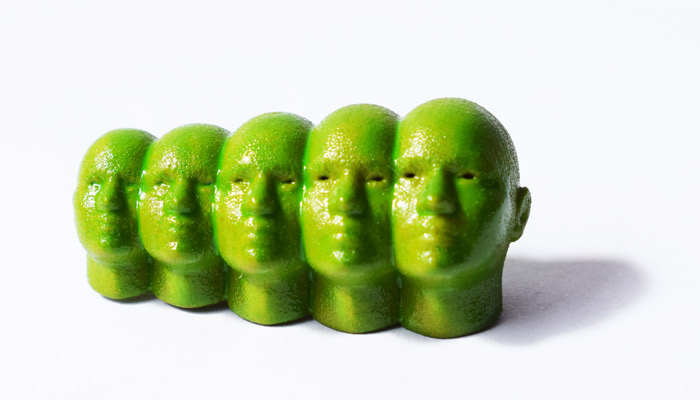
With 3D printing you can achieve original designs | Credits: Caroline Auraix
3DN: What are the challenges you have faced in developing your products?
The biggest challenge I have faced and still face is the modeling of my parts. It is often mistakenly thought that once your 3D model is finished, you can move on to the printing stage. What a mistake! It is necessary to take into consideration the material with which one will print.
I learned all this on the job, and I no longer count the “unprinted” models I have made. In addition, there is the difficulty of having a “clean” file, i.e. without holes or non-manifold edges (a kind of duplicate on the edges of a part). Finally, as I said earlier, the definition of the model and its weight are the cornerstones of a successful job. Sometimes you have to sacrifice details to see a project come into life. All this seems obvious to me today, but for the beginner I was, I had to meet each of these problems to be able to solve them.
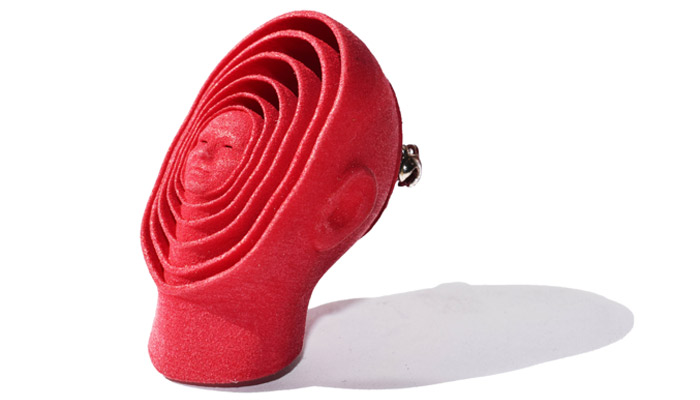
Credits: Caroline Auraix
3DN: What are the biggest benefits of 3D printing for you?
3D printing opens up many perspectives in a wide variety of fields. In the creative sector, it pushes back the field of possibilities by its ability to manufacture structures that a creator’s hand could not achieve. I am thinking of parts with internal structures intertwined in various forms. Or the complex and precise geometries that 3D printing can accurately render, and which would be long and tedious to do in a traditional production.
The time saved by printing your projects without going through the various classic stages such as mock-up, moulding, foundry, rework, etc., makes it possible to see very quickly if the prototype meets expectations. This will result in more attractive prices for the end customer. In short, printing your projects means being more autonomous in your creation, and above all, more free!
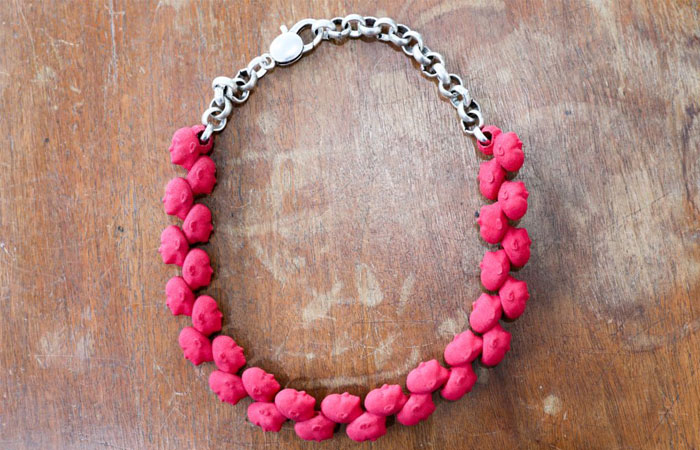
A bracelet designed using 3D technologies | Credits: Caroline Auraix
3DN: What do you think is the future of 3D printing in the jewelry sector?
Some large companies use 3D printing to make quick prototypes to show customers or to manufacture complex molds. But they remain very attached to traditional manufacturing methods that enhance their know-how. However, technical advances now allow precious metals to be printed with a beautiful definition. The Francéclat committee, an actor in the economic development of the profession in France, has launched a competition since 2017 to promote this new way of making jewelry. The idea is beginning to make its way.
3DN: Any last words for our readers?
3D printing has made me dream for many years, don’t wait to get started, with patience and practice you can realize your projects. The internet is full of advice of all kinds, don’t hesitate to try things, to make mistakes, to start over. Whatever your business, 3D printing will become increasingly important in the years to come. Taking the digital shift now means ensuring the sustainability of your business. Many craftsmen remain resistant to this technology and believe that the “machine” will steal their work in a way that is not possible. However, the opposite is going to happen, the expanded manufacturing possibilities will allow them to offer new, customizable, and accessible services. Because that is what we are talking about, the standardization of yesterday will be replaced by a need for authenticity, far from the mass production and over-exploited resources generated by this economic model.
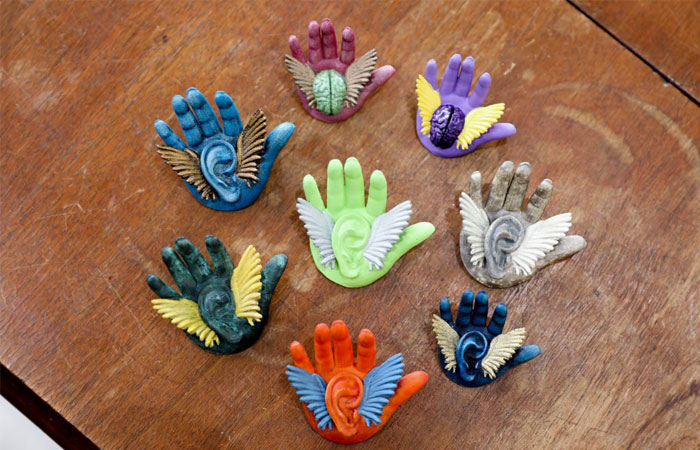
Credits: Caroline Auraix
Find all Caroline Auraix’s work on her website HERE.
What do you think of Caroline Auraix’s work? Let us know in a comment below or on our Facebook and Twitter pages! And remember to sign up for our free weekly Newsletter, to get all the latest news in 3D printing send straight to your inbox!