Carbon on Developing More Innovative Materials and the Importance of Sustainability in AM
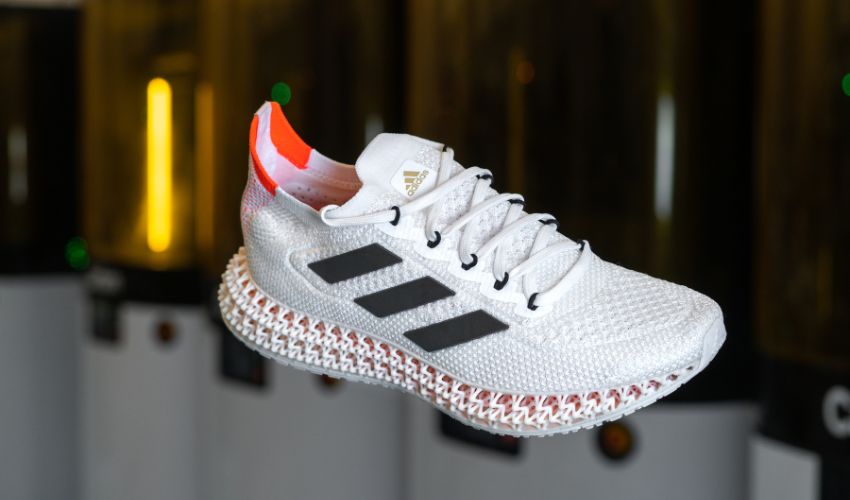
When Carbon was founded in 2013, it set about to radically change product development and manufacturing with its ultra-fast photopolymerization printing process, Digital Light SynthesisTM (DLS). Since then, the company has continued to make waves as companies like adidas, Ford Motor Company, Becton Dickinson Company, and others leverage the Carbon DLS™platform to “deliver better products in less time.” And it does not plan to stop there. Beyond continually improving its technology, the company has been focusing on innovative material development as well as helping the industry become more sustainable as a whole. We sat down with Jason Rolland, Senior Vice President of Materials at Carbon, to learn more about how their technology works, materials, and of course how they are working towards a more environmentally-friendly world.
3DN: Could you please introduce yourself?
My name is Jason Rolland, I lead the Materials team at Carbon, I’ve been with the company for over eight years. I joined really early on, I was employee number 8 and we now have over 500 employees so it’s been fun to watch the company grow and see all the awesome things that have emerged. My background is in Polymer chemistry, I did my undergrad at Virginia Tech and my PhD at University of North Carolina Chapel Hill. That’s where I met Joseph DeSimone who was my PhD advisor and later brought me into Carbon. Joe is a cofounder at Carbon. He introduced me to the technology early on and recruited me to build up the Materials team and platform. I was brand new to 3D printing prior to that and it was super exciting to see the new technology and the potential for where it could go.
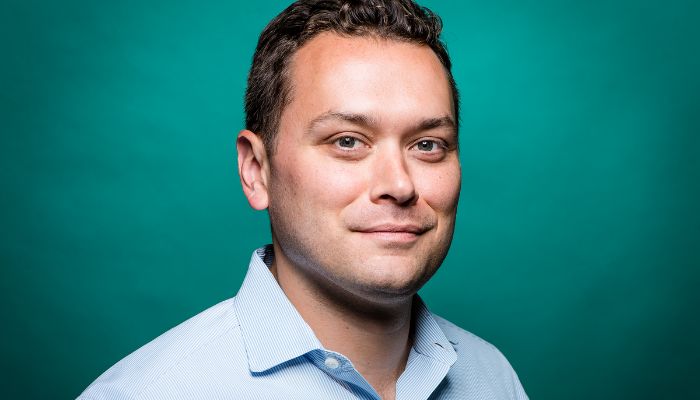
Jason Rolland, SVP of Materials at Carbon
3DN: Could you tell us more about Carbon and your DLS technology?
Since the beginning of Carbon, we have been focused on getting 3D printing into production at scale. To do this, two major issues we needed to address were print speed and material performance. 3D printers can be quite slow no matter what technology you are using and that impacts cost per part, as you are not able to produce in high volume. To address this, we developed Digital Light SynthesisTM (DLS) technology. With it, essentially, we were able to greatly reduce the adhesion forces of the building part to the bottom of the cassette and, consequently, greatly increase print speeds.
Just to give you a better idea, when you are looking at one of our machines, we have a build platform that is set up similar to a bottom-up Digital Light Processing (DLP) machine. We have a cassette that holds the resin and at the bottom there is a very special window and below that is the digital projection system. The key innovation was realizing the importance of oxygen. The permeability of oxygen through the base of that cassette can give a thin layer of uncured resin that is consistently there throughout the build, which greatly decreases your adhesion forces and increases print speeds.
Through the use of this oxygen permeable material at the base of the cassette, you can actually ensure the polymerization happens right at that interface and cure right above that. So, you consistently have this thin liquid layer that decreases your adhesion forces and allows you to print much faster. And now, with certain geometries, we can print 10x faster than traditional 3D printers. From there, we started to really think about material development.
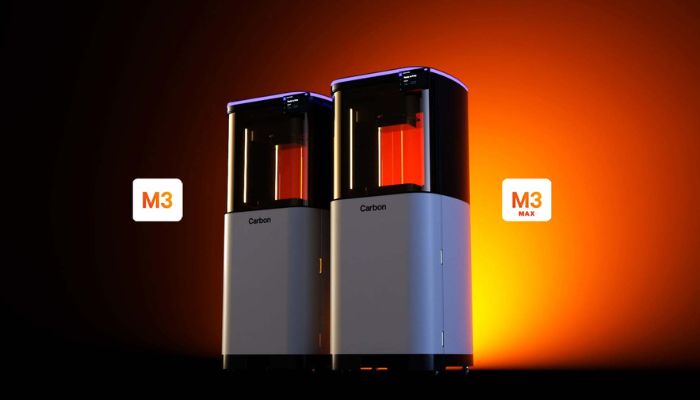
Carbon’s latest launch was the M-series printers, the M3 and the M3 Max
3DN: Expanding on that point, what can you tell us about material development at Carbon?
We realized that in order to enable customers to bring applications to production, we needed materials that are on par with the materials used with injection molding processes or used with foams. That was a really challenging problem because we have a printer based on UV-curable chemistry and patterning of UV light and there are only certain chemistries that are compatible with UV-curable chemistry. You need to have certain functionalities at the ends of your polymer chains. And we saw that as pretty limiting in terms of properties and formulations we could make. To address this, we created dual-cure material systems, which we subsequently patented. That means instead of just UV-curable chemistry, we have a combination of UV-curable chemistry and thermally curable chemistry.
What do I mean by that? With thermally curable chemistry you have two reactive components (part A and part B) for example with epoxy resin or silicone resin. And there is a whole world of thermally cured chemistries out there including polyurethanes, epoxy chemistry, high-temperature thermosets, all these things that are non-UV reactive. We started to combine the two-part thermally-curable chemistry with the UV-curable chemistry and make resins with a part A and part B that are blended just before going into the printer. The printer activates the UV allowing you to define the shape of the part you are building and then entraps the thermal chemistry inside the part in an unreacted state. You finish with a part in the green state, that is then washed or spun to remove residual resin before moving to the baking step. In this baking step, we are activating a separate thermal chemistry that has now been trapped in the UV network. So now you have both components reacted and you have your final part. And it has really opened up the range of available materials, allowing for more cost-effective additive manufacturing in a factory setting with high-performance materials. To be clear, this is very different from UV flood-curing which is a common finishing step for single-part UV-curable chemistry. There, you are simply further polymerizing your initial UV reaction.
3DN: What is the importance of sustainability for Carbon? How are you working to address this issue?
Sustainability is a really important topic for us at Carbon and we have identified several key areas where we can make advances. The first is around the overall problem of generation of hazardous waste. This is particularly important in the liquid resin printing technology sector.
The standard approach is that you print the part, dripping with resin, you have some kind of a tank with a solvent like isopropyl alcohol, you dunk it in, wash it away and then you have a clean part but you have a solvent with resin dissolved in it and this has to all be treated as hazardous waste. This might be okay at small volumes if someone is just prototyping, but when you get into production you have a big problem on your hands. And it’s not just a sustainability issue, but also an economic issue because you are wasting resin as well as generating hazardous waste and this all, of course, costs money.
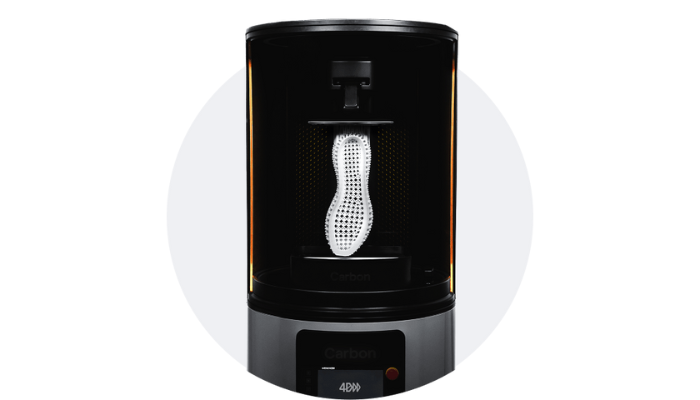
Carbon’s spinning post-processing has helped reduce toxic waste in the creation of midsoles for adidas
Instead, we developed a spin cleaning technology which is completely solvent free. This results in very clean parts with a very thin layer of residual resin which is dealt with in post-curing. This type of spinning technique is used in high-volume production applications such as thermoforming models for dental, adidas midsoles, and other lattice geometries. In fact, for our high-volume applications, we project that in 2022, this spin cleaning technology will have prevented the generation of thousands of metric tons of hazardous waste in total. When economic and sustainability initiatives are aligned, it’s straightforward to make progress. Because it’s a single solution that hits both problems.
In addition, we are using bio-derived or plant-derived raw materials for some of our resins. There are essentially two primary sources for all of the raw materials to make all the chemicals in the world. One is petroleum, all the plastics you would commonly think about are by-products of oil refinement and those are then converted into the building blocks for polymers. But you can also use nature as a factory to make those same types of building blocks. And there is a big trend in the chemical industry to find more sustainable and renewable resources in the form of plants to make building blocks for polymer systems. One of our focus areas is polyurethanes and our partners have created polymers that are part of the overall polyurethane chain that are derived from corn.
In this vein, we have a new resin called EPU44. The material is 40% by weight of raw material derived from plants (resulting in a reduced carbon footprint). It is high performance and has a lower viscosity which is better for printing. In fact, it’s already being used in high volumes for midsoles by adidas. We also have a rigid material called RPU130 which is 25% by weight derived from plant-based material and that is a very high-performance material with high-thermal stability and impact strength. These products show that it is possible to have sustainable materials without sacrificing performance. In fact, in these cases, we even saw a benefit to performance when using the more sustainable raw materials.
Also, like many additive manufacturing companies, we have identified light-weighting and material reduction as a crucial point for sustainability. To help us achieve that, we have a new stand-alone software product, called Design Engine. Using it, you can input a solid CAD model, adjust settings for the properties you want to have and it will generate a lattice model in line with those requirements, allowing for less material and lighter parts. This matters a lot in areas like transportation. If you look at automotive or aerospace, every ounce you can pull out matters in fuel efficiency so if you can make strong but lightweight parts that’s a win for everybody. It’s exciting that the material, software, and hardware sides of our business can each contribute to making products made with Carbon technology more sustainable.
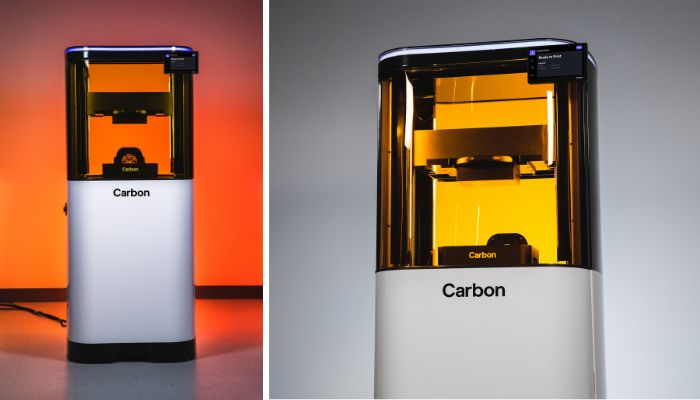
Carbon’s new, more sustainable materials can be used in their machines
The final area is recycling and this is a challenging problem because, globally, the recycling workflow is very inefficient and only a small amount is actually recycled. There are two major technologies for recycling. The first is the more traditional mechanical recycling method. In this process, a discarded part is cleaned, chopped, and blended with virgin feedstock material, typically at a concentration around 5-10%, and melt-processed to form a new part. That serves a purpose, but it’s very inefficient. And there is a problem there in that every time you heat up the polymer, your chains get shorter and you lose some mechanical properties, there are only so many loops you can do before the recycled material doesn’t perform. But we are certainly working in this space. For example, adidas midsoles can be chopped in pieces and then put into an extruder and be processed into a new form. Approximately 80% of the mechanical properties are maintained through this process.
There is also chemical recycling. Now this is very exciting because instead of chopping a material up and remelting it, it can be run through a chemical process where the polymer chain is unzipped, and the monomers used to construct it are regenerated. This then enables the generation of a recycled polymer with all its properties. We’ve created R&D-stage resins where we can recover 50% of starting material by doing a chemical recycling kind of process. This can then be used in a next batch of resin and you have a closed loop system. We are currently looking for partners for this and you can expect to hear more about this in the coming years.
Finally, we are also looking at reducing packaging waste as with high-volume production; your container size actually matters a lot in terms of the amount of waste generated.
3DN: What about additive manufacturing as a whole? How is it sustainable?
Additive manufacturing makes local production possible, manufacturers can make what they need, where and when they need it, which helps reduce transportation costs and the resulting carbon footprint. We learned during covid that supply chains are optimized around cost, not around efficiency and speed of making parts, and this can lead to shortages and other issues.
Additionally, with traditional manufacturing, you have a warehouse full of parts that are injection molded and that need to be temperature and humidity controlled. This is very energy intensive. And to top that off, these are often over-ordered because you’re trying to predict what you need and the extra goes to waste. Alternatively, you could have a warehouse full of 3D printers and you can manufacture parts on demand instead of trying to predict these complicated supply chains. Furthermore, as we previously discussed, light-weighting with additive manufacturing allows less material to be used.
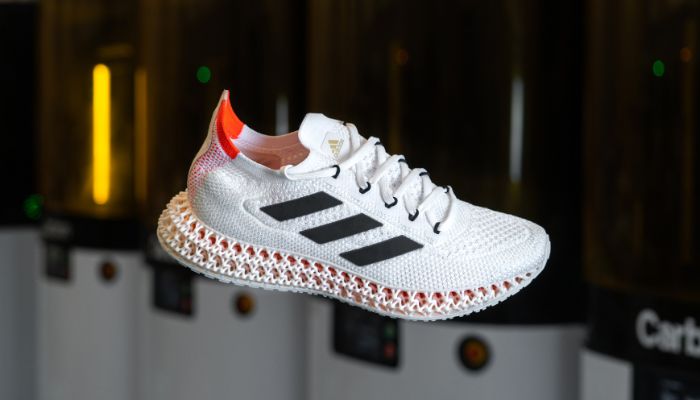
Carbon’s more sustainable methods have played a role in the development of products for adidas
3DN: Any last words for our readers?
I actually think additive manufacturing is more important now than ever in our history. Especially when it comes to the supply chain challenges that everyone is facing. For us, in particular, one of the big things we are pushing is finding ways to make products faster. Carbon’s approach is to work with designers and makers from the idea stage all the way through production and have a common set of processes and materials that is used throughout the development cycle. You can learn more about us and our projects HERE.
What do you think of Carbon’s approach to material development and sustainability? Let us know in a comment below or on our LinkedIn, Facebook, and Twitter pages! Don’t forget to sign up for our free weekly Newsletter here, the latest 3D printing news straight to your inbox! You can also find all our videos on our YouTube channel.
*All Photo Credits: Carbon
I am left foot amputee who desperately seeks an alternative to the Otto Bock Flexfoot which simply is not designed for my active life style. With so much innovation taking place in 3D printing and advanced durable materials could anyone guide me toward a custom printing provider or the kind of machinery I need to do it myself and share with others in similar circumstance?
Hi Leslie, where are you located?
I’d like to help by connecting you to a CPN Partner who can help design and print something for you.
Best regards,
Gary