Can 3D Printing Facilitate Space Exploration?
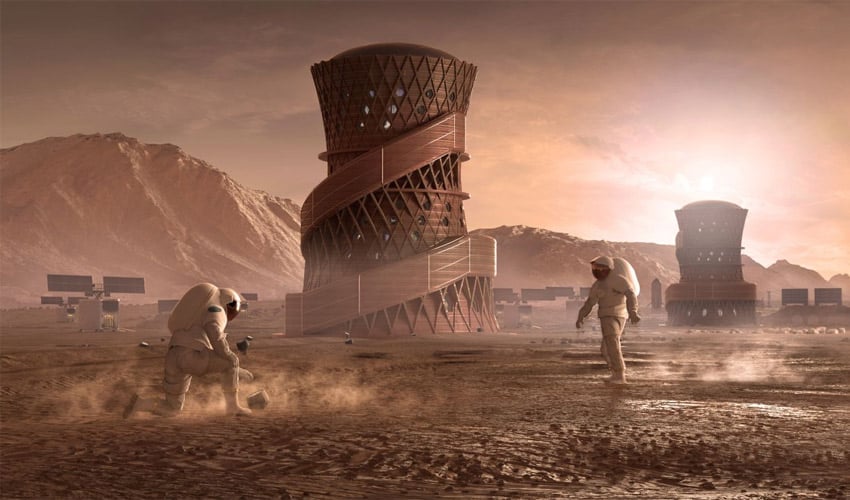
Since the 20th century, humans have been fascinated with exploring space and understanding what lies beyond our planet. Major organizations like NASA and ESA have been at the forefront of space exploration, including with a new significant player in this conquest: 3D printing. This design technique has become increasingly popular among companies due to its ability to produce complex parts quickly and at a low cost. It has enabled the creation of numerous applications such as satellites, spacesuits, and rocket parts. Indeed, according to SmarTech, the market value of additive manufacturing in the private space industry is expected to reach €2.1 billion by 2026. This begs the question: how can 3D printing help humans be more prominent in space?
Initially, 3D printing was mainly used for rapid prototyping in the medical, automotive, and aerospace sectors. However, with the democratization of the technology, it has become increasingly used for end-use parts. Metal additive manufacturing techniques, particularly laser powder bed fusion (L-PBF), have allowed for the production of a wide variety of metals that possess properties and resistance suitable for the extreme conditions of space. Other 3D printing technologies, such as directed energy deposition (DED), binder jetting, and extrusion processes, are also used for manufacturing aerospace components. In recent years, new business models have emerged, with companies like Made in Space and Relativity Space designing aerospace parts using 3D printing technologies.
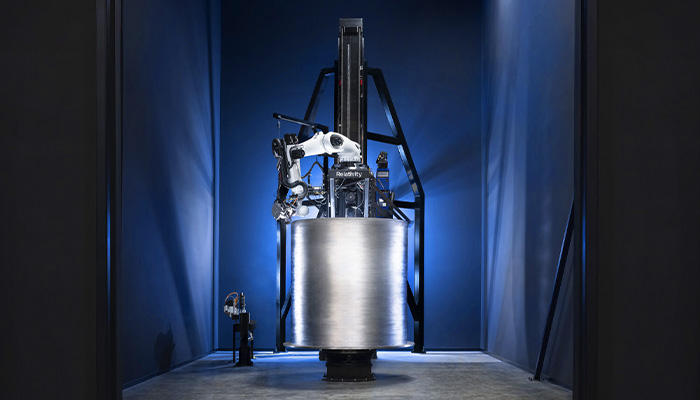
Relativity Space develops 3D printers for the aerospace industry (photo credits: Relativity Space)
3D Technologies in Aerospace
Now that we have introduced them, let us examine the various 3D printing technologies used in the aerospace industry more closely. Firstly, it should be noted that metal additive manufacturing, especially L-PBF, is the most widely used in the sector. This process involves fusing metal powders together layer by layer using a laser energy source. It is particularly useful for producing small, complex, detailed, and customized parts. Aerospace manufacturers can also benefit from DED, which involves depositing a metallic wire or powder and is primarily used for repairing, coating, or producing custom-made metallic or ceramic parts.
In contrast, binder jetting, despite its advantages in terms of production speed and low cost, is not suitable for producing parts with high mechanical properties. This is because it requires post-processing reinforcement steps that increase the manufacturing time of the final product. Extrusion technology can also be effective in space environments. It is essential to note that not all polymers are suitable for use in space, but high-performance plastics such as PEEK can replace some metal parts due to their strength. However, this 3D printing process is still less widespread, but it could be a valuable asset for space exploration by allowing the use of new materials.
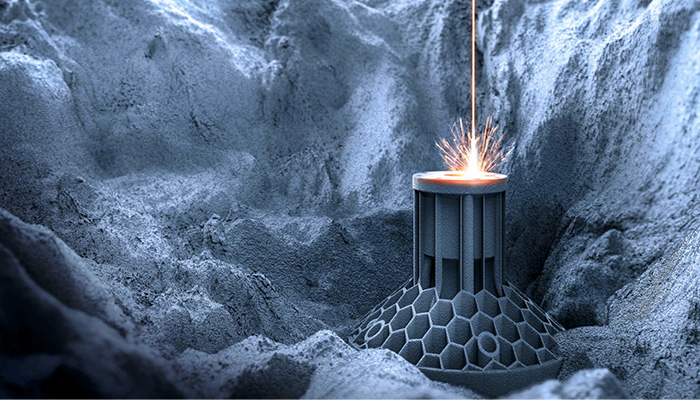
Laser fusion on a powder bed is a widespread process in aerospace 3D printing (photo credits: DMG Mori)
The Potential of Space Materials
The aerospace industry has been utilizing 3D printing to explore new materials and propose innovative alternatives that could potentially transform the market. While metals such as titanium, aluminum, and inconel have been the primary focus, there is a new material that could soon take center stage: lunar regolith. Lunar regolith is a type of dust that covers the Moon, and the European Space Agency has demonstrated the benefits of combining it with 3D printing. Advenit Makaya, an advanced manufacturing engineer at the European Space Agency, describes lunar regolith as similar to concrete, primarily composed of silicon and other chemical elements like iron, magnesium, and aluminum, along with oxygen. In collaboration with Lithoz, the ESA has produced small functional parts such as screws and gears using a lunar regolith simulant that mimics the properties of real moon dust.
Most of the processes involved in manufacturing from lunar regolith use heat, making it compatible with technologies like SLS and printing solutions that use the powder bonding process. The ESA is also working with D-Shape technology, with the goal of mixing magnesium chloride with the material to create a solid part by combining it with the magnesium oxide present in the simulant. One of the significant advantages of this lunar material is its finer print resolution, allowing it to produce parts with the highest level of precision. This characteristic could be a major asset in broadening the range of applications and manufacturing components that are well-suited for lunar bases in the future.
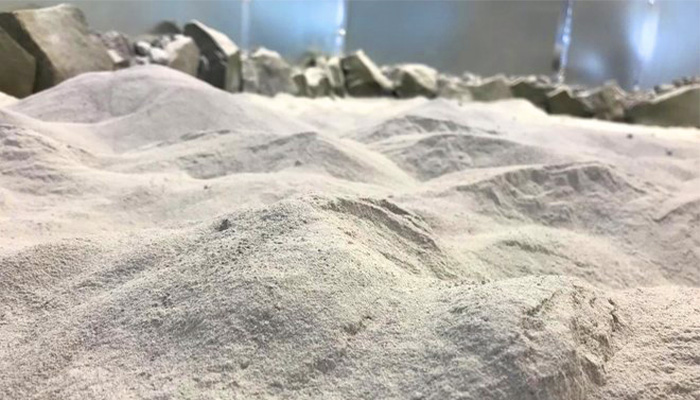
Lunar regolith can be found everywhere on the Moon (photo credits: TriasRnD)
There is also Martian regolith, which refers to the surface material found on the planet Mars. Currently, international space agencies have not been able to retrieve this substance, but that has not stopped scientists from studying its potential in some aerospace projects. Researchers are using a simulant of this material and combining it with a titanium alloy in the hopes of manufacturing tools or rocket parts. Initial results suggest that this material would offer greater strength and protect equipment from rust and radiation damage. Although the two materials have similar properties, lunar regolith remains the most tested material. Another advantage is that these materials can be directly manufactured on-site, eliminating the need to transport raw materials from Earth. Additionally, the regolith represents an inexhaustible source of materials, which helps prevent shortages.
The Different Applications of 3D Printing in Aerospace
The applications of 3D printing technology can vary depending on the specific process used. For instance, the laser melting powder bed process can be utilized to create detailed, short-run parts, such as tooling systems or space spares. A California-based startup called Launcher used Velo3D’s Sapphire metal 3D printing technology to enhance their E-2 Liquid rocket engine. The manufacturer’s process was employed to create the inductor turbine, which plays a critical role in accelerating and driving LOX (liquid oxygen) to the combustion chamber. The turbine and inductor were printed separately using 3D printing and then assembled. This innovative part provides greater fluid flow and more thrust for the rocket, making it a crucial component of the engine.
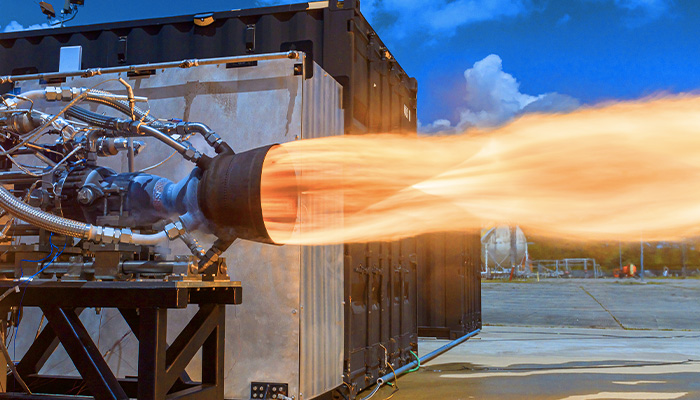
Velo3D contributed to the manufacturing of the E-2 Liquid engine using PBF technology (photo credits: Launcher)
Additive manufacturing has a wide range of applications, including the production of both small and large-scale structures. For instance, 3D printing technology, such as Relativity Space’s Stargate solution, can be used to create large parts such as rocket tanks and propeller blades. Relativity Space has already successfully demonstrated this by producing Terran 1, a rocket that is almost entirely 3D printed, including a fuel tank that measures several meters in size. This industry first launch, which occurred on March 23, 2023, showcased the efficiency and reliability of the additive manufacturing process.
Extrusion-based 3D printing technology also allows for the use of high-performance materials like PEEK to produce parts. Components made from this thermoplastic have already been tested in space and placed on the Rashid rover as part of the Emirates Lunar mission. The purpose of this test is to evaluate the resistance of PEEK to the extreme conditions on the Moon. If successful, PEEK could potentially replace metal parts in cases where they break or when materials are scarce. Additionally, PEEK’s lightweight nature could prove valuable in space exploration.
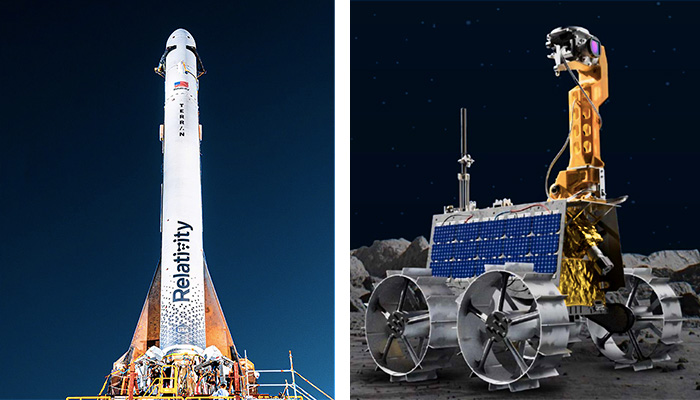
3D printing makes it possible to create many parts for the aerospace industry
The Benefits of 3D Printing in Aerospace
3D printing is an attractive technology that has its advantages over traditional construction techniques, particularly in the final appearance of parts. According to Johannes Homa, CEO of Austrian 3D printer manufacturer Lithoz, “This technology makes parts lighter.” Printed products are more efficient, requiring fewer resources thanks to the freedom of design. This has a positive impact on the environmental impact of part production. Relativity Space has demonstrated that additive manufacturing can significantly reduce the number of components required to manufacture a spacecraft. In the case of the Terran 1 rocket, 100 parts were saved. Additionally, this technology offers a significant advantage in terms of production speed, with the rocket completed in less than 60 days. In contrast, building a rocket using traditional methods can take several years.
In terms of resource management, 3D printing saves materials and, in some cases, recycles waste. Finally, additive manufacturing could be a valuable asset in reducing the weight of rockets during take-off. The goal is to maximize the use of local materials, such as regolith, and minimize the transport of materials in the spacecraft. This makes it possible to carry only the 3D printer, which can create everything on-site after the trip is complete.
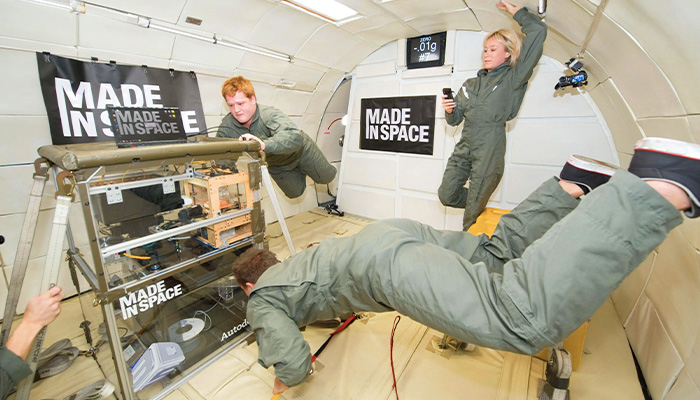
Made in Space has already sent one of its printers into space for testing (photo credits: Made in Space)
The Limits of 3D Printing in Space
Although 3D printing offers many advantages, the technology is still relatively new and has its limitations, according to Advenit Makaya, “One of the main issues with additive manufacturing in the aerospace sector is the control and validation of the process.” Manufacturers have access to labs where each part can be tested for strength, reliability, and micro-structure before validation, a process known as non-destructive inspection (NDI). However, this can be time-consuming and expensive, so the ultimate goal is to reduce the need for these tests. NASA has recently established a center to address this issue, focused on the rapid certification of metal parts made with additive manufacturing. The center aims to improve computer models of products using digital twins, which will help engineers better understand the capabilities and limitations of the parts, including how much stress they can handle before breaking. By doing so, the center is expected to help promote the use of 3D printing in the aerospace industry, allowing it to compete more effectively with traditional manufacturing techniques.
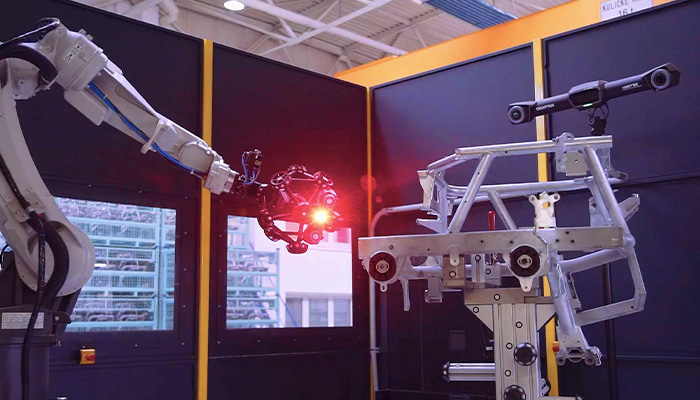
The parts are thoroughly tested for reliability and strength (photo credits: Creaform)
On the other hand, if the manufacturing is done in space, the verification process is different. Advenit Makaya of ESA explains: “There is a technique that consists of analyzing the part while it is being printed.” This method helps to identify which printed products will be suitable and which ones will not be usable. Additionally, there is a self-correction system for 3D printers used in space, which is being tested on metal machines. The machine can identify potential errors during the manufacturing process and automatically change its parameters to correct any defects in the part. These two systems are expected to improve the reliability of printed products in space.
To validate a 3D printed solution, standards have been developed by NASA and ESA. These standards consist of a list of tests to be performed on the part to determine its reliability. They take into account powder bed fusion technology, and are being updated for other processes. However, many major players in the materials industry, such as Arkema, BASF, Dupont, and Sabic, also offer traceability of this kind.
Living in Space?
With the advances in 3D printing, we have seen numerous successful projects on Earth in which houses have been built using this technology. It leads us to wonder whether, in the near or distant future, this process could be used to construct habitable structures in space. While it is not currently practical to live in space, building houses, particularly on the Moon, would be beneficial for astronauts who embark on space missions. The European Space Agency (ESA) aims to build domes on the Moon using lunar regolith, which can be used to create walls or bricks to protect astronauts from radiation. According to Advenit Makaya of ESA, lunar regolith, which is composed of about 60% metal and 40% oxygen, is an essential material for the survival of astronauts as it provides an inexhaustible source of oxygen if extracted from the material.
NASA has awarded $57.2 million to ICON to develop a 3D printing system for lunar surface construction, and is also collaborating with the company to create a Martian home, called Mars Dune Alpha. The goal is to test living conditions on Mars, with volunteers living in the home for a year to simulate conditions on the red planet. These efforts represent important steps towards building 3D printed structures directly on the Moon and Mars, which could eventually pave the way for human colonization of space.
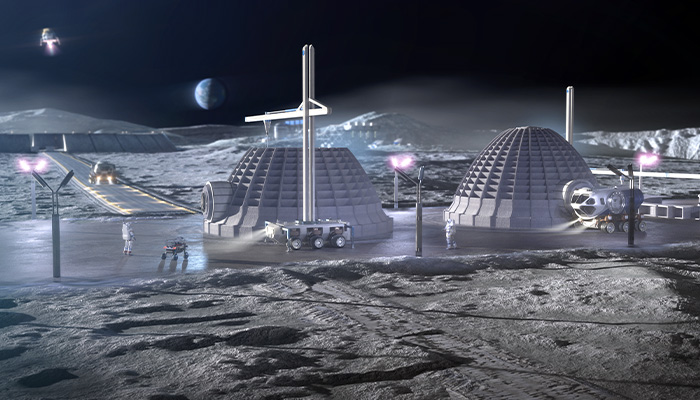
In a distant future, these houses could allow life on space (photo credits: ICON)
What do you think of the use of 3D printing in space exploration? Let us know in a comment below or on our LinkedIn, Facebook, and Twitter pages! Don’t forget to sign up for our free weekly Newsletter here, the latest 3D printing news straight to your inbox! You can also find all our videos on our YouTube channel.
*Cover photo credits: SEArch+