Cambridge Develops Laser-Assisted Cold Spray Technique with Potential for Aerospace Applications
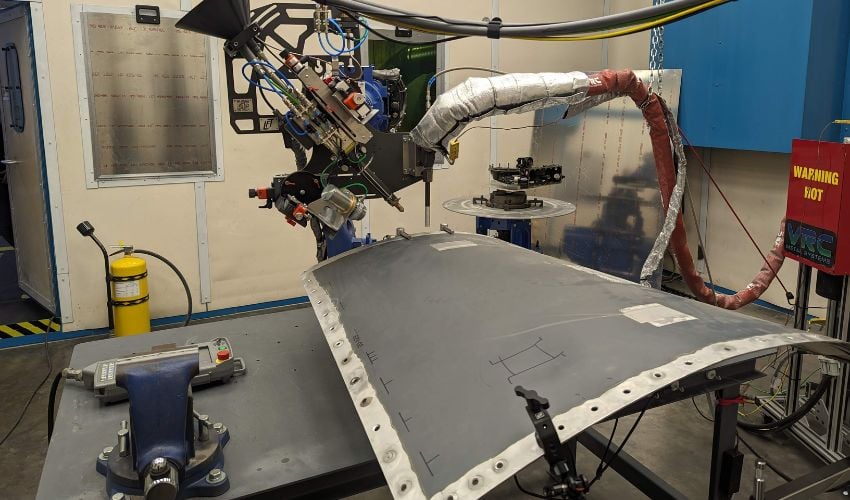
The Centre for Industrial Photonics (CIP) at the University of Cambridge’s Institute for Manufacturing (IfM) has developed a new technology: laser-assisted cold spray (LACS). The team claims LACS is an improvement over existing cold spray technologies. They have also demonstrated LACS’ effectiveness in aerospace applications.
Prior to developing the new method, the IfM team used nitrogen as a carrier gas for the powder. Then, they realized that when working with high-strength materials such as titanium and aluminium alloys, using helium was essential for achieving optimal deposition. Project leader Professor Bill O’Neill explained, “This is because helium, because of its lower molecular weight, enables higher particle velocities in cold spray, enhancing impact energy and improving adhesion to the substrate.”
However, using helium posed a problem: it costs around £80 per minute of operation, and even state-of-the-art recycling efforts recovered only around 85% of the helium. Additionally, the recycling equipment greatly restricted the size of the parts that could be manufactured, as they had to fit within a size-limited chamber for capturing excess helium. The researchers knew they needed to find a more realistic solution than a helium recycling system, so they started to investigate lasers.
How Laser-Assisted Cold Spray Works
- A cold-spray nozzle deposits a supersonic powder stream of solid-state material powders
- A laser heats the deposition site, reducing the substrate yield stress, resulting in a stronger bond between the materials without the need for melting.
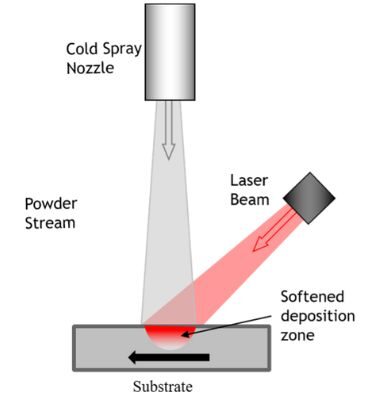
A laser beam softens the deposition zone for the powder stream.
Advantages Over Other Cold Spray Methods
LACS overcomes the high-temperature and material limitations of comparable techniques. Advantages include:
- Reduces costs by removing the need for helium;
- Enhanced adhesion and deposition efficiency, resulting in stronger coatings than conventional cold spray, important for high-strength materials like titanium and refractory metals;
- Powder’s structure is maintained because deposition occurs at a lower particle velocity, an advantage for materials with specialised properties that are easily damaged, such as nano-structured coatings and rare earth magnets;
- Improved material compatibility, enabling the deposition of harder and more challenging materials that typically have poor adhesion in standard cold spray
- Reduced residual stresses and porosity, thanks to the laser’s thermal input;
- Minimal thermal impact on substrate, avoiding phase transformations or distortion, unlike traditional thermal spray methods;
- Speed, with coatings that can be added at up to 10 kg per hour.
- Lower temperatures in the overall process, because laser assistance allows the process to operate at lower gas temperatures, for example, 400–700 oC, compared to up to 1200 oC for cold spray, reducing power consumption and simplifying system design;
- Fine-tuning of coating properties by creating customised powders enables specialised characteristics such as magnetism, solid-state lubrication and enhanced wear resistance to be introduced into deposits;
- Local control of properties with grading composition that allows the stresses at interfaces between dissimilar materials to be reduced.
LACS for Aerospace
Aerospace demands high precision, high strength and relatively low-volume manufacturing. By enabling the on-demand fabrication of high-quality coatings and component repairs, the LCAS has a high potential for extending aircraft lifespans. LACS offers a sustainable, cost-effective and efficient solution. Traditional repair techniques, such as welding, are unsuitable for high-performance applications because the heat needed to adhere the new and old material together impacts the strength and reliability of the part.
Further Applications
Because LACS allows users to customise material properties, technology has a wide range of applications. O’Neill listed the following examples:
- Producing lightweight components for electric vehicles and aerospace
- Creating hydrogen storage systems
- Enhancing wind turbine maintenance
- Manufacturing energy-efficient batteries and fuel cell components
- Developing advanced heat exchangers for industrial energy savings and catalyst coatings for carbon capture.
“The potential applications for LACS are limitless and we are motivated to deliver a technology that can significantly aid in the transition to net zero, through both a more efficient, low-waste manufacturing technology and the doors it opens for sustainable product development,” O’Neill said.
Future Research
The lab’s next goal is to refine LACS technology so that it can 3D print a shape. The researchers are looking into several ways to achieve this, including mounting the part on a moving arm to allow it to be moved in three dimensions and increasing the control over the direction of the powder stream to produce clean, smooth edges. “Currently, we have little control over the shape of deposition of the powder,” O’Neill said. “This is not an issue for coatings but presents a significant restraint for part-building applications. Our next goal is to find a solution to this limitation, and we already have some very promising results.” To learn more about the research, click HERE.
What do you think of laser-assisted cold spray? Let us know in a comment below or on our LinkedIn or Facebook pages! Plus, don’t forget to sign up for our free weekly Newsletter to get the latest 3D printing news straight to your inbox. You can also find all our videos on our YouTube channel. For more 3D printing news in the aerospace and defense sectors, check out our dedicated page HERE.
*Cover Photo: LACS equipment set-up to add a coating to repair an aircraft wing panel. All Photo Credits: University of Cambridge