Boeing to Use 3D Printing for Apache Helicopters
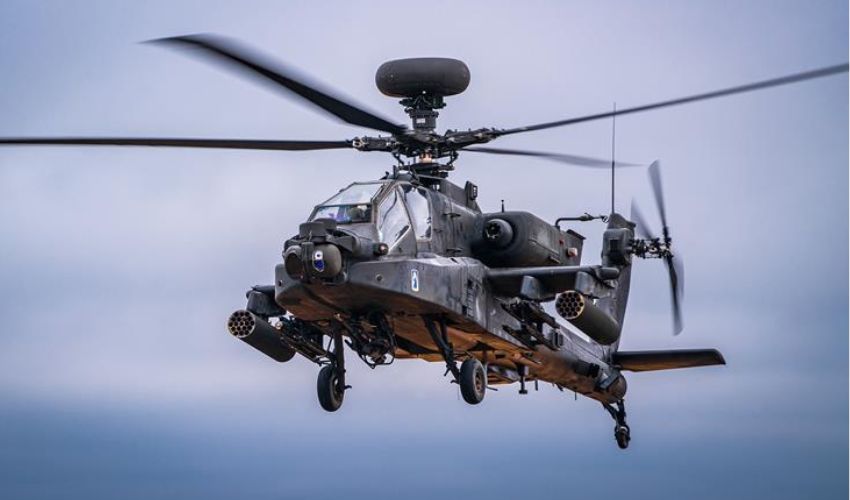
3D printing is continuing to gain momentum in the U.S. defense industry! Boeing has announced plans to start testing the fully 3D-printed prototype of the main rotor system of their AH-64 Apache attack helicopter in April 2024. In addition, Boeing plans to compare the 3D-printed parts with those made by conventional means. Furthermore, fatigue tests will be run against the traditionally forged parts, according to Andy Pfeiffer, Boeing Global Services’ senior design engineer and additive manufacturing expert.
At the recent annual meeting of the Association of the U.S. Army (AUSA), Boeing and the non-profit Applied Science and Technology Research Organization of America (ASTRO) jointly unveiled their first 3D printed component as part of the Jointless Hull Project. This was the main rotor joint assembly, a joint for the rotor system. Printed in its entirety and in one piece by the world’s largest metal 3D printer at Rock Island Arsenal, Illinois.
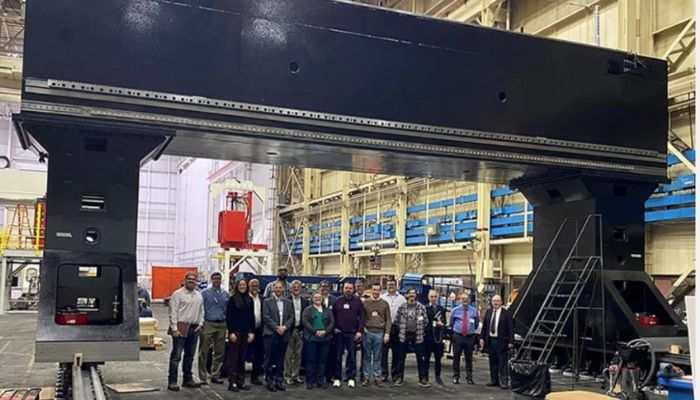
The world’s largest metal 3D printer at Rock Island Arsenal (photo credits: ASTRO America)
We have previously told you about the Jointless Hull Project. In it, the army seeks to create a printer even large enough to print an armored hull in one piece. This is being done through the Army’s Ground Vehicle Systems Center which is financially supporting ASTRO with $95 million from the U.S. budget. The money is intended to help ASTRO advance advances in large format additive manufactured parts. Such as tank hulls and other combat vehicle prototypes in the defense industry. ASTRO is also studying the economics of producing different 3D-printed components, according to ASTRO engineer Emma Gallegos, including of course the Apache helicopter parts.
Trade-off Between Conventional and Additive Manufacturing for Apache Helicopters at Boeing
In the case of the 3D printing used by Boeing for the AH-64 Apache, what stands out in particular is the high speed of the printing process compared to conventionally used production methods. The 3D printing process of the 6000 series aluminum main rotor joint itself took about eight hours. In addition, the application of the aluminum took 45 minutes. Performing the manufacturing of the components using the traditional technology of forging takes significantly longer, one year, according to Pfeiffer. Accordingly, additive manufacturing clearly reduces manufacturing lead times. As a result, Boeing has given ASTRO a list of components to be renewed and potentially created from the 3D printer.
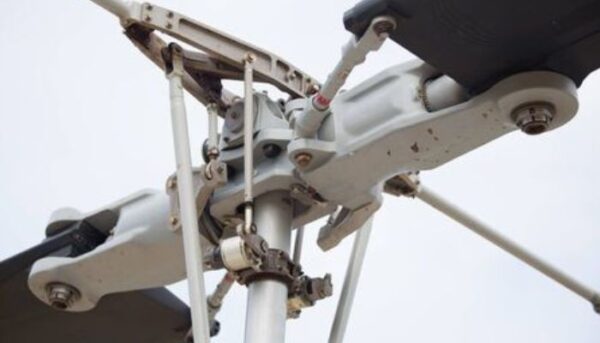
The helicopter’s rotor (photo credits: 123RF)
However, in terms of cost, conventional forging can be more profitable in areas of mass production. For the production of smaller quantities, however, 3D printing is cheaper and economically advantageous. Furthermore, the microstructure of 3D-printed components has higher stability, robustness and material strength than the structure fabricated by the conventional manufacturing process.
In any case, Boeing hopes that the new process will optimize the supply chain for parts that are usually forged. In addition, when deciding between one of the two processes, the decisive factor is whether the company already has a supplier and the tools needed to manufacture using conventional methods. Boeing, on the other hand, emphasizes the importance of additive manufacturing for urgent aircraft repair work that requires flexible replacement delivery of parts.
What do you think of Boeing and the production of Apache helicopter parts using 3D printing? Let us know in a comment below or on our LinkedIn, Facebook, and Twitter pages! Don’t forget to sign up for our free weekly Newsletter here, the latest 3D printing news straight to your inbox! You can also find all our videos on our YouTube channel.
*Cover Photo Credits: US Army